Шлакоблоки технология производства: видео, чертежи станков, форм и вибропресса
Производство шлакоблоков
Производство шлакоблоков бизнес. Технология и оборудование для производства шлакоблоков.
Шлакоблок – простой в производстве и доступный по цене строительный материал, обладает хорошими тепло и звукоизоляционными свойствами. Организовать производство шлакоблоков можно с небольшим стартовым капиталом.
Существует несколько разновидностей шлакоблоков, которые отличаются размером и наличием пустотелых отверстий.
Оборудование для производства шлакоблоков.
Для организации производства шлакоблоков понадобится оборудование:
Бетономешалка принудительного типа для приготовления полусухих смесей.
Станок для производства шлакоблоков. Станок представляет собой пресс с формой матрицей для блоков.
Существует несколько разновидностей станков для производства шлакоблоков. Самый простой это ручной станок (несушка), станок вручную передвигается и оставляет готовые блоки на площадке.
Более производительные полуавтоматические станки, здесь усилие пресса уже в несколько раз больше ручного станка и шлакоблоки получаются более прочными.
Это минимальный комплект оборудования для небольшого мини производства шлакоблоков, если требуется высокая производительность, понадобится установить автоматическую линию.
Автоматические линии для производства шлакоблоков, состоят из автоматического станка, ленты транспортёра для подачи бетонного раствора и бетономешалки принудительного типа.
Автоматические линии позволяют организовать производство с высокой производительностью.
Технология производства шлакоблоков.
Процесс производства шлакоблоков состоит из нескольких этапов.
Приготовление полусухой бетонной смеси.
Для изготовления шлакоблоков используется полусухая смесь, существует несколько разновидностей смеси в зависимости от используемого сырья.
Состав раствора для изготовления шлакоблоков согласно ГОСТ 6665-91 «Камни стеновые бетонные»
- 5 частей отсева щебня.
- 1 часть цемента М400 класс Д20.
- 3 части просеянного песка.
- Вода 0,5% от количества цемента.
Таблица: расход материалов на изготовление одного шлакоблока размером 188 x 190 x 390 мм, количество блоков в 1 м3 — 72 шт, марка прочности — м75, объём каждого блока — 0,0139 м
В качестве наполнителя вместо отсева щебня могут использоваться отходы горения доменных печей, шлак, перлит или керамзит. Обычно для производства используется наполнитель, который наиболее распространён в регионе, если это гранитный карьер, то есть смысл делать шлакоблоки из гранитного отсева.
Следующий этап формовка
В форму матрицу станка засыпается бетонный раствор, включается режим вибрации, в процессе чего бетонная смесь уплотняется в форме, остатки воздуха выходят на поверхность раствора.
Затем в форму с раствором опускается пуансон, под воздействием пресса формируется шлакоблок и сразу извлекается из формы, при этом блок должен не крошиться сохранять форму.
Заключительный этап – набор прочности.
Блоки сразу укладываются на ровную площадку на 2 – 3 суток для набора первоначальной прочности необходимой для транспортировки. Когда шлакоблоки набирают первоначальную прочность, их укладывают на паллеты и оставляют на 3 – 4 недели при температуре 20 °C и высокой влажности для окончательного набора прочности, после чего блоки можно использовать для строительства.
Процесс производства шлакоблоков на автоматическом станке показан в этом видео.
Бизнес на производстве шлакобетонных блоков.
При наличии доступного наполнителя (отсев щебня, керамзит, шлак или известняк) себестоимость производства шлакобетонных блоков будет довольно низкой, это позволит войти на рынок стройматериалов и занять нишу.
Оборудование для шлакоблока. Производство шлакоблока на вибропрессах
На смену традиционным кирпичам сейчас приходят другие строительные материалы, и в первую очередь шлакоблок.
Производство шлакоблока — мифы
- Это ненадежный материал, который быстро разрушится. Ведь в его состав входят различные отходы, и они не могут гарантировать качество и прочность изделий.
– Известно, что действующему гаражу в Эрмитаже уже сто лет (постройка 1911 года). Это одно из наиболее старых шлакоблочных (!) сооружений. - Изготовление шлакоблока и его последующая эксплуатация – небезопасный процесс, так как используется вредное сырье.
– В состав блоков входят хорошо известные безопасные материалы — бетон, отходы кирпича, бетона и гранита, отсев щебня, зола, керамзит и песок.Это сырье уже давно применяется в строительной отрасли и отлично зарекомендовало себя. Поэтому шлакоблок — абсолютно безвредный материал, не оказывающий негативного влияния на здоровье человека. Никакие радиоактивные отходы в производстве шлакоблока никогда не использовались и их применение не планируется.
- Дешевый строительный материал не может быть хорошим.
– Низкая цена на шлакоблок объясняется использование дешевых доступных материалов. При этом качество зависит от оборудования шлакоблока и соблюдения технологического процесса, но не от стоимости исходного сырья. - Оборудование для шлакоблока покупать не обязательно. Производство материала простое, зачем лишние траты?
Но именно благодаря такому «самопалу» и возникают мифы о недолговечности шлакоблока. Отсутствие вибропресса не дает смеси равномерно распределиться по форме. Смешение ингредиентов на глаз снижает морозостойкость и увеличивает теплопроводность. Дома, построенные из самодельных шлакоблоков, зимой сыреют, летом в них жарко. Кустарным шлакоблокам требуются минимальные три месяца для просушки, в отличие от четырехнедельного срока заводских изделий (даже если это мини-завод).
- Дома из шлакоблоков холодные.
– Действительно, нельзя сказать, что это сильно теплоаккумулирующий стройматериал. Так, полнотелые камни вообще предназначены для фундаментов, цоколей и нежилых помещений. Однако пустотелые камни сохраняют тепло в помещении гораздо лучше, а использование опилок в качестве заполнителя значительно повышает теплоизоляционные свойства шлакоблоков. - Шлакоблок пригоден только в малоэтажном строительстве.
– В одно- и двухэтажных домах шлакоблок идеален в качестве стройматериала.
Основными достоинствами шлакоблока являются дешевизна производственного процесса и при этом высокое качество изделий. Вибропресс для производства блоков создает из бетона и вспомогательных материалов прочные, морозостойкие, тепло- и звукоизоляционные изделия. Большой размер блоков позволяет ускорить темпы строительства и в то же время облегчить процесс, так как вес камней гораздо меньше, чем, например, у тех же кирпичей. Еще один фактор в пользу шлакоблоков — их устойчивость к огню, высоким и низким температурам. Материал не трескается и не крошится ни в холода, ни в жару.
Избавиться от повышенной гигроскопичности поможет применение облицовочного кирпича. Большинство крупных компаний, занимающихся изготовлением оборудования шлакоблоков, выбрало оборудование «Рифей». Производители отмечают его высокую скорость работы, автоматизацию процесса и отличное качество готовых изделий. Вибропрессы линии «Рифей» позволяют организовать эффективное производство качественных и надежных строительных материалов.
Производимый шлакоблок:
Какой состав смеси для шлакоблока?
Шлакоблок является строительным материалом, его изготавливают промышленным способом или вручную. При промышленном производстве применяют прессование путем вибрации в специальных формах. Такой материал пользуется спросом так как его стоимость не является высокой, это помогает сэкономить на строительстве. Для самостоятельного изготовления используют различное сырье, в данной статье описывается, какие материалы необходимо использовать.
Из чего состоит шлакоблок?
Шлакоблок называют стеновым камнем, для его производства необходимо правильно приготовить смесь. Шлакоблок, состав смеси которого достаточно прост, изготавливается не только промышленным образом, но и в домашних условиях.
В раствор стандартного вида входят такие компоненты, как шлак, зола или отходы с металлургических печей. Такие материалы применять необязательно, можно использовать различные наполнители, известняк, керамзит, опилки, щебенку, перлит или гравий. При соблюдении правильных пропорций, и добавлении нестандартных материалов, то можно повысить прочность, и сэкономить на расходах, к таким компонентам может относиться битый кирпич или другие подобные виды отходов. Шлакоблок усиленного типа должен соответствовать ГОСТу.
Обязательно необходимо соблюдение основных пунктов
- Должен соблюдаться цвет по образцу.
- По ГОСТу должна в точности соблюдаться форма блока.
- Наличие пустот или полнотелость.
- Толщина пустотелой перегородки и стенок должна быть не менее 20 миллиметров.
Состав смеси также должен соответствовать условиям ГОСТа
- Для изготовления используют цемент 400 марки класса Д 20.
- Кварцевый песок должен быть очищенным, и просеянным.
- Отсевом называют сырье, которое получают путем дробления горной породы или щебенки.
- Воду можно использовать любую, питьевую или техническую.
В состав смеси для производства шлакоблока входит песок, цемент, шлак, в пропорциях 3 к 1 к 5. Воды добавляют в количестве половины объема цемента. Если блоки изготавливают без включения песка, то пропорции меняются, для этого берется 1 часть цемента и 9 шлака, воды необходимо такое же количество, как и в первом случае.
Полное застывание блоков, которые уже будут готовы к использованию, наступает спустя 30 дней, при температуре до 20 градусов тепла, и повышенной влажности. Застывание можно укорить, добавив в смесь пластификатор.
После полного просыхания, блоки складывают на подготовленные поддоны, пустотными участками вниз, это поможет предотвратить появление трещин.
Вид наполнительного материала
Состав шлакоблочной смеси различается по разновидности наполнительного материала, и условно обозначается различными аббревиатурами.
- Смесь, в основе вяжущего элемента которой лежит цемент.
(СКЦ)
- Раствор, где вяжущим веществом является известь. (СКИ)
- Добавление шлака различного производства. (СКШ)
- Использование алебастра или гипса. (СКГ)
Блоки разделяются по размеру, и маркируются различным образом, то есть цифра 1 означает продольный вид, 2 – половинчатый шлакоблок, 3 – перегородочный стеновой тип материала.
