Производство керамзита бизнес: оборудование, технология изготовления, как делают
Назначение оборудования: Производство керамзита |
В состав линии входят: Транспортер SS 500 Смеситель двухосный JS 2400 Гранулятор Добавочный гранулятор Конвейер гранул Двуствольная вращающаяся печь спекания Склад угольной пыли Ковшовый погрузчик угля Система горячего шлифования Ковшовый элеватотр Дробилка Горелка Подъемник готовой продукции Сито готовой продукции Дымо- и пылеуловитель. |
Срок изготовления : 3 месяца |
В комплект не входит |
Энергетика: Около 121 кВт Двуствольная вращающаяся печь спекания — 30 кВт.Смеситель двухосный JS 2400 -15 кВт. Система горячего шлифования — 15 кВт. Гранулятор — 10 кВт |
Потребление тепловой энергии: 9000 к Кал/час |
Вес: Двуствольная вращающаяся печь спекания 28 т. Смеситель двухосный JS 2400 – 3 т. Система горячего шлифования 3,5 т. |
Габариты: (ш*в): Двуствольная вращающаяся печь спекания: 35000*500 мм. Смеситель двухосный JS 2400: 3500*500 мм. ![]() Система горячего шлифования: 4000*200 мм. |
Количество работников : 8 – 10 чел./смена |
Потребление воды: 15-25 м3/день |
Производственная площадь |
Проектная производительность за смену : 80 — 110 м3/день. 30000м3/год |
Параметры работы климат: Теплое время года |
Транспортировка: 7 40-футовых контейнеров |
Фото: Смеситель двухосныйГранулятор |
Характеристики продукции: На выходе получаем готовые шарики керамзита |
Сырье: Глина, бурый уголь. |
Бизнес по производству керамзита
Производство керамзита — бизнес, максимально привязанный к сырьевой базе. Керамзит представляет собой натуральный строительный материал, отличающийся прочностью, влагостойкостью, легкостью, длительным сроком эксплуатации, звуко- и теплоизоляционными свойствами.
Основным материалом для производства является глина, которая в различных точках месторождений существенно отличается от аналогов по составу и физическим свойствам. Для качественного производства необходимо подбирать легковспучиваемые глины. Производителям приходится использовать корректирующие консистенцию добавки в сырье: газообразующие и выгорающие.
Применение стройматериала
Область применения керамзита разнообразна:
- создание керамзитных конструкций;
- составление кладочных теплых растворов;
- наполнение бетонов;
- тепло и звукоизоляция всех поверхностей постройки;
- сооружение объектов инфраструктуры: мостов и дорог;
- утепление трубопроводов;
- фильтрация воды;
- цветоводство.
Необходимое технологическое оснащение
Для организации производства необходимо специальное оборудование. Главным элементом является печь. Обычно они выпускаются весом около 50 тонн. Меньшие печи считаются экономически невыгодным вариантом. Кроме основной печи необходим следующий набор оборудования:
- минитранспортер;
- смеситель;
- специальный гранулятор;
- конвейерная лента для гранул;
- погрузчик;
- элеватор для материала;
- система шлифования;
- установка для дробления;
- специальное сито для сортировки готовой продукции;
- горелка;
- уловитель для пыли.
Исходя из габаритов оборудования, на начальной стадии бизнеса необходимы крупные вложения для доставки и установки всех необходимых элементов производственной цепочки.
Процесс производства керамзита
Технологический процесс производства керамзита начинается с обжига гранул глиняного сырья с добавками измельченного угля или мелких остатков содержащих топливо шлаков. Процесс обжига проводится до спекания шихты. Уровень скорости процесса выгорания отходов и некоторого вспучивания массы влияет на степень пористости материала. После первоначального этапа керамзит охлаждается, причем от процесса охлаждения зависит прочность готовой продукции.
Стоимость готового материала будет зависеть от стоимости сырья, всех составляющих технологического процесса, затрат на оплату труда, амортизацию, налогов и страховых отчислений. Популярность материала обусловлена оптимальным соотношением качества и цены.
