Материалы для производства стеклопластиковой арматуры: Материалы для производства стеклопластиковой арматуры
Производство стеклопластиковой арматуры
Основное направление работы ТПК «К-АРМА» – производство строительного материала нового поколения – композитной (стеклопластиковой) арматуры.
Процесс производства
С использование оборудования СПА-2 по технологии, разработанной лабораторией на базе Ивановского Государственного Химико-Технологического Университета (ИГХТУ), у нас есть возможность производить арматуру диаметром от 4 до 16 мм с высокими прочностными показателями. Производительность данной линии составляет от 11000 до 25000 метров в сутки в зависимости от диаметра производимой арматуры (при работе 23 часа, 1 час технологический перерыв), что позволяет в короткие сроки выполнять любые заказы клиентов.
- Нити из бобин внутренней размотки со стеллажа подаются в ванну пропитки со смолой через нагревательные элементы. Подогрев необходим для активизации замасливателя, что улучшает пропитку нитей ровинга смолой. Для предотвращения скручивания нитей и их равномерного распределения установлен разделитель нитей.
- После пропитки на входе из ванны происходит отжим и формирование стержня.
- Сформированный стержень будущей стеклопластиковой арматуры подается в устройство подготовки профиля, который придает цилиндрическую форму стержню арматуры и удаляет воздух за счет армирования базальтовой или стеклопластиковой нитью.
- Следующий этап производства – полимеризация в печи, длинна которой 6 метров, состоящая из 4 секций. В каждой секции установлен термодатчик для соблюдения температурного режима. Температура в печах составляет от 230 до 300 С в зависимости от диаметра стержня.
- После термообработки арматура поступает в ванну водяного охлаждения. Охлаждение происходит за счет циркуляции воды под действием насоса.
- Движение арматуры по всем этапам производства придается протяжным устройством, полиуритановыми валами, которые в свою очередь приводятся в движение электродвигателем по цепной передаче. Мощность привода – 2,5 тонн/силы. Диаметр протягиваемой арматуры 4-16 мм.
- Нарезка арматуры на заданную длину происходит на отрезном механизме, состоящем из дисковой пилы, счетчика длины арматуры. Длина нарезки от 0,1 метра до 300 метров.
- Готовая продукция в основном связывается в пучки (если нарезка идет прутками по 3 или 6 метров) либо в бухты по 50 или 100 метров.
- Управление всеми процессами и контроль за показаниями датчиков происходит на основном и дополнительном щитках управления.
Материалы
Одно из немаловажных условий производства арматуры с высокими техническими характеристиками является использование только высококачественного сырья (олигомеров, компаунда, отвердителей, катализаторов). Рецептура технологии, разработанная лабораторией Ивановского Государственного Химико-Технологического Университета – научно обоснована, многократно проверена опытным путем, рассчитана с учетом используемого сырья.
Стеклопластиковый ровинг
При производстве стеклопластиковой арматуры с ребристой поверхностью (периодического профиля) используется стеклоровинг однопроцессный (директ-ровинг) компании Jushi (Джуши), Китай – некрученая прядь из стеклянных элементарных нитей, состоящая из одной комплексной нити. Основные характеристики – текс и диаметр элементарной нити (Текс (tex) – вес 1 км ровинга в граммах).
Основные марки однопроцессного ровинга Jushi (директ-ровинга), используемые при производстве композитной арматуры:
Замасливатели, которые применяют при производстве ровингов, обеспечивают его совместимость с различными типами смол: полиэфирные, эпоксидные, фенолоформальдегидные и термопластичные (ПП, ПА, ПЭТФ, ПЭ) и др.
Смола эпоксидная
Эпоксидная смола LR1100, производство компании «Jana», Саудовская Аравия – немодифицированная жидкая эпоксидная смола (Аналог ЭД-20, DER 331, CHS-EPOXY 520).
Свойства:
- средневязкая эпоксидная смола с высокой хим. активностью
- совместима с различными отвердителями, активными разбавителями и катализаторами
- низкое содержание гидролизуемого хлора и как следствие незначительная кристаллизация смолы при низких температурах
- соответствует требованиям FDA (Министерство здравоохранения США).
Полимеризированная смола демонстрирует:
- превосходные механические и электрические свойства
- отличную химстойкость и водостойкость.
Наименование показателя | Норма |
Внешний вид | Вязкая, прозрачная жидкость |
Массовая доля эпоксидных групп, % | 18,4–19,4 |
Массовая доля омыляемого хлора, % | не более 0,1 |
Динамическая вязкость, Па*с, при 25°С | 11–14 |
Анализ эпоксидной смолы
Изометил тетрагидрофталевый ангидрид (ИМТГФА)
Изо-МТГФА, ИМТГФА (Изометилтетрагидрофталевый ангидрид), легкокристаллизующаяся растворимая жидкость. Используется в качестве отвердителя эпоксидных смол горячего отверждения. Страна производитель Китай.
Прозрачная жидкость без механических включений светло-желтого цвета, переходящая в пастообразное состояние. Она легко кристализуется (ниже 20°С), хорошо растворима в бензине, толуоле, ацетоне, эфире.
Химическая формула: C9h20O3
Техническая характеристика | Показатель |
Плотность (г/см³ при 20°С) | 1.21±0.05 |
Температура кристализации (°С) | -15 |
Коэффициент кислотности (mgKOH/g) | 660-685 |
Продолжительность желатинизации (час) | в пределах 6-8 |
Ускоритель
Алкофен МА (аналог УП-606/2, DMP-30) 2, 4, 6 — трис (диметиламинометил) фенол.
Вязкая прозрачная жидкость от желтого до коричневого цвета.
Химическая формула: С15h37N30.
Наименование показателя | Норма |
Массовая доля основного вещества, % | не менее 93,0 |
Массовая доля титруемого азота, % | не менее 8,0 |
Плотность при 25°С, г/см³ (не нормируется) | 0,98 |
Все указанные выше материалы для производства композитной арматуры вы также можете приобрести в компании «К-Арма». Ознакомиться с ценами и оставить заявку можно с помощью нашего каталога.
Композитные материалы давно признаны развитыми странами и максимально успешно используются строителями по всему миру.
Строительство – это безграничный мир. Качественная строительная стеклопластиковая арматура в большинстве случаев с успехом заменяет стальную арматуру класса А-3 и пользуется огромным спросом. Композитные материалы незаменимы для строительства и ремонта фундаментов любых видов и стен зданий любой этажности, дорог, свай, мостов, особенно для эксплуатирования в зонах повышенной влажности и химически агрессивных средах.
Она легче, дешевле, прочнее и долговечнее стальной.