При использовании скрепляющего компонента, лучше не экономить потому, что блоки, изготовленные на низких марках цемента, не способны выдерживать значительных нагрузок, и являются слабыми к воздействию атмосферных осадков. Из-за воздействия таких факторов края блока будут отслаиваться. Смеси могут изготавливаться несколькими способами.
Способы приготовления смесей для шлакоблока
Самыми распространенными считаются такие пропорции: часть цемента, 3 песка, 5 шлака, количество воды равно половине цемента. Такие пропорции используют при условии, что применяется настоящий вид шлака, отработанного с металлургических предприятий. Чтобы блоки получились качественными, и прочными, шлак должен быть серого цвета, его используют как наполнительный элемент.
Можно использовать другой вид смеси без применения песка. Для этого необходимо взять одну часть цемента, и 9 шлака с металлургического предприятия, воды берется столько же, как и в первом случае.
Если применяются другие материалы, то пропорции снова меняются, для этого берут одну часть цемента, 4 отсева мелкой фракции, и воды в количестве половины объема от цемента.
Помимо основных компонентов, в любой состав можно добавить пластификатор, хотя это не является обязательным. Используя различные добавки, можно придать блоку максимально идеальные формы, а также ускорить процесс их застывания.
После того как смесь будет выполнена, ею заполняют подготовленные формы, эту работу необходимо выполнять сразу, так как раствор быстро схватывается. Хотя раствор застывает быстро, блокам необходимо время до полного высыхания изнутри.
Основные преимущества шлакоблока
Основным преимуществом такого строительного материала является невысокая стоимость. В состав смесей для изготовления шлакоблока входит большое количество шлака, золы или других отработанных материалов, которые служат основой раствора. От этого и получается низкая стоимость блоков.
Помимо этого шлакоблок имеет другие положительные характеристики.
- Материал обладает высокой прочностью для строительства стен до трех этажей.
- Блоки достаточно просто укладывать, эту работу можно выполнить самостоятельно, при этом сэкономив на найме рабочих.
- Компоненты, входящие в состав, являются доступными.
- Возведение стен не занимает много времени, укладка происходит быстро.
Преимущества шлака металлургического происхождения
В основном наполнителем служит шлак металлургического происхождения или другие отходы. Лучше использовать шлак, он имеет ряд преимуществ в сравнении с другими материалами.
- Частицы сырья отличаются прочностью, это влияет на прочность шлакоблока.
- Благодаря беспорядочным четким сторонам шлака, повышается показатель сцепления смеси.
- Шлак не является горючим веществом, что обеспечивает полную безопасность.
- Его стоимость является низкой.
Как правильно производится шлакоблок?
Форму для заливки смеси можно сделать самому, соблюдая необходимые размеры. Шлакоблок производится промышленным путем или в домашних условиях, то есть собственного изготовления. Для этого необходимо использовать вибрационный станок, и нужное сырье для приготовления раствора, также на площадке должно быть электрическое питание.
- Вначале приготавливают раствор из цемента, наполнителя, воды, и пластификатора по желанию. Пропорции цемента могут изменять в зависимости от его марок. Как описывалось выше, в качестве наполнителя лучше использовать шлак или другие подручные материалы. Перемешивают раствор вручную или при помощи бетономешалки так, чтобы получить однородную смесь. Если работы выполняются вручную, нужно подготовить лопату или тяпку, и большую емкость, например, корыто или старую ванну.
- Готовую смесь помещают в формы, и устанавливают на вибрационный станок для уплотнения. Благодаря такой процедуре, блок будет сохранять свою форму на протяжении всей сушки. Уплотнение происходит до 30 секунд.
- Затем блоки располагают на открытом воздухе, желательно установить их на поддоны, чтобы в случае дождя, можно было накрыть полиэтиленом, таким образом, защитить от влажности. Сушатся шлакоблоки около 4 недель при температуре 20 градусов тепла, влажность воздуха должна быть высокой. Чтобы ускорить высыхание добавляют пластификатор.
- Спустя 96 часов, блоки можно сложить на специальные подставки пустотой вниз, это предотвратит их разрушение, особенно в зимний период.
Технология производства блоков не является сложной, это позволяет выполнить всю работу в домашних условиях.
Смесь для изготовления шлакоблока состоит из цемента, он считается связующим материалом, шлака, который служит наполнителем, воды, и песка, этот материал добавлять необязательно. По желанию можно использовать пластификатор, он способствует быстрому застыванию, что позволяет повысить производство блоков. Шлак должен быть металлургического производства, обычно он имеет серый цвет, цемент 400 марки, песок – кварцевый, просеянный, и очищенный, а воду можно использовать любую. Все компоненты необходимо тщательно перемешать до образования однородного состава, только так можно повысить прочность блоков. Шлакоблок используют для возведения стен, сооружения фундаментов, заборов, и других строительных конструкций.
Изготовление шлакоблоков своими руками — подробная инструкция
Шлакоблок – это практичный и в тоже время не дорогой строительный материал. Подходит для строительства как гаража, так и жилого дома. Строить из шлакоблоков не дорого и быстро, а если изготовить их самостоятельно, экономия будет намного ощутимее.
А можно ли сделать блоки самому – спросите вы – Есть ли в этом смысл. Конечно, если вы надумали большое строительство ( дом, коттедж) материала потребуется много.
В этом случае лучше купить – дешевле обойдется и быстрее. Ну а если вам надо построить гараж, баню, сарай или сделать пристройку к дому и у вас на участке имеется большое количество строительных отходов – другое дело. Такая затея будет обречена на успех.
Что же давайте разберем вопрос про изготовление шлакоблоков своими руками по порядку.
Размер шлакоблоков
Стандартный шлакоблок выпускается таких размеров: длина – 390 мм; ширина – 190 мм; высота – 188 мм. Есть еще и блоки для перегородок (полу блоки), их размер: 390 × 120 × 188 мм.
Не обязательно делать шлакоблоки по стандартным размерам, можно и уменьшить или увеличить, если вы человек сильный. В зависимости от пустот, они весят от 17 до 25 кг, поэтому работать с ними довольно тяжело (особенно к концу дня).
Форма для шлакоблоков
Для их изготовления, на производстве применяются специальные металлические формы, вибростолы и прессы, прессующие бетон в форме с нагрузкой в несколько тон.
При изготовлении шлакоблоков своими руками форму обычно изготавливают из дерева. Виды и конструкции таких форм разнообразны. А по сути просто емкость или опалубка, в которую заливается бетонная смесь.
Форма служит для удержания изделия до схватывания бетонного раствора. А что бы готовый блок легче было доставать, самодельные формы часто делают разборными и без дна, подкладывая под них пленку.
Для устройства пустот можно использовать обычные бутылки (наполненные водой, чтобы не всплывали), вдавленные в нужных местах в бетон. Для удобства производства и качества изделия, цилиндры или квадраты для пустот (куски труб или деревянный брусок), лучше зафиксировать к самой форме, прикрепив их к дну или крышке.
Из чего делать шлакоблок
Как видно из названия, для его производства применяется шлак, бросовый и можно сказать бесплатный материал. Не только отходы металлургии, но и отходы от сжигания угля в котельной, старый кирпич (дробленный), и древесные опилки, придающий материалу хорошие теплоизоляционные свойства.
Конечно в состав смеси для шлакоблока входит еще цемент, песок и вода. Для дополнительной прочности, можно применять и различные добавки для бетона.
Пропорции шлакобетона
Тут в принципе все так же как и для обычного бетона, отличие лишь в том, что в качестве заполнителя применяется не щебень, а шлак. Состав: 1 ведро цемента — 3 ведра песка — 5 ведер шлака.
Цемент берут М-400, но лучше использовать М-500, его можно брать на 10 — 15 процентов меньше.
Технология изготовления
Шлакобетон делается как и обычная бетонная смесь для фундамента. Делать его можно в бетономешалке (если есть) или вручную. После заливки раствора в форму, его желательно уплотнить.
В промышленном производстве для этого используется специальное оборудование. Было бы не плохо в домашних условиях иметь строительный вибратор, а если нет, тогда просто можно простукать форму снаружи молотком.
Это делается для того, чтобы бетонная смесь распределилась по всему объему заполнив все пустоты, а так же чтобы вышел воздух, при наличии пузырьков воздуха прочность изделия снижается. Шлакоблоки извлекают из форм через 2 — 4 суток.
Так же как и при сушке бетона, следует избегать пересыхания блоков, для этого их надо периодически обрызгивать водой или накрыть пленкой. Прочность шлакоблоки наберут только через 28 дней, после этого их можно применять по назначению.
Посмотрите видео: Изготовления шлакоблока в домашних условиях
станок для производства шлакоблоков в домашних условиях и принципы его работы, состав и пропорции смеси, технология изготовления
Проблема необходимости утилизации отходов металлургического производства решилась с помощью открытия нового производства. Шлаки и золы стали добавлять в обычный бетон и получились шлакоблоки. Это такой материал, который обладает отличными звукоизоляционными и теплоизоляционными свойствами. При производстве шлакоблоков довольно небольшой расход цемента, а плотность полученного материала более низкая.
Неотъемлемым преимуществом такого полученного материала является то, что можно производить шлакоблоки своими руками. Для этого даже не требуется никакого специального технологического оборудования.
Всего существует несколько способов изготовления шлакоблоков. Это может быть самое обычное ручное замешивание с последующим уплотнением, а может быть способ, требующий использования простейшего оборудования, которое так же можно изготовить самостоятельно.
Оборудование для производства шлакоблоков: самодельный станок, вибропресс и формы
Для самостоятельного изготовления шлакоблоков понадобиться бадья, в которой вручную будет замешиваться состав, форма, лопата и мастерок. Если будет необходимость в создании пустот, внутрь формы устанавливаются обычные пустые бутылки или цилиндрические болванки.
