Изготовление блоков керамзитных: Технология изготовления керамзитобетонных блоков
Изготовление стеновых блоков
У частных застройщиков строительные блоки пользуются высоким спросом из-за оптимального соотношения цены и качества. Сегодня керамзитобетонные блоки считаются одним из наиболее популярных строительных материалов. Для производства строительных блоков используется оборудование для формовки блоков.
Что же нужно знать для собственного производства керамзитобетонных и арболитовых стеновых блоков?
Керамзитобетонные стеновые блоки
Исходным сырьем для изготовления керамзитобетонных блоков служит керамзит – вспененная и обожженная глина, вода и цемент. В изломе гранула керамзита имеет структуру застывшей пены. Спекшаяся оболочка, покрывающая гранулу, придает ей высокую прочность. Керамзит, обладающий высокой прочностью и легкостью, является основным видом пористого заполнителя. Поэтому высококачественные керамзитобетонные блоки имеют плотность от 600 до 1800 кг/м3.
Как строительный материал керамзитобетонные блоки представляет собой лёгкий бетон, в котором заполнителем является керамзит — ячеистый материал в виде гранул.
Применяя керамзитобетон можно существенно снизить вес зданий и конструкций, достигнув ряда положительных технико-экономических показателей. В климатических условиях России будет достаточно уложить керамзитобетонные блоки в один ряд при строительстве основных внешних стен, чтобы соблюсти нормы теплосбережения строительных конструкций.
Арболитовые стеновые блоки
Дерево в России всегда оставалось самым популярным строительным материалом для личного коттеджно-дачного строительства: хорошая теплопроводность, привлекательный внешний вид, сравнительно невысокая стоимость и высочайшая экологичность долгое время делали этот материал действительно наилучшим выбором. Но и серьёзных недостатков у деревянных домов немало, что вкупе с неуклонным ростом стоимости и падением качества деревянного домостроения даёт повод для поиска лучших аналогов. Но, лучшим заменителем дерева, как ни странно, является само дерево.
Арболит – так называемый деревобетон, материал, на 80-90% состоящий из древесной щепы, позволяет не только получить все преимущества деревянного дома, но и обладает рядом существенных плюсов. Сравним особенности практического применения этих материалов в современных условиях.
В строительстве загородных деревянных домов наиболее используемыми разновидностями стеновых материалов сейчас являются обычный брус, оцилиндрованное бревно и клееный брус (в порядке возрастания стоимости). К сожалению, производимые размеры этих материалов практически никогда не превышают 30 сантиметров в диаметре или толщине, ранее же брёвна менее 50см вообще не применялись в строительстве
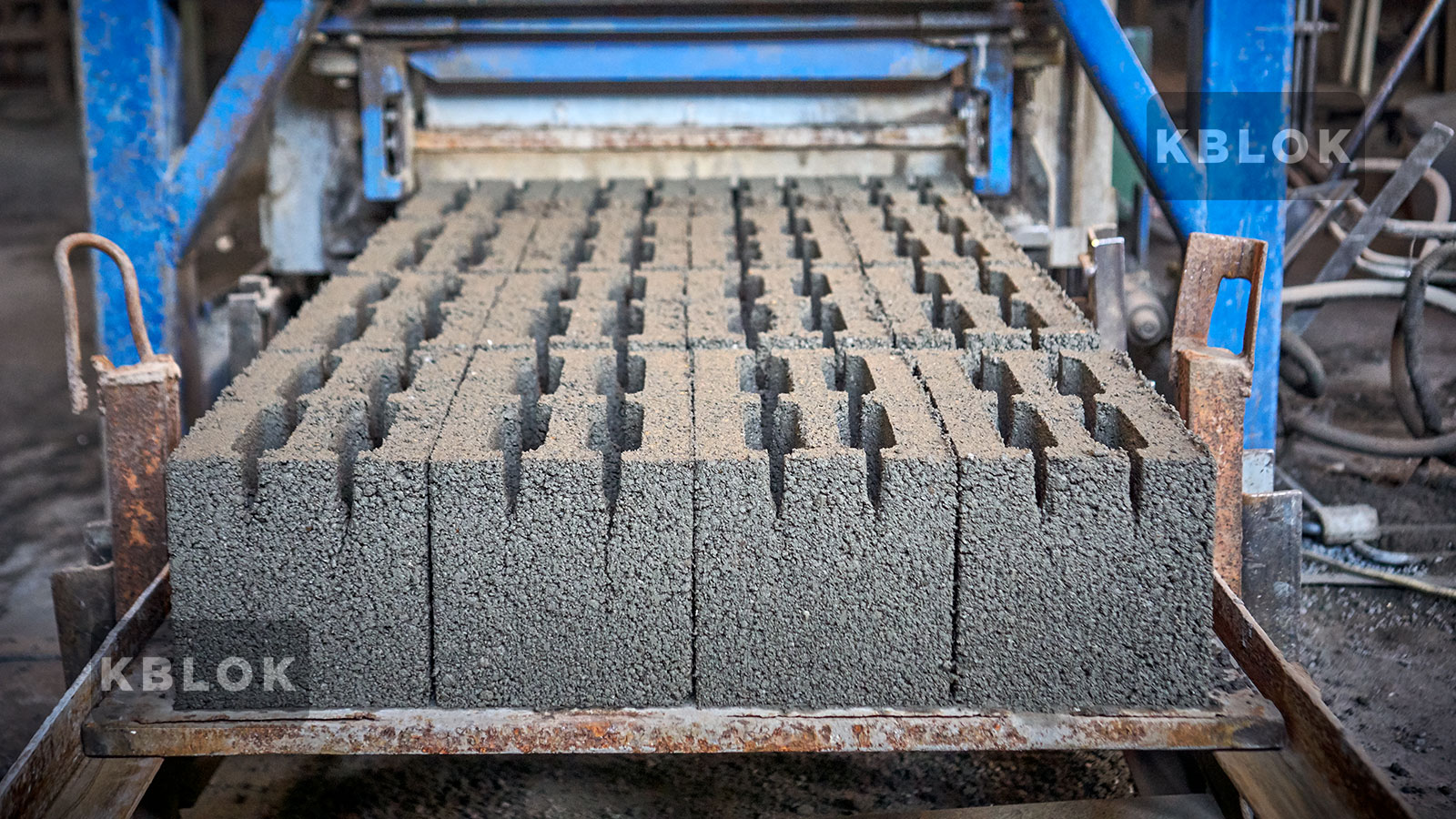
Следовательно, мало того что точно придётся забыть о желаниях иметь настоящую бревенчатую или брусовую поверхность внутри дачного дома и произвести дополнительные (иногда весьма немалые) затраты на утеплители, но и вспомнить о том, что с ними – вы в большинстве случаев получаете постоянное фенольное или стирольное загрязнение атмосферы в доме.
Теплопроводность дерева составляет 0.15-0.4 Вт/(мК), арболита – 0.07-0.17 Вт/(мК). Толщина стены из стандартных блоков из арболита (400х200х200 мм.) – 40 см, такая стена по теплосбережению вполне соответствуют классическим стенам из полуметровых бревён

Вернёмся к дереву, к наиболее важной из его особенностей – дышащим свойствам деревянных стен. Именно они создают тот уникальный микроклимат деревянных домов из бруса или брёвен, регулируя уровень влажности и обеспечивая пассивную вентиляцию огромной мощности – до 35% внутреннего воздуха в помещении может обновляться через поры стен каждые сутки. Но снова вспомним об утеплении. Безусловно, и сам утеплитель, и соответствующий облицовочный материал можно подобрать также с дышащими свойствами, но… Дышащие стены – это вентиляция. А вентиляция – это наиболее эффективный способ распространения всех ядов. Поэтому, при использовании минваты, пенопласта, многих других видов утеплителей, а также при покрытии стен различными видами красок – просто
Далее, главное, в чём дерево всегда проигрывало всем видам кирпича и бетона – высокая горючесть. Различные составы (которые следует учитывать и в расчете стоимости деревянного дома), конечно, снижают степень воспламеняемости, но, во-первых, достаточно слабо, а, во-вторых, со временем уровень защиты падает. К тому же, в данном свете наибольшую проблему опять представляют легковоспламеняемые и высокотоксичные утеплители.
Также, большую проблему всегда представляла плохая биологическая устойчивость древесины – гниение, заражение различными грибками и вредителями, просто потеря внешнего вида из-за атмосферных факторов, появление микротрещин и т.д.… И такая проблема именно в современных загородных домах становится ещё более актуальной – при оцилиндровке брёвен оголяются самые мягкие слои древесины, которые значительно сильнее подвержены всем этим факторам. Всё это в какой-то степени решаемо специальными средствами. Но, в любом случае,
В самом процессе строительства дерево имеет ещё ряд неприятных особенностей. Высокая усадка всех видов древесины не позволяет быстро построить деревянный дом – обязательно требуется потратить минимум год на усадку здания (до 10%) и только после этого можно начинать отделку. К тому же, при этом дерево нередко сильно растрескивается, что не только влияет на внешний вид, но, опять же, ухудшает параметры биостойкости и теплоизоляции здания. Строительство домов из бревён ещё и требует затрат на весьма недешевую и непростую операции по конопатке щелей, требующую хороших материалов и профессиональных исполнителей, так как некачественная работа здесь (а проводится она дважды – до и после усадки строения) наносит сильнейший удар по теплосберегающим качествам дома.
Арболит имеет усадку всего 0.4%, поэтому возможно оперативное возведение здания из стеновых блоков в один заход, то есть полное строительство типового садового дома можно завершить, при желании, всего за месяц. И очень весомое качество арболита – чрезвычайно низкая сложность строительства, как и по требованиям к трудозатратам, так и, главное – к профессиональности. Дерево – очень капризный материал и требует грамотного подхода специалистов. Даже громкое имя строительной компании – не залог качества, и узнать кто и как на самом деле строит ваш дом – практически невозможно, если вы сами не строитель. На полноценную же проверку результата – уйдут годы. А
В итоге, современное деревянное домостроение на практике оказывается абсолютно неэффективным. В результате длительного, сложного и очень дорогостоящего строительства – возможно получить красивый бревенчатый или брусовый дом (и то только с внешней стороны), набитый утеплителем с сомнительной экологичностью, загерметизированный со всех сторон, требующий постоянной заботы, чтобы сохранять хоть в каких-то разумных параметры огнестойкости и биостойкости. А через некоторое время, даже при качественной постройке и уходе, — всёравно потребующий обшивки вагонкой, блок-хаусом, сайдингом или другими облицовочными материалами. И есть ли смысл во всём этом процессе, если за значительно более низкую цену и в в кратчайшие сроки можно получить дом с изначально теплыми, негорючими и экологичными стенами из арболита.
Материалы для изготовления стеновых блоков
ЦементДля стеновых блоков цемент является наилучшим вяжущим. Цемент обладает достаточной скоростью твердения, обеспечивает высокую прочность и влагоустойчивость изделий. Для изготовления изделий могут применяться все типы цементов с маркой прочности от 400 до 500. Минимальные затраты на цемент обеспечиваются, когда его марка прочности в 1,5…2 раза выше требуемой прочности изделий.
ЗаполнителиВ качестве заполнителей обычно используют песок, щебень, шлаки, золы, керамзит, опилки, древесную щепу и другие инертные материалы, а также их любые комбинации. В заполнителе должны отсутствовать чрезмерное количество пыли, мягкие глинистые включения, лед и смерзшиеся глыбы. Для размораживания смерзшихся кусков заполнителя его постоянные хранилища желательно размещать в теплых зонах помещений или снабжать выходные люки бункеров с заполнителями устройствами парового подогрева. Такой подогрев способствует также более быстрому твердению бетона в холодное время года.
Мелкий заполнитель (за исключением зол) по гранулометрическому составу должен относится к группам «крупный» и «средний» (Мк более 2,0). Использование заполнителя меньшей крупности допускается в сочетании с крупным заполнителем. Наличие в песке зерен размером свыше 10мм не допускается. Количество пылевидных, илистых и глинистых частиц в природном песке не должно превышать 3%. Мелкий заполнитель следует хранить на складе в бункере, закрытом от атмосферных осадков. В зимнее время должен обеспечиваться подогрев заполнителя.
Установлено — если стружка или щепа будут слишком длинными (более 40 мм. ) — ухудшаются характеристики прочности на сжатие, если щепа мелкая, или это опилки — резко ухудшаются характеристики прочности на изгиб (мелкие частички не обеспечивают армирующего эффекта), и дерево просто становиться как наполнитель, не неся никакой пользы и не улучшая материал.
Заполнители обычно подразделяются на два вида: мелкие и крупные.
1. Мелкие заполнители
Имеют размер зерен от 0,01 до 2 мм. Обычный песок является наиболее широко применяемым мелким заполнителем. Небольшое содержание в песке ила, глины или суглинков допустимо при условии, что их количество не превышает 10% по весу. Отходы щебеночного производства — мелкие частицы гранита, доломита, мрамора и т.п., зола-унос, мелкая фракция шлаков также относятся к этой группе. Мелкий заполнитель обеспечивает пластичность смеси, уменьшает количество трещин в изделиях и делает их поверхность более гладкой. Однако избыток мелкого заполнителя, и особенно его пылевидной составляющей, снижает прочность изделий.
2. Крупные заполнители
К крупным заполнителям относятся материалы, имеющие размер зерен 5 и более мм. В составе бетонной смеси крупный заполнитель необходим для создания внутри изделия пространственной рамы, от прочности которой зависит прочность изделия. Обычно недостаточная прочность изделия (при качественном вяжущем) объясняется недостатком в бетоне крупного заполнителя. Избыток крупной фракции заполнителя в смеси приводит к тому, что поверхность изделий и их грани получаются пористыми и неровной формы, а при транспортировке готовых изделий увеличивается количество боя. С увеличением размеров зерен крупного заполнителя прочность изделий возрастает.
Максимальная фракция заполнителя составляет 15 мм. При увеличении размера зерен появляется вероятность их заклинивания в затворе бункера, загрузочном ящике и матрице. При этом в загрузочном ящике гнутся ворошители и создаются избыточные нагрузки на их подшипники и цепной привод, а при попадании больших камней в матрицу — гнуться ее перемычки и пуансон. В качестве крупного заполнителя широкое распространение получил гравий — совокупность окатанных зерен и обломков, получаемых в результате естественного разрушения и перемещения скальных горных пород. Гравий должен быть чистым, прочным и не содержать каких-либо мелких включений. Щебень из природного камня является наиболее распространенным крупным заполнителем, получаемым в результате искусственного дробления горных пород. Не рекомендуется применять щебень из сланцев, т.к. они не обеспечивают долговечность изделий. Очень важно, чтобы в щебне не было пыли, для чего его целесообразно промывать. К крупным заполнителям относится также большая группа различных легких заполнителей.
В воде, используемой для приготовления бетона, должны отсутствовать примеси масел, кислот, сильных щелочей, органических веществ и производственных отходов. Удовлетворительной считается вода питьевого качества или вода из бытового водопровода. Вода обеспечивает гидратацию (схватывание) цемента. Любые примеси в воде могут значительно снизить прочность бетона и вызвать нежелательное преждевременное или замедленное схватывание цемента. Кроме того, загрязненная вода может привести к образованию пятен на поверхности готового изделия. Температура воды не должна быть ниже 15° С, поскольку снижение температуры ведет к увеличению времени схватывания бетона. Воду рекомендуется подавать в смеситель через перфорированную трубу.