Г.Д. Андреевская подробно рассматривает влияние
условий фиксируется структура расплавленного стекла более гомогенная, чем структура объемных образцов. ![]() происходит настолько быстро, что температура на их поверхности и в центре бывает практически одинакова. Это обеспечивает от сутствие внутренних остаточных температурных напряжений. С увеличением диаметра волокна скорость остывания на поверх температурные напряжения. Кроме того, при вытягивании волок на происходит ориентация микротрещин вдоль оси волокна. Чем больше скорость вытягивания (тонкое волокно), тем больше вероятность ориентации трещин, и наоборот, при малых скоро стях в грубом волокне вероятность ориентации трещин умень шается, что и обусловливает его меньшую прочность по сравнению с тонким. ![]() П.А. Ребиндером и его школой [5, 6] даны теоретические обо снования влияния окружающей среды и длительности воздейст вия нагрузок на прочность стеклянного волокна. Известно, что чем выше влажность окружающей среды, тем ниже прочность волокна. Снижение его прочности в этих условиях объясняется прониканием влаги в микротрещины. Разрастание микротрещин происходит в результате двух явлений. С одной стороны, на стенках микротрещин молекулы воды образуют адсорбционные слои. Молекулы этих слоев стремятся двигаться во все стороны вдоль поверхностей трещин, и в частности к их вершинам, и тем самым способствуют углублению трещин. С другой стороны, тон кая пленка влаги, т. ![]() внутри трещины, вызывает расклинивающий эффект при ее суже нии (при деформации волокна). Нам уже известно, что при вытягивании стеклянного волокна происходит ориентация трещин вдоль оси волокна. Следователь но, в стеклянном волокне часть трещин расположена параллельно его оси, а часть трещин может иметь иное направление. Количе ственное соотношение трещин вдоль оси волокна и трещин других направлений зависит от скорости выработки волокна и, как след ствие, от диаметра волокна. При растяжении волокон посредством внешней нагрузки тре щины, ориентированные вдоль оси волокна, будут сужаться, а влага, находящаяся в них, из-за расклинивающего эффекта будет их удлинять. ![]() влага будет создавать расклинивающий эффект, способствующий дальнейшему развитию трещин, и тем самым еще более снижать прочность стеклянного волокна. Таким образом, присутствие молекул воды во всех трещинах, расположенных на поверхности волокна независимо от их на правления, снижает прочность волокна. Адсорбционная влага производит механическое разрушение волокон в напряженном состоянии, причем особенно велико будет разрушающее действие этой влаги при изменениях напряженного состояния образцов. Следовательно, надежная защита полимерным связующим волок на в арматурном стержне от проникания влаги является весьма важной задачей. ![]() волокон — процесс обратимый, так как после высушивания об разцов первоначальная прочность волокна может восстановиться. Такое свойство волокна проявляется и в стеклопластиковой ар матуре. А.Ф. Зак и ЮЛ. Манько изучали изменение прочности стеклян ного волокна алюмоборосиликатного состава при нагреве. При этом установлено, что температурные воздействия в пределах О.. . 500°С не сказываются на снижении прочности волокна. Однако после термообработки стеклянных волокон при темпе ратуре выше 200°С и последующем охлаждении прочность их при повторном нагреве до 300°С составляет 70% исходной, а при тем пературе 500°С — всего лишь 35 . ![]() кратные нагревы стеклянного волокна приводят к непрерывному снижению его прочности после охлаждения [7]. Наиболее высокая механическая прочность волокна достигает ся при его охлаждении до минусовых температур. Это явление объясняется вымораживанием влаги при низких температурах, в результате чего устраняется расклинивающий эффект несжи маемой адсорбционной влаги, которая ранее находилась в мик ротрещинах стеклянного волокна. Следует заметить, что повыше ние прочности волокна при воздействии отрицательных темпера тур — процесс обратимый, так как после помещения волокна в зону положительных температур прочность его вновь снижается до исходных значений. ![]() Следует предположить, что при температурных воздействиях на стеклопластиковую арматуру возможны подобные изменения ее прочности. Модуль деформации волокна при повышении тем пературы меняется незначительно. Только при температуре, близ кой к температуре стеклования, можно наблюдать некоторое снижение его значений, зафиксированных при комнатной темпе ратуре. 12 Стеклопластиковая арматура должна обладать высокой корро зионной стойкостью. Химическая стойкость арматуры предопре деляется стойкостью основного материала арматуры, т.е. стек лянного волокна, поэтому изучение причин снижения прочности волокна при воздействии агрессивных сред представляет опреде ленный интерес. ![]() гентов на стеклянное волокно наблюдается процесс растворения волокна, т.е. химического взаимодействия состава стеклянного волокна со средой. При таком взаимодействии происходит либо равномерное растворение всех компонентов стекла, либо выще лачивание некоторых. Характер и скорость разрушения волокон при этом зависят от химического состава самого стекла и воздей ствующего на него реагента. После процесса взаимодействия наблюдается снижение массы стеклянного волокна и его прочно сти. При более или менее равномерном растворении всех компонен тов стекла происходит утонение стеклянного волокна. В тех слу чаях, когда в раствор переходят не все компоненты, несмотря на глубокое и полное растворение части компонентов, волокно сохраняет цилиндрическую форму и, как правило, первоначаль ный диаметр. ![]() ет собой пространственный каркас из нерастворенного компонен та, обладающий довольно сильными молекулярными связями. На пример, при действии раствора серной кислоты на алюмобороси- ликатное стеклянное * волокно растворяются все компоненты стекла, кроме кремнезема. При этом характер разрушения воло кон зависит от их диаметра и продолжительности обработки раст вором. На массивном стекле возникают поверхностные трещины, имеющие форму сот. На грубом волокне появляются поперечные трещины, причем от волокон отслаиваются отдельные части кольцевидной формы. Такие волокна рассыпаются на отдельные небольшие куски. В процессе воздействия раствора щелочи на алюмоборосиликатное волокно химическим анализом раствора установлено, что происходит растворение всех компонентов стекла и диаметр волокна при этом уменьшается. ![]() Таким образом, в результате многочисленных исследований химической стойкости стеклянного волокна установлено, что все волокна в большей или меньшей мере подвержены разруше нию при воздействии различных агрессивных сред, причем сте пень, скорость и характер разрушения зависят от многочислен ных факторов: химического состава стекла, количества компо нентов, вида реагентов, диаметра, времени, температуры, состоя ния поверхности водокна и др. Влияние агрессивных сред на прочность стеклянного волокна в ИСиА Госстроя БССР изучал С.С. Жаврид [8, 9]. Жгуты стек лянных волокон длиной 400 мм выдерживали в сушильных шка фах при температуре 110 . . . 120°С в течение 1 ч, после чего эти жгуты средней частью погружали в раствор реагента и кипятили Через 6, 12, 24 и 48 ч жгуты извлекали,
просушивали и опре |
Сырье для производства композитной арматуры
Основой для производства стеклопластиковой арматуры является ровинг.
Ровинг – это жгут из нитей стекловолокна. Виды ровинга: прямой, базальтопластиковый, ровинг на основе натуральных волокон, другие, менее распространенные типы ровинга. Покупая ровинг у нас, Вы можете быть уверены в его качестве и стабильности поставок — многолетние связи с нашими зарубежными поставщиками гарантируют Вам лучшие цены и качество.
Эпоксидная смола
Является одним из компонентов при производстве стеклопластиковой арматуры. Компания «POLYARM» применяет эпоксидные смолы, как составляющее в технологическом процессе производства стеклопластиковой арматуры и другой продукции. Большое количество волокон собираются в пучок, пропитываются смолами, которые потом, с помощью отвердителя, отвердевают. В результате мы получаем полимерную арматуру с уникальными физическими и химическими свойствами.
Отвердитель
Эпоксидные смолы приобретают необходимые свойства только в сочетании с различными отвердителями. Технологический процесс выглядит следующим образом: пучки стекловолокна пропитываются эпоксидной смолой и, для того чтобы они стали безупречно твердыми, мы используем специальный отвердитель. Продукция, которая получается путем полимеризации, с использование предлагаемого нами отвердителя не боится влаги, становится устойчивой к химическим, температурным воздействиям. Кроме того, он менее токсичен и летуч, что намного упрощает технологический процесс.
Ускоритель
Ускорители — это добавки, которые ускоряют реакцию между смолой и отвердителем.
Скорость затвердевания очень важна при производстве полимерной арматуры и других видов полимерной продукции. Для этого, при производстве полимерной продукции, не обойтись без специальных добавок, которые ускоряют процесс затвердевания и называются укорителями отвердевания. Наша компания использует в технологическом процессе только высококачественные ускорители отвердевания, которые могут быть использованы не только при производстве стеклопластиковой арматуры, но и других технологических процессах.
Пластификатор (ДЭГ-1 или аналоги)
Используется для пластификации и снижения вязкости смолы снижения вязкости смолы и пластификации стеклопластика
Купить сырье для производства полимерной арматуры
«Научно-Производственная Компания «Композит» предлагает ровинг, смолы и отвердители и ускорители по самым выгодным ценам в Украине. Для удобства наших клиентов, наши склады расположены в г. Киеве, что гарантирует быструю и удобную доставку товара нашим клиентам. Большие объемы наших закупок продукции для производства предоставляют Вам отличную цену и качественное сырье.
Руководство по проектированию стекловолокна и композитных материалов
Целью данного руководства по проектированию является предоставление некоторой общей информации о стекловолокне и композитных материалах, а также объяснение того, как проектировать изделия из этих материалов. Если у вас есть конкретные вопросы, свяжитесь с нашими инженерами из Performance Composites, и они с радостью вам помогут.
Композитные материалы
Композитные материалы изготавливаются путем объединения двух материалов, один из которых представляет собой армирующий материал (волокно), а другой — матрицу (смола).Комбинация волокна и матрицы обеспечивает характеристики, превосходящие любой из материалов, используемых по отдельности. Примерами композитных продуктов в природе являются дерево, бамбук и кость, а примером раннего искусственного композита является глина и солома, которые использовались более 10 000 лет.