Сама форма для изготовления шлакоблоков может быть выполнена из обычной обрезной доски. Между двумя параллельно установленными досками делают перемычки и в образовавшиеся модули заливают раствор. Внутренние стенки самодельной формы необходимо смазать солидолом или какой-то другой смазкой. Как только раствор отвердеет, форму можно разбирать и начинать процесс сначала.
Подобная техника производства шлакоблоков в домашних условиях подойдет лишь для изготовления небольшого количества материала, которого хватит только для маленькой хозяйственной постройки. Если же планируется большая стройка, то лучше изготовить станок для производства шлакоблоков. Так же нужны будут и формы, способные выдержать большое количество заливок. Для их изготовления лучше использовать металл, ламинированное ДСП, фанеру или пластик.
Как же сделать станок для изготовления шлакоблоков? Самым главным критерием при выпуске шлакоблоков является вибрация, ведь станок должен полностью обеспечивать быстрое и надежное уплотнение раствора. Как нельзя лучше для подобного действия подойдет вибростол, на который и будут устанавливаться формы для заливки.
Конечно же, можно придумать и более сложную конструкцию вибростанка для производства шлакоблоков. Для этого подойдут станины или рамы, основой которых будет вибромотор, который можно сделать из самого обычного электродвигателя с эксцентриком. На такую конструкцию будут закрепляться различные разборные формы. Сам двигатель лучше закрыть кожухом, это предохранит его от попадания брызг раствора и воды.
Делаем шлакоблоки: технология производства, необходимое сырье, состав смеси и сушка готовых изделий
После момента познания как сделать станок для шлакоблока и его производства, можно приступать непосредственно к процессу изготовления блоков. Начинается такое производства с подготовки материала. Помимо шлаков в смесь добавляются и иные наполнители. Оптимальным вариантом состава для производства является следующий:
- Керамзитовый песок – 2 части;
- Шлак – 7 частей;
- Мелкий гравий – 2 части;
- Вода – 3 части;
- Цемент М500 – 1,5 части.
Важно, что бы во всех наполнителях отсутствовали чужеродные примеси. Именно поэтому лучше керамзитовый песок и шлак посеять через сито, освободив их при этом от мусора и земли.
Технология изготовления шлакоблоков заключается в том, что изначально готовится сухая смесь. Все компоненты тщательно перемешиваются. Лучше если это будет сделано в бетономешалке. После добавляется вода и вновь все перемешивается.
Готовую смесь разливают в формы для изготовления шлакоблоков, стенки которых предварительно смазываются мыльным раствором или техническим жиром. Разливать в формы готовый состав необходимо как можно быстрее. Уровень заливки в формы должен быть ниже края на 5 см.
Формы с составом устанавливают на оборудовании для шлакоблоков. Далее идет процесс вибрации, который длится обычно 5-10 минут. Далее уже многое зависит именно от конструктивных особенностей станка. После формы убирают со станка и ставят новые. Если количество форм ограничено, то выдерживают время до отвердения материала, вынимают блоки и повторяют всю процедуру заново.
Складируют сырые блоки вдали от прямых солнечных лучей. В противном случае может произойти их растрескивание из-за неравномерного высыхания. Использовать готовые блоки в строительстве можно не ранее 3 дней после производства. Однако лучше это делать ещё позже. Стоит отметить, что шлакобетон набирает свою марку только на 28 день.
Строительные блоки. Технология производства блоков
Процесс производства строительных блоков на вибростанках Вибромастер можно представить в виде следующей технологической схемы:
Таким образом, производство строительных блоков включает в себя следующие технологические этапы:
Приготовление жесткой бетонной смеси из цемента, заполнителя и воды
Раствор лучше всего готовить в бетономешалке принудительного типа (т.е. со смешивающими лопастями).
Из предлагаемого нами ассортимента это модели смесителей Вибромастер РП-200 и Вибромастер СБ-80. Бетономешалки гравитационного типа («груши») использовать можно, но получить при этом качественное смешивание не получится.
Смешивать также можно и вручную, лопатой в любой емкости. При этом для приготовления жесткой смеси потребуется значительные физические усилия. Крайне мала будет и производительность такого перемешивания.
В зависимости от использованного заполнителя (керамзит, опилки, шлак, песок) получаем соответственно раствор будущего керамзитобетона, опилкобетона, шлакобетона, пескобетона.
Цикл вибропрессования
Цикл вибропрессования, состоит из следующих этапов:
- Загрузка раствора в форму станка (производится вручную)
- Уплотнение в форме с помощью вибрации и прижима (пуансона).
Уплотнение в форме под действием вибратора занимает обычно 20-30 секунд. Это время и качество уплотнения зависит только от вибратора. На станках «Вибромастер» мы применяем только настоящие сертифицированные вибраторы с большой возмущающей силой. Поэтому качество шлакоблоков и скорость производства гарантируется. - Выемка блока из формы происходит сразу же после уплотнения. Блок остается либо на поддоне, либо прямо на земле (в зависимости от конструкции станка). Жесткий раствор и качественное уплотнение позволяют полученному блоку не рассыпаться и держать форму «самостоятельно» и «не поплыть» во время высыхания. Блок на поддоне можно сразу же перенести на стеллаж для дальнейшей сушки и набора прочности. Некоторые модели вибростанков «Вибромастер» предусматривают распалубку формы непосредственно на месте сушки.
В итоге получаем отформованный стеновой строительный блок. Опять же, в зависимости от состава это может быть:
- керамзитобетонный блок,
- арболитовый блок,
- шлакоблок,
- пескоблок.
Необходимый набор прочности
Набор первоначальной прочности (достаточный для складирования) происходит при естественной температуре от 36 до 96 часов (без применения специальных добавок — ускорителей твердения – ХК, релаксола и других). Это время в данном случае зависит только от свойств цемента и температуры окружающего воздуха.
При использовании указанных ускорителей твердения это время может быть уменьшено до 5-8 часов (в зависимости от дозировки ускорителя).
Очень желательно в первые дни набора прочности предохранять блоки от пересыхания. Для этого достаточно накрывать их пэ пленкой. Также можно время от времени поливать блоки водой.
Набор отпускной прочности (согласно ГОСТ — не менее 50% от расчетной окончательной) происходит при положительной температуре примерно в течение недели. После этого периода блоки уже можно продавать потребителю и использовать на стройплощадке.
Набор 100%-ой прочности протекает в течение 28 суток при положительной температуре.
Технология производства блоков в виде печатной брошюры бесплатно прилагается к любому из станков «Вибромастер». В «Технологии производства строительных блоков» (ее объем — свыше ста страниц текстовой и графической информации) приведены все возможные составы формовочной смеси (в т.
ч. и бесцементные, на основе природных вяжущих веществ — извести, гипса, магнезии и их смесей) для изготовления шлакоблоков, керамзитобетонных блоков, арболитовых блоков, пескоблоков, саманных камней из грунтобетона, а также для всех других видов блоков. Используя приведенные в технологии методики, Вы также сможете самостоятельно рассчитать составы смесей с использованием имеющихся в Вашем распоряжении местных заполнителей. Фактически — это целый справочник по всем основным вопросам производства строительных блоков. Отдельно от оборудования он не предоставляется и не продается.
Помимо технологии производства к установкам прилагается подробная инструкция по работе с ними. Для работы на установках не требуется специального обучения и каких-то особенных навыков работы. Будет достаточно внимательно ознакомиться с технологией производства и инструкцией.
Вы также можете посмотреть следующие разделы
- Cтроительные блоки
- Исходные компоненты
- Конструкция станков
- Сертификация
- О нашей марке «Вибромастер»
- Полезные статьи
- ГОСТы и СНиПы
- Термоблок
Технология производства шлакоблоков | ООО «Златстрой»
Вибропрессованные блоки обладают лучшими характеристиками морозостойкости, прочности, плотности, нежели блоки, полученные с применением иных технологий. Вибропресс для производства шлакоблоков от ООО «Вибропресс« позволяет повысить эти характеристики, а также добиться непревзойденно точной геометрии готовых блоков. Вибростанок обладает высокой производительностью (до 500 блоков в час), следовательно быстро окупается.
На заводе по производству блоков вибропрессованием можно создавать теплоблоки (легкие, ровные, надежные, безотходные), для кладки которых не требуется высокая специализация, сложная отделка и привлечение грузоподъемной техники для монтажа стеновых блоков. Методика вибропрессования позволяет полностью механизировать процесс в отличие от устаревшей технологии вибролитья.
Керамзитобетонный блок изготавливается из жесткой/полусухой бетонной смеси путем вибропрессования сбоку и снизу при одновременном давлении сверху. Технология производства шлакоблоков на вибропрессе выглядит следующим образом:
1 этап: подготовка смеси.
Полусухая бетонная смесь содержит цемент, воду и отсев. Количество добавляемой воды в смесь — минимально, за счет чего экономится цемент. Смесь готовится при помощи бетономешалки или включенного в линию бетоносмесителя. Идеальная консистенция смеси — когда в процессе прессования из зазоров выделяется цементное молоко.
Определить качество смеси можно, сжав ее в руке — нерассыпающийся плотный комок без воды говорит о правильном подборе смеси (дополнительный тест — блестящая поверхность при затирании куска смеси гладким металлическим предметом).
2 этап: формование.
Следующий этап технологии производства шлакоблоков начинается с выгрузки раствора в матричные формы. Смесь усиленно прижимается (сила прижима — несколько тонн) пуансоном и подвергается вибрации. Процесс формования на оборудовании «Златич» занимает около 7-10 секунд против 30-90 на другом оборудовании. Матрица удаляется, а на поддоне остаются готовые блоки.
3 этап: сушка.