В последние годы достигнут значительный прогресс в области разработки различных химических присадок к бетону. Они используются для снижения расхода цемента, увеличения скорости его схватывания, сокращения продолжительности тепловлажностной обработки изделий, придания бетону способности твердеть в зимнее время, повышения его прочности и морозостойкости.
Из добавок ускорителей твердения наиболее распространен хлористый кальций СаСl. Количество добавок хлористого кальция составляет 1.. .3% от массы цемента. Эти добавки повышают прочность бетона в возрасте 3 суток в 2…4 раза, а через 28 суток прочность оказывается такой же, как и у бетона без добавок.
Хлористый кальций применяется как в сухом виде, так и в растворе. В сухом виде он добавляется в заполнитель, в растворе вносится в предназначенную для приготовления смеси воду с сохранением суммарного количества воды в смеси. Добавление СаСl несколько увеличивает стоимость исходных материалов, однако за счет более быстрого набора прочности обеспечивает изготовителю строительных изделий экономию энергии на обогрев помещения для их вылеживания перед отгрузкой заказчику, значительно превышающую расходы на хлористый кальций, а также уменьшает количество боя изделий при транспортировке.
Большой положительный эффект в производстве бетонных изделий дает использование воздухововлекающих добавок: древесной опыленной смолы СДО нейтрализованной воздухововлекающей смолой СНВ, теплового пекового клея (КТП), сульфитно-дрожжевой бражки (СДБ). Воздухововлекающие добавки улучшают подвижность смеси при заполнении матрицы вибропресса, повышая этим качество поверхности изделий и уменьшая количество боя. Главным достоинством воздухововлекающих добавок является увеличение морозостойкости бетона. Эффект повышения морозостойкости объясняется насыщением пузырьками воздуха пор бетона, что уменьшает проникновение в них воды и препятствует возникновению разрушающих напряжений в бетоне при замерзании капиллярной воды за счет демпфирующего сжатия пузырьков воздуха.
Воздухововлечение несколько снижает прочность бетона, поэтому не следует вводить в него большое количество воздухововлекающей добавки. Например, количество СДБ, вводимой в бетонную смесь, составляет 0,15…0,25% от массы цемента в пересчете на сухое вещество бражки. Оптимальное количество других добавок не превышает 1% от массы цемента и уточняется экспериментально.
Перечень некоторых химических добавок
№ |
Наименование химической добавки |
Нормативная документация |
Содержание от массы цемента, % |
Воздухоотвлекающие добавки |
|||
1 |
СДО смола древесная омыленная |
ТУ 81-05-02-78 |
~ 0,01. |
2 |
Смола нейтрализованная СНВ |
ТУ 81-05-75-74 |
~ 0,01…0,02 |
Пластифицирующие добавки |
|||
3 |
Сульфитно-дрожжевая бражка СДБ |
ТУ 81-04-225-73, ОСТ 81-79-71 |
~ 0,2 |
4 |
Поверхностно активный щелок ПАЩ-1 |
ТУ 6-03-26-77 |
~ 0,15…0,35 |
5 |
Суперпластификатор С-3 (разжижитель) |
ТУ 6-1429-258-79 |
~ 0,3. |
6 |
Лингосульфанаты технические ЛСТ |
ТУ 13-0281036-05 |
~ 0,2…0,3 |
7 |
Лингосульфанаты ЛСБУ |
ТУ 13-7308001-738 |
~ 0,2…0,3 |
8 |
Лингосульфанаты модифицированные ЛСТИ |
ОСТ 13-278 |
~ 0,2…0,3 |
Пластифицирующие-воздухоотвлекающие |
|||
9 |
Мылонафт |
ГОСТ 13302 |
~ 0,02 |
10 |
Асидол |
ГОСТ 13302 |
~ 0,02 |
11 |
Этилсиликонат натрия ГКЖ-10 и метилсиликонат натрия ГКЖ-11 |
ТУ 6-02-6978-72 |
~ 0,2 |
Газообразующие (гидрофобизирующие) |
|||
12 |
Полигидроксилоксан ГКЖ-94 |
ГОСТ 10834-76 |
~ 0,1 |
Составы для изготовления стеновых камней
№ |
Марка камня по прочн. |
Вид бетона |
Марка бетона |
Объемная масса сухого бетона кг/м3 |
Материал |
Расход материалов (сухих) на 1 м3 |
|
по массе, кг |
по объему, м3 |
||||||
1 |
75 |
Песчаный бетон |
М200 |
1970-2020 |
Портландцемент М400 |
320 1650-1700 |
0,26 1,13 0,16 |
2 |
50 |
Керамзито-бетон на кварцевом песке |
М150 |
1430-1590 |
Портландцемент М400 |
230 600-760
600 190 |
0,18 0,91
0,40 0,19 |
3 |
50 |
Шлакобетон |
М150 |
1650-1750 |
Портландцемент М400 |
250 1400-1500 200 |
0,2 1,25 0,20 |
4 |
50 |
Золошла-ковый бетон |
М150 |
1400-1600 |
Портландцемент М400 |
200 650-700 550-700 |
0,16 1,58
0,70 0,28 |
5 |
50 |
Бетон на известня-ковом щебне |
М150 |
1870-1970 |
Портландцемент М400 |
220 1650-1750 |
0,18 1,25 |
6 |
35 |
Бетон на щебне из кирпичного боя |
М100 |
1520-1670 |
Портландцемент М400 |
170 1350-1500 |
0,14 1,25 |
7 |
35 |
Керамзито-золобетон |
М100 |
1270-1470 |
Портландцемент М400 |
170 600-700 |
0,14 0,87 |
8 |
35 |
Золопесча-ный бетон |
М100 |
1710-1780 |
Портландцемент М400 |
200 |
0,16 |
9 |
35 |
Перлитобетон на кварцевом песке |
М100 |
1340-1355 |
Портландцемент М400 |
370 170-185 |
0,3 0,85 |
10 |
25 |
Бетон на щебне из туфа |
М75 |
1220-1345 |
Портландцемент М400 |
220 1000-1125 |
0,18 1,25 |
11 |
25 (сплош-ной камень) |
Опилкобетон на кварцевом песке |
М35 |
1090-1115 |
Портландцемент М400 |
300 150-175 |
0,24 1,25 |
12 |
25 (сплош-ной камень) |
Опилкозо-лобетон |
М35 |
780-910 |
Портландцемент М400 |
250 150-175 |
0,20 1,25 |
Примечание: Составы подобраны с использованием сырьевых материалов, отвечающих требованиям ГОСТ; при наличии материалов с другими характеристиками требуется корректировка составов. |
Общие рекомендации по изготовлению блоков
Подбор состава бетонной смесиИзготовитель должен творчески подойти к вопросу подбора бетонной смеси и самостоятельно найти ее оптимальный состав, руководствуясь приведенными ниже рекомендациями и готовыми рецептами. Процесс поиска оптимального состава не является сложным и не требует особой квалификации. В его основе лежит перебор различных комбинаций имеющихся в распоряжении изготовителя компонентов и испытания изготовленных из них образцов изделий. На основании большого опыта работы и наблюдений за работой вибропрессующих линий, можно утверждать, что качество получаемых на них изделий зависит на 70% от качества смеси и на 30% от умения оператора, работающего за пультом управления вибропрессом.
Во-первых, изготовленные из смеси камни должны иметь необходимую прочность. Этот параметр зависит от количества введенного в смесь вяжущего и соотношения между собой мелкой и крупной фракции заполнителя. Во-вторых, смесь должна хорошо формоваться в матрице, что зависит от ее влажности и опять от соотношения мелкой и крупной фракции. Смесь должна быть в меру сыпучей для быстрого и полного заполнения матрицы и в меру липкой для удержания формы изделия после его выпрессовки из матрицы.
В связи с тем, что для получения необходимой прочности изделий смесь должна содержать вполне определенное количество вяжущего (например, при изготовлении стеновых камней количество цемента марки 400 обычно составляет 200. ..230 кг на один кубический метр смеси), изготовитель не может в широких пределах влиять на смесь меняя содержание вяжущего. В его распоряжении остается только подбор правильного соотношения мелкой и крупной фракции заполнителя и количества воды. В процессе этого подбора изготовитель может столкнуться с рядом противоречий. Например, сочетание мелкого и крупного заполнителя, которое позволяет достичь максимальной прочности, может привести к слишком грубой структуре и неровной поверхности изделий, что затруднит их реализацию, а состав смеси, который обеспечивает наивысшие теплоизоляционные свойства, может не обеспечивать наилучшие прочностные характеристики изделий. Такие противоречия изготовитель должен разрешать самостоятельно. Соотношение мелкого и крупного заполнителя, пропорция между заполнителем и вяжущим обычно являются компромиссом, которым изготовитель обеспечивает наиболее важные для него характеристики изделий в ущерб каких-либо других характеристик, с его точки зрения второстепенных.
Один изготовитель в качестве главной характеристики может выбрать прочность, а другой — товарный вид изделия или его теплозащитные свойства.
Точное количество каждого компонента может быть установлено только опытным путем с помощью изготовления и лабораторных испытаний пробных партий изделий. Предварительная оценка прочности смеси может быть сделана без лабораторных испытаний: если внешний вид поверхностей и ребер изделий является удовлетворительным и при этом у изделий через 2…3 суток ребра и углы не обламываются от слабых ударов, можно считать, что состав смеси подобран правильно.
Влияние крупного заполнителяВообще говоря, чем крупнее заполнитель, тем выше прочность изделия. Крупный заполнитель образует внутри изделия жесткий пространственный скелет, который воспринимает основные эксплуатационные нагрузки изделия. Крупный заполнитель повышает прочность изделия на сжатие, увеличивает его долговечность, уменьшает ползучесть, усадку и расход цемента. Однако все эти положительные свойства крупного заполнителя могут проявиться только в том случае, если в смеси присутствует достаточное количество мелких частиц, роль которых заключается в заполнении пространства между крупными зернами и исключении их взаимного сдвига при сжатии изделия. Максимальную прочность бетона при заданном количестве вяжущего обеспечивает такой состав заполнителя, при котором крупные зерна заполняют весь объем изделия и касаются друг друга, между крупными зернами, контактируя с ними и друг с другом, располагаются зерна чуть меньшего размера, оставшееся пространство заполнено еще более мелкими частицами и т.д. до полного заполнения всего объема изделия. На практике такой идеальный состав получать трудно и необязательно. Достаточно обеспечить наличие в смеси двух основных фракций: крупной, размером 5…15 мм и мелкой размером от пыли до 2 мм. Содержание крупной фракции должно составлять 30-60%. В случае использования материала, содержащего меньшее количество крупных зерен, требуется большее количество цемента или гипса, т.
к. увеличивается общая цементируемая площадь заполнителя.
Если при выпрессовке из матрицы в изделиях появляются большие трещины, то вероятнее всего это происходит из-за недостатка мелких частиц в мелком заполнителе. Недостаток мелких частиц может объясняться, например, вымыванием большого количества очень мелкого песка при промывании мелкого заполнителя. Смесь, имеющая недостаток мелких частиц, менее пластична, склонна образовывать трещины, плохо слипается и формуется. Недостаток мелких частиц может быть устранен добавлением в смесь небольшого количества мелкого песка, каменной пыли или увеличением содержания воздухововлекающих добавок. При этом следует учитывать, что избыток в смеси очень мелких частиц и пыли приводит к потере прочности изделия или к увеличению его себестоимости за счет вынужденного увеличения количества вяжущего (до 20…40%), необходимого для достижения заданной прочности изделий. Необходимость в увеличении содержания вяжущего объясняется следующим. Для получения прочного бетона вяжущее должно покрыть тонким слоем каждую частицу заполнителя. В процессе схватывания бетона покрытые вяжущим частицы срастаются друг с другом и образуется прочное монолитное изделие. Если мелкой фракции слишком много и, кроме того, в ее составе много пыли, то общая площадь частиц заполнителя становится настолько велика, что обычной дозы цемента не хватает на обволакивание всех частиц заполнителя. В бетоне появляются участки не содержащие цемента и прочность изделия снижается.
При изготовлении изделий методом вибропрессования бетонная смесь требует гораздо меньше воды, чем при обычной заливке бетона в формы. Известно, что слишком большое количество воды в бетоне уменьшает его прочность. Для полного прохождения реакции схватывания достаточно всего 15…20% воды от массы цемента и 40…60% от массы гипса. Бетонная смесь с таким содержанием воды является почти сухой. Метод вибропрессования позволяет применять смеси с минимальным количеством воды, так как заполнение матрицы происходит за счет вибрации и давления на смесь, а не за счет текучести смеси, как в обычном жидком бетоне. Фактически вибропрессование является индустриальным вариантом детской песочницы, в которой с помощью уплотнения влажного песка в игрушечной форме получаются «пирожки». Влажность бетонной смеси и ее липкость должны быть примерно такими же, как у песка в детской песочнице. При перемешивании недостаточно влажной смеси частицы вяжущего плохо прилипают к частицам заполнителя, отформованные из слишком сухой смеси изделия осыпаются при выпрессовке из матрицы или в них появляются трещины. Избыток воды также оказывает отрицательное воздействие на процесс изготовления изделий. Переувлажненная смесь становится слишком липкой. Это затрудняет заполнение матрицы вибропресса и вызывает разрушение верхней плоскости отформованных изделий из-за прилипания смеси к пуансону при его подъеме. Кроме того, выпрессованные изделия оплывают на поддоне, приобретая бочкообразную форму и теряя точность размеров.
При изготовлении стеновых камней оптимальным является такое количество воды в смеси, при котором поверхность выпрессованных из матрицы камней имеет сухой вид, но при перемещении поддонов от стола вибропресса к стеллажу накопителя в изделиях не появляются трещины. Опытные операторы обычно легко оценивают качество смеси для всех изделий визуально, по ее внешнему виду в работающем смесителе. В процессе работы оператор смесителя может останавливать его для оценки влажности смеси на ощупь, путем сильного сжатия ее в руке. Если при этом получается не рассыпающийся плотный комок без выступающей влаги и при затирании его поверхности каким-либо гладким металлическим предметом получается гладкая, блестящая, влажная поверхность, то количество воды подобрано правильно.
Приготовление бетонной смеси необходимо осуществлять в соответствии с требованиями СНиП 3.03.09.01-85.
Перемешивание смеси играет важную роль в получении прочного бетона. Цель перемешивания состоит в покрытии каждой частицы заполнителя тонкой пленкой вяжущего. Для приготовления бетонной смеси следует использовать смесители принудительного действия, соответствующие ГОСТ 16349-85. Объем замеса должен быть не более 0,75 и не менее 0,4 полезной емкости смесителя. Продолжительность приготовления бетонных смесей, за исключением смесей с древесным заполнителем должна составлять 4-5 мин., в том числе 2-3 мин. после введения воды затворения. Время, прошедшее от приготовления бетонной смеси до ее использования, как правило, не должно превышать более 40 мин., для смесей с добавкой ускорителя твердения – 20 мин.