Композитные материалы очень универсальны и используются в различных областях. Композитные детали обеспечивают превосходную прочность, жесткость и малый вес, и им можно придать любую форму.Идеальным применением являются большие конструкции сложной формы, такие как покрытия из стекловолокна. Композитные изделия идеально подходят для приложений, где требуется высокая производительность, таких как аэрокосмическая промышленность, гоночные автомобили, лодочный спорт, спортивные товары и промышленное применение. Наиболее широко используемым композитным материалом является стекловолокно в полиэфирной смоле, которое обычно называют стекловолокном. Стеклопластик легкий, устойчивый к коррозии, экономичный, легко обрабатывается, обладает хорошими механическими свойствами и имеет более чем 50-летнюю историю. Это доминирующий материал в таких отраслях, как судостроение и коррозионное оборудование, и он играет важную роль в таких отраслях, как архитектура, автомобилестроение, медицинское, рекреационное и промышленное оборудование.
Типичные композитные материалы могут быть изготовлены из таких волокон, как стекловолокно, углеродное волокно (графит), кевлар, кварц и полиэстер. Волокна бывают вуалевого мата, мата из коротких волокон, тканой ткани, однонаправленной ленты, двухосной ткани или трехосной ткани. Смолы обычно представляют собой термоотверждающиеся смолы, такие как полиэфирные, винилэфирные, эпоксидные, полиуретановые и фенольные.Смолы начинаются как жидкость, полимеризуются в процессе отверждения и затвердевают. Массовое соотношение волокон к смоле может варьироваться от 20% волокон к 80% смолы, до 70% волокон к 30% смолы. Как правило, более высокое содержание волокон обеспечивает еще большую прочность и жесткость, а непрерывные волокна обеспечивают лучшую прочность и жесткость. Использование композитных материалов дает инженерам возможность адаптировать комбинацию волокон и смолы в соответствии с требованиями дизайна и работать лучше, чем стандартные материалы.
Композитные материалы заменяют металлы и пластмассы во многих отраслях промышленности, а композиты являются предпочтительным материалом для многих новых применений. См. таблицу 1 для сравнения стоимости и свойств коммерческих композитных материалов с алюминием, сталью и деревом.
ТАБЛИЦА 1
Стекловолокно и полиэстер | Графит и эпоксидная смола | Древесина (дугласова пихта) | Алюминиевые листы 6061 T-6 | Стальные листы | |
Стоимость материала $/фунт | 2 доллара.![]() | $9.00-20.00+ | 0,80 $ | 4,50–10,00 $ | 0,50–1,00 $ |
Прочность, предел текучести (psi) | 30 000 | 60 000 | 2 400 | 35 000 | 60 000 |
Жесткость (psi) | 1,2 x 10 6 | 8 x 10 6 | 1.8 x 10 6 | 10 х 10 6 | 30 x 10 6 |
Плотность (фунт/дюйм 3 ) | .055 | .065 | .02 | .10 | .30 |
Наиболее распространенным производственным процессом для стекловолокна является процесс мокрой укладки или распыления с использованием измельчителя с использованием открытой формы. Форма детали определяется формой литейной формы, а поверхность литейной формы обычно соприкасается с внешней стороной детали. Сначала на форму наносят разделительный состав, чтобы предотвратить прилипание детали из стекловолокна к форме. Гелькоут, представляющий собой пигментированную смолу, наносится на форму для придания цвету детали. Затем стекловолокно и смола наносятся на форму, и стекловолокно сжимается роликами, которые равномерно распределяют смолу и удаляют воздушные карманы. Несколько слоев стекловолокна наносятся до тех пор, пока не будет достигнута желаемая толщина.Как только смола затвердеет, деталь вынимается из формы. Излишки материала обрезаются, и деталь готова к покраске и сборке. Существуют также закрытые формы для изготовления деталей из стекловолокна.
Процесс вакуумной инфузии (облегченный RTM)
Процесс вакуумной инфузии (VIP) — это метод, в котором используется вакуум для втягивания смолы в ламинат. Процесс выполняется сначала путем загрузки волокон ткани и материалов сердцевины в форму, а затем либо с помощью вакуумного мешка, либо с помощью контрформы, чтобы закрыть форму и создать вакуумное уплотнение. Вакуумный насос используется для удаления всего воздуха из полости и уплотнения волокон и материалов сердцевины. Все еще под вакуумом в полость формы вливается смола, чтобы смочить волокно. Расположение вакуумных портов и точек ввода смолы необходимо тщательно спланировать, чтобы обеспечить полную инфузию смолы. Преимущество процесса вакуумной инфузии заключается в создании ламината с очень высоким содержанием волокон (до 70% волокон по весу), что позволяет получить очень прочную и жесткую деталь при минимальном весе.Вакуумная инфузия также является эффективным производственным процессом для сложного ламината с большим количеством слоев волокон и материалов сердцевины.
Процесс производства препрега
Препрег — это ткань, предварительно пропитанная смолой (обычно эпоксидной). Смола отверждается до стадии B, создавая гель, который не является ни жидким, ни твердым. Материалы препрега необходимо хранить в замороженном состоянии, чтобы предотвратить его полное отверждение. Препрег разрезают на формы и наносят на форму слоями.Затем на материал помещается вакуумный мешок, и вакуумный насос вытягивает весь воздух, сжимает слои вместе и уплотняет материалы. Затем загруженную форму помещают в печь, в которой смола разжижается, чтобы она смачивала волокна. При повышении температуры смола полимеризуется и затвердевает. Преимуществом препрега является очень жесткий контроль соотношения волокон, малое количество пустот и точное расположение ткани и однородность толщины. Препреги обычно используются для аэрокосмической продукции и легких деталей с высокими эксплуатационными характеристиками.
Информация о конструкции
Как и любой материал, стеклопластик имеет преимущества и недостатки; тем не менее, в таких областях применения, как коррозия, мелкосерийное и среднесерийное производство, очень большие детали, контурные или закругленные детали и детали, требующие высокой удельной прочности, предпочтительным материалом является стекловолокно. Стекловолокно — идеальный материал для конструктора, потому что детали могут быть адаптированы для обеспечения прочности и/или жесткости в необходимых направлениях и местах путем стратегического размещения материалов и ориентации направления волокон.Гибкость конструкции и производства стекловолокна дает возможность консолидировать детали и включать в них множество функций, чтобы еще больше снизить общую стоимость детали. Некоторые общие рекомендации по проектированию перечислены ниже:
Толщина материала | Обычно в диапазоне от 1/16 до 1/2 дюйма. Можно использовать сэндвич-конструкцию для получения более легких и жестких деталей. |
Угловой радиус | Рекомендуется 1/8″ или больше |
Форма | Дублирует форму формы.![]() |
Размерный допуск | Сторона инструмента может быть + 0,010 дюйма от инструмента Сторона без инструмента + 0,030 дюйма |
Поверхность | Сторона, обращенная к инструменту, может быть класса A Сторона, обращенная к инструменту, будет шероховатой, но ее можно сгладить Можно покрасить гелем или использовать любой другой |
Усадка | .002 в/в |
Электрические свойства | RF Прозрачный Отличные изоляционные характеристики Может обеспечивать экранирование электромагнитных помех за счет проводящего покрытия |
Огнестойкий | Имеются огнезащитные смолы, отвечающие различным спецификациям ASTM или UL |
Коррозия | Имеются смолы для защиты от коррозии, особенно для горячих солевых растворов, большинства кислот, щелочей и газообразного хлора |
Механика и анализ композиционных материалов
Механические свойства металлов и пластмасс изотропны (одинаковая прочность и жесткость во всех направлениях). Механические свойства композиционных материалов анизотропны (разная прочность и жесткость в зависимости от направления волокон и нагрузки). Разница между изотропными и анизотропными свойствами усложняет анализ конструкции композита, но большинство программ МКЭ имеют возможности для анализа композитов. Анизотропное свойство композитных материалов позволяет инженеру адаптировать композитные материалы для добавления прочности и жесткости только в тех областях и направлениях, где это необходимо, тем самым снижая вес и стоимость.Наши инженеры будут рады помочь вам с анализом и проектированием.
Инструменты
Инструменты или формы используются для определения формы деталей из стекловолокна. Деталь из стекловолокна подхватит все формы и особенности форм; поэтому качество детали сильно зависит от качества пресс-формы. Формы могут быть как мужскими, так и женскими. Охватывающие пресс-формы являются наиболее распространенными, и они производят деталь с гладкой внешней поверхностью, в то время как охватываемые пресс-формы производят гладкую внутреннюю поверхность (см. рисунок ниже).