Технология производства шлакоблоков подразумевает естественную сушку в течение 36-96 часов. При добавлении в смесь фулерона, релаксола или пропаривании готовых изделий процесс затвердевания можно ускорить. Сушка осуществляется на многоярусных стеллажах. После просушки блоки можно складировать друг на друга. Полное затвердевание занимает 20-27 дней. Важно сохранять на складе повышенную влажность во избежание пересыхания бетона.
Купить вибропресс могут даже предприниматели, мало знакомые с технологией производства шлакоблоков — наши специалисты создадут план-проект размещения оборудования в цехе, доставят, выполнят пуско-наладку, произведут первую партию продукции, проведут обучение. Цена станка позволяет закупить его даже небольшим предприятиям и ИП и выйти на быструю окупаемость. Стоимость продукции вы найдете в разделе «Цены». Заказать оборудование и получить консультацию можно по телефону 8 (800) 775-51-89.
Производственный процессCMU | Кладка Nitterhouse
В Nitterhouse Masonry Products мы гордимся каждым производимым нами блоком, брусчаткой и камнем.
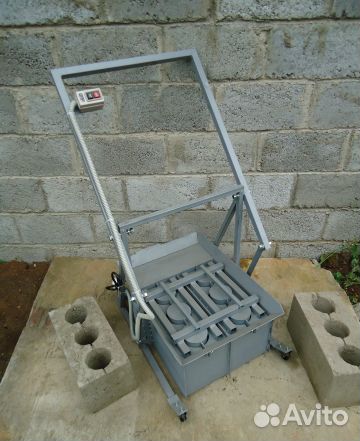
Процесс изготовления бетонной кирпичной кладки (CMU) не сильно изменился с момента его создания в начале 1900-х годов.Сырье смешивают с водой, формуют в форму и оставляют на некоторое время для отверждения. Базовый процесс прост, но с развитием отрасли на протяжении многих лет производство CMU превратилось в науку химической инженерии и архитектурной целостности.
С момента основания в 1923 году как Nitterhouse Concrete Products до семейства компаний по производству бетона и камня, которое сегодня является Nitterhouse, мы создали более совершенные системы для увеличения производства, контроля качества, мониторинга процессов и широкого спектра архитектурных бетонных изделий.В нашем процессе CMU используются лучшие технологии и оборудование, которым управляет и контролирует специальная команда, которая гордится каждым производимым нами блоком.
Мы предлагаем широкий выбор визуальных эффектов и создаем определенные конструкции, которые обеспечивают определенные структурные особенности для уникальных приложений. Вы обнаружите, что эстетически приятная естественная красота камня проявляется по-разному в зависимости от типа блока. Кроме того, переработанный материал в нашей переработанной CMU может быть именно тем, что необходимо для вашей следующей экологически ориентированной сборки.
Хотя у вас есть большой выбор внешнего вида архитектурного блока, основной процесс изготовления бетонного блока остается таким же. Тип и количество сырья, а также время отверждения будут варьироваться, а условия окружающей среды будут регулироваться в зависимости от качества, необходимого для готового продукта. Мы предоставляем наш процесс изготовления блоков CMU, чтобы помочь архитекторам реализовать наши производственные возможности, помочь инженерам выбрать блок, который является структурно стабильным для их конструкции, и дать возможность подрядчикам по кладке знать, что можно быстро произвести, когда это необходимо.
Обычно для изготовления бетонных блоков требуется всего два типа материалов: заполнители и цементы. Такие агрегаты, как песок и щебень, образуют основную структуру блока. Цемент действует как связующее, которое скрепляет агрегаты и затвердевает при смешивании с водой.
Песок, камень и цемент доставляются на наши заводы крупнотоннажными самосвалами из местных карьеров. Заполнители хранятся в открытых бункерах на территории нашего двора.Поскольку цемент чувствителен к влаге, его выдувают в наши цементные силосы. У нас есть различные типы и размеры заполнителей и цементов для производства нашей разнообразной линейки архитектурных бетонных блоков.
Каждая единица бетонного блока будет содержать следующие материалы в различных количествах и вариациях в зависимости от того, какой тип архитектурного блока мы используем на производственной линии:
Производственный процесс По сравнению с бетонными смесями, используемыми для общих строительных целей, смесь для бетонных блоков будет иметь более высокое соотношение песка, гравия и воды. В результате получается сухая густая смесь с высокой прочностью на сжатие, которая сохраняет свою форму при извлечении из блочной формы.
Материалы, необходимые в течение дня, собираются во дворе фронтальным погрузчиком и сбрасываются в закрытые отсеки, подключенные к производственной линии. Наш оператор станка выбирает количество сырья, необходимое для производимой партии, с помощью нашей компьютеризированной системы, которая точно измеряет и высвобождает материал для изготовления блока того типа, который мы используем.
Вот как проходит процесс:
- Смешивание
После измерения необходимого количества материалов они выгружаются на конвейерную ленту. Конвейер перемещает материалы в смеситель объемом 1,75 куб. Ярда, куда добавляется вода по мере заливки заполнителей и бетона. Вода также точно контролируется с помощью нашей электронной измерительной системы, чтобы гарантировать, что смесь не будет слишком влажной или слишком сухой.
Затем добавляют любые дополнительные добавки, такие как гидрофобизаторы или пигменты, и смесь перемешивают в течение шести-восьми минут.
- Багет
Когда смесь должным образом смешана, бетон перемещается на другую конвейерную ленту, которая направляется в нашу блочную машину. Одна из наших различных форм будет настроена для конкретного типа CMU, который мы производим для данной партии. После заливки шихты в формы блочная машина уплотняет бетонную смесь вибрацией. Мы делаем это, чтобы придать бетону прочность и закрепить бетон в блок.
Формовка бетона — самый важный этап в изготовлении CMU.Правильное сжатие необходимо для получения качественного готового продукта. Материалы загружаются в формы с измеренной скоростью потока, а время и сила вибрации точно контролируются, чтобы обеспечить подходящую высоту и прочность блока.
Когда достигается надлежащее сжатие и уплотнение, блок выталкивается из формы на стальной поддон, чтобы его можно было транспортировать в нашу печь для отверждения. На этой стадии цемент называют «зеленым блоком», прежде чем он затвердеет.
- Отверждение
Затем поддоны перемещаются на тележки, которые перемещаются в нашу паровую печь низкого давления для нагрева. Как правило, стеллаж для бетонных блоков предварительно устанавливается в печи при нормальной влажности и температуре (от 70 до 100 градусов по Фаренгейту) на срок до трех часов. Затем пар постепенно вводится в печь, и температура постепенно повышается до соответствующего уровня.
Когда достигается максимальная температура, пар и тепло отключаются, и блоки полимеризуются еще 12-18 часов в горячем влажном воздухе.Затем влажный воздух выпускается из печи, и температура повышается, чтобы полностью высушить блок.
Блок обычно затвердевает в течение 16-24 часов при высокой влажности и средней температуре примерно 100 градусов по Фаренгейту.
- Создание кубов и хранение
По окончании отверждения бетонный блок выкатывается из печи. Затем каждый блок разбирается и помещается на конвейер. Они переходят к нашей системе кубиков, которая укладывает блоки на деревянный поддон.Каждый блок выровнен и уложен в куб, четыре блока в поперечнике, два блока в глубину и шесть блоков в высоту.
Наши блоки с разъемной поверхностью, например, формуются из двух блоков, соединенных вместе. Как только они затвердеют, двойные блоки проходят через наш сплиттер. Разделитель ударяет по соединенным блокам, заставляя их ломаться и создавать грубую текстуру на одной стороне каждой части. Затем они складываются в кубы.
Мы оборачиваем кубик в пластик для безопасности и защиты от непогоды, и его забирают вилочным погрузчиком для размещения в соответствующей части нашего двора для этого конкретного типа блока или для определенного заказа.Отсюда будут прибывать блочные грузовики и загружать продукт по мере необходимости.
Гарантия качества на нашем производстве CMU
Различные участки нашего завода постоянно контролируются, чтобы подтвердить, что мы производим блоки с конкретными характеристиками. Будь то прочность, атмосферостойкость и химическая стойкость или технические характеристики конструкции, у нас есть электронный контроль, и операторы станков постоянно следят за тем, чтобы готовый блок работал должным образом. Гарантируем:
- Заполнители и цемент взвешиваются с помощью электроники, чтобы убедиться, что правильные части каждого материала, которые влияют на внешний вид, ощущение и долговечность блока, являются правильными.
- Содержание влаги в песке и гравии измеряется ультразвуковыми датчиками, поэтому в смесь можно добавить точное количество воды для точного содержания воды, необходимого для партии.
- Размер и плотность каждого блока проверяется датчиками лазерного луча при выходе каждого блока из блочной машины.
- Среда отверждения регулируется электроникой для контроля времени цикла, температуры и давления. Вся информация записывается по каждой партии.
- Готовые блоки проходят испытания на различные качества, такие как звукопроницаемость, водопроницаемость, огнестойкость, прочность и усадка.
Бетонный блок может выдерживать суровые погодные условия, огонь и другие формы серьезных повреждений. Нет ничего лучше, чем строить из блоков, если вам нужен прочный, огнестойкий, устойчивый к насекомым и вторжению строительный материал. Мы заботимся о сохранении целостности каждого блока, покидающего наше растение.
Многоликий архитектурный бетонный блокВ Nitterhouse Masonry Products мы гордимся каждым производимым нами блоком, брусчаткой и камнем.Мы всегда следим за тем, чтобы вся наша продукция производилась в соответствии с высочайшими стандартами и наилучшим качеством. Наша линейка архитектурных бетонных блоков включает в себя множество вариантов с текстурированной поверхностью или гладкой отделкой шпоном, а также различных цветов, форм и размеров, чтобы предоставить профессионалам в области дизайна широкий спектр возможностей для строительства бетонной кладки.