При приготовлении опилкобетона или арболита в бетоносмеситель предварительно загружают древесный заполнитель, добавляют раствор химических добавок и перемешивают в течение 1-1,5 мин. Затем загружают песок, (золу), цемент и перемешивают в течение 1 мин., после чего заливают остальную воду и окончательно перемешивают смесь в течение 2-3 минут. При изготовлении перлитобетона в бетоносмеситель предварительно загружают перлит, затем остальные материалы и воду.
Изготовление форм для керамзитобетонных блоков
Изготовление форм для керамзитобетонных блоков – важный этап изготовления стенового материала. От качества формы зависит качество стеновых камней, в том числе параллельность граней, выдерживание нужных углов и размеров.
Керамзитобетонные блоки, как известно, изготавливаются вибропрессованием, поэтому формы должны быть устойчивыми к вибрации.
Особенности форм для керамзитобетонных блоков
Основные требования к формам, в которых изготавливаются керамзитоблоки:
- надежность, механическая прочность;
- устойчивость к воздействию воды, цемента и других веществ;
- легкость выемки изделия;
- долговечность.
В основном формы для керамзитоблоков изготавливают из дерева, металла или из пластика. Все эти материалы имеют свои достоинства и недостатки.
Деревянные формы. Годятся только для изготовления небольших партий керамзитобетонных блоков, так как размокают от воды и разрушаются. Металлические формы. Металл – материал, позволяющий создавать сложные эффективные конструкции. Касается это и пресс-форм.
Они бывают:
- кассетными, в которых дно неподвижно, а бортики откидываются для удобства выемки изделия;
- разборными, для удобства транспортировки разбирающимися на несколько листов;
- комбинированные, со специальным устройством для выемки блока.
Пластиковые формы. Они изготавливаются на специальном оборудовании для переработки пластмасс. Обладают хорошими механическими и эксплуатационными характеристиками.
Заключение
Можно самостоятельно изготовить формы для керамзитоблоков из дерева или из металла. Для изготовления таких форм из металлических листов понадобятся навыки сварщика и умение работать с металлообрабатывающим оборудованием.
Похожие материалы:
Производство керамзитобетонных блоков своими руками: станки, оборудование (+видео)
Простота изготовления и дешевизна компонентов позволяют освоить производство керамзитобетонных блоков самостоятельно. В состав керамзитобетона входит глиняный гранулированный керамзит, который после обжига становится очень легким и прочным. К тому же гранулы керамзита обладают низкой способностью к впитыванию влаги, поэтому данный строительный материал идеально подходит для возведения стен и пола в слабо отапливаемых помещениях. Высокая теплопроводность керамзитобетона и звукоизоляция делают его востребованным материалом для строительства жилых домов и хозяйственных построек. Цена на керамзитобетонные монтажные блоки приблизительно на треть получается ниже стоимости кирпича (при равных условиях для возведения определенного типа здания).
Фото: дом из керамзитобетонных блоков
Как правильно приготовить смесь для производства блоков
Чтобы приготовить керамзитобетонные блоки своими руками, необходимо знать, каким образом составляются пропорции для состава. Данный материал считается абсолютно безопасным для человека, поскольку в состав керамзитобетона входят только натуральные компоненты. Рекомендуется для изготовления использовать гранулы керамзита, не превышающие в диаметре 1 см. Этот стройматериал используют для приготовления пола в качестве утеплителя.
Простота изготовления керамзитобетонных строительных блоков открывает возможность для масштабного кустарного производства, поэтому можно сделать блоки и самому. Это связано с тем, что несоблюдение пропорций компонентов и их экономия приводит к низкому качеству готовой продукции (цена не соответствует качеству блоков). Помимо этого необходимо использовать песок с улучшенной зернистостью (обогащенный), поскольку применение речного песка может сказаться на прочности материала.
Технология приготовления рабочей смеси представляет собой смешивание всех ее компонентов в определенной последовательности и с точным соблюдением пропорций. Для этого необходимо взять:
- портландцемент (рекомендуется марка М-400), который по технологии исполняет роль связующего компонента – 1 часть;
- вода – 1 часть;
- керамзит мелкофракционный – в пропорции 8 частей;
- песок (обогащенный) – 3 части.
Чтобы приготовить керамзитобетонные блоки своими руками, необходимо знать, что 100-килограммовая приготовленная смесь может быть использована для производства 10 блоков. По ГОСТу размер керамзитобетонного блока составляет 190*390*188 мм. Вес керамзитобетонного блока может колебаться от 7 до 20 кг, в зависимости от объема пустот. В состав керамзитобетона по технологии добавляют древесную омыленную смолу, что позволяет увеличить устойчивость материала к воздействию низких температур, а также лигносульфонат для лучшей связки компонентов состава.
Стандартный размер керамзитобетонного блока
Совет прораба: для улучшения пластических характеристик керамзитобетонных монтажных блоков, в рабочий состав можно добавить 1 ст. ложку обычного стирального порошка.
Какое потребуется оборудование
Чтобы самостоятельно сделать керамзитобетонные монтажные блоки, потребуется использование определенного оборудования. Цена его невелика, поэтому вибрационный станок можно приобрести для личного пользования. Также можно использовать арендные станки и оборудование, цена которого обговаривается на определенный срок. Станок позволяет в специальной форме равномерно распределить массу рабочего состава для того, чтобы готовое изделие получилось максимально прочным. Есть модели, которые оснащаются пустотообразователями, благодаря которым можно приготовить полые блоки (без них получаются цельные).
Также потребуется электрическая бетономешалка, в которую необходимо в определенных пропорциях поместить все компоненты, где они тщательно перемешиваются (бетономешалку необходимо неподвижно установить на полу). Для получения блоков потребуются специальные формы, которые можно приобрести. Цена на них невысока, к тому же можно выбрать модели с различной конфигурацией полостей. Формы можно сделать и самостоятельно, для чего используются деревянные доски и жесть.
Изготовление формы для керамзитобетонных блоков
Совет прораба: покупки оборудования можно избежать. Для этого производится ручное замешивание рабочей смеси с обязательным соблюдением пропорций. Можно обойтись и без вибростанка, для чего залитый состав тщательно утрамбовывают, а затем выравнивают по границе формы. Более подробную информацию о ручном производстве блоков можно посмотреть в видео.
Особенности технологии самостоятельного приготовления керамзитобетона
Наверняка Вы неоднократно задумывались над тем, для чего нужны пустоты внутри керамзитобетонных монтажных блоков. Несложно догадаться, что в первую очередь они необходимы для существенного снижения веса изделия. К тому же пустоты при кладке образуют так называемые воздушные колодцы, которые уменьшают теплопроводность.
Рекомендуется тщательно перемешивать раствор до тех пор, пока не получится мягкая пластическая масса. После ее приготовления можно приступать к заполнению форм, в которых раствор будет застывать в течение 24 часов. Полное время застывания блоков составляет 3 недели (28 дней). Спустя сутки после застывания блоки укладывают на поддонах на поверхности пола.
Нельзя допускать прямого попадания лучей солнечного света на готовые изделия. Поэтому в период полного застывания рекомендуется сложенные на полу блоки периодически поливать водой, а затем укрывать полиэтиленовой пленкой. Использовать готовые изделия можно будет спустя месяц, когда цемент полностью наберет свою крепость.
Видео
Производство керамзитобетонных блоков на заводе компании ООО «Калита»
ООО «Калита», используя современные технологии, профессионально занимается изготовлением строительных материалов с 2000 года. В это время заработал наш завод керамзитобетонных блоков в г. Алексин Тульской области. На сегодняшний день изделия производятся на двух высокопроизводительных линиях Златоустовского производства Рифей-Универсал.
Являясь одним из лидеров по производству сертифицированных керамзитобетонных блоков в центральном регионе, предприятие выпускает широкий ассортимент продукции: более 10 видов наименований товарных единиц с объемом более 140 м3 блоков.
На данном этапе развития строительной отрасли производство керамзитобетонных блоков с точным соответствием ГОСТ 6133-99 осуществляется методом полусухого вибропрессования.
Технологические этапы производства керамзитоблоков:
- Смешивание компонентов в бетономешалке.
- Формовка изделий на вибрационно-прессовальном оборудовании.
- Сушка блоков.
- Складирование готовой продукции.
- Транспортировка блоков заказчику.
В производственный цех подается исходное сырье: песок, керамзит мелкой фракции, цемент. Все составляющие обладают регламентируемыми ГОСТ характеристиками.
Подача пескаОт процентного содержания того или иного компонента зависят свойства готовой продукции.
Благодаря соблюдению оптимальных пропорций получаются универсальные керамзитобетонные блоки с уникальными характеристиками: прочные, легкие, с высокими звуко- и теплоизоляционными качествами.
Далее происходит смешивание компонентов бетонной смеси.
Замес керамзитобетонаПоследовательность поступления в бетоносмесительную установку исходных компонентов такова: первой в емкость поступает вода, затем идет засыпка керамзитового гравия, далее – цемента, и только в последнюю очередь – песка. Автоматическая поддержка уровня воды обеспечивается поплавковым механизмом.
Выход блоковПриготовленная растворная смесь отправляется на формовку. На этом этапе происходит наполнение рабочей смесью формообразующей оснастки.
Непосредственно изготовление керамзитобетонных блоков начинается на специальном оборудовании – вибрационно-прессовальном станке. Форму конечного продукта создают стальные пластины-матрицы, в которые и засыпают приготовленную керамзитобетонную смесь. Процесс вибропрессования исключает возможность образования пространства в стенках изделий, обеспечивая плотную укладку керамзито-бетонной смеси в форму. Давление в гидросистеме пресса создается насосной установкой.
От того, какие матрицы были использованы, керамзитобетонные блоки могут быть различных размеров и видов: полнотелые или пустотелые.
В результате процесса вибропрессования керамзитобетонная смесь уплотняется, будущая продукция приобретает рекомендуемые ГОСТ физико-механические характеристики и форму. Внутри устройства находится ровнитель, который снимает с блоков излишки растворной смеси, убирает неровности.
В зону распалубки блоки из керамзитобетона перемещаются после отвердевания.
Камера сушкиПосле завершения этапа формовки вместе со стальной пластиной блоки перемещают в сушильную камеру. Для окончательного затвердевания готовых изделий требуется определенное время.
ЦехПосле завершения процесса сушки готовые изделия укладывают на специальные товарные поддоны, на которых они хранятся и транспортируются заказчику
Складирование готовой продукцииЗаводские условия позволяют нам работать в течение всего года. Стабильное качество сертифицированной продукции обеспечивается за счет комплексного оборудования и точного соблюдения всех звеньев технологического процесса.
Мы гордимся не только эффективной технологией производства керамзитоблоков – отправка продукции осуществляется собственным большегрузным автотранспортом. Оперативно, точно в оговоренный срок керамзитовые блоки доставляются на объект заказчика. Автопарк состоит из техники не старше пяти лет. Также для вашего удобства компания предоставляет услугу доставки грузов манипулятором.
Отправка блоков заказчикуООО «Калита» имеет собственную лабораторию, контроль качества выпускаемой продукции ежедневно проводится на каждом производственном этапе. Независимые специалисты ОАО «Гурово-Бетон» контролируют качество блоков еженедельно. Блоки из керамзитобетона производства «Калита» рекомендованы для применения во всех областях строительства без ограничения, о чем свидетельствует сертификат Тульской областной СЭС.
Технология изготовление керамзитобетонных блоков. Плюсы и минусы керамзитобетонных блоков.
Технология изготовление керамзитобетонных блоков. Плюсы и минусы керамзитобетонных блоков.
Технология производства керамзитобетонных блоков заключается в процессе вибропрессования нескольких составляющих, а именно цемента, воды и керамзита. Смешанные в определенной пропорции материалы поступают на формовку, где и приобретают свою форму и размеры, благодаря оборудованию для изготовления керамзитобетонных блоков, а именно вибропрессу и камере затвердения. После ни хитрых манипуляций, сформированным и затвердевшим блокам дают просохнуть и укладывают на поддоны, на которых он и храниться на складах до момента приобретения.
Не стоит путать технологию изготовления керамзитобетонных блоков с блоками из пенобетона. Их так же часто используют при строительстве коттеджей, но эти два материала не имеют между собой ничего общего. Пенобетон может быть и хорош, но не для нашего климата и по сравнению с ним, технологии производства керамзитобетонных блоков позволяют выпускать на рынок качественный и экологически чистый товар, не подверженный образованию конденсата из-за разницы температур внутри помещений и улицы. Кроме этого, керамзитобетонные блоки, сами по себе сохраняют комфортную температуру внутри помещений, а стены коттеджей из пенобетона приходить дополнительно утеплять, что ведет к дополнительным финансовым затратам на строительство. Из-за перепада температур (от -30 зимой до +30 летом) и уровня влажности, пенобетон начинает осыпаться. Керамзитобетонные блоки с легкостью выдерживают все капризы погоды наших широт.
Керамзитобетонные блоки, отлаживают влагосодержание воздуха в жилом помещении. Все постройки из керамзитобетонных блоков в основном вечны и не нуждаются в особенном уходе. Материал не сгнивает, не горит и не ржавеет, имеющие одновременно положительные качества дерева и камня.
Преимущества керамзитобетонных блоков перед кирпичом:- Обособленный вес;
- Значительно меньше содержание цемента;
- Один блок в состоянии заменить семи кирпичей;
- В течение суток реально уложить объем в три раза больше, по сравнению с кирпичом;
- Экологические свойства ничем не уступают;
- Отличная теплоизоляция.
Оборудование для керамзитобетонных блоков в основном представляет собой бетономешалку, и специальный станок, для образования нужной формы. Керамзитобетонные блоки и оборудование для их изготовления должны соответствовать всем техническим и санитарным требованиям.
Для изготовления керамзит блоков раствор бетона, следует готовить по нижеследующим пропорциям: песок – 3 порции, вода примерно от 0,8 до 1 порции, цемент – 1 порция и 6 порций керамзита. Все это смешивается и помещается в специальную форму. Для того чтобы блок был плотным, пока смесь не застыла, ее помещают на вибростол, с помощью которого избавляются от лишних воздушных пузырьков. После всех этих манипуляций сформировавшийся блок вынимается из формы и переносится в камеру, в которой под влиянием температуры находится около 2 суток.
Основной вопрос, возникающий при строительстве любого здания, связан с выбором материала, его качеством и стоимостью. Строительство домов из керамзитобетонных блоков все большее применение в связи с характеристиками этого строительного материала.
Актуальность строительства из керамзитобетонных блоков обусловлена значительным снижением затрат, связанных с процессом возведения здания и его эксплуатации. Вместе с тем, материал имеет множеством преимуществ, таких как влагостойкость, тепло и звукоизоляция, надежность, паропроницаемость, малый вес.
Еще одним преимуществом строительства домов из керамзитобетонных блоков является достаточно высокая скорость кладки, по сравнению с любыми другими видами материалов, что позволяет экономить время при возведении здания.
Постройка стен и перегородок из керамзитобетона не требует особых инженерных решений, в связи с этим строительство из керамзитобетонных блоков снижает трудозатраты застройщика. Материал хорошо сочетается с металлоконструкциями, железобетонными изделиями, имеет небольшой вес, что значительно упрощает процесс закладки фундамента. При этом, дом из керамзитобетонных блоков не теряет функциональные и эстетические свойства.