Для очень коротких производственных циклов (менее 10 деталей) временные формы могут быть изготовлены из дерева, пенопласта, глины или гипса. Эти формы экономичны и могут быть изготовлены быстро, что позволит изготавливать недорогие прототипы деталей. Для крупносерийного производства формы обычно изготавливаются из стекловолокна. Эти формы имеют ожидаемый срок службы более 10 лет и более 1000 циклов. Формы из стекловолокна недороги и обычно стоят в 6-10 раз дороже самой детали.
Форма является зеркальным отражением детали. Для создания формы требуется мастер (заглушка). Мастер может быть реальной деталью или может быть изготовлен из дерева, пенопласта, гипса или глины. Точная форма и отделка мастера будут перенесены в форму. После того, как мастер готов, его полируют, натирают воском, и на мастере создается форма. Технология изготовления формы аналогична изготовлению детали из стекловолокна, за исключением того, что для изготовления прочной формы с низкой усадкой и хорошей размерной стабильностью используются вспомогательные материалы (гелевое покрытие, смолы и ткань). После ламинирования формы ее укрепляют деревянной, стекловолоконной или металлической конструкцией, чтобы она сохраняла правильную форму. Затем форму снимают с мастера и запускают в производство.
Материалы для производства стекловолокна — пластик Arrowhead
Термореактивные материалы (стекловолокно и пластик, армированный стекловолокном)В мире пластмасс существует два основных типа материалов: термопластичные смолы и термореактивные смолы. Термопластичные материалы составляют большую часть обычных пластиков, которые окружают нас в повседневной жизни. Эти материалы являются твердыми при комнатной температуре и могут быть нагреты до «жидкого» состояния, впрыснуты в форму, а затем снова охлаждены до твердого состояния в виде объекта. Мы используем эти термопласты в процессе термоформования.
Процесс термоформования не доводит пластик до полностью жидкого состояния, а вместо этого включает нагрев листа пластика до температуры, при которой лист становится ковким или формуемым. При этой температуре детали можно придать желаемую форму, используя вакуум, чтобы притянуть горячий лист пластика к поверхности формы.
Если снова нагреть термопластический материал до достаточно высокой температуры, он снова станет жидкостью. Благодаря тому, что их можно вернуть в жидкое состояние, термопластичные смолы (особенно товарные смолы, такие как полиэтилен, полипропилен, ТПО и АБС), как правило, легко перерабатываются.
Термореактивные смолы образуются в результате химической реакции, называемой полимеризацией.Эти смолы находятся в жидкой форме при комнатной температуре и при добавлении отвердителя превращаются из жидкости в твердое вещество. После отверждения или полимеризации термореактивная смола не может снова превратиться в жидкость — этот процесс необратим.
При производстве композитов доступно несколько типов и составов смол. Наиболее широко используемые полимеры включают полиэфирную смолу, винилэфирную смолу и эпоксидную смолу.
Термин «композиты» буквально означает «собирать воедино»; то есть комбинировать разные материалы. В этом случае термореактивная смола комбинируется с волокнистым материалом, известным как армирование. Волокно усиливает полимерную матрицу; то есть волокно обеспечивает прочность, а полимерная смола скрепляет волокно и обеспечивает форму изделия. Многочисленные комбинации смолы и волокна позволяют композитам обеспечивать определенные свойства и соответствовать требованиям конечного пользователя. Наиболее часто используемые армирующие волокна включают стекловолокно (стекловолокно), углеродное волокно и арамидное волокно, чаще называемое Kevlar®.
Выбор композиционных материалов и производственного процесса зависит от требуемых свойств конечного продукта, скорости производства и факторов стоимости для отдельного продукта. Мы используем два основных метода производства: открытое формование и закрытое формование . В технологии открытого формования полимерная смола подвергается воздействию атмосферы во время процесса формования и отверждения. Как и при закрытом формовании, процесс происходит внутри полости формы, где материалы не подвергаются воздействию атмосферы.
Руководство для начинающих по армированным волокнам пластикам (FRP) — Crafttech Industries — Высокоэффективные пластики
Армированный волокном пластик (FRP), также известный как армированный волокном полимер, на самом деле представляет собой композитный материал
, представляющий собой полимерную матрицу, смешанную с некоторыми армирующими материалами, такими как волокна. Волокна обычно базальтовые, углеродные, стеклянные или арамидные; в некоторых случаях также можно использовать асбест, дерево или бумагу.
Формирование ФРП
Возвращаясь к основам, есть два процесса, посредством которых получают полимер: ступенчатая полимеризация и аддитивная полимеризация.Композитные пластмассы образуются, когда пара однородных материалов, обладающих разными характеристиками, склеивается вместе для получения конечного продукта с желаемыми механическими свойствами и свойствами материала. Эти композитные материалы могут быть двух типов: армированные волокном и армированные частицами.
Пластмасса, армированная волокном относится к категории, в которой механическая прочность и эластичность пластмасс повышены за счет включения волокнистых материалов. Матрица, представляющая собой основной материал, лишенный армирующих волокон, твердая, но сравнительно слабая, и ее необходимо упрочнить путем добавления мощных армирующих волокон или нитей.Именно волокно имеет решающее значение для отличия исходного полимера от FRP.
Большинство этих пластиков формируются с помощью различных процессов формования, при которых форма или инструмент используются для размещения заготовки волокна, представляющей собой сухое волокно или волокно, содержащее определенную долю смолы. После «смачивания» сухих волокон смолой происходит «отверждение», при котором волокна и матрица принимают форму формы. На этой стадии время от времени применяется тепло и давление. Различные методы включают, среди прочего, компрессионное формование, формование в баллоне, обмотку оправки, автоклавирование, намотку нитей и мокрую укладку. Посмотрите это видео о процессе:
Общие свойства FRP
Эти композитные материалы обычно имеют малый вес и высокую прочность. Они настолько прочны, что автомобильная промышленность все больше заинтересована в их использовании для замены части металла в автомобилях. Пластмассы, армированные волокном, могут быть такими же прочными, как некоторые металлы, но они намного легче и, следовательно, более экономичны.
Можно настроить свойства армированного волокном пластика в соответствии с широким спектром требований.Полимеры, армированные волокном, обычно обладают впечатляющими электрическими и компрессионными свойствами, а также демонстрируют высокую устойчивость к воздействию окружающей среды. Одним из важных факторов, который делает эти материалы популярными в различных отраслях промышленности, является производственный процесс, который является весьма рентабельным. Уровень производительности от среднего до высокого, а готовое склеивание демонстрируется с разнородными материалами.
Другие исключительные свойства армированных волокном пластиков включают высокую теплоизоляцию, структурную целостность и огнестойкость, а также устойчивость к ультрафиолетовому излучению и устойчивость к химическим веществам и другим агрессивным материалам.
Характеристики пластмасс, армированных волокном, зависят от определенных факторов, таких как механические свойства матрицы и волокна, относительный объем обоих этих компонентов, а также длина волокна и ориентация внутри матрицы.
Общие волокна включают:
- Стекло является очень хорошим изоляционным материалом и при смешивании с матрицей образует стекловолокно или пластик, армированный стекловолокном. По сравнению с углеродным волокном оно менее прочное и жесткое, менее хрупкое и дорогое.
- Пластики , армированные волокном, на основе углерода обладают высокой прочностью на растяжение, химической стойкостью, жесткостью и термостойкостью, а также низким тепловым расширением и весом.
Атомы углерода образуют кристаллы, расположенные в основном вдоль длинной оси волокна. Такое выравнивание делает материал прочным за счет высокого отношения прочности к объему.
- Арамид представляет собой волокнистый компонент, из которого получают прочные и термостойкие синтетические волокна. Он находит широкое применение во многих отраслях промышленности.
Пластмассы, армированные волокном, находят широкое применение в автомобильной, аэрокосмической, строительной и морской отраслях. Стекло , армированный волокном пластик s — очень хороший вариант для энергетики, поскольку они лишены какого-либо магнитного поля и обладают значительной устойчивостью к электрическим искрам. Применение углеродных волокон становится все более разнообразным, что проявляется в появлении углеродных волокон в спортивных товарах, планерах и рыболовных удочках, а также в применении FRP в Японии к гидравлическим воротам.
Ищете дополнительную информацию о пластиковых материалах? Загрузите наше бесплатное руководство!
Различные типы и формы стекловолокна и способы их использования
Стекловолокно — это тип армированного волокном пластика, в котором стекловолокно является армированным пластиком. Вот почему стекловолокно иногда называют пластиком, армированным стекловолокном, или пластиком, армированным стекловолокном.