Если вам нужен базовый бетонный блок для срочной работы, у вас есть архитектурная особенность для строительства или вам нужен особый вид сложного офисного здания, мы можем изготовить нужный вам блок. Ознакомьтесь с каждой единицей бетонных блоков, чтобы узнать все, что доступно для вашего следующего строительного проекта:
- Шлифованная поверхность. Наша шлифованная поверхность CMU отшлифована по крайней мере с одной стороны, что придает ей гладкую, богатую поверхность. С 20 стандартными цветами у вас будет множество вариантов комбинирования цветов, но мы также можем настроить пигмент в соответствии с вашими требованиями к дизайну.
- Разделенная поверхность. Этот текстурированный блок поставляется со стандартной отделкой Split Face, Split Wide Profile и Split Fluted, чтобы удовлетворить широкий спектр архитектурных образов.Глубина и размер этой конструкции являются фаворитом для множества внутренних и внешних строительных проектов и, как и многие наши CMU, могут использоваться на уровне или ниже.
- Античная отделка. Наш Antique CMU обработан дробью, которая красиво обнажает находящийся под ним камень.
У нас есть несколько стандартных цветов, и если они вам не подходят, мы можем настроить цвет именно для вашего проекта. Этот блок обеспечивает прекрасный, выветренный вид с деревенской текстурой, которая используется как для внутреннего, так и для внешнего строительства.
- Традиционный монарх. Вы получаете вид глиняного кирпича с качеством блока в нашей линейке Monarch Traditional. Эти CMU имеют длину и глубину обычного блока, но высоту стандартного кирпича. Вы можете использовать этот блок на уровне и ниже. Мы разработали их в соответствии со стандартами ASTM-C90 для несущей бетонной кладки.
- Elite CMU. Нет необходимости укладывать блок и облицовывать его керамической плиткой для внутренних работ.Наш Elite CMU — это выдающийся строительный материал для совершенства как внутри, так и снаружи. Эти полированные и наполненные блоки с такими вариантами цвета, как лосось и ружейный металл, идеально подходят для крупных коммерческих проектов, таких как школы или муниципальные здания, где требуется этот оттенок цвета и стиля.
Лица шлифуются, а затем заполняются наполнителем из акриловой смолы. После полировки они герметизируются нашим герметиком, совместимым с летучими органическими соединениями (VOC).
- CMU из вторичного сырья. Наш «Эко-умный» вторичный преобразователь частоты производится с нашей шлифованной поверхностью и с разделенной поверхностью.С минимум 30% переработанного материала, это популярный выбор для вашего экологически ориентированного проекта. Переработанный контент будет приносить баллы LEED (Лидерство в области энергетики и экологического дизайна) для вашего устойчивого развития.
- Камень наследия. Наш Камень Наследия — это архитектурный фанерный блок, который демонстрирует совокупное содержание блока. Он изготовлен с прочностью 8500 фунтов на квадратный дюйм и поглощением менее 5%. В нашей линейке Legacy есть четыре разных вида отделки, которые часто смешиваются в одном проекте для визуальной привлекательности и структуры:
- Linear Collection — две отделки на одном блоке: шлифованная поверхность и дробеструйная обработка.
Ширина каждой полосы настраивается для соответствия уникальному дизайну, а между двумя разными видами отделки есть глубокие линии.
- Текстурированный — поверхность обработана дробеструйной обработкой, дающая легкую текстуру и размер.
- Terrazzo — законченный с отшлифованной поверхностью, гладкий и полированный определяет этот бетонный блок. Его часто используют для обозначения полос.
- Точеный циферблат — эти камни с отделкой, напоминающей ограненный известняк, часто используются в качестве акцентирующих полос для разделения больших участков одного цвета и текстуры.
- Linear Collection — две отделки на одном блоке: шлифованная поверхность и дробеструйная обработка.
Выберите нужный блок различных форм для конкретных строительных приложений. Мы производим специальные формы бетонных блоков для строительства соединительных балок, контрольных швов, закругленных углов и многих других архитектурных планов.
Все архитектурные CMU Nitterhouse герметизированы герметиком на водной основе из акриловой смолы, совместимым с летучими органическими соединениями, и должны быть покрыты другим герметиком после завершения кладочных работ. Мы также добавляем водоотталкивающую добавку во все партии бетонных блоков, чтобы уменьшить впитываемость и проницаемость.Мы предлагаем эту добавку для добавления в раствор при кладке стен.
Работая более 90 лет, мы расширяем линейку продуктов и производственные возможности по мере изменения технологий и лучших практик. От бизнес-амбиций каменщика Уильяма Л. Ниттерхауза, строящего свой собственный блок в своем гараже до семейной линии в пятом поколении, которая занимается нашим производством камня сегодня, мы сделали своим делом обеспечение наилучшего качества, возможностей и дизайна.
В будущем промышленность по производству блоков продолжит вводить новые формы, размеры и экономические преимущества в строительство зданий. Энергоэффективность и долговечные конструкции по-прежнему будут в авангарде новых разработок. Наши дизайнеры создали превосходные продукты, которые доказали, что представляют собой гармоничное сочетание эстетической привлекательности и структурной надежности для любого типа здания.
Если вам нужно построить общественный центр или построить высотное здание, вы обнаружите, что мы можем предоставить именно то, что вам нужно, чтобы сделать ваш проект исключительным.Ознакомьтесь с нашей полной линейкой архитектурных бетонных блоков и откройте для себя разнообразие, которое даст вам гибкость проектирования. Для получения дополнительной информации о нашем процессе изготовления блоков или о любых наших изделиях из каменной кладки, пожалуйста, свяжитесь с нами сегодня.
Процесс производства бетонных блоков — BESS
Бетонный блокБетонный блок — это бетонный блок. Для повышения качества блоков необходимо приложить вибрацию и усилие, чтобы раствор получился максимально сжатым.
Бетонный блок — это общее название, которое включает в себя различные типы блоков. Ниже вы можете увидеть несколько примеров бетонных блоков.
1. Пустотные бетонные блоки различных форм и размеров.
2. Полнобетонные блоки различной формы и размеров.
3. Бордюры разных форм и размеров.
4. Брусчатка разной формы, размера и цвета.
5. Газобетонные блоки (также называемые газонными камнями).
6.Бетонные желоба, также известные как водосточные желоба.
7. Лего бетонные блоки
8. Блоки пенобетонные
9. Блоки пустотного перекрытия
Во всех пунктах вы можете увидеть бетон, но вы можете спросить, что это такое. Бетон формируется из заполнителей, воды и портландцемента, который обычно находится в виде порошка. Существуют разные стандарты соотношения компонентов смеси. Также доступны добавки для придания бетону дополнительных свойств.
Обратите внимание, что есть разница между добавкой и добавкой. Добавки добавляются в цемент во время производства, чтобы получить новые свойства цемента, но добавки добавляются в бетон во время смешивания, чтобы получить новые свойства.
В зависимости от страны вы также можете использовать различные заполнители, наиболее распространенными заполнителями являются известняк, ракушечник, мел или мергель в сочетании со сланцем, глиной, сланцем, доменным шлаком, кварцевым песком и железной рудой. Вы можете узнать больше об этой теме в Concrete Network.Также подробнее о пустотных бетонных блоках вы можете прочитать в нашей статье «что такое пустотелый бетонный блок вообще и подробно».
Процесс производства бетонных блоков состоит из различных этапов в зависимости от системы, в которой вы их производите. Процесс производства бетонных блоков может быть ручным, полуавтоматическим, автоматическим и полностью автоматическим в зависимости от вашего спроса, страны и бюджета. Ниже вы можете прочитать о них.
1.Процесс изготовления бетонных блоков вручную:Ручной метод — самый простой и дешевый способ. Все, что вам нужно, это формочки. Бетон смешивается вручную, а затем заливается в формы для бетонных блоков. Обычно при ручном методе нет вибрации и высокого давления, поэтому качество бетонных блоков низкое.
Поскольку раствор смешивается вручную, вы не можете достичь определенного соотношения, и каждый раз оно будет другим, что будет влиять на качество конечного продукта. Ручной метод также слишком медленный, поскольку все дела выполняются вручную. Этот метод больше не предлагается, так как он не имеет преимуществ и не является промышленным.
В процессе производства полуавтоматических бетонных блоков вам понадобится машина, которая производит блоки. Эта машина называется машиной для производства бетонных блоков, в ней установлены формы, и она производит бетонные блоки, используя давление и вибрацию в формах.Преимущества полуавтоматического процесса изготовления бетонных блоков заключаются в том, что качество конечного продукта выше, чем у ручного, поскольку оно производится с использованием гидравлического давления и вибрации.
Недостатком этого метода является то, что процесс смешивания по-прежнему выполняется вручную, и соотношение бетона каждый раз будет различным. Кроме того, поддоны из машины доставляются ручными тележками, и для обработки производства требуется 3 рабочих, поэтому вам потребуется больше рабочих по сравнению с другими методами производства.
Если у вас ограниченный бюджет и вы живете в стране с низкой стоимостью рабочей силы и дешевой землей, этот вариант — лучший вариант для вашего бизнеса.
3. Автоматический процесс изготовления бетонных блоков:Автоматический метод изготовления бетонных блоков — самый популярный вариант по данным нашего отдела продаж. Приготовление раствора в этом методе выполняется автоматически, поэтому качество раствора будет неизменным с течением времени, поскольку точное соотношение используется постоянно.Производственным процессом также занимаются роботы, и вместо трех ручных тележек для обработки продукции используется один вилочный погрузчик. Цемент также хранится в цементном бункере и автоматически добавляется в смеситель. Таким образом вы можете сократить количество рабочих на вашем предприятии. Учтите, что в этом методе машиной управляет оператор.