Керамзитобетон обладает высокой степенью паропроницаемости. В связи с этим, в доме создается благоприятный микроклимат и обеспечивается нормальная влажность воздуха.
Благодаря морозоустойчивости материала, дом из керамзитобетонных блоков не уязвим перед низкими температурами. Это одно из главных достоинств керамзитобетона. Для обеспечения нормального сохранения тепла в помещении, достаточно укладки блоков с внешней стороны здания в один слой.
Плюсы и минусы керамзитобетонных блоков.Они активно используются в строительстве, однако, как и большинство других стройматериалов, не лишены как достоинств, так и недостатков.
Керамзитобетонные блоки плюсы:
- При производстве блоков используются натуральные природные материалы, поэтому это довольно экологичный стройматериал.
- Высокая прочность.
- Теплопроводность и звукоизоляция значительно выше, чем у бетона, а стоимость при этом – ниже.
- Влагоустойчивость — остаются прочными даже при химическом воздействии и агрессивной окружающей среде.
- Вес блоков значительно снижен за счет достаточно мелкого гравия, входящего в состав.
- Физические и механические свойства изделий из керамзитобетона в разы превышают характеристики блоков, изготовленных из ячеистого бетона.
Минусы керамзитобетонных блоков:
Такие блоки более хрупкие по сравнению с кирпичом и имеют пористую структуру, следовательно, отсюда вытекают другие минусы керамзитобетонных блоков, такие как снижение прочности и морозоустойчивости. Тем не менее, керамзитобетонные блоки массово применяются в строительстве малоэтажных зданий.
Коллектив компании
«Оранж Строй»
Керамзитобетонные блоки своими руками: состав, пропорции
Изготовить строительные керамзитобетонные блоки своими руками возможно. Для этого следует строго соблюдать установленные пропорции смеси. А чтобы готовое изделие соответствовало заявленным стандартам ГОСТа 33126–2014, для придания ему прочности и надежности рекомендуется использовать специальный станок для изготовления такого вида стройматериала.
Посмотреть «ГОСТ 33126-2014» или cкачать в PDF (230 KB)
Керамзитоблоки по своим свойствам не уступают бетонными, только в них используется не щебень, а керамзит.
Характеристики
Блочные элементы из керамзитобетона изготавливаются из бетона различных марок, все зависит от того, какими свойствами должно обладать изделие и какова сфера его применения. Бетон с наполнителем из керамзита бывает таких разновидностей:
Материал по структуре может быть уплотненным, крупнопористым, поризованным.- крупнопористый;
- поризованный;
- уплотненный.
Блоки используются для возведения конструкций различного предназначения. Учитывая сферу применения, различают такие виды этого стройматериала:
- конструктивный;
- конструктивно-теплоизоляционный;
- теплоизоляционный.
Если состав и указанные пропорции для керамзитобетонных блоков соблюдены строго, получится качественный материал, обладающий такими достоинствами:
- надежная теплоизоляция;
- увеличенная прочность;
- высокий коэффициент морозостойкости;
- малый уровень расширения и деформации;
- экологическая чистота и безопасность;
- небольшая масса;
- простота монтажа и обработки, изделие можно резать обычной ножовкой.
Но как и у любого вида стройматериала, у бетона с керамзитом есть свои недостатки, основные из которых:
- Невозможность возводить многоэтажные конструкции ввиду повышенной пористости структуры блока.
- Узкая сфера применения керамзитобетона.
- Необходимость в дополнительной наружной отделке, потому что под влиянием негативных погодных условий и механического воздействия поверхность склонна к деформации и разрушению.
Состав раствора
В процессе изготовления керамзитобетонных блочных элементов важно использовать качественное сырье, используемое в строго указанных нормативными документами пропорциях. В состав керамзитобетона входят такие компоненты:
Материал готовится из компонентов, соотносящихся между собой в нужной пропорции.- Цемент. Чтобы сделать керамзитобетон прочным и качественным, специалисты советуют добавлять в раствор цемент маркой не ниже М400.
- Керамзит.
Материал, используемый вместо щебня, отличающийся пористой структурой и небольшим весом. Для производства керамзитоблоков используется фракция 5—10 мм.
- Песок. Не должен иметь примесей глины и чернозема. Используется в качестве наполнителя, создающего скелет блочного элемента. Допустимые фракции песка — средняя и крупная.
- Вода. Изделие выйдет более качественным, если вода используется очищенной.
Для увеличения пластичных свойств керамзитоблока разрешено добавлять в массу средство для мытья посуды либо жидкий порошок. Химическая реакция между компонентами способствует образованию внутри воздушных микропор. Благодаря такому эффекту повышается коэффициент влаго- и морозоустойчивости, что положительно влияет на качество готового изделия.
Оборудование и инструменты
При постоянной необходимости в изготовлении изделий стоит купить оборудование, а не мучиться с подручными средствами.Если средства позволяют и решено наладить беспрерывное производство материала на керамзите, можно купить специальное оборудование для производства керамзитобетонных блоков. Сюда входит вибростанок, имеющий ровное основание. Вибрации на таком устройстве строго отрегулированы, благодаря чему во время производства готовые блоки будут полностью соответствовать заявленным физико-техническим характеристикам.
Чтобы приготовить качественный, однородный раствор, потребуется бетоносмеситель, минимальный объем бункера должен быть 130 л. Помимо спецоборудования, понадобятся такие инструменты:
- лопата;
- ведро;
- мастерок;
- металлический лист для подложки;
- деревянные доски для опалубки или готовые формы.
Технология производства своими руками
Формы и опалубка
Несложно из досок соорудить опалубку для изготовления изделий.Чтобы изделие получилось нужных размеров, необходимо подготовить формы для керамзитобетонных блоков. Для этого понадобятся деревянные доски и металлический лист-подкладка. С помощью рулетки делается разметка параметров формы, далее ножовкой из доски вырезаются поддон и 2 части, соединенные буквой «Г». Элементы соединяются уголками, внутреннюю часть формы рекомендуется оббить тонким металлическим листом, чтобы готовое изделие можно было легко вынуть. Если это невозможно, тогда нужно перед заливкой смазать внутренние стенки опалубки техническим маслом.
Пропорции раствора
Чтобы изготовить прочные блоки для стен, рекомендуется соблюдать пропорции керамзитобетона, указанные в частях от общей массы на 1 м куб. готового раствора. Данные представлены в таблице:
Компоненты | Пропорции на 1 м³, части |
Портландцемент класса М400 | 1 |
Керамзит | 6—8 |
Песок | 2 |
Вода | 0,8—1 |
Моющее средство или стиральный порошок | 1 |
Важно не только соблюдать рецепт приготовления керамзитобетонной смеси, но и соблюдать последовательность введения компонентов:
Вода должна оказаться в бетономешалке первой.
- Сначала в бетономешалку заливается вода с разведенным в ней моющим средством.
- Далее засыпается керамзит, после чего все перемешивается.
- Затем добавляется цемент и в конце песок. Масса тщательно перемешивается на протяжении 2—3 мин.
Отлив блоков
Отливать элементы необходимо в предварительно подготовленные и смазанные машинным маслом формы, установленные на максимально ровной поверхности. В помещении, где происходит заливка, не должно быть лишней влаги, оптимальная температура воздуха — 15—18 °C. Так как керамзит легкий и после заливки сразу всплывает, пока масса не схватится, необходимо гранулы утрамбовать внутрь блока. Для этого лучше использовать вибрационный станок для производства керамзитобетонных блоков. Но если оборудования нет, можно воспользоваться широким бруском, которым массу трамбуют до тех пор, пока на поверхности не образуется «цементное молоко».
После заливки в формы смесь обязательно нужно утрамбовать.Как происходит сушка?
Через сутки утрамбованное изделие можно извлекать из опалубки, затем поместить на поддон и дать подсохнуть еще 2—3 дня. Однако, чтобы изготовленный керамзитобетон своими руками получился прочным и соответствовал заявленным характеристикам, специалисты советуют дать ему вылежаться еще месяц. По истечении этого времени стройматериал будет полностью готов к применению. Из него можно смело возводить несущие стены построек любого предназначения.
Оборудование для производства керамзитобетонных блоков
Керамзитобетонные блоки весьма востребованный строительный материал, широко использующийся в частном малоэтажном строительстве и при возведении как жилых, так и вспомогательных строений. Множество компаний и частных фирм занимаются производством этого материала, но спрос на него не снижается. В то же время материалы, из которых делают блоки, весьма распространены, технология отработанна годами, а оборудование позволяет провести максимальную автоматизацию труда на производствах любого уровня.
Состав керамзитобетонной смеси
Технические и эксплуатационные характеристики керамзитобетонных блоков, а также пропорции состава регламентирует ГОСТ 6133-99 «Камни бетонные стеновые. Технические условия».
Пропорции компонентов для изготовления керамзитобетонных блоков
В качестве вяжущего вещества в состав рабочей смеси входит портландцемент не ниже марки М400. В процессе производства применять пластифицирующие добавки нецелесообразно. Если необходимо наладить производство блоков с заданными характеристиками влагопоглощения или термостойкости, то в качестве вяжущего используют специальные цементы:
- гидрофобный портландцемент с добавлениями оленковой кислоты и мылонафты;
- алитовый цемент содержащий трехкальциевый силикат и трехкальциевый алюминат.
Использование пуццолановых, шлакопортландцементов или пластифицированных ССБ цементов настоятельно не рекомендуется. Это существенно снижает прочность бетона на ранних стадиях отвердения, ухудшает воздухостойкость и водостойкость.
В качестве крупных заполнителей используется керамзит и керамзитовый гравий. Величина их фракций и технические характеристики материала регламентирует ГОСТ 9757-90 «Гравий, щебень и песок искусственные пористые. Технические условия».
Мелким заполнителем может выступать керамзитовый песок, который получают путем дробления – он обладает большими абсорбционными возможностями, чем обычный песок. Другой тип керамзитового песка получают, обжигая исходное сырье в двух барабанных печах, фракции песка обоих способов получения регламентируются тем же ГОСТ–ом. Однако, в последнее время больше практикуют использование кварцевого песка по ГОСТ 22551-77 «Песок кварцевый, молотые песчаник, кварцит и жильный кварц для стекольной промышленности. Технические условия».
Вода, которую используют в производстве блоков, должна соответствовать параметрам, описанным в ГОСТ 23732-79 «Вода для бетонов и растворов». Кислотность рН должна быть меньше 4, а содержание сульфатов (SO4) более 1% категорически не допускается. Применение морской воды для затворения раствора так же не рекомендуется из-за образования на поверхности готовых изделий высолов (налета из соли).
Производство
На каждом производстве технология изготовления может несколько отличаться от общепринятой в ГОСТе. Это связано с естественным стремлением производителя снизить себестоимость продукции. Для этого в состав рабочей смеси могут добавлять пластификатор для улучшения заполнения формы.
В мелких частных предприятиях для увеличения подвижности смеси в состав добавляют жидкое мыло или клей (силикат), это значительно уменьшает расход воды и снижает время на виброобработку.
Сама технология изготовления, независимо от применяемого оборудования, разделяется на три основных этапа:
1. Подготовка смеси. Обычно, максимальный диаметр керамзита не должен превышать 10 мм. Количество цемента может быть различным в зависимости от предназначения изготавливаемых блоков. Для кладки несущих стен используют больше цемента, он увеличивает прочность конструкции, но существенно снижает теплоизоляционные свойства материала.
Стандартные пропорции для универсальных блоков на 100 кг выглядит так:
- Керамзит крупных фракций – 54,5кг;
- Керамзитовый спекшийся или кварцевый песок – 27,2 кг;
- Портландцемент – 9,21 кг;
- Вода – 9,096 л.
ВАЖНО! При использовании дробленого песка в качестве мелкого наполнителя количество воды необходимое для затворения будет значительно выше. В зависимости от величины фракции до 15 л.
В бетономешалку указанные ингредиенты добавляются в следующем порядке: вода, керамзит, цемент, песок. Перемешивание осуществляется не более 2 минут. На один стандартный блок, имеющий размер 39х19х19 см пойдет 10-11 кг смеси.
2. Формовка. Для этого процесса широко применяется разнообразное ручное и автоматизированное оборудование. Основой процесса является вибрация, с ее помощью смесь, поступившую в форму, быстро уплотняют.
3. Сушка. Формы с блоками должны сушиться на протяжении двух дней. Затем стальные пластины убирают и изделия досушиваются на открытом воздухе, на протяжении 7-10 дней.
Применяемое оборудование
Оборудование, которое используется в производстве керамзитобетонных блоков можно классифицировать по производительности и степени автоматизации.
1. Ручной станок для производства керамзитобетонных блоков. Оптимальный выбор для мелкосерийного производства в домашних условиях.
Пример ручного станка для производства керамзитоблоков
Вибратор простой конструкции крепится к корпусу. Производимые им колебания способствуют быстрому и полному заполнению формы. Может комплектоваться съемными стержнями для образования пустот. При их демонтаже можно изготовить полнотелые блоки для несущих стен двух и трехэтажных домов. В этом случае пропорции смеси будут несколько изменены в сторону увеличения количества цемента. Видео работы ручного вибростанка:
com/v/051Xozpw3Ao?fs=1&hl=ru_RU»>
2. Передвижные станки с высоким уровнем механизации способны значительно снизить себестоимость продукции. Они используют многосекционные формы, имеющие от 4 до 6 матриц. Вибромотор крепится к несущему корпусу станка.
Передвижной станок для изготовления керамзитобетонных блоков
Некоторые модели могут быть оснащены дополнительным прессом для утрамбовывания. Процесс производства выглядит следующим образом:
- Формы заполняются смесью;
- Под воздействием вибрации и давления блоки принимают свою форму;
- Секция из 4-6 блоков опускается на землю, на заранее подготовленную опалубку для просушки;
- Станок перемещается на новое место над новой, пустой секцией опалубки.
Подробное видео о конструкционных особенностях и способе работы на передвижном станке:
youtube.com/v/s_DK-tYDWdQ?fs=1&hl=ru_RU»>
3. Вибростол. Условно состоит из двух частей. Основы – металлической станины, к которой крепится вибродвигатель. Поддон на станине имеет толщину металла до 3 мм и бортики, чтобы установленные формы не соскользнули. На поддон устанавливаются заполненные формы, содержание которого уплотняется вибрацией.
Вибростол
Размещение вибродвигателя снизу и в центре станины значительно повышает эффективность и равномерность распределения вибраций. Такое устройство для изготовления блоков имеет не слишком большую производительность.
4. Вибропресс. Это оборудование высокой сложности. Автоматизированная линия для производства керамзитобетонных блоков, устанавливается на крупных предприятиях.
На фото – вибропресс “Рифей Удар”
В состав производственной линии могут входить:
- конвейер для транспортировки сформованных блоков на просушку;
- ленточный податчик рабочей смеси;
- автоматизированная бетономешалка, способная самостоятельно рассчитать необходимые пропорции.