Стеклянные волокна могут состоять из различных видов стекла.Сплющенное в лист стекловолокно хаотично расположено или вплетено в ткань. Стекловолокно легкое, прочное и менее хрупкое.
Одной из наиболее привлекательных особенностей стекловолокна является то, что ему можно придавать различные формы. Это объясняет, почему стекловолокно широко используется в строительстве, гражданском строительстве, коммерческих и жилых продуктах, самолетах, кровле и спортивном оборудовании.
В конце 18-го -го -го века французским ученым Рене Фершо де Реомюром было открыто стекловолокно, хотя оно в значительной степени осталось на втором плане.Записано, что немецкий стеклодув изготовил кусок ткани, переплетая шелковые волокна в одном направлении со стеклянными волокнами в другом.
В 1893 году на Всемирной ярмарке в Чикаго Эдвард Д. Либби ─ из Libbey Glass Company ─ продемонстрировал платье из этой ткани. Только для демонстрационных целей платье имело тенденцию рваться в сложенном виде и весило 13,5 фунтов.
Помимо одежды, стеклянные волокна предлагали множество применений, хотя в то время они не были полностью гибкими.Также не существовало способа массового производства этих стеклянных волокон.
К счастью, в 1930-х годах компания Owens-Illinois Glass Company из Иллинойса открыла процесс производства воздушных фильтров из стекловолокна для вентиляционного оборудования. Эти воздушные фильтры были более эффективными, чем хлопковый материал, используемый для той же цели.
Кроме того, эти воздушные фильтры из стекловолокна были недорогими, и их можно было выбросить, когда они забились. Компания Owens-Illinois была стабильным продавцом этих воздушных фильтров на протяжении десятилетий благодаря широкому использованию кондиционеров.
Стекловолокно ведет себя как обычное стекло:
- Не впитывает влагу
- Не образует плесень и грибок
- Непроводящий
- Не ржавеет, не сжимается, не расширяется и не горит
Спустя несколько десятилетий и множество открытий продукты из армированного волокном полимера (FRP) используются для изготовления таких предметов, как лопасти роторов для ветряных мельниц и вертолетов, компоненты для коммерческих и военных самолетов, детали для автомобилей и даже грузовиков.
FRP используются в спортивном и рекреационном оборудовании, таком как доски для серфинга, зимние лыжи, велосипеды и спортивное снаряжение, такое как спортивная обувь.Гибкость FRP, произведенных в процессе производства, известном как пултрузия, означает, что можно создавать профили с плавными формами. Это означает, что если желаемый продукт можно смоделировать, его можно построить.
Цены на традиционные материалы, такие как сталь и дерево, имеют тенденцию к росту, в то время как стоимость материалов из стеклопластика снижается. Кроме того, производственные процессы с годами совершенствуются, становясь более эффективными. Для промышленности продукты FRP с каждым годом становятся все более экономичными.
Раньше многие изделия из FRP нужно было красить, поскольку они были полупрозрачными. В настоящее время производители могут наносить слой геля перед укладкой стеклянных матов и смолы. Инновационный метод производства, известный как пултрузия, протягивает пряди стекловолокна через чаны со смолой в нагретую форму.
В этом процессе производства жестких или гибких профилей могут быть изготовлены и сформированы индивидуальные. К ним относятся стержни, армирование окон, столбы для деревьев и указатели проезжей части или любой профиль с постоянным поперечным сечением, такой как двутавровая балка.
Типы стекловолокна:
Стекловолокно можно разделить на различные формы, каждая из которых используется для различных целей:
- А-стекло: также известное как щелочное стекло. А-стекловолокно устойчиво к химическим веществам и имеет некоторое сходство с оконным стеклом. За пределами США он используется для изготовления технологического оборудования.
- C-стекло: также известное как химическое стекло. С-стекло обладает высокой устойчивостью к химическому воздействию.
- E-стекло: также называется электрическим стеклом.Е-стекло является отличным изолятором электричества.
- AE-стекло: щелочестойкое стекло.
- S-стекло: также известное как структурное стекло.
S-стекло используется из-за его механических свойств.
Атрибуты стекловолокна
Высокая прочность на растяжение: в проектах, несущих тепловую нагрузку, арматура из стекловолокна так же прочна, как сталь, когда дело доходит до точки изгиба. Они сохраняют свою целостность и не подвергаются коррозии при использовании в суровых условиях.
В исследовании арматуры из стеклопластика, используемой в строительстве для уменьшения тепловых мостов, несущая арматура из стекловолокна имела более высокую прочность на растяжение в продольном направлении и более низкий модуль упругости и плотность по сравнению со сталью (550 МПа и 200 ГПа для стали по сравнению с 1000 МПа). и 50 ГПа для арматуры из стекловолокна).
- Электрическая изоляция: Стекловолокно обладает отличными электроизоляционными свойствами.
- Негорючий: негорючий. Он не распространяет и не поддерживает пламя. При воздействии тепла не дымит и не выделяет токсичных химических веществ.
- Стабильность размеров: стекловолокно не деформируется, не изгибается и не деформируется, так как имеет низкий коэффициент линейного расширения.
- Не гниет: стеклопластик сохраняет свою целостность и не подвергается воздействию грызунов и насекомых.
- Теплопроводность: Стеклопластик популярен в строительстве, так как имеет низкую теплопроводность.
Применение стекловолокна в промышленности
Стеклопластик прочный, безопасный и обеспечивает высокую теплоизоляцию. Он не только обеспечивает лучшую изоляцию, но и широко используется в следующих отраслях промышленности:
.- Производство: Решетка из стекловолокна имеет встроенную поверхность из песка для предотвращения скольжения во влажных зонах или в местах, где присутствуют гидравлические жидкости или масла.
- Металлургия и горнодобывающая промышленность: стекловолокно используется для изготовления решеток, особенно в местах, подверженных химической коррозии.
- Производство электроэнергии.
Во многих областях производства электроэнергии, таких как резервуарные парки, скрубберы и т. д., используется стекловолокно, поскольку оно обладает непроводящими свойствами.
- Автомобильная промышленность: Стекловолокно широко используется в автомобильной промышленности для изготовления комплектов и компонентов автомобилей, кузовов.
- Аэрокосмическая промышленность и оборона: стекловолокно используется для производства деталей как для военной, так и для гражданской аэрокосмической промышленности, включая испытательное оборудование, воздуховоды, кожухи и другие.
- Доки и причалы: стекловолокно не подвергается коррозии, ржавчине и повреждениям в соленой водной среде.
- Фонтаны и аквариумы: стекловолокно используется для поддержки камней, чтобы способствовать циркуляции и фильтрации из-под камней. Там, где есть большие общественные фонтаны, решетки из стекловолокна используются для защиты распылительных коллекторов и фонарей от повреждений. Это также помогает предотвратить утопление людей в фонтанах.
- Целлюлозно-бумажная промышленность: стекловолокно обладает свойствами устойчивости к химической коррозии и используется во многих областях благодаря своей коррозионной стойкости и противоскользящим свойствам.
Поговорите с нами
Tencom сотрудничает с дизайнерами, строителями и производителями, чтобы реализовать широкий спектр дизайнерских возможностей. Наша команда опытных инженеров-специалистов стремится помочь вам настроить и внедрить ваш дизайн в производственный процесс. Свяжитесь с нами сегодня.
Стекловолокно – типы, свойства и применение
Стекловолокно – это форма армированного волокном пластика, где стекловолокно является армированным пластиком. Возможно, по этой причине стекловолокно также известно как пластик, армированный стекловолокном, или пластик, армированный стекловолокном.Стекловолокно обычно сплющено в лист, произвольно расположено или вплетено в ткань. В зависимости от использования стекловолокна стекловолокно может быть изготовлено из различных видов стекла.
Стекловолокно легкое, прочное и менее хрупкое. Лучшая часть стекловолокна — это его способность принимать различные сложные формы. Это в значительной степени объясняет, почему стекловолокно широко используется в ваннах, лодках, самолетах, кровлях и других областях.
В этой статье мы более подробно поговорим о видах стеклопластика, их свойствах и применении.Давайте начнем.
Типы и формы стекловолокна:В зависимости от используемого сырья и их пропорций для изготовления стекловолокна стекловолокно можно разделить на следующие основные типы:
- А-стекло : стекло стекло и устойчиво к химическим веществам. По составу стекловолокна А оно близко к оконному стеклу. В некоторых частях мира он используется для изготовления технологического оборудования.