4. Полностью автоматический процесс изготовления бетонных блоков: Разница между автоматическим и полностью автоматическим методами заключается в том, что в автоматическом методе вам нужен оператор для управления машиной, но в полностью автоматической машине для бетонных блоков машина работает автоматически. Эта конструкция подходит для развитых стран, где стоимость рабочей силы высока, а земля также дорога.
Эти машины также называются блокировочными кирпичными машинами. На рынке доступны различные типы машин для производства бетонных блоков. Некоторые из них мобильные, некоторые — стационарные. Также существуют разные уровни автоматизации для машин.
Эта статья посвящена процессу производства бетонных блоков, поэтому детали машины здесь не обсуждаются. Если вам интересно узнать больше о машинах для производства бетонных блоков, вы можете прочитать «Машина для производства бетонных блоков: описание и цена» или «Цена и детали машины для производства кирпича».
Учтите, что выбирать машину, подходящую для вашего завода, совсем неразумно. Чтобы выбрать лучшую машину, необходимо учитывать техническую информацию, такую как размер поддона, гидравлическое давление, потребляемая мощность и сила вибрации. Bess предлагает вам высококачественные машины для производства бетонных блоков с различной производительностью и уровнем автоматизации. Ниже вы можете увидеть процесс производства бетонных блоков на нашем полуавтомате. Вы можете получить доступ к большему количеству видео на наших каналах YouTube VESS machine EN и BESS machine EN.
Для производства бетонных блоков вам необходимо обеспечить завод сырьем, таким как заполнитель, вода и портландцемент.Затем вам нужно смешать их вместе, чтобы получилась однородная кремообразная смесь. Доступны различные соотношения компонентов смеси в зависимости от стандартов вашей страны и общей доступности. Также, в зависимости от выбора машины, это делается вручную или автоматически.
После того, как вы приготовили раствор, пора подавать его в машину. Обычно это делается с помощью конвейерных лент. Затем обо всем остальном позаботится машина. раствор сначала заливается в бункер агрегата машины, а затем раствор автоматически подается в формы.Когда форма заполнена раствором, пора гидравлическому прессу произвести сжатие. Вибрация также помогает гидравлической системе максимально сжать ее.
После того, как бетонные блоки сформированы на поверхности поддонов, машина направляет поддон к выходу из машины. Теперь все зависит от вашей машины, если она полуавтоматическая, она доставляется в секцию твердения ручными тележками.
Если ваша машина для производства бетонных блоков является автоматической машиной, то сначала 5 поддонов складываются друг на друга, а затем они забираются вилочным погрузчиком и доставляются в секцию твердения.
Если покупка земли в вашем районе стоит слишком дорого, то лучше выбрать автоматическую систему, чтобы сэкономить землю для участка обработки до 5 раз.
Каждый день состоит из трех смен, каждая смена длится восемь часов. Проще обсуждать вместимость в каждую смену, чтобы не было путаницы.
В зависимости от производимого вами бетонного блока мощность вашего завода по производству бетонных блоков различается. Обычно мощность производства брусчатки указывается в квадратных метрах, а пустотелые блоки и массивные блоки описываются цифрами. Машины для производства бетонных блоков, предлагаемые Bess, могут производить 4000 штук стандартных блоков (ширина 20 см, длина 40 см, высота 20 см) или 300 квадратных метров брусчатки за восемь часов.
Заключение
Для производства бетонных блоков в соответствии с рыночным спросом и доступностью на местном уровне вам необходимо выбрать подходящую машину и соответствующий бизнес-план по производству бетонных блоков. Инженеры Bess могут помочь вам на каждом этапе этого бизнеса. Все, что вам нужно сделать, это связаться с нами.
Машины для производства бетонных блоков и их классификация
История блокировочных машин
Современная промышленность по производству бетонных блоков не является результатом постепенной эволюции, а была внезапно вызвана изобретением машины с регулируемыми съемными формами, способными производить твердые блоки.
Твердые бетонные блоки были впервые применены в 1832 году в Англии строителем Уильямом Рейнджером, который запатентовал свою версию «Искусственного камня Рейнджера».Спустя несколько десятилетий, в 1860 году, для возведения стен стали использовать пустотелые бетонные блоки.
В 1868 году строитель по имени Фрир основал то, что можно было считать первым стационарным заводом по производству бетонных блоков на американском континенте. Однако ссылок на первый блочный слой не обнаружено.
Внешний вид блоков (potser posaria — внешний вид блоков), который известен сегодня, был установлен, когда Harmon S. Palmer получил свой первый патент США на «Машины для формования бетонных блоков» в 1887 году, хотя есть и другие патенты на другие типы машин, такие как как у Эйхельбергера в 1905 году.
Сегодня бетонные блоки производятся практически во всем мире благодаря их высокому качеству и спросу на экономичные строительные материалы. Из разнообразного сырья можно производить тысячи бетонных блоков разных размеров и форм. Характеристики существующих бетонных блоков будут представлены позже.
Производство блоков также направлено на частичную замену глубоко укоренившейся в нашем обществе технологии строительства жилья на основе обычного кирпича из обожженной земли, сделанного из невозобновляемых ресурсов и с воздействием на окружающую среду, которое его продукция приносит.
Классификация
Из рассмотренных ссылок известно, что машины для изготовления блоков производятся как в развитых, так и в развивающихся странах. Есть два ведущих производителя этих машин: Китайская Народная Республика и Республика Индия.
Согласно полученной информации, машины для изготовления блоков можно классифицировать следующим образом:
1. Укладочные машины
Гидравлика : это колесные машины, которые производят бетонные блоки.Они кладут блоки на бетонный пол, а затем переходят к следующей позиции, где будут размещены новые блоки. Этот процесс устраняет необходимость в деревянных или стальных платформах. Форма и поршень перемещаются через гидроцилиндры, создавая более прочный блок и позволяя производителю использовать меньше бетона. Любые пустотные блоки могут быть изготовлены из хорошего качества, а также полнотелый кирпич и брусчатка. Пример этих машин показан на рисунке 1.
Рисунок 1 — rometa — укладчик гидравлический (https: // www.rometa.es/bloques-hormigon-instalaciones/ponedoras-hormigon-instalaciones). Пример гидравлического укладчика
Руководства : это машины с ручным управлением, которые производят блоки по низкой цене. Он идеально подходит для запуска мелкосерийного производства блоков. Блоки укладываются на бетонный пол, и машина перемещается оператором к следующей укладке. Эта процедура устраняет необходимость в платформах для обработки блоков и манипуляторах, которые обычно перемещают зеленые блоки и платформу машины до того, как могут быть изготовлены следующие блоки.На машину можно установить любую форму.
2. Стационарные машины:
Гидравлика : это стационарные машины для производства бетонных блоков. Блоки помещаются на деревянную платформу, а затем рабочие перемещают их на пол. Форма и поршень перемещаются через гидроцилиндры. Возможно изготовление полых блоков любого типа.
Руководства : это ручные машины, которые производят блоки по низкой цене. Блоки размещаются на деревянной платформе, а затем оператор переносит их на пол.
Ручной с вибратором на 1 или 2 формы : это ручные машины, которые производят блоки из 1 или 2 форм. Вибратор улучшает качество блоков. Блоки размещаются на деревянной платформе, а затем оператор переносит их на пол.
3. Автоматические стационарные установки:
Эти машины имеют системы периодической обработки, автоматизированные системы смешивания и прессования бетона. Передача блоков осуществляется системой передачи, обычно через конвейеры.Производительность этих машин, в зависимости от типа блока, может составлять от 12 000 до 20 000 блоков за 8 часов. Человеческие усилия минимальны. Это самые дорогие машины.
Ниже описаны основные преимущества и недостатки укладочных и стационарных машин, за исключением растений:
Укладчики:
Преимущества:
- Платформы для передачи произведенных блоков не требуются.
Недостатки:
- Для производства требуется довольно большая бетонная плита.Плита дорогая и ее размеры должны соответствовать производственным параметрам.
Стационарные машины:
Преимущества:
- Для производства требуется относительно небольшое пространство.
Недостатки:
- Платформы необходимы для перемещения произведенных блоков. Эти платформы изначально дороги и требуют замены при повреждении в повседневной работе.
Вы можете увидеть больше машин и типов блоков на фабрике блоков Rometa, откуда мы получили информацию.
Блок для зеленых стен
Портландцемент — это материал, который ненавидят архитекторы и дизайнеры, занимающиеся устойчивым строительством. Но до недавнего времени на рынке не было альтернатив, особенно для строительных конструкций. Это меняется. Среди продуктов, призванных восполнить этот пробел, — новая кладочная из Напы, Калифорния. Watershed Materials, которым руководит евангелист строительства утрамбованной земли Дэвид Истон. Модульный Блок водораздела состоит из расплавленных обломков почвы и горных пород, включая кварц, полевой шпат, глину и другие минералы.Блок с полыми ячейками содержит половину цемента, чем типичные бетонные блоки, но весит на 30 процентов больше.
Какова ваша цель для блока водораздела?
Мы пытаемся избавиться от нашей зависимости от энергоемкого портландцемента и разрабатываем серию формул, позволяющих воссоздать оригинальный римский цемент, в котором вулканический пепел был смешан с известью и фрагментами горных пород для создания этого удивительно прочного бетона. .Портландцемент — фантастический продукт, потому что он может склеивать песок и гравий для получения чрезвычайно прочных готовых изделий — от 7 000 до 10 000 фунтов на квадратный дюйм. Римский цемент не может обладать такой прочностью, но очень мало областей применения, в которых вам нужно что-то, чтобы быть настолько прочным.
Какие преимущества для архитекторов и дизайнеров, работающих с клиентом?
Вы берете один из самых распространенных в мире строительных компонентов и делаете его лучше — более ресурсосберегающим, энергоэффективным, географически подходящим, полностью пригодным для вторичной переработки и с меньшим углеродным следом. И это действительно эффективная структура и отделка. Ваши каменщики сложили его, и готово. Нет Тайвека, нет картины, нет обрешетки снаружи. Это очень интересно, если у вас короткие сроки проекта. Мы упорно трудились, чтобы разработать ряд композиций, которые делают блок выглядят как сырая порода.