Видео процесса изготовления на автоматизированной линии:
(PDF) Производство керамзитобетона-заполнителя для легкого бетона из несамовспучивающихся глин
В последнее время постоянно проводятся исследования по производству искусственного легкого заполнителя с использованием отходов. Несмотря на то, что были проведены различные исследования механизма вздутия заполнителя с использованием отходов, существует много недостатков в объяснении существующей теории, поскольку она отличается от керамзитового материала. И нет исследований, предлагающих модель для установления механизма вздутия живота.В этом исследовании были исследованы характеристики существующего керамзита, чтобы установить механизм вспучивания легкого заполнителя с использованием отходов, и было смоделировано оптимальное условие активации вспучивания для вспучивания легкого заполнителя. Изучено физико-химическое состояние сырья и формованных изделий для серийного производства и предотвращения расплавления заполнителя.
Кислая глина, используемая в этом исследовании, представляет собой глинистые минералы, состоящие из монтмориллонита в качестве основной фазы, а минералы монтмориллонита являются подходящими материалами для производства заполнителей из-за удаления кристаллизационной воды при высоких температурах.Большинство керамзитов, используемых в производстве легкого заполнителя, изготовлено из сырья на основе пирофиллита и подходит для объяснения механизма вспучивания существующим керамзитом и подходит для проектирования сырьевой модели легкого заполнителя.
Затем, чтобы исследовать характеристики набухания легкого заполнителя при нормальных условиях спекания, сравнивали механизм набухания искусственного легкого заполнителя в нормальных условиях спекания и в условиях быстрого спекания с использованием кислых глинистых материалов.Экспериментальные результаты показали, что в условиях быстрого спекания черного ядра не наблюдалось. И при нормальных условиях спекания плотность достигала пика при 1150 ℃, а при нормальных условиях спекания было три зоны в зависимости от времени спекания независимо от входной температуры.
Ⅰ. Участок, где плотность увеличивается по мере увеличения времени спекания
становится длиннее. (зона спекания)
Ⅱ. На участке, где плотность резко снижается при
время спекания увеличивается. (зона активации вздутия живота)
Ⅲ.На участке, где плотность постепенно снижается по мере
время подъема температуры увеличивается. (зона перепекания)
Когда время спекания составляло менее 60 минут при температуре на входе 300 ℃, плотность увеличивалась, и заполнитель спекался, поскольку время спекания увеличивалось.
Наблюдалась оптимальная зона активации вспучивания, в которой плотность резко уменьшалась при времени спекания 210 минут. Когда время спекания превышало 210 мин, плотность постепенно уменьшалась, и этот участок представлял собой зону переспекания.Независимо от температуры инъекции появлялась зона активации вздутия живота. Чтобы оптимизировать вздутие заполнителя, необходимо провести спекание на этом участке.
Чтобы найти оптимальные условия процесса спекания для контроля оптимальной зоны активации вздутия легкого заполнителя, каждый участок процесса нагрева был разделен на комнатную температуру до 300 ℃, от 300 ℃ до 600 ℃, от 600 до 900 ℃, от 900 до 1200 ℃. ℃, 1200 ℃ соответственно. Экспериментальное время составляло 10-40 минут, и измерялась плотность заполнителя и наблюдались поры.Время в секции сушки и предварительного нагрева (комнатная температура ∼600℃) не повлияло на вздутие заполнителя. Секция прокаливания (от 900 ℃ до 1200 ℃) короткая, чем дольше время выдержки при 1200 ℃, тем активнее вздутие живота и легче.
При более высоких температурах, чем температура начала вздутия, чем выше температура, тем ниже плотность конечного заполнителя. Переменными, оказывающими наибольшее влияние на активацию легкого заполнителя, были температура спекания и время выдержки в сечении.Тенденция экспериментальных результатов, предсказанных методом Тагучи, хорошо согласуется с фактическими результатами измерений, благодаря этому эксперименту удалось установить единичный процесс спекания для оптимизации условий активации вздутия. Чтобы подтвердить применимость оптимального единичного процесса и механизма вспенивания в фактическом процессе массового производства, была изучена пригодность пилотной вращающейся печи. Когда легкий заполнитель производился с использованием только кислой глины, его сплавляли во вращающейся печи перед вздутием.Чтобы найти зону активации вздутия, которая может предотвратить плавление, были добавлены Fe2O3 и углерод, чтобы вызвать механизм вздутия соединения с черным ядром, и был подтвержден оптимальный химический состав для вздутия легкого заполнителя.
Чтобы понять влияние образования давления внутри заполнителя на вспучивание и найти подходящий метод формования для массового производства, были исследованы характеристики вспучивания заполнителя и изменение температуры активации вспучивания путем изменения метода формования.И мы подтвердили возможность массового производства с использованием экспериментальной вращающейся печи. Оптимальное содержание добавок составляло 8~13 мас.% Fe2O3 и 2~3 мас.% углерода. При содержании указанных добавок механизм пенообразования черным ядром работал в широком диапазоне, снижая температуру вспучивания. Плотность неспеченных тел различалась в зависимости от способа формования. Размер пор 1 мкм был измерен очень низким в сыром теле, сформированном экструдером и компрессионным формованием. По этой причине можно обеспечить более высокое внутреннее давление, необходимое для набухания сырца, формируемого экструдером, и, в конечном счете, набухание заполнителя при более низкой температуре.Было подтверждено, что путем разработки рецептуры с оптимальной комбинацией, как описано выше, и образования агрегатов с использованием экструдера температура активации пенообразования была снижена, а образование сплавления во вращающейся печи было предотвращено.
Поскольку температура активации вздутия снижается, можно также ожидать эффекта энергосбережения.
Благодаря этому исследованию было установлено, что оптимальные технологические параметры по химическому составу сырья, формованию сырца, сушке, предварительному нагреву, прокалке и прокаливанию сырья для вспучивания легкого заполнителя были подтверждены.Я надеюсь, что это исследование будет использовано в качестве важной модели для разработки всего процесса производства легких заполнителей.
Строительные блоки | Кирпич строительный
Керамзитовый заполнитель (ECA ® ) Легкий строительный кирпичный блок
Блоки из керамзитобетона(ECA ® ) представляют собой кладочные блоки, изготовленные с использованием керамзитобетона (ECA ® ) , золы-уноса класса F, и цемента .Они используются для кладки ненесущих стен.
После применения высокопроизводительной инновационной технологии производства и процесса пост-отверждения керамзитобетонный заполнитель (ECA ®) BLOCKS приобретает превосходные свойства материала.
Он также предлагает без уменьшенной усадки и превосходную огнестойкость и химическую стойкость, добавляя к ряду преимуществ, включая долговечность, универсальность, скорость и простоту использования, а также экономическую выгоду и экологические соображения.
Ссылка на онлайн-видео : Нажмите здесь, чтобы посмотреть видео
Керамзитовый заполнитель (ECA ® ) Строительный кирпичный блок доступен в 2 размерах
Размеры: 600 X 200 X 225 мм (дюймы: 24 дюйма X 8 дюймов X 9 дюймов) — 1 CMT: 36 блоков 9 дюймов ) — 1 CMT: 83 количества 4-дюймовых блоков
Мы часто видим, что у клиентов возникают вопросы перед окончательной доработкой строительных материалов или при поиске поставщиков легкобетонных блоков.Общие вопросы, которые приходят в голову при выборе легкобетонных блоков для их строительства: сколько стоят бетонные блоки? Или каков размер бетонного строительного блока? Есть ли в их районе поставщики легкобетонных блоков? Или есть разница между шлакоблоком и бетонным блоком? Или есть поставщик с дешевыми бетонными строительными блоками для продажи?
Долгое ожидание упускает из виду монолитные блоки из легкого бетона в Индии. Решения для всех — твердый строительный блок из керамзитобетона.
Впервые в Индии предлагаются бетонные строительные блоки, которые представляют собой не только легкие бетонные блоки, но также относятся к премиальному сегменту монолитных строительных блоков. Они производятся с использованием керамзитобетона.
Блоки из керамзита впервые производятся в Индии. Они также известны во всем мире как блоки Leca или блоки из легкого керамзитобетона.В этих блоках Leca или твердых строительных блоках из заполнителя из керамзита используется особый тип заполнителя из керамзита, который образуется путем обжига натуральной горной глины при температуре 1200 ° C во вращающейся печи. В результате получается жесткая сотовая структура из соединяющихся между собой пустот. Эти бетонные строительные блоки, изготовленные из керамзитового заполнителя, улучшают внутреннее отверждение и повышают прочность на сжатие, возникающую с течением времени. Блоки ECA ® или блоки Leca, произведенные в Индии, являются лучшим выбором для строительства, который предлагает гибкость конструкции в сочетании с отличными тепловыми и акустическими свойствами. Их легко прибивать гвоздями, сверлить, формировать и раскалывать, и, в отличие от других обычных строительных блоков, на них не образуются трещины штукатурки из-за сильной связи с обычным цементным раствором.
Твердые строительные блоки ECA ® относятся к премиум-сегменту из всех типов строительных блоков, доступных на рынке Индии. Они являются наиболее предпочтительными зелеными блоками для строительства. Из всего сегмента строительных блоков для строительства, который также включает в себя цементные блоки для строительства, глиняные блоки для строительства, блоки CLC, строительные кирпичи, строительные цементные кирпичи, газобетонные блоки, строительные зольные кирпичи, легкий керамзитовый заполнитель является наиболее Востребованы легкие строительные блоки.
Для чего используются легкие бетонные блоки:
Легкие блоки из керамзитобетона используются как во внутренних, так и во внешних стенах, где нагрузка немного меньше, или в качестве заполняющих блоков в балках и блочных перекрытиях. Применяются также для мелкозаглубленного фундамента, возведения перегородок и панельных стен в каркасных конструкциях. Будучи прочным бетонным блоком с их свойствами долговечности и прочности, они обычно выбираются для ненесущих стен.Легкие блоки, которые часто выбирают для заполнения, обеспечивают большую экономию времени и средств, но менее прочны по сравнению с плотными бетонными блоками. Легкий керамзитобетонный блок представляет собой бетонную кладку из керамзитового заполнителя для снижения плотности и веса по сравнению со стандартным бетонным блоком.
Предпочтения клиентов в Индии:
Большинство клиентов, которые ищут кирпичи для строительства своих новых проектов, переходят на эту новую инновационную технологию легких строительных блоков из керамзитобетона (ECA ®).Строительство из кирпича является наиболее традиционным способом, и, сравнивая преимущества, которые предлагают строительные блоки, изготовленные из керамзитобетона и летучей золы и цемента, архитекторы и инженеры-строители считают обязательным включить то же самое в свои проекты.
Благодаря бесчисленным преимуществам, в том числе небольшому весу, высокой прочности на сжатие, отличной огнестойкости, высокой тепло- и звуко-/акустической изоляции, прочному конструкционному блоку, отсутствию требований к перекрытиям для горизонтальной и вертикальной кладки до 10-15 футов каменной кладки, экономия Расходы на раствор, экономия затрат на рабочую силу и многие другие дополнительные преимущества, они предпочтительны для строительства кирпичных стен, наружных стен, внутренних стен, открытых стен, вместо строительных кирпичей с летучей золой, строительных цементных кирпичей из нескольких других типов строительных кирпичей. доступны на рынке.
Для ваших требований к строительным легким кирпичам или легким блокам для строительства — Полнотелые строительные блоки ECA ® — единственный и лучший выбор. Свяжитесь с нами сегодня.
Ссылка на онлайн-видео : Нажмите здесь, чтобы посмотреть видео
ЭКА | ЛЕКА Стены | Expandedclayaggregate.

- Дом
- Керамзитовый заполнитель
- Стены
Керамзитовый заполнитель (ECA®) или Легкий керамзитобетонный заполнитель (LECA) используется в качестве основного материала для изготовления смеси низкой плотности, низкой стоимости, легких, долговечных строительных блоков и строительных панелей.Керамзитовый заполнитель (ECA ®) представляет собой уникальный зеленый строительный материал, который на 100% состоит из натурального и инертного легкого заполнителя.
На рынке нет альтернативного материала, обеспечивающего структурную целостность при плотности около 350 кг/м³, что помогает создавать очень устойчивый легкий гибкий зеленый строительный материал.
С использованием керамзитобетона могут быть изготовлены несколько вариантов, в том числе конструкция стен для вечеринок, акустические перегородки, подвалы и внутренние листовые блоки.
ECA ® предлагает такие преимущества, как легкий вес, огнестойкость, сейсмостойкость, низкая несущая способность, термо- и звукоизоляция, экономичность, экологичность и многое другое.
Международные производственные стандарты для материала включают:
- EN 771 Спецификация для каменной кладки «Технические условия для каменных блоков. Часть 3: Блоки бетонной кладки из заполнителей (плотные и легкие заполнители)»
- EN 1520 Спецификация для панелей «Сборные армированные компоненты из легкого заполнителя с открытой структурой с конструктивным или неструктурным армированием»
- EN 14992 Спецификация для сборных железобетонных изделий «Сборные железобетонные изделия — Стеновые элементы»
- EN 13055-1 Технические условия на заполнители из керамзита «Легкие заполнители.Легкие заполнители для бетона, растворов и растворов»
При правильном представлении составов смесей с использованием ECA ® может быть изготовлена серия продуктов, которая включает в себя панели, полнотелые блоки, пустотелые блоки, сэндвич-блоки, перегородки, внутренние стены, наружные стены, стены подвала и акустические перегородки.
Общая механика готового изделия допускает их как несущие, так и ненесущие элементы зданий.
Обладая указанными выше техническими преимуществами, продукт является огнестойким и негорючим без необходимости какой-либо вторичной обработки.
Легкий
Керамзитовый заполнитель(ECA®) на 100% инертен, но очень легкий по весу и может использоваться для производства легких бетонных блоков и панелей благодаря плотности материала керамзитобетона (ECA®) от 350 кг/м³.
Производимая продукция представляет собой легкий продукт, но обладающий огромной прочностью на сжатие по сравнению с традиционными бетонными материалами, доступными на рынке.
МатериалКерамзитовый заполнитель (ECA®) в блоках и панелях значительно легче, чем его доступные альтернативы, что впоследствии позволяет строительным работам продвигаться быстрее, чем некоторые альтернативы.
Устойчивое развитие
Керамзитовый заполнитель (ECA®) на 100% инертен, но очень легкий по весу и может использоваться для производства легких бетонных блоков и панелей благодаря плотности материала керамзитобетона (ECA®) от 350 кг/м³.
Производимая продукция представляет собой легкий продукт, но обладающий огромной прочностью на сжатие по сравнению с традиционными бетонными материалами, доступными на рынке.
МатериалКерамзитовый заполнитель (ECA®) в блоках и панелях значительно легче, чем его доступные альтернативы, что впоследствии позволяет строительным работам продвигаться быстрее, чем некоторые альтернативы.
Огнестойкость
Керамзитовый заполнитель(ECA®) представляет собой круглую гранулированную структуру, полученную путем обжига натуральной глины при температуре 1200°C. Они классифицируются как полностью негорючий материал Еврокласса А1.
Блоки и стены ECA ® из керамзитобетона (ECA®) обладают негорючими и огнестойкими свойствами, а также высокой водопоглощающей способностью. Это превышает установленные законом требования Стандартного строительного кодекса и обеспечивает значительный уровень защиты жизни и имущества от пожара.