- С-стекло : С-стекло обладает очень хорошей устойчивостью к химическому воздействию и также называется химическим стеклом.
- Е-стекло : Его также называют электрическим стеклом, оно является очень хорошим изолятором электричества.
- AE-стекло : щелочестойкое стекло.
- Стекло S : Оно также называется структурным стеклом и известно своими механическими свойствами.
Стекловолокно выпускается в различных формах для различных применений, основными из которых являются:
- Лента из стекловолокна : Ленты из стекловолокна состоят из нитей из стекловолокна и известны своими теплоизоляционными свойствами.Эта форма стекловолокна находит широкое применение в обертывании сосудов, горячих трубопроводов и т.п.
- Ткань из стекловолокна : Ткань из стекловолокна гладкая и доступна в различных вариантах, таких как нити из стекловолокна и нити из стекловолокна. Широко используется в качестве тепловых экранов, в противопожарных завесах и др.
- Веревка из стекловолокна : Веревки сплетены из пряжи из стекловолокна и используются для упаковки.
- Механическая прочность : Удельное сопротивление стекловолокна выше, чем у стали.
Таким образом, он используется для изготовления высокопроизводительных
- Электрические характеристики : Стекловолокно является хорошим электрическим изолятором даже при небольшой толщине.
- Негорючесть : Поскольку стекловолокно является минеральным материалом, оно негорюче. Он не распространяет и не поддерживает пламя. Он не выделяет дыма или токсичных продуктов при воздействии тепла.
- Размерная стабильность : Стекловолокно не чувствительно к колебаниям температуры и влажности.Имеет низкий коэффициент линейного расширения.
- Совместимость с органическими матрицами : Стекловолокно может иметь различные размеры и может сочетаться со многими синтетическими смолами и некоторыми минеральными матрицами, такими как цемент.
- Негниющий : Стекловолокно не гниет и не подвержено воздействию грызунов и насекомых.
- Теплопроводность : Стекловолокно имеет низкую теплопроводность, что делает его очень полезным в строительстве.
- Диэлектрическая проницаемость : Это свойство стекловолокна делает его подходящим для электромагнитных окон.
Материалы с высокотемпературной изоляцией обеспечивают эффективный тепловой барьер для промышленных прокладок. Поскольку стекловолокно является прочным, безопасным и обеспечивает высокую теплоизоляцию, стекловолокно является одним из наиболее предпочтительных материалов для промышленных прокладок. Они не только обеспечивают лучшую изоляцию, но также помогают защитить оборудование, сохранить энергию и обеспечить безопасность профессиональной рабочей силы.Возможно, по этой причине стекловолокно широко используется в следующих отраслях промышленности:
- Производство напитков : Решетки из стекловолокна используются во многих областях, например, на линиях розлива и в варочных цехах.
- Автомойки : В последнее время решетки из стекловолокна широко используются для защиты от ржавчины и для придания контрастного цвета областям, которые ранее выглядели запрещенными.
Он осветляет внутреннюю часть туннеля автомойки, заставляя машину выглядеть чище, чем она была.
- Химическая промышленность : В этой отрасли решетка из стекловолокна используется для защиты от скольжения встроенной поверхности песка и химической стойкости различных смоляных соединений.Используемые химикаты сочетаются со смолами.
- Градирни : Поскольку градирни всегда влажные, их необходимо защищать от ржавчины, коррозии и других проблем с безопасностью. Благодаря превосходным свойствам стеклопластика, он используется в этих башнях в качестве экранирования для защиты людей и животных от опасных зон.
- Доки и причалы : Доки подвергаются коррозии, ржавчине и повреждению соленой морской водой. Так, стекловолокно здесь используется для защиты.
- Пищевая промышленность : На предприятиях по переработке курятины и говядины решетки из стекловолокна используются для защиты от скольжения и для удержания разъедающей крови.
В большинстве областей пищевой промышленности также используется стекловолокно, поскольку другие материалы для решетки не подходят.
- Фонтаны и аквариумы : Фонтаны и аквариумы всех размеров используют стекловолокно для поддержки камней, чтобы способствовать циркуляции и фильтрации из-под камней. В больших общественных фонтанах решетки из стекловолокна используются для защиты форсунок и фонарей от повреждений.Это также удерживает людей от утопления в фонтанах.
- Производство : Встроенная зернистая поверхность решетки из стекловолокна обеспечивает сопротивление скольжению во влажных местах или в местах, где присутствуют гидравлические жидкости или масла.
- Металлургия и горнодобывающая промышленность : Решетка из стекловолокна используется в областях переработки электроники, подверженных химической коррозии. Здесь нельзя использовать другие решетчатые материалы.
- Производство электроэнергии : Многие области производства электроэнергии, такие как резервуарные парки, скрубберы и другие, используют стекловолокно.
Причиной этого является непроводящее свойство стекловолокна.
- Гальванические установки : В этом приложении используется решетка из стекловолокна из-за противоскользящих свойств поверхности.
- Целлюлозно-бумажная промышленность : Свойство стекловолокна, которое делает его устойчивым к химической коррозии, используется на целлюлозно-бумажных предприятиях. В последнее время стеклопластик используется во многих сферах благодаря своей коррозионной стойкости и противоскользящим свойствам.
- Автомобильная промышленность : Стекловолокно широко используется в автомобильной промышленности.Почти каждый автомобиль имеет компоненты и обвесы из стекловолокна.
- Аэрокосмическая промышленность и оборона : Стекловолокно используется для производства деталей как для военной, так и для гражданской аэрокосмической промышленности, включая испытательное оборудование, воздуховоды, кожухи и другое.
Узнайте больше о портфолио стекловолокна Phelps
Стекловолокно является важным компонентом целого ряда отраслей промышленности, в том числе установок по очистке сточных вод, систем отопления, вентиляции и кондиционирования, противопожарной защиты и нефтяных месторождений. Чтобы узнать больше о стекловолокне и его применении, позвоните в Phelps по телефону 1-800-876-SEAL сегодня для получения более подробной информации и ознакомьтесь с ассортиментом стекловолокна Phelps.
Наука и технология композиционных материалов
Послушать эту тему
В таком развитом обществе, как наше, мы все зависим от композитных материалов в некоторых аспектах нашей жизни. Стекловолокно был разработан в конце 1940-х годов и стал первым современным композитом. Он по-прежнему остается самым распространенным, составляя около 65 процентов всех производимых сегодня композитов. Он используется для изготовления корпусов лодок, досок для серфинга, спортивных товаров, облицовки бассейнов, строительных панелей и кузовов автомобилей.Вы вполне можете использовать что-то из стекловолокна, не подозревая об этом.
Лодки, доски для серфинга, автомобили и многое другое: стекловолокно и другие композитные материалы окружают нас. Источник изображения: sobri/Flickr.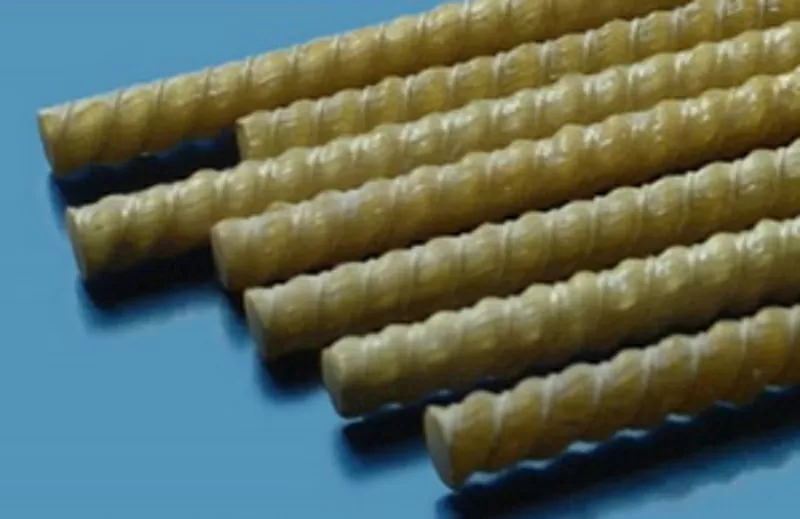
Что делает материал композитным
Композитные материалы образуются путем объединения двух или более материалов, обладающих совершенно разными свойствами. Различные материалы работают вместе, чтобы придать композиту уникальные свойства, но внутри композита вы можете легко отличить разные материалы — они не растворяются и не смешиваются друг с другом.