Вы можете объяснить науку, лежащую в основе этих формулировок?
Цемент включает известняк, который был добыт, раздроблен, нагрет и измельчен в порошок, и его сцепление может быть улучшено путем добавления смеси других материалов.Мы пытаемся идентифицировать эти встречающиеся в природе материалы, смешивать их и определять размер для использования с активаторами, с которыми они смешаны, такими как гидроксид натрия и силикат натрия. Затем мы применяем гидравлическое давление и высокочастотную вибрацию. Процесс основан на технологии утрамбовки земли, которая показала, что сжатия недостаточно. Вам нужно, чтобы все частицы отскакивали друг от друга в матрице для создания плотности за счет контакта зерна с зерном.
Как этот процесс влияет на производственные затраты?
Это один из элементов, который мы пытаемся решить.Мы пытаемся разработать технологию, которая отражает производство бетонных блоков, но с исключительно низким углеродным следом. Наш пресс для водораздела первого поколения — это машина с медленным циклом, поэтому стоимость изготовления каждого блока на этом этапе высока. Это трудоемко. Мы сравниваем его с ценами на все другие дорогие бетонные блоки, включая окрашенные блоки, блоки с разделенной поверхностью и блоки с шлифованной поверхностью. Мы начинаем вкладывать средства в совершенствование технологии, чтобы машина имела более короткий цикл. Стоимость нашего сырья значительно ниже, чем стоимость сырья для типичного бетонного блока, поэтому все, что нам нужно сделать, это достичь эффективности производства, и тогда мы думаем, что у нас будет очень привлекательная цена.
Сколько времени сейчас нужно на создание одного блока?
Двадцать секунд или три в минуту. Я хочу получать 20 блоков в минуту. Тогда у нас была бы машина, которая была бы такой же быстрой, как большие машины для бетонных блоков, которые используются сегодня.
Откуда вы берете материалы?
Наш завод находится рядом с карьером, который обеспечивает 80 процентов наших необработанных заполнителей. Мы намеренно расположились рядом с этим карьером, потому что знали, что у него есть побочный продукт, который соответствует нашей философии бизнеса, и что он не может продаваться как продукт премиум-класса.Многие наши формулы содержат от 70 до 80 процентов материала этого конкретного карьера. Для оставшихся 10 или 15 процентов, которые влияют на цвет блока, мы уйдем на расстояние 30 миль от завода.
Как далеко вы отправите блоки, чтобы выполнить заказ?
Он доступен везде, но я не думаю, что нужно брать что-то подобное и отправлять его [далеко]. Вы могли бы привести аргумент, что, пытаясь развить понимание и широкое распространение продукта, вы захотите поместить его в вагоны поезда и доставить на большие расстояния. Но в конечном итоге это не соответствует нашей философии сохранения ресурсов и сокращения выбросов углекислого газа.
Какие проблемы возникают на пути понимания технологии цепочкой поставок?
В начальных блоках используется обычный портландцемент, чтобы обеспечить уровень уверенности, который, по нашему мнению, нужен рынку сейчас. В отличие от бетонных блоков, которые везде одинаковы, блок водораздела требует более глубоких научных исследований. Без портландцемента в качестве универсального клея производитель должен быть более осторожным в его составах.Сладкое пятно — это смесь, в которой природные минералы делают большую часть работы, а углеродный след минимален.
Каков статус вашей работы с Национальным научным фондом (NSF) по разработке блока, не содержащего портландцемента?
В 2012 году компания Watershed получила грант Фазы I от NSF на исследование возможности производства строительного блока, который отвечал бы стандартам качества ASTM C-90, без использования портландцемента. Это исследование подтвердило нашу гипотезу [о создании блоков, которые соответствуют требованиям прочности без использования портландцемента], и поэтому мы подали заявку на грант Фазы II, который, в случае его присуждения, поддержит начальную фазу коммерциализации внедрения блока с нулевым содержанием цемента в рынок.Формулировка является запатентованной, но мы ожидаем, что этот блок появится на рынке к середине 2015 года.
Где такое изделие, как Блок водораздела, попадает в царство утрамбованной земли?
Мы рассматриваем блок как логическую эволюцию монолитной утрамбованной земли. Строительство из блоков дешевле, чем монолитные стеновые системы, из-за отсутствия опалубки и меньших затрат на мобилизацию. На сложных строительных площадках или там, где конструктивная конструкция требует большей прочности стен, блоки могут быть намного более эффективными.Кроме того, утрамбованная земля — это специализированный промысел. Квалифицированных монтажников не так уж много, и это отпугнет подрядчика или банкира. Кажется, что [рынок примет] протараненную землю через 15–20 лет, и хотя я не думаю, что это займет так много времени для блока «Водораздел», он действительно должен проникнуть в сознание архитектурного и дизайнерского сообщества.
Где вы запускаете первые блоки?
Мы выбрали район залива [Сан-Франциско].Я знаю там архитектурное сообщество. Люди доверяют тому, что мы делаем, и это то, что нужно для начала.
Примечание. Эти вопросы и ответы были отредактированы и сокращены для ясности.
Производство бетонного кирпича
ИЛИ
09 июля 2019
Процесс изготовления бетонных блоков
Бетонный блок — это один из нескольких сборных железобетонных изделий, используемых в строительстве. В основном они используются при возведении стен.
Смешивание, формование, отверждение и измельчение — четыре основных процесса производства цемента
Этап 1 — Смешивание:
- Песок и гравий хранятся снаружи в штабелях и по мере необходимости транспортируются в складские бункеры на заводе. Портландцемент хранится снаружи в больших вертикальных силосах для защиты от влаги.
- Начинается производство, и необходимое количество песка, гравия и цемента под действием силы тяжести или механическими средствами переносится на весовой дозатор, который измеряет нужное количество каждого материала.
- В течение нескольких минут сухие материалы, поступающие в стационарный смеситель, смешиваются. Часто используются два типа смесителей. Планетарный или тарельчатый миксер, напоминающий неглубокую кастрюлю с крышкой, является одним типом, а горизонтальный барабанный миксер, напоминающий кофе, может быть повернут на бок, а лопасти смешивания, прикрепленные к горизонтально вращающемуся валу внутри миксера, — это другой тип.
- При смешивании сухих материалов в смеситель добавляется небольшое количество воды. В это время также могут быть добавлены красящие пигменты и химические добавки.Затем бетон перемешивается почти десять минут.
Этап 2 — Формовка:
- После завершения смешивания смесь выгружается на наклонный ковшовый конвейер и транспортируется в приподнятый бункер. Снова начинается цикл смешивания для следующей загрузки.
- В верхней части блочной машины бетон транспортируется в другой бункер с измеренной скоростью потока. Бетон в блочной машине выдавливается в формы. Формы содержат внешнюю формовочную коробку, состоящую из нескольких вкладышей формы.Внешняя форма и внутренняя форма полостей блока определяется вкладышами. За один раз можно формовать пятнадцать блоков.
- Бетон уплотняется под весом верхней головки формы, опускающейся на полости формы, только когда формы заполнены. Цилиндры гидравлического давления могут дополняться воздухом, воздействующим на формовочную головку.
Для дальнейшего облегчения уплотнения в большинстве блочных машин используется короткая волна механической вибрации.
- Уплотненные блоки перемещаются вниз и из форм на плоский стальной поддон.Блоки и поддон выталкиваются из машины на цепной конвейер. Блоки в некоторых операциях проходят под вращающейся щеткой, которая удаляет рыхлый материал с верхней части блоков.
Этап 3 — Отверждение:
- Поддон блоков транспортируется к погрузчику, который удерживает их в стойке для твердения. В каждой стойке по несколько сотен книг. И его свертывают в рельсы и перемещают в сушильную печь только тогда, когда стеллаж заполнен.
- Печь представляет собой замкнутое помещение, в котором можно одновременно разместить несколько стеллажей блоков. Двумя основными типами сушильных камер являются паровые сушильные камеры низкого давления и паровые сушильные камеры высокого давления. В паровой печи низкого давления блоки выдерживают от одного до трех часов при комнатной температуре, чтобы дать им возможность немного затвердеть в печи.
При контролируемой скорости 60 ° F в час (16 ° C в час). Подача пара отключается, и блоки могут впитаться горячим влажным воздухом в течение 12-18 часов, когда будет достигнута температура отверждения.Затем после замачивания блоки сушат, выпуская влажный воздух и повышая температуру в печи. Полный цикл отверждения занимает около 24 часов.
- В паровой печи высокого давления, также называемой автоклавом. В этом типе температура повышается до 300–375 ° F (149–191 ° C), а давление — до 80–185 фунтов на квадратный дюйм (5,5–12,8 бар). Блоки замачивают на пять-десять часов. Затем давление быстро сбрасывается, что заставляет блоки быстро выпускать захваченную влагу.Процесс отверждения в автоклаве требует больше энергии и дорогостоящей печи, которая может производить блоки за меньшее время.
Этап 4 — Кубинг:
- Поддон блоков разложен, и стеллажи вулканизированных блоков выкатываются из печи, которая помещается на цепной конвейер.
Пустые поддоны подаются обратно в блочную машину, когда блоки отталкиваются от стальных поддонов для получения нового набора формованных блоков.
- Когда блоки должны быть преобразованы в блоки с разъемными гранями, их сначала формуют как два блока, соединенных вместе.Если эти двойные блоки затвердевают, они проходят через разделитель, который ударяет по ним с помощью тяжелого лезвия по секции между двумя половинами. Это заставляет двойной блок ломаться и образовывать грубую каменную текстуру на одной стороне каждой части.