Огнестойкость будет зависеть от типа элемента, толщины и типа соединения, соединения и применяемой отделки. По сравнению с альтернативными строительными системами, такими как деревянный каркас, глиняный кирпич и тяжелые бетонные элементы аналогичного размера, использование стен и панелей из керамзитобетона (ECA®) обеспечивает значительное улучшение огнестойкости благодаря присущим ему свойствам.
Производство легкого керамзита
Все глины могут расширяться, хотя некоторые расширяются легче, чем другие.И плавление не должно происходить до того, как глина расширится — это в основном зависит от минералов, содержащихся в глине. Идеальная глина очень мелкая, с низким содержанием извести и высоким содержанием железа.
Глина, используемая для производства гранул из керамзита, перед использованием должна проветриваться около года. Затем его измельчают, смешивают с водой и превращают в гранулы. В глину среднего качества могут быть добавлены химические вещества, в основном сульфит аммония в пропорции 3% от объема сухой глины и фосфат натрия в пропорции 0.1%.
Расширение может происходить в печи для обжига, где опилки, масло или уголь смешиваются с глиной и затем обжигаются. В качестве альтернативы более эффективная вращающаяся печь может работать на угольной пыли, парах нефти, природном газе или биогазе. Вращающаяся печь обычно состоит из металлического цилиндра диаметром 23 м и длиной 12-60 м. Существуют также мобильные модели меньшего размера (см. рис. 8.12). Температура печи составляет около 1150 °C, а время обжига от глиняных окатышей до керамзита составляет примерно семь минут.
Для изготовления блока из легкой глины формы Zytan заполняют легким керамзитом, затем нагревают до температуры около 1000°C (Brien et al., 1978). Светлый клинкер расширяется еще больше. Пространства внутри формы заполняются, и материал становится сплошным блоком. Как только формы остынут, в результате получится однородный термоблок с высокими изоляционными свойствами, который можно использовать немедленно. Плотность
м аид
ость vhw kH
8.11
Примеры английских узоров для плитки примерно 1200 года нашей эры.
8.11
Примеры английских узоров для плитки примерно 1200 г. н.э.
блоки могут варьироваться от 200 кг/м3 до 1200 кг/м3 в зависимости от температуры обжига. Все блоки несущие. Отверстия можно пилить и сверлить, как и в других легких глиняных блоках. В настоящее время эти блоки не производятся в промышленных масштабах.
Продолжить чтение здесь: Изделия из обожженной глины и снижение энергопотребления
Была ли эта статья полезной?
Производство керамзита с использованием устройства вихревого слоя
Производство керамзита основано на гомогенизации и измельчении частиц глинистого сырья, формировании и дальнейшем обжиге гранул.С учетом таких процессов целесообразно использовать устройство вихревого слоя (АВС) из GlobeCore .
Актуальность производства керамзита
Керамзит — востребованный строительный материал, недорогой теплоизолятор, наполнитель, декоративное изделие. Выпускается в виде шариков, гравия, щебня, песка с толстой оболочкой и пористой внутренней структурой. Сырьем для керамзита служат легкоплавкие, вспучивающиеся глины, сланцы и суглинки.
Зерно получается в результате гомогенизации, смешивания шихты и обжига. Отличаются низкой теплопроводностью, инертностью к воздействию щелочей, кислот, долговечностью, экологичностью, звукопоглощающей способностью. Применяются в основном в строительстве и при производстве строительных материалов:
- Производство пористых бетонов
Наполнитель для легких, сверхлегких пористых бетонов, используемых в стяжках, монолитных стенах и конструкциях.
- Производство блоков из керамзита
Основной наполнитель стеновых блоков из керамзита. Они также содержат цемент, песок и воду. Конструктивные элементы применяются в малоэтажном строительстве при возведении стен и перегородок в домах.
- Теплоизоляция зданий, сооружений
Высокопористые разновидности керамзита применяют в качестве теплоизолятора полов, стен и межэтажных перекрытий.
- Строительство фундаментов
Используется для наполнения с целью предотвращения промерзания. Это позволяет снизить расход материала при возведении конструкций.
Является хорошей основой для чернового выравнивания пола. материал легкий; поэтому не оказывает нагрузки на межэтажные перекрытия. Повышает теплоизоляционные характеристики внутреннего пространства.
Материал относительно низкой пористости применяется в насыпях при строительстве дорог и водоотводов, при обработке и подготовке почвы.
- Теплоизоляция инженерных систем
Трубы системы теплоснабжения, подведенные к домам и зданиям, покрыты гранулами. Они обеспечивают качественную теплоизоляцию и легкий доступ к системе.
Столь широкая сфера применения керамзита делает его востребованным на рынке строительных материалов, в промышленности, сельском хозяйстве. Перспективной и актуальной выглядит модернизированная технология производства керамзита с использованием устройства вихревого слоя. Но сначала обсудим, какими недостатками характеризуются существующие линии по производству этого материала.
Производство керамзита традиционными способами, недостатки этих способов
Практически на каждом современном заводе по производству керамзита в процессе смешивания и измельчения сырья используются глиносмесители, вальцы и кромкообрезные станки. Выпечка осуществляется в печных барабанах. Обработка гранул в устройстве занимает примерно 45 минут.
Однако традиционное оборудование для подготовки, гомогенизации и диспергирования сырья не обеспечивает качественного измельчения и смешивания ингредиентов.Это отрицательно сказывается на прочности готового изделия.
При низкой степени гомогенизации и плохой диспергируемости частиц даже 3% карбонатных примесей во вспучивающихся легкоплавких глинах отрицательно сказываются на качестве материала. Гидратация СаО сопровождается деструкцией керамзита и потерей прочности при хранении.
Традиционное производство керамзита с использованием катков, бегунков и глиносмесителей также неактуально для обработки глинистых масс с высоким содержанием песка. При содержании в смеси 10–30 % свободного SiO2 невозможно изготовить из сырья качественный прочный продукт.
Обработка сырья в вихрепластовом аппарате помогает в решении этих задач классическими методами. Кроме того, появляется возможность производить качественный керамзит даже из изначально непригодных глиняных масс.
Кроме того, по традиционной технологии отсортированное сырье можно смешивать с веществами, улучшающими его набухание, — мазутом, соляркой.Применение АВС позволяет минимизировать использование добавок или отказаться от них, что дает положительный экономический эффект и влияет на чистоту и экологичность готового продукта.
Производство керамзита с помощью устройства вихревого слоя
Производство керамзита с помощью устройства вихревого слоя основано на обработке сырья в электромагнитном поле с ферромагнитными частицами. Агрегат может работать как с сухими, так и с влажными влажными средами.В рабочей камере аппарата наблюдаются процессы диспергирования и перемешивания, сопровождающиеся активацией частиц. Это влияет на прочность готового изделия. Процессы происходят при воздействии электромагнитного поля, акустических колебаний, высокого локального давления, электролиза.
В вихревом слое ферромагнитные иглы превращаются в мешалки и дробилки. При этом они перемещаются по камере, вращаются, сталкиваются с обрабатываемым материалом, друг с другом и со стенками устройства.Все это способствует эффективному перемешиванию, измельчению и активации шихты и смеси.
Эффект обработки глинистого сырья на керамзит с помощью АВС описан и экспериментально изучен Д. Д. Логвиненко. В результате мы получаем материал с меньшим объемным весом и лучшими прочностными характеристиками. Результаты представлены в таблице 1.
Таблица 1 – Характеристики керамзита при переработке сырья в АВС
Эксперимент № | Характеристика сырья и продолжительность обработки в АВС | Характеристики керамзита | |||||
Переработка сырья в АВС | Переработка сырья без АВС | ||||||
Объемный вес (γ), г/см3 | Предел прочности на скалывание (σс*10-5), Па | Коэффициент прочности | Объемный вес (γ), г/см3 | Предел прочности на скалывание (σс*10-5), Па | Коэффициент прочности | ||
1 | Глина, содержащая 26% свободного SiO2 (30% от обработки шликера) | 0.![]() | 2,25 | 10,3 | 0,38 | 1,60 | 5,1 |
2 | Глина, содержащая 41% свободного SiO2 (30% от обработки шликера) | 0,34 | 2,45 | 7,8 | 0,84 | 3,24 | 4.1 |
3 | Монотермит (7 минут сухой обработки) | 0,85 | 29,4 | 36 | 1,6 | 9,81 | 6.5 |
4 | Глина, содержащая угольную золу в соотношении 50/50 (7 минут сухой обработки) | 0,57 | 10,7 | 18 | 0,58 | 4,32 | 8,4 |
5 | Глина, содержащая угольную золу в соотношении 50/50 при опыливании полуфабриката каолином (7 минут сухой обработки) | 0,74 | 27,9 | 32,0 |
Для сравнения обработан шликер, содержащий до 40 % свободного диоксида кремния. Производство керамзита с применением АВС отличается двукратным снижением объемной массы при одновременном повышении прочности материала. Прочностно-массовая характеристика изделия, полученного из шихты после обработки в вихреслойном устройстве, в два раза выше, чем у материала, изготовленного традиционным способом.
Этому результату способствует тщательная обработка сырья в вихревом слое с активацией входящего в состав смеси кварцевого песка.При обработке в АВС наблюдается разрыв силоксановой связи Si-O. Следовательно, на поверхности частиц появляются активные центры в виде свободных радикалов. Это стало причиной повышения качества конечного продукта. Песок активируется по тому же принципу, что и при диспергировании в дезинтеграторах на высоких скоростях.
В связи с активацией кварцевого песка происходят реакции стеклообразования и силикатообразования с участием диоксида кремния. После завершения производства керамзита обжигом изделия в нем отсутствуют крупные песчинки SiO2, в которых концентрировались бы напряжения. А в составе стекла кварцевый песок влияет на повышение прочности и термостойкости материала.
Кроме того, изучена сухая технология производства керамзита с использованием вихревого слоя. Для исследования был взят монотермит. Из сырья, обработанного в сухой среде с помощью АВС, получен наполнитель, прочность которого в три раза выше, чем у материала, изготовленного классическим способом. При этом объемная масса огнеупорного заполнителя была вдвое меньше, чем в образце.
Сухая обработка многокомпонентных шихт, состоящих более чем наполовину из зол тепловых электростанций (золы ТЭС), также показала положительный результат.
Полученные данные свидетельствуют о том, что технология производства керамзита с использованием вихревого слоя позволяет получать высокопрочный строительный материал даже из глин с высоким содержанием песчаных или карбонатных примесей.
Преимущества использования устройства вихревого слоя в производстве керамзита
Устройство вихревого слоя – передовое оборудование, которое может быть использовано для оптимизации как компактного завода по производству керамзита, так и крупного предприятия по следующим причинам:
Готовый материал характеризуется повышенной прочностью и термостойкостью даже при высоком содержании песка и карбонатных примесей в глиняных массах. Также АВС позволяет использовать отходы энергетики, в том числе золу ТЭС, в производстве керамзита.
Оборудование отличается низким потреблением электроэнергии и преимуществами в несколько раз по сравнению с обычными установками. Потребляемая мощность моделей AVS-100 и AVS-150 составляет 4,5 кВт и 9,5 кВт соответственно.
Устройство компактное, простое в эксплуатации и может быть интегрировано в существующую производственную линию. При этом для этого оборудования нет необходимости делать тумбу или дополнительные конструкции.AVS без проблем перемещается по мастерской.
Таким образом, АВС из GlobeCore – это универсальное, удобное, высокопроизводительное оборудование, которое позволит расширить и оптимизировать производство высококачественного керамзита. Кроме того, снижаются требования к качеству сырья, а значит, появляется больше возможностей в части производства легкого заполнителя, на котором базируется производство керамзитоблоков, легких бетонов и т. д.Себестоимость материала можно снизить за счет повышения его эксплуатационных характеристик.
Для получения консультации и заказа моделей АВС-100 или АВС-150 для завода по производству керамзита обращайтесь к торговым представителям GlobeCore.
Как сделать керамзитобетон самостоятельно. Как сделать керамзитобетонные блоки своими руками? Ручной вибропресс
Керамзит, как сыпучий утеплитель, применяется не только для теплоизоляционных мероприятий, связанных с утеплением полов.Его часто используют для производства бетонных блоков, где он выступает в качестве наполнителя. От этого блоки становятся легкими, ведь керамзит в несколько раз легче гравия или щебня, которые он заменяет в керамзитобетонных блоках, плюс снижается теплопроводность самого стенового материала. Производство керамзитобетонных блоков ничем не отличается от обычных бетонных блоков, главное точно соблюдать рецептуру используемого раствора.
Обозначим состав керамзитобетона для изготовления блоков из расчета на 1 м³ приготовленного раствора.
Приведенная рецептура соответствует марке бетона М150, достаточной для монтажа стеновых конструкций.
Сегодня большое внимание уделяется такой характеристике, как влагостойкость. Поэтому для производства блоков из керамзитобетона, которые легко выдерживали бы повышенную влажность и даже прямое воздействие воды (например, косой дождь), в раствор добавляют гидроизоляционные материалы. Один из них – битумная мастика, которую замешивают в виде 10% водного раствора.
Следует отметить, что этот раствор имеет немного измененную рецептуру.
Существует другой подход к производству керамзитобетонных блоков. Производственная линия с мощным оборудованием и высокой производительностью, с дозаторами, настроенными на весовые ограничения точно по рецепту. Второй – ручной метод, при котором компоненты взвешивают чаще в ведрах. Поэтому стоит указать вес материалов в ведрах (10 л):
цемент- — 13 кг;
- песок — 16;
- вода — 10;
- керамзит (гравий) — 4-4.
5;
- керамзит (песок) — 5,5-6.
Оборудование для производства
Для производства керамзитобетона (вручную) необходимо:
- бетономешалка;
- несколько лопат; вибромашина
- ;
- несколько форм.
Бетоносмеситель можно купить или арендовать. Машины тоже продаются, хотя это не самое дешевое оборудование. Сделать их можно своими руками, а если вы хороший сварщик, то на сборку одного станка уйдет один день.Существует огромное количество конструкций станков. В основном это каркасные узлы, внутри устанавливаются и жестко закрепляются формы. К раме также жестко крепится вибратор, работающий от сети 220 вольт. Устройство продается в строительных магазинах.
Еще один вариант – вибростол, представляющий собой горизонтальную плоскость. Он обычно устанавливается на пружинах, и к нему крепится вибратор. Для станка придется сделать несколько фигур своими руками. И чем больше площадь стола, тем больше формочек на нем поместится, тем выше производительность самодельного оборудования.
Важно! Не переусердствуйте, ведь вибратор имеет определенную мощность, которой достаточно, чтобы провибрировать определенную массу.
Форма для керамзитобетонных блоков
Для изготовления форм используются различные плоские материалы: листовое железо толщиной не менее 2 мм, доски, фанера, плиты ОСП и др. Основная задача подрядчика – подогнать размеры формы под размеры блока: 190х188х390 мм (стандартный блок несущей стены).Бывают так называемые полублоки (используются для возведения перегородок), размеры: 90х188х390.
Одной из особенностей керамзитобетонных блоков являются пустоты, которые облегчают камень без снижения несущей способности, удешевляют за счет уменьшения объема используемой смеси, повышают теплотехнические характеристики изделия. Поэтому при изготовлении в формы жестко устанавливают три трубы диаметром 40-50 мм, расположенные на одинаковом расстоянии друг от друга и от стенок формы.