Композиты существуют в природе. Кусок дерева представляет собой композит, состоящий из длинных волокон целлюлозы (очень сложной формы крахмала), скрепленных гораздо более слабым веществом, называемым лигнином. Целлюлоза также содержится в хлопке и льне, но именно связывающая способность лигнина делает кусок древесины намного прочнее пучка хлопковых волокон.
Это не новая идея
Человечество использует композитные материалы тысячи лет. Возьмем, к примеру, глиняные кирпичи.Если вы попытаетесь согнуть лепешку из засохшей грязи, она легко сломается, но будет прочной, если вы попытаетесь раздавить или сжать ее. С другой стороны, кусок соломы обладает большой силой, когда вы пытаетесь его растянуть, но почти не имеет силы, когда вы его смываете. Когда вы смешиваете глину и солому в блоке, свойства двух материалов также объединяются, и вы получаете кирпич, который устойчив как к сжатию, так и к разрыву или изгибу. Говоря более технически, у него есть как хорошие
прочность на сжатие и хорошо
предел прочности .
Еще одним известным композитом является бетон. Здесь заполнитель (мелкие камни или гравий) связан цементом. Бетон обладает хорошей прочностью при сжатии, и его можно сделать более прочным при растяжении, добавив в композит металлические стержни, проволоку, сетку или тросы (таким образом создавая железобетон).
Композиты были изготовлены из формы углерода, называемой графеном, в сочетании с металлической медью, в результате чего получается материал, в 500 раз прочнее, чем медь сама по себе. Точно так же композит графена и никеля имеет прочность, превышающую прочность никеля более чем в 180 раз.
Что касается стекловолокна, то оно изготовлено из пластик армированный нитями или стеклянными волокнами. Эти нити можно либо связать вместе и сплести в мат, либо иногда нарезать на короткие отрезки, которые произвольно ориентированы в пластиковой матрице.
Больше, чем сила
В настоящее время многие композиты производятся не только для повышения прочности или других механических свойств, но и для других целей. Многие композиты предназначены для того, чтобы быть хорошими проводниками или изоляторами тепла или обладать определенными магнитными свойствами; свойства, которые являются очень специфическими и специализированными, но также очень важными и полезными. Эти композиты используются в огромном количестве электрических устройств, включая транзисторы, солнечные элементы, датчики, детекторы, диоды и лазеры, а также для изготовления антикоррозионных и антистатических покрытий поверхностей.
Композиты, изготовленные из оксидов металлов, также могут обладать особыми электрическими свойствами и используются для производства кремниевых чипов, которые могут быть меньше по размеру и более плотно упакованы в компьютер. Это увеличивает объем памяти и скорость компьютера. Оксидные композиты также используются для создания высокотемпературных сверхпроводящих свойств, которые теперь используются в электрических кабелях.
Изготовление композита
Большинство композитов состоят всего из двух материалов.Один материал (матрица или связующее) окружает и связывает вместе группу волокон или фрагментов гораздо более прочного материала (армирования). В случае сырцовых кирпичей две роли выполняют глина и солома; в бетоне цементом и заполнителем; в куске дерева, целлюлозой и лигнином. В стекловолокне армирование обеспечивается тонкими нитями или волокнами стекла, часто вплетенными в своего рода ткань, а матрица представляет собой пластик.
Примеры различных форм армирования стекла, используемых при создании стеклопластика.
Стеклянные нити в стекловолокне очень прочны при растяжении, но они также хрупкие и ломаются при резком изгибе. Матрица не только удерживает волокна вместе, но и защищает их от повреждений, разделяя любые стресс из их. Матрица достаточно мягкая, чтобы ее можно было формировать с помощью инструментов, и ее можно смягчить подходящими растворителями, чтобы можно было произвести ремонт. Любая деформация листа стеклопластика обязательно растягивает часть стеклянных волокон, а они способны этому противостоять, поэтому даже тонкий лист очень прочен.Он также довольно легкий, что является преимуществом во многих приложениях.
За последние десятилетия было разработано много новых композитов, некоторые из которых обладают очень ценными свойствами. Тщательно выбирая армирование, матрицу и производственный процесс, который объединяет их, инженеры могут адаптировать свойства в соответствии с конкретными требованиями. Они могут, например, сделать композитный лист очень прочным в одном направлении, выровняв таким образом волокна, но более слабым в другом направлении, где прочность не так важна. Они также могут выбрать такие свойства, как устойчивость к теплу, химическим веществам и атмосферным воздействиям, выбрав соответствующий матричный материал.
Выбор материалов для матрицы
В качестве матрицы во многих современных композитах используются термореактивные или термопластичные пластмассы (также называемые смолами). (Использование пластика в матрице объясняет название «армированный пластик», обычно данное композитам). Пластмассы полимеры которые скрепляют арматуру и помогают определить физические свойства конечного продукта.
Термореактивные пластмассы жидкие при приготовлении, но затвердевают и становятся жесткими (т.е. отверждаются) при нагревании. Процесс схватывания необратим, поэтому эти материалы не становятся мягкими при высоких температурах. Эти пластмассы также устойчивы к износу и воздействию химических веществ, что делает их очень прочными даже в экстремальных условиях.
Термопластические пластмассы, как следует из названия, являются твердыми при низких температурах, но размягчаются при нагревании. Хотя они используются реже, чем термореактивные пластмассы, у них есть некоторые преимущества, такие как более высокая вязкость разрушения, длительный срок хранения сырья, способность к переработке и более чистое и безопасное рабочее место, поскольку для процесса отверждения не требуются органические растворители.
Керамика, углерод и металлы используются в качестве матрицы для некоторых узкоспециализированных целей. Например, керамика используется, когда материал будет подвергаться воздействию высоких температур (например, теплообменники), а углерод используется для продуктов, подверженных трению и износу (например, подшипники и шестерни).
Электронно-микроскопическое изображение в искусственном цвете композита с магниевой матрицей, армированного карбидом титана-алюминия. Источник изображения: микроскопия ZEISS / Flickr.Выбор материалов для армирования
Хотя стекловолокно является наиболее распространенным армирующим материалом, во многих передовых композитах теперь используются тонкие волокна из чистого углерода. Можно использовать два основных типа углерода — графит и углеродные нанотрубки. Оба они представляют собой чистый углерод, но атомы углерода расположены в разных кристаллических конфигурациях. Графит — очень мягкое вещество (используется в «графитовых» карандашах) и состоит из листов атомов углерода, расположенных в виде шестиугольников. Связи, скрепляющие шестиугольники вместе, очень прочные, но связи, скрепляющие листы шестиугольников, довольно слабые, что и делает графит мягким. Углеродные нанотрубки изготавливаются путем скручивания одного листа графита (известного как графен) в трубку.Получается чрезвычайно прочная конструкция. Также возможно иметь трубки, состоящие из нескольких цилиндров — трубки внутри трубок.
Композиты из углеродного волокна легче и намного прочнее стекловолокна, но и дороже. Из этих двух графитовые волокна дешевле и проще в производстве, чем углеродные нанотрубки. Они используются в конструкциях самолетов и высокоэффективном спортивном оборудовании, таком как клюшки для гольфа, теннисные ракетки и гребные лодки, и все чаще используются вместо металлов для ремонта или замены поврежденных костей.
Нити из бора еще прочнее (и дороже), чем углеродные волокна. Нанотрубки из нитрида бора имеют дополнительное преимущество, заключающееся в том, что они намного более устойчивы к теплу, чем углеродные волокна. Они также обладают пьезоэлектрическими свойствами, что означает, что они могут генерировать электричество при воздействии на них физического давления, такого как скручивание или растяжение.
Полимеры также могут использоваться в качестве армирующего материала в композитах. Например, кевлар, изначально разработанный для замены стали в радиальных шинах, но наиболее известный своим использованием в пуленепробиваемых жилетах и шлемах, представляет собой полимерное волокно, обладающее чрезвычайной прочностью и повышающее ударную вязкость композита.Применяется в качестве армирования в композитных изделиях, требующих легкой и надежной конструкции (например, конструкционные детали корпуса самолета). Еще более прочным, чем кевлар, является вещество, изготовленное из комбинации графена и углеродных нанотрубок.
Выбор производственного процесса
Для изготовления объекта из композитного материала обычно используется какая-либо форма. Армирующий материал сначала помещается в форму, а затем напыляется или закачивается полужидкий матричный материал для формирования объекта.Можно приложить давление, чтобы вытеснить любые пузырьки воздуха, а затем форму нагреть, чтобы матрица затвердела.