- Блоки проходят между кубом, который выравнивает каждый блок, и который укладывает их в куб на три блока по шесть блоков глубиной и три или четыре блока по высоте. Таким образом, кубики перемещаются вилочным погрузчиком наружу и помещаются на хранение.
Преимущества бетонных блоков:
- Площадь коврового покрытия здания будет увеличена за счет небольшой ширины бетонного блока по сравнению с кирпичной стеной.
- Обеспечивает лучшую теплоизоляцию, повышенную огнестойкость и звукопоглощение.
- Результатом станет экономия ценных сельскохозяйственных угодий, которые используются для производства кирпича.
- По сравнению с кладочным кирпичом возведение кладки из бетонных блоков проще, быстрее и прочнее.
- Бетонный блок имеет идеальную форму и размер, что значительно облегчает работу каменщику.
- Блоки могут быть подготовлены путем автоматического смещения вертикальных швов за счет сокращения квалифицированного надзора.
- Метод строительства из бетонных блоков может быть принят и широко распространен.
Теперь вы можете купить высококачественные высокопрочные бетонные блоки онлайн по лучшей рыночной цене на сайте materialtree.com!
ПроектFE / NETL развивает «зеленый» процесс изготовления бетонных блоков
В сотрудничестве между U.Национальная лаборатория энергетических технологий (NETL) Министерства энергетики США (DOE), Национальная лаборатория энергетических технологий (NETL) и Калифорнийский университет в Лос-Анджелесе (UCLA), более 1200 часов полевых испытаний были проведены в Комплексном испытательном центре Вайоминга ( ITC), успешно демонстрируя процесс создания бетонных блоков кладки (CMU или бетонных блоков) с использованием углекислого газа (CO 2 ) из дымовых газов электростанции без необходимости в стадии улавливания углерода. Эта демонстрация является успешной для Программы утилизации углерода и демонстрирует потенциал технологии утилизации для обеспечения большого рынка низкоуглеродистыми бетонными изделиями при одновременном сокращении выбросов CO 2 электростанций.
«Как наиболее широко используемый строительный материал, ежегодно производится более 20 миллиардов тонн бетона», — сказал Эндрю Джонс, руководящий демонстрационным проектом NETL. «Бетон дешев, плотен и эластичен, но производство обычного портландцемента (OPC), который традиционно связывает смесь, создает примерно 10% всех глобальных выбросов CO 2 ».
Технология UCLA помогает снизить эти выбросы за счет уникального процесса карбонизации, известного как минерализация, который преобразует газообразный CO 2 из дымовых газов электростанции и других источников в стабильные твердые карбонатные частицы, которые связывают компоненты в бетоне.Полученные блоки, получившие название CO 2 Concrete, могут использоваться в тех же строительных приложениях, что и традиционные бетонные блоки, изготовленные с использованием OPC, и выходить на потенциальный глобальный рынок отходов CO 2 для цемента, бетона, асфальта и заполнителей, который был оценен неправительственной организацией Carbon180 в 1,3 миллиарда долларов.
«ЦМТ расположен на сухой вилочной станции бассейнового электроэнергетического кооператива, и во время 12 полевых испытаний более четырех тонн CO 2 было удалено из дымовых газов электростанции, образующихся при сжигании угля, для производства 200 тонн бетонных блоков, что соответствует примерно до 2% по массе поглощения CO 2 на блок », — сказал Джонс.
Полученные бетонные блоки соответствовали всем проектным спецификациям, включая достижение эффективности использования более 75% CO 2 , использование более 250 кг CO 2 за цикл и производство продукции, соответствующей спецификации прочности ASTM C90. более 14 мегапаскалей для конструкционных несущих бетонных блоков. Демонстрация ITC технологии бетона CO 2 также была признана финалистом конкурса NRG COSIA Carbon XPRIZE, который разрабатывает прорывные технологии для преобразования выбросов CO 2 в полезные продукты.
«Завершение этого успешного полевого тестирования подтверждает производительность и масштабируемость модульного процесса», — сказал Джонс. «Теперь технология готова к полевым испытаниям с другими источниками дымовых газов».
Следующими шагами проекта будет продолжение полевых испытаний системы в Национальном центре улавливания углерода (NCCC) в Уилсонвилле, штат Алабама, где в процессе карбонизации будут использоваться потоки дымовых газов от сжигания угля и природного газа. Дальнейшие испытания в NCCC нацелены на возможное усовершенствование конструкции системы; дальнейшая оптимизация производительности системы и потребления энергии; продемонстрировать надежность в отношении дымовых газов, материалов и условий окружающей среды; и использовать большой объем остатков сгорания угля (например,г., угольная зола) в блочной постановке. Технология UCLA коммерциализируется новым предприятием под названием CO 2 Concrete.
Национальная лаборатория энергетических технологий Министерства энергетики США (DOE) разрабатывает и коммерциализирует передовые технологии, которые обеспечивают надежные и доступные решения энергетических проблем Америки. Работа NETL поддерживает миссию Министерства энергетики США по укреплению национальной, экономической и энергетической безопасности США.
Знай свой бетонный блок: качество и практичность | by Construction Caribbean
В зависимости от потребностей вашего проекта и того, чего вы пытаетесь достичь, это небольшое разнообразие блоков может найти широкое применение.Как и любой другой инструмент, ключевое значение имеет то, как вы их используете.
Стандартный бетонный блок
Пустотелые бетонные блоки, пожалуй, самые популярные из сборных железобетонных материалов. Впервые изобретенные в 1890-х годах, они изначально были настолько тяжелыми, что их приходилось поднимать на место с помощью крана. В настоящее время они являются основным продуктом строительства, и их вес больше не является проблемой. Первоначально изготовленные вручную, человеку требовалось около часа, чтобы произвести 10 штук, по сравнению с технологией, которая у нас есть сегодня, когда машины производят до 2000 блоков 8x8x16 дюймов в час. Поскольку на отрасль растет давление, заставляющее строить здания быстрее и дешевле, качество становится все более важным фактором, поскольку оно имеет огромное значение, когда дело доходит до использования этих удобных строительных блоков. Каждый блок требует смешивания, формования, отверждения и изготовления кубов, причем на каждой стадии требуется постоянный мониторинг для контроля качества. Сырье следует взвешивать электронным способом, содержание воды в песке и гравии измерять с помощью ультразвуковых датчиков, а температуру воды контролировать с точностью до долей градуса.
Без этих строгих мер контроля, гарантирующих, что каждый блок имеет точное измерение и силу, проект может обернуться чрезвычайно дорогостоящей катастрофой. Разница в несколько миллиметров в одном блоке может показаться не такой уж большой проблемой, но умножьте это на тысячи, и вы можете столкнуться с гораздо большей проблемой.
Бетонные блоки в Ready Block Ltd., Лирс, Сент-Майкл, БарбадосOmnidec
Потребность в скорости в промышленности позволила технологиям развиваться, и теперь существует множество форм сборного железобетона, помимо традиционного бетона. block, и с каждым качество имеет решающее значение.Omnidec — это разновидность сборного железобетона, которая позволяет быстро и безопасно возводить большие площади полов и кровли. В каждой большой сборной плите используется треугольная решетчатая балка, прикрепленная к нижнему слою арматуры. Эта решетчатая балка изготовлена из высокопрочной стальной проволоки, чтобы обеспечить жесткую структуру внутри панели. Это позволяет ему легко связываться с бетоном, который заливается на месте.
Помимо скорости и безопасности, эта инновационная строительная технология имеет множество других преимуществ.
●. Структурная прочность: может быть спроектирована так, чтобы выдерживать большинство условий нагрузки и выдерживать жесткие воздействия, а также защищать от огня в течение длительных периодов времени.
●. Гибкость дизайна: можно получить уникальные, нестандартные и сложные формы.
●. Экономичное решение: поскольку Omnidec устраняет необходимость в фанере и боксе, это простой и очень экономичный способ подготовки подвесной плиты перекрытия. Что касается кровли, это позволяет оставить Soffit открытым, что позволяет сэкономить на дополнительных затратах на подвесные потолки.
Полы Omnidec от Ready Block Ltd., устанавливаемые на новом курорте Sandals Resort в Дувре, Барбадос.Interlocking Lego Concrete Blocks
Interlocking Lego Concrete Blocks — технологически продвинутый младший родственник стандартного бетонного блока. Эти игривые звучащие блоки, одна из новейших тенденций в производстве сборного железобетона, отличаются высокой прочностью и универсальностью. Несмотря на то, что они предлагаются в установленном размере, они предназначены для использования в ряде приложений.
Их можно легко использовать для подпорных стен, сегрегационных и силосных площадок, взрывных стен, бетонных зданий, складских бункеров и даже вывесок. В зависимости от проекта это может быть простой вариант штабелирования. Однако для тяжелых условий эксплуатации существуют типы, в которых предусмотрены каналы для армирования арматуры и цементного раствора.
Lego Blocks:
10 Узелковых блоков 2’x2’x5 ‘
8 Узелковых блоков 2’x2’x4′
6 Узелковых блоков 2’x2’x3 ‘
4 Узелковых блока 2’x2’x2′
2 Блок конкреций 2’x2’x1 ‘
Укупорочные блоки:
10 Укупорочные блоки 2’x2’x5′
8 Укупорочный блок 2’x2’x4 ‘
6 Укупорочный блок 2’x2’x3 ‘
4 Блок закрытия конкреций 2’x2’x2′
2 Блок закрытия конкреций 2’x2’x1 ‘
Блокирующие бетонные блоки Lego просты в установке, экологичны, повторно используются, экономичны и экологичныКак указано в названии предполагает, что их чрезвычайно легко собрать, а также транспортировать и при необходимости можно использовать повторно, что делает их экономически выгодным вложением.
Стандартный бетонный блок остается иконой в строительной отрасли, поскольку с годами он только приобрел ценность.
Комментариев нет