Трубы соединяются между собой сваркой с горизонтальными перемычками (арматурой, уголком или стальной лентой). Формы крепятся к стенам электросваркой, если форма изготовлена из стального листа, или с помощью саморезов, если используются деревянные изделия.
Технология производства
Сам технологический процесс осуществляется в любом помещении с отлаженной системой вентиляции. Размеры помещения зависят от габаритов используемых машин.После производства керамзитобетонные блоки должны пройти процесс сушки, проводимый на открытой площадке на улице. Если есть вероятность выпадения атмосферных осадков, то над участком лучше возвести навес.
В первую очередь готовится раствор: в бетономешалку заливают цемент и часть воды. Смесь перемешивают несколько минут до получения однородного состава. Затем в нее порциями добавляют песок и керамзит. В конце добавляется остальная вода.Окончательный раствор должен быть густым и податливым.
После этого сбрасывается из бетономешалки в заранее подготовленную емкость (корыто), а оттуда лопатами забрасывается в формы, уложенные на вибростол или установленные на вибростоле. Перед этим стенки форм промазывают отработанным техническим маслом, чтобы после затвердевания блоки легко выходили наружу. Пол вибростола или площадки посыпают мелким песком, чтобы бетон не прилипал.
Формы равномерно заполняются раствором, например, в них забрасывается пара лопаток смеси. Затем включают вибратор, бетонный раствор равномерно распределяют по всему объему формы и уплотняют. Затем процесс повторяется. Эта процедура повторяется несколько раз для полного заполнения форм. Иногда для придания более точных размеров уложенный и утрамбованный раствор дополнительно прижимают сверху металлической крышкой, это позволит создать на поверхности блока ровную и гладкую поверхность.
В таком виде керамзитоблоки должны простоять не менее суток прямо в формах. Затем их вытаскивают, укладывают на уличную площадку так, чтобы между ними был зазор в пределах 2-3 см. Блоки из керамзитобетона следует просушить в течение 28 дней, что придаст им марочную прочность. Материал должен сохнуть равномерно со всех сторон, поэтому каждый блок во время сушки переворачивают из стороны в сторону. Если положить их на деревянные поддоны для сушки, то с переворотами бороться не нужно.
Производство блоков из керамзитобетона как бизнес
Начать производство керамзитоблоков, чтобы получать прибыль, не проблема. Главное, все точно рассчитать. Как показывает практика, главное требование не к оборудованию, а к размерам помещения и открытой площадки. Чем они больше, тем больше блоков можно уложить на сушку, которая длится около месяца. Поэтому предлагаются различные варианты сушки. Один из таких представлен на фото ниже, где можно увидеть специальные стеллажи с уложенными на пол блоками.
Все остальное упирается в стоимость сырья, которая колеблется в зависимости от сезона. Летом цемента всегда больше, потому что спрос на него растет из-за увеличения объемов строительства. Особенно это касается частного сектора.
Поэтому оптимально производить керамзитоблоки в осенне-весенний период. Если помещение отапливается, производство зимой не останавливается. Расход готового стенового материала зимой невелик, иногда он сводится к нулю, зато летом весь запас произведенной продукции будет распродан.Здесь нужно будет пересчитать его стоимость на новую цену цемента и других компонентов. Вот где большая прибыль лежит.
Кто не первый год в этом виде бизнеса старается все предусмотреть. Кто-то зимой старается закупать материалы по низкой цене, но есть нюанс – цемент со временем теряет свои свойства, снижается качество. Кто-то, как описано выше, пытается увеличить производство блоков зимой. В любом случае, это прибыльный бизнес, пока строительство в самом разгаре, пока стройматериалы пользуются спросом.Блоки из керамзитобетона сегодня на пике популярности благодаря невысокой цене, высоким теплотехническим характеристикам и простоте монтажа.
Частные строения с каждым годом становятся все более актуальными, ведь жить в собственном доме гораздо комфортнее, чем в многоэтажке. Но главным препятствием зачастую является высокая стоимость строительства, поэтому застройщики ищут способы сэкономить. Если делать керамзитобетонные блоки своими руками, то это не только сэкономит значительные средства, но и послужит гарантией того, что изделия изготовлены в соответствии с нормами прочности.
Что нужно для работы
Для изготовления самодельных керамзитоблоков необходимо приобрести все необходимые материалы. Их количество рассчитывается исходя из планового количества изделий, и рассчитывается в соответствии с пропорциями в объеме:
Цемент | Если взять за основу широко распространенную марку М400, то понадобится около 1/10 объема блоков, которые необходимо изготовить. В одном кубическом метре содержится 1300 килограммов цемента, именно на этот показатель следует ориентироваться при определении необходимого количества. |
Керамзит | Вам понадобится вариант плотностью от 350 до 500 кг/м3, оптимальная фракция от 5 до 20 мм. Так как в раствор нужно добавить 8 частей, то несложно догадаться, что этот материал будет основным.![]() |
Песок | Песок речной лучше всего приобрести среднезернистый или крупнозернистый без каких-либо примесей глины и чернозема.Подойдет и песок из карьеров, но его желательно хотя бы просеять, а лучше вообще промыть. Для приготовления требуется 2 части, исходя из этого и рассчитан объем |
Вода | Для технологии требуется примерно 215-230 литров на м3. Правильная дозировка воды очень важна для прочности блоков. Недостаток его, как и избыток, приводит к снижению прочности и появлению трещин на поверхности в процессе высыхания. |
Добавки | Этот компонент используется по желанию, но следует учитывать, что различные добавки позволяют значительно улучшить свойства бетона и повысить его влагостойкость и морозостойкость. При их использовании вероятность появления трещин на изделиях намного меньше. |
Совет!
Для улучшения качества изделий и экономии средств лучше приобретать универсальные, улучшающие свойства смеси и повышающие ее пластичность.
Организация рабочего процесса
На самом деле процесс настолько прост, что для керамзитобетонных блоков практически не требуется никакого оборудования. Но какие-то простейшие приспособления все же понадобятся.
Формы для блоков
Есть два варианта: либо приобрести готовые варианты, либо сделать их самостоятельно.
В первом случае следует руководствоваться следующими факторами:
- Новые формы довольно дорогие, но можно купить и бывшие в употреблении. . Их стоимость намного ниже, но важно тщательно проверять каждое изделие на наличие повреждений и соответствие геометрическим параметрам.
- Важно подобрать оптимальные размеры, чаще всего используется вариант 190х190х390 для стен и вариант 80х190х390 для установки внутренних перегородок. Параметры могут меняться в зависимости от специфики работы.
- Другой вариант – арендовать постройки. , в некоторых регионах предоставляется данная услуга, что позволяет значительно сэкономить расходы.
Второй вариант — собрать формы своими руками.
Производственные инструкции:
- Можно собрать каркас из досок толщиной 25 мм, при этом их внутреннюю поверхность желательно обшить жестью или жестью. Параметры для блоков берутся те же, что и для стандартных форм или любых других.
На фото — один из вариантов конструкции из доски или фанеры
- Другим решением является изготовление каркаса из листового металла, усиленного металлическими уголками.Для фиксации формы могут использоваться либо защелки, либо болтовое соединение через приваренные проушины, либо стяжка со шпильками и барашковыми гайками.
- Для создания пустот можно использовать как специально подготовленные заготовки, так и просто бутылки. Все зависит от возможностей и пожеланий.
Еще один вариант — машина для блоков из легкого заполнителя, представляет собой комбинированный вибрационный агрегат и формы, в малых вариантах их 2-4 штуки, в более производительных их количество может быть значительно больше.
Формовочные изделия
Этот этап выполняется следующим образом:
- Раствор готовят в пропорциях, указанных выше.Важно контролировать, чтобы консистенция была оптимальной. Лучше всего использовать бетономешалку, это гарантирует высокое качество смешивания, что очень важно для прочности изделий.
Совет!
Проще всего проверить консистенцию следующим образом: небольшое количество состава сжимают в руке, должен получиться плотный комок, который разбивается при падении на землю.
- Дальнейшее рассмотрение вопроса, как сделать керамзитоблоки самостоятельно, зависит от того, есть ли у вас виброустановка.Если есть, то формы заполняют и устанавливают на оборудование для удаления воздуха из состава. Если нет установки, то состав утрамбовывается булавкой или деревянной палочкой.
- Полученные самодельные керамзитобетонные блоки оставляют на сутки, после чего формы можно разобрать и аккуратно выложить изделия на ровную поверхность для дальнейшей просушки.
Полную силу продукт набирает в течение четырех недель.
Если вы не умеете резать керамзитобетонные блоки, то лучше всего подойдет болгарка с алмазным диском по бетону и камню диаметром 230 мм, так как специальные пилы по кирпичу есть не у всех.
Выход
Видео в этой статье поможет вам лучше понять этот процесс. Важно соблюдать все требования технологии, и вы получите отличный результат.
Керамзитобетон – легкий строительный материал, обладающий высокой прочностью, практичностью и, главное, эксплуатационными характеристиками своими руками. Несмотря на небольшой вес, модули имеют высокую плотность, низкую теплопроводность и разнообразие моделей.Экологическая чистота материала – еще один плюс модулей, поэтому, если застройщик хочет с самого начала процесса взять строительство здания в свои руки, стоит наладить производство керамзитобетонных блоков. на его сайте. При этом производство блоков из легкого заполнителя потребует небольших финансовых вложений, а стоимость модуля будет намного ниже, чем покупка готового изделия у производителя.
Оборудование для производства модулей
Для изготовления керамзитобетонных блоков своими руками необходимо приобрести, арендовать или изготовить соответствующее оборудование, а также купить качественное сырье.И здесь не стоит дешеветь – чем выше качество исходного материала, тем долговечнее и практичнее будут модули. Для облегчения процесса и наладки линии по производству легкобетонных блоков в необходимом для застройщика объеме потребуется следующее оборудование:
- Вибростол;
- Бетономешалка;
- Формовка металлических поддонов.
Если позволяют финансы, то неплохо приобрести установку вибропрессового типа, она заменит два устройства: формы и вибростол.Также необходимо найти хорошее помещение с ровным полом и определить место для сушки модулей.
Важно! Вибростолы различаются по маркам и производительности: некоторые из них производят до 120 модулей в час, а некоторые до 70 единиц. Для частного использования вполне подходят малоформатные станки мощностью до 0,6 кВт и производительностью до 20 блоков/час.
Ценовая градация в пределах 30 долларов – это идеальные по своим компактным размерам устройства, применяемые для производства керамзитобетонных блоков своими руками в частном домостроении.
Изготовление машины для производства блоков из легкого заполнителя собственными силами также возможно.
Также возможно изготовление станка для производства керамзитобетонных блоков своими силами. При небольшой сноровке и небольших навыках устройство получится не хуже заводского, а цена его будет в 10 раз ниже. Предлагаем вариант простейшего оборудования для производства керамзитобетонных блоков типа «несушка» — это агрегат, оснащенный формовочной коробкой без дна, вибратором, расположенным на боковой стенке и ручками для демонтажа матрицы .
Важно! Стандартные размеры одного блока 390*190*188 мм, допустимый процент пустотности не более 30%, а прорези могут быть как круглыми, так и продолговатыми — важно только, чтобы стержнеобразователь был выполнен в виде конус для облегчения снятия опоки с готового блока.
Для изготовления матрицы необходим лист металла толщиной 3-5 мм, из которого нужно вырезать заготовку с запасом 5 см для процесса уплотнения смеси.Молдинг выполнен в виде сквозного короба без дна. Сварной шов должен оставаться снаружи, иначе он испортит форму модуля.
Для устойчивости машины по бокам устройства приварены полосы из профильных тонких труб, а конструкция по периметру оснащена резиновой обивкой. Неплохо оборудовать всю систему фартуком, чтобы раствор не выливался. А вот вибратор сделан из двигателя старой стиральной машины на 150 Вт (это можно сделать, сдвинув центры).На вал крепится металлическая полоса с краевым отверстием — эксцентриком, параметры которого лучше всего определить опытным путем. Если у вас остались вопросы, как сделать станок для изготовления модулей, посмотрите видео — ответы будут полными и подробными.
Подготовка и процесс изготовления модулей из керамзита своими руками
Для приготовления смеси и блоков вам понадобится форма с гладкой поверхностью. Допускается выполнение заготовок как из металлического листа, так и из досок – в этом случае готовый модуль получится фактурным.Сам процесс включает 4 этапа:
- Смешивание ингредиентов строго по рецепту. В частности, песок составляет 3 части от общего объема смеси, вода – 0,8-1 часть, как цемент, но керамзита берут 6 частей. Важно не только соблюдать рецептурную технологию производства керамзитобетонных блоков, но и правильно смешивать компоненты: сначала в бетономешалку помещают воду, керамзит, затем цемент и песок. При использовании дополнительных компонентов их также загружают в емкость бетономешалки.
- После обещаний начинается этап лепки. Ускорит процесс использование вибромашины: смесь укладывается в формовку, куда предварительно уложена плита, включается двигатель для вибрации, удаляются излишки состава.
- Поднимите тарелку с готовой формой за ручки, получится полноценный модуль, который отправляется на сушку.
- Сушка длится не менее 48 часов, при этом заготовки необходимо защищать от солнца и дождя.
После высыхания плиты снимают с модулей.
Это самый быстрый процесс, при котором изготовление керамзитобетонных блоков в домашних условиях не вызывает проблем. Однако, если вам необходимо сделать керамзитобетонные блоки своими руками более прочными и плотными, имеет смысл добавить процесс пропарки, тогда материал наберет повышенную прочность и время набора бетоном марки прочности сократится до 28 дней.
Варианты состава смеси разные, однако основными компонентами являются песок, вода, цемент и керамзит.В качестве добавки могут быть добавлены омыленные древесные смолы, повышающие морозостойкие качества материала, и технический лигиносульфонат, повышающий сцепление смеси.
А теперь еще немного о том, как самому сделать керамзитоблоки:
- Для приготовления раствора пропорции и ингредиенты следующие:
- Портландцемент М400 или шлакопортландцемент — 1 часть;
- Керамзитовый гравий — 8 частей;
- Песок кварцевый чистый — 2 части и 3 части для фактурного слоя;
- Чистая вода — расчет 225 литров на 1м3 смеси.
Совет! Для придания пластичности неплохо добавить ложку обычного стирального порошка или средства для мытья посуды.
- Все ингредиенты заливаются в бетономешалку, причем здесь сначала следует высыпать сухие компоненты, и только потом вливать воду. Если пропорции соблюдены, то масса по консистенции будет похожа на пластилин.
Совет! Полученный блок будет весить примерно 16-17 кг. При этом допускается форма заготовки как стандартных размеров, так и произвольная: 390*190*14, 190*190*140 и другие.
- Молдинги устанавливаются на ровную поверхность, с внутренней стороны стенки заготовки обильно смазываются машинным маслом, а основание присыпается песком.
- Заполните формочки смесью, утрамбуйте их на вибростоле или используйте для этого деревянный брусок. Утрамбовку проводят до образования цементного молока. После этого поверхность выравнивается, а заготовки отправляются на сушку.
Важно! Опалубку снимают не ранее, чем через сутки! Важно защитить заготовки от прямых лучей солнца, так как неравномерная сушка приводит к растрескиванию поверхности модулей.