Процесс формования часто выполняется вручную, но автоматическая обработка на машинах становится все более распространенной. Один из этих методов называется пултрузия (термин, образованный от слов «тянуть» и «экструзия»). Этот процесс идеально подходит для изготовления прямых изделий с постоянным поперечным сечением, таких как мостовые балки.
Во многих тонких конструкциях сложной формы, таких как изогнутые панели, композитная структура строится путем наложения листов тканого волокнистого армирования, пропитанного пластиковым матричным материалом, на базовую форму соответствующей формы. Когда панель изготовлена до необходимой толщины, матричный материал отверждается.
Многослойные композиты
Многие новые типы композитов производятся не методом матрицы и армирования, а путем укладки нескольких слоев материала. Структура многих композитов (например, используемых в панелях крыльев и корпусов самолетов) состоит из сот из пластика, зажатых между двумя обшивками из композитного материала, армированного углеродным волокном.
Сэндвич-структура из сотового композита от НАСА.Источник изображения: НАСА/Викисклад.Эти сэндвич-композиты сочетают в себе высокую прочность и особенно жесткость на изгиб с малым весом. Другие методы включают простое наложение нескольких чередующихся слоев различных веществ (например, графена и металла) для получения композита.
Зачем использовать композиты?
Самым большим преимуществом композитных материалов является прочность и жесткость в сочетании с легкостью.Выбирая подходящую комбинацию армирующего и матричного материала, производители могут добиться свойств, точно соответствующих требованиям к конкретной конструкции для конкретной цели.
- Композиты в Австралии
Австралия, как и все развитые страны, проявляет большой интерес к композитным материалам, которые многие считают «материалами будущего». Основная задача состоит в том, чтобы снизить затраты, чтобы композиты можно было использовать в продуктах и приложениях, которые в настоящее время не оправдывают затрат.В то же время исследователи хотят улучшить характеристики композитов, например, сделать их более устойчивыми к ударам.
Один из новых методов включает «текстильные композиты». Вместо того, чтобы укладывать армирующие волокна по отдельности, что медленно и дорого, их можно связать или сплести вместе, чтобы сделать своего рода ткань. Это может быть даже трехмерным, а не плоским. Пространства между текстильными волокнами и вокруг них затем заполняются матричным материалом (например, смолой) для изготовления изделия.
Этот процесс может быть легко выполнен с помощью машин, а не вручную, что делает его более быстрым и дешевым. Соединение всех волокон вместе также означает, что композит с меньшей вероятностью будет поврежден при ударе.
По мере снижения затрат другие варианты использования композитов начинают казаться привлекательными. При изготовлении корпусов и надстроек лодок из композитов используется их устойчивость к коррозии. У минных охотников ВМС Австралии композитный корпус, поскольку магнитный эффект стального корпуса будет мешать обнаружению мин.
Также в разработке находятся вагоны для поездов, трамваев и других транспортных средств, изготовленных из композитных материалов, а не из стали или алюминия. Здесь привлекательность заключается в легкости композитов, поскольку в этом случае транспортные средства потребляют меньше энергии. По той же причине мы будем видеть все больше и больше композитов в автомобилях в будущем.
Ярким примером является современная авиация, как военная, так и гражданская. Без композитов было бы гораздо менее эффективно. Фактически, потребность этой отрасли в легких и прочных материалах была главной движущей силой разработки композитов.В настоящее время часто можно встретить секции крыла и хвостового оперения, пропеллеры и лопасти несущего винта, изготовленные из передовых композитов, а также большую часть внутренней конструкции и фурнитуры. Планеры некоторых небольших самолетов полностью сделаны из композитных материалов, как и крылья, хвостовое оперение и панели корпуса больших коммерческих самолетов.
Размышляя о самолетах, стоит помнить, что композиты менее склонны к полному разрушению под нагрузкой, чем металлы (например, алюминий). Небольшая трещина в куске металла может очень быстро распространиться с очень серьезными последствиями (особенно в случае с самолетом).Волокна в композите блокируют расширение любой небольшой трещины и распределяют напряжение вокруг.
Подходящие композиты также хорошо противостоят нагреву и коррозии. Это делает их идеальными для использования в продуктах, которые подвергаются воздействию экстремальных условий, таких как лодки, оборудование для обработки химикатов и космические корабли. В целом композитные материалы очень прочны.
Еще одно преимущество композитных материалов заключается в том, что они обеспечивают гибкость конструкции. Композитным материалам можно придавать сложные формы, что очень удобно при производстве чего-то вроде доски для серфинга или корпуса лодки.
Кроме того, большая работа в настоящее время направлена на разработку композитных материалов, изготовленных из отходов, таких как сельскохозяйственные отходы, строительные материалы или пластиковые контейнеры для напитков.
Обратной стороной композитов обычно является их стоимость. Хотя производственные процессы часто более эффективны при использовании композитов, сырье стоит дорого. Композиты никогда полностью не заменят такие традиционные материалы, как сталь, но во многих случаях это именно то, что нам нужно.И, несомненно, по мере развития технологии будут найдены новые применения. Мы еще не видели всего, на что способны композиты.
Современная авиация стала основной движущей силой развития композитов. Источник изображения: Пол Нелхамс / Flickr.FRP по сравнению со стекловолокном
Некоторые специалисты отрасли используют термины «стекловолокно» и «армированный волокном полимер (FRP)» как синонимы. Однако технически существует разница, поскольку они могут относиться к разным продуктам. Ниже мы расскажем, что такое стекловолокно и FRP и чем они отличаются.
Что такое стекловолокно?
Стекловолокно — это материал, получаемый путем плавления вращающегося стекла. В процессе производятся стекловолокна, которые можно использовать сами по себе или в сочетании с другими материалами для различных целей. В последнем случае стекловолокно используется в качестве армирующего материала. Стекловолокно обеспечивает доминирующие механические свойства для превращения основного материала, который может быть жидким полимером, металлом или керамикой, в более прочный композитный материал.
Композиты, армированные стекловолокном, иногда называют просто «стекловолокном», поскольку стекловолокно присутствует во всех из них независимо от основного материала. В композитных материалах стекловолокна доступны во многих формах, которые облегчают производство, включая пряжу, ровницы, маты и ткани текстильного типа.
Что такое FRP?
Полимер, армированный волокном (FRP), представляет собой материал, полученный путем объединения полимерного базового материала с материалом, армированным волокном. Волокна обеспечивают структуру и стабильность полимерной матрицы. Полимерная матрица поддерживает волокна, обеспечивая правильную работу. Он также защищает волокно от условий окружающей среды, таких как соль, влага и УФ-излучение.
Термин «полимер» относится к химическим соединениям, состоящим из длинных цепочек молекул. Для конструкционных композитов это синтетический материал (например, полиэстер, виниловый эфир, эпоксидная смола). Общие слова, иногда используемые для полимера, — смола и пластик. Волокнистой арматурой может быть ряд материалов (например,например, стекловолокно, углеродное волокно или графитовое волокно). Конкретные выбранные полимерные и волокнистые материалы влияют на свойства, проявляемые конечным композитным материалом, а это означает, что производители могут адаптировать материал FRP для удовлетворения конкретных требований применения при минимальных затратах и весе. Например, в самолетах, высококачественном оборудовании для отдыха и в индустрии автогонок часто используется углерод или графит в качестве армирующего материала из-за высокой жесткости материалов. Стекловолокно является предпочтительной арматурой для большинства изделий из стеклопластика, поскольку оно имеет наилучшее сочетание свойств и стоимости.Некоторые компании и страны ссылаются на полимеры, армированные стекловолокном (GFRP), чтобы обеспечить различие с углеродным армированием (CFRP).
В чем разница между стекловолокном и FRP?
Принимая во внимание приведенные выше определения, мы можем сделать вывод, что стекловолокно и FRP взаимозаменяемы в большинстве, но не во всех случаях. При обсуждении композитного материала стекловолокно означает полимер, армированный стекловолокном (FRP или GFRP). Композит из стекловолокна, в котором полимер не используется в качестве основного материала, нельзя назвать композитом FRP.Точно так же композит FRP, в котором не используются стекловолокна в качестве армирующего материала или полимер в качестве основного материала, нельзя назвать композитом GFRP.
Узнайте больше о FRP от экспертов Creative Composites Group
Хотите получить дополнительную информацию о полимерных композитах, армированных стекловолокном? Creative Composites Group готова помочь! Мы предлагаем решения FRP для широкого спектра отраслей и приложений.
Комментариев нет