Как видите, купить, изготовить оборудование для производства керамзитоблоков в домашних условиях и выполнить все процессы несложно. Но модули, изготовленные таким образом, будут не хуже заводских.
Рассчитываем стоимость
Все работы требуют предварительных расчетов, иначе не стоит начинать производство керамзитобетонных блоков в домашних условиях своими руками. Для расчета стоимости придется точно узнать цену комплектующих и понять, сколько будет стоить единица готового материала.В частности, учитывая стандартный модуль 390*190*140 мм, объем раствора составляет 14 литров. Вычитаем пустотообразователи, которых, как правило, не более 25-30%, итого 11 литров смеси. Теперь расчет компонентов:
- На одну штуку уходит 0,005 кубометра песка, что заполняет 5 литров общего объема;
- Керамзит примерно такой же, как песок;
- Цемента потребуется 1,25 кг.
Осталось узнать цену ингредиентов, учесть воду, другие компоненты и рассчитать удельную стоимость модуля.По самым приблизительным расчетам она составит до 5 долларов. Как видите, цена невероятно низкая. Однако для полной картины недостаточно подсчитать стоимость оборудования, трудозатраты и время, которые любой застройщик обязан включить в расчеты. Но даже в такой полной расстановке стоимость блок-модулей, из которых получатся отличные стены из керамзитобетонных блоков, сделанных своими руками, все же ниже, чем от завода-изготовителя. Поэтому, если вы планируете поставить свой дом на участке, посмотрите еще раз технологию изготовления материала, видео от профессионалов и начните планировать процесс запуска производства керамзитобетонных блоков на своем участке – это выгодно, практично и доступно. для каждого мастера.
Комментарии:
Блоки из керамзитобетона своими руками изготовить несложно. Для их создания используется керамзитобетонная смесь, которая значительно снижает вес будущей конструкции.
Благодаря использованию натуральных материалов блоки экологически чистые.
Характеристики керамзитобетонных блоков
Керамзитовые блоки состоят из песка, цемента, воды и наполнителя, в качестве которого используется керамзит, поэтому изготовить их самостоятельно может любой мастер.При этом можно сэкономить значительные суммы денег. Понятно, что такие блоки нельзя использовать для строительства многоэтажного дома, но для строительства гаража, сарая или небольшого дома керамзитоблоки ручной работы – идеальное решение.
Если вы решили сделать керамзитоблоки своими руками, то вам следует знать, что по своим экологическим характеристикам они приравниваются к обычному кирпичу, так как изготавливаются из натуральных материалов.
Формы для изготовления керамзитобетонных блоков.
Керамзит используется в качестве наполнителя при изготовлении этого строительного материала. Так как он легкий, вес блоков тоже небольшой. Если вас интересует вопрос, как сделать керамзитоблоки своими руками, и вы реализуете это решение, то сможете значительно удешевить строительные работы. При сравнении затрат при строительстве из обычного кирпича и таких блоков можно сэкономить около 30% своих денег.Тот факт, что один блок соответствует 7 кирпичам, позволяет ускорить процесс строительства.
Вы также можете приобрести указанный материал, но максимальная польза будет в том случае, когда вы делаете керамзитобетонные блоки своими руками.
Одним из недостатков этого строительного материала является низкая прочность, что объясняется высокой пористостью. Для того чтобы увеличить этот показатель, при изготовлении блоков в смесь необходимо добавлять кварц или обогащенный песок.
Если вы делаете строительные блоки своими руками и будете использовать их для создания внутренних перегородок, несущих незначительные нагрузки, то можно использовать керамзитобетон. В том случае, если вы будете возводить из этого материала несущие стены и укладывать на них железобетонные перекрытия, лучше использовать обогащенный песок.
В зависимости от пропорции компонентов, входящих в состав смеси для изготовления блоков, определяются конечные характеристики строительного материала.
Если вы хотите получить материал с высокими теплоизоляционными свойствами, то вам необходимо увеличить количество керамзита, но в этом случае прочностные характеристики блоков снизятся.
В зависимости от пропорций компонентов керамзитобетонные блоки станут прочнее или приобретут повышенные теплоизоляционные свойства.
Плотность такого строительного материала почти на 50% меньше, чем у керамического или силикатного кирпича, что позволяет снизить нагрузку на фундамент здания.На его строительстве можно сэкономить, так как его можно сделать менее мощным.
Если вы все же решили изготовить такие строительные блоки самостоятельно, то вам нужно учесть, что они, по сравнению с кирпичом, имеют более высокую пористость и поэтому хрупкие, менее прочные.
Еще одним недостатком этого стройматериала является низкая морозостойкость, поэтому отделка стен обязательна. Если сравнивать их с газобетоном, то этот материал обрабатывается хуже.
Вернуться к содержанию
Самодельные блоки
Создание керамзитобетонных блоков своими руками – задача, которая под силу любому мастеру. Эту работу можно выполнить самостоятельно, а если работать вдвоем, то реально сделать 100-120 штук указанного строительного материала в день.
Если следовать инструкции и технологии, то можно самостоятельно заготовить материал, например, для строительства гаража, сарая, других подсобных помещений или небольшого домика.
Для начала вам понадобится форма, она может быть деревянной или металлической. Для изготовления формы проще и дешевле использовать доски. Для того чтобы облегчить вытягивание блоков, их рекомендуется обить жестью. Чтобы форма не меняла своих размеров в процессе эксплуатации, на концах двух ее половинок необходимо сделать специальные затворы.
Так как вы все делаете своими руками, размеры могут быть те, которые удобны в вашем случае. Все будет зависеть от размера подготовленной формы.
С помощью пресс-формы можно производить до 100 блоков из легкого заполнителя в сутки.
Для выполнения работы вам потребуется:
- форма;
- Мастер в норме;
- лопата;
- готовая смесь; Металлический лист
- , на котором будут производиться работы;
- вибростол.
Для приготовления раствора лучше всего приобрести или арендовать бетономешалку, но если такой возможности нет и требуется небольшое количество стройматериала, то можно сделать раствор вручную.
Для приготовления раствора вам понадобится:
- 1 часть цемента, необходимо использовать не ниже М 400.
- 8 частей керамзита. Для упрощения расчетов необходимо руководствоваться тем, что в ведро емкостью 10 литров поместится около 5 кг керамзита фракцией 5-20 мм. Вам понадобится около 300-500 кг керамзита на кубометр раствора. Все будет зависеть от того, какая плотность сторон вам нужна.
- 1 часть воды.
- 3 части песка, он не должен содержать глинистых примесей.
- 1 часть обычного стирального порошка, это сделает смесь более пластичной.
Для получения более качественных блоков необходимо использовать вибростол. Его можно купить, сделать самому или просто арендовать. Если у вас нет такой возможности, то можно утрамбовать состав в форме и с помощью обыкновенной лопаты, но качество и прочность полученного стройматериала будут низкими.
После того, как раствор схватится, а это будет зависеть от погодных условий, форму снимают, а блоки оставляют еще на 2 дня. Теперь их можно складывать и использовать для строительства через 28 дней.
Так как мы убедились в технологичности, надежности и практичности этого материала. Эта статья расскажет вам о том, что такое керамзитобетонные блоки и как их сделать своими руками, в чем их особенности и преимущества перед другими строительными материалами.
Вы узнаете о технологии производства, как можно изготовить керамзитобетонные блоки своими руками, стоит ли этот процесс потраченного времени и сил.
Керамзитобетон легкий, что позволяет создавать прочное жилье достаточно презентабельного вида даже на незначительном фундаменте.
Керамзитобетон — единственный среди наиболее перспективных современных строительных материалов. Его свойства по скорости возведения различных объектов и экономичности использования значительно превосходят качество других материалов.
Керамзитобетонные конструкции изготавливаются исключительно из натуральных компонентов, и по этой причине они не выделяют токсичных веществ в окружающую среду. Если верить отзывам тех, кто строил дом из легкобетонных блоков, они утверждают, что в помещении создаются очень комфортные климатические условия для проживания.
Примечание. Качественные керамзитобетонные блоки имеют плотность от 600 до 1800 кг/м3.
Производство керамзитобетонных блоков
Керамзитобетон обладает уникальными свойствами, определяемыми особенностью их изготовления.За основу взят керамзит — экологически чистый материал.
Имеет поры, по структуре напоминающие губку, в которых находится специально обожженная глина, приобретающая текстуру застывшей пены. В результате такой материал получается очень легким и прочным. В качестве вяжущего компонента используется цемент.
Прочность и способность удерживать тепло зависят от правильно подобранных пропорций смеси. Чем больше гранул в смеси, тем более хрупким становится блок, но в то же время и теплее, и наоборот.
Разновидности керамзитобетонных блоков
Керамзитобетонные конструкции по своим физико-технологическим данным и назначению подразделяются на:
Плотность теплоизоляционных керамзитобетонных блоков самая низкая. Этот вид керамзита изготавливается особым образом, что способствует образованию крупных пор. Плотность таких гранул составляет 150-200 кг/м3.
Керамзит конструкционный имеет сходство с природным камнем, поэтому стены дома из такого материала будут чрезвычайно плотными.Существенным преимуществом керамзитобетона перед другими строительными материалами является цена.
Темпы монтажа стен из керамзитобетона в 4 раза быстрее, если сравнивать с кирпичными зданиями. Кроме того, при строительстве домов из этого материала расходуется раствора в 2 раза меньше, опять же, если сравнивать с кирпичом.
Блоки из легкого заполнителя имеют сложную форму, в них много пустот-щелей, улучшающих сохранение тепла в доме.
Желание иметь частный дом толкает людей на поиск дешевых материалов для строительства.Керамзитовые блоки – как раз тот материал, который пользуется все большей популярностью у застройщиков.
Главная особенность керамзитобетона в том, что, помимо низкой стоимости на рынке, его можно изготовить своими руками. Предлагаем рассмотреть основные нюансы и хитрости, а также состав керамзитобетонных блоков по ГОСТу.
Что нужно для начала?
Процесс изготовления несложный, главное соблюдать пропорциональное соотношение компонентов — 1:3:8.Воду добавляют из расчета 200 литров на 1 м3.
Материалы (редактирование)
Инструменты
Ручной вибропресс
Можно купить в магазинах, где продается все для строительства. Примерная стоимость 7-10 тысяч рублей. Также можно заказать у производителей. В конструкции уже есть специальные формы для отливки блоков. Также станок можно сделать своими руками из старого двигателя и металлической столешницы.
При наличии необходимого количества форм и лишней пары рук в день можно изготовить около 150 керамзитобетонных блоков.
За один рабочий цикл машина производит от 1 до 4 блоков. А если собрать команду из нескольких рабочих, то количество может увеличиться примерно в 2 раза. Блоки можно сделать без оборудования, главное подобрать вместительную емкость для замеса и разлить по формам.
Сами формы для керамзитобетонных блоков могут быть металлическими, пластиковыми, деревянными (скрепляются уголками из металла, внутри также могут быть обшиты).Для образования пустот в блоках некоторые мастера используют пластиковые бутылки, наполненные водой.
При замешивании раствора сначала берется точное количество воды. Смешивают песок, цемент и керамзит, песок, а затем вводят жидкие вещества (воду, пластификаторы). По внешнему виду смесь должна получиться как размягченный пластилин.
Сушка керамзитобетона
Завершающим этапом изготовления блоков из керамзитобетона является сушка готового изделия.
Это занимает около 2 дней. Во влажную погоду скала увеличивается.
Затем блоки укладываются на поддоны в ряд по 3-4 штуки. Готовые блоки не должны подвергаться воздействию солнечных лучей и дождя; лучше держать их под навесом. Вводятся в эксплуатацию через 1-1,5 недели после изготовления.
Лучший вариант — сушить месяц. Перед укладкой блоки очищают от шероховатостей и неровностей.
Себестоимость керамзитобетонных блоков своими руками
По некоторым оценкам примерная цена керамзитобетонных блоков составит около 20 руб.Для сравнения, цена готовой продукции около 80 рублей. Экономия, как говорится на лицо.
Запущена третья линия крупнейшего в регионе производства легких заполнителей LECA – Leca Asia
Таким образом, теперь LECA IRAN стала крупнейшим производителем LECA в регионе, открыв третью линию и начав строительство четвертой линии по производству керамзитобетона и третьей линии по производству легких блоков.
LECA Иран был зарегистрирован по лицензии LECA International более 40 лет назад. Завод расположен в 20 км от Савеха, Иран. Открыв первую производственную линию в 1976 году, что стало началом массового производства с 1981 года под названием LECA IRAN. Вторая производственная линия начала свою деятельность в 2006 году.
В настоящее время на заводе LECA работают три линии по производству легких заполнителей номинальной мощностью 750 000 кубометров в год и три линии по производству легких блоков номинальной мощностью 35 000 000 блоков в год.
В настоящее время LECA предпринимает большие шаги, строя четвертую линию по производству керамзитобетона и одну линию по производству легких блоков, что сделает ее крупнейшим производством керамзита не только в Азии и на Ближнем Востоке, но и на всей планете.
Керамзитовый заполнитель представляет собой пористый керамический продукт с однородной структурой пор. Производится во вращающихся печах из сырья, содержащего глинистые минералы. Сырье подготавливают, укладывают на поддоны, а затем подвергают обжигу при температуре от 1100 °C до 1200 °C, что приводит к значительному увеличению объема за счет расширения.Внутренняя ячеистая структура зерна LECA с тысячами заполненных воздухом полостей обеспечивает тепло- и звукоизоляционные свойства.
Производство искусственных легких заполнителей становится все более популярным из-за дефицита, изменчивости плотности, а также неравномерного распределения природных источников по всему миру. Среди искусственных легких заполнителей легкий керамзитовый заполнитель (LECA) изготавливается из глины как широко доступного сырья, которое позволяет производить легкую гальку с одинаковой плотностью и лучшим качеством.
Ученые почти уверены, что деятельность человека вызывает глобальное потепление. Сумма энергии, которая потребляется для производства материалов, называется воплощенной энергией. Минимизация этой энергии помогает уменьшить выброс углекислого газа (CO 2 ) и, как следствие, уменьшить потенциал глобального потепления.
Поскольку легкий заполнитель LECA имеет меньшую плотность, чем заполнитель нормального веса, бетон, изготовленный из LECA, имеет воплощенную энергию почти вдвое по сравнению с бетоном обычного веса. Выделение углекислого газа легким заполнителем составляет около 0.16 кг CO2 на килограмм заполнителя по сравнению с портландцементом, который немного меньше, чем один кг CO 2 на килограмм.
Принимая во внимание воплощенные энергетические критерии и выбросы парниковых газов легким заполнителем LECA, как сам заполнитель, так и легкий бетон, этот материал может внести значительный вклад в повышение устойчивости.
Плотность легкого бетона LECA варьируется от 600 кг/м 3 до 1900 кг/м 3 . уменьшить количество армирующей стали.Все эти сбережения влияют на решение архитекторов и инженеров-строителей использовать легкий бетон во многих проектах.
В то время как LECA превосходит повседневные требования к дизайну, такие как противопожарная защита и звукоизоляция, где основным соображением является энергосбережение, он предлагает сочетание легкости, теплоизоляции и низкого водопоглощения.
Комментариев нет