Только глина и заключенные
Под Горно-Алтайском после 20-летней консервации на базе местного завода ЖБИ заработал завод по производству керамзита. Для крайне небольшого рынка Сибири производство мощностью 50 тыс. кубометров за сезон — значительное событие. Опытная партия керамзита на заводе уже произведена. Однако в нормальном режиме он будет работать в весенне-осенний период, в течение семи месяцев, когда глина находится в «рабочем» состоянии.
Тем не менее предпосылки для его возобновления сохранялись. Дело в том, что локация производства керамзита практически полностью зависит от сырьевой базы. Керамзит на 100% состоит из легкоплавкой глины, и производить его необходимо непосредственно около месторождения, поскольку перевозить глину на значительные расстояния, понятно, невыгодно. Отсюда и достаточно узкие возможности для расположения производств: сейчас они работают под Красноярском, Томском, Кемерово и Омском. Все это были либо производства с «особым режимом», подобным алтайскому, либо подведомственные специализированным органам власти. Например, завод под Красноярском создавался для нужд закрытых городков Минатома.
Это тоже имеет свои причины. С одной стороны, керамзит — один из лучших теплоизоляционных материалов. С другой — добиться нормальной рентабельности на этом производстве можно только при значительных объемах. Поэтому большинство керамзитовых производств сохранилось в Центральной России (сейчас там сосредоточено 65% производства российского керамзита), а в Сибири, напротив, отрасль сжималась.
Тем не менее, местный предприниматель Виталий Мамышев
Но есть и обстоятельство иного рода. Дело в том, что у Мамышева получилось вновь восстановить «советскую экономику» производства, договорившись на привлечение к работам осужденных из исправительной колонии общего режима — всего до 40 человек (они и составят основной штат завода). «К настоящему времени они уже получили соответствующую квалификацию», — успокаивает мэрия.
Завод по производству кирпича и керамзита, г. Керчь, Крым
Россия, Крым, Керчь
Основная информация
- 0 aРасходы
- 0 aЗаемные средства
- 0 a Товарный остаток
- — Окупаемость
Объявление находится в архиве
Средства производства
Производство кирпича:
— линия формовки производительностью 1,2 млн. штук кирпича в месяц;
— 18 блоков тоннельных сушил;
— кольцевая печь на 18 камер производительностью 1,2 млн.штук кирпича в месяц.
Дополнительно возможен после ремонта запуск второй линии формовки с производительностью 1,0 млн.штук кирпича в месяц, 26 тоннельных сушил и кольцевой печи на 16 камер производительностью 1,0 млн.штук кирпича в месяц.
Керамзитовая установка по производству керамического пористого заполнителя. Возможен запуск производства керамзитового гравия на газе в объеме 50 тыс.куб.м в год, извести и сыпучих строительных смесей.
Собственная сырьевая база: месторождение суглинков, на которое оформлено спец.разрешение на пользование недрами.
Собственная артезианская скважина для производства кирпича.
Недвижимость (в собственности)
Завод «Сармат» основан в 1934 году. Полностью работающее производство. Располагается в стратегически перспективном городе Керчь в Крыму в близости от строительства моста через Керченский пролив.
Завод имеет удобные подъездные дороги, собственную ж/д ветку.
На территории завода имеется все необходимое для обеспечения производства: сырьевое месторождение, производственные комплексы, генераторы, административное здание с удобствами для персонала, парковка,ан площадь для отгрузки продукции автомобильным и ж/д транспортом.
На территории производства расположено восемь земельных участков общей площадью 6,14 га
- Площадь зданий 52393 кв.м.
- Площадь земли 52400 кв.м.
Сертификаты, лицензии
Спец.разрешение на пользование запасами суглинки.
Дополнительная информация
Кирпичный завод «Сармат» находится в г.Керчь в Крыму, вблизи от строительства моста через Керченский пролив. Стратегически привлекательный объект.
Объявление находится в архиве
Самара
Россия, Самарская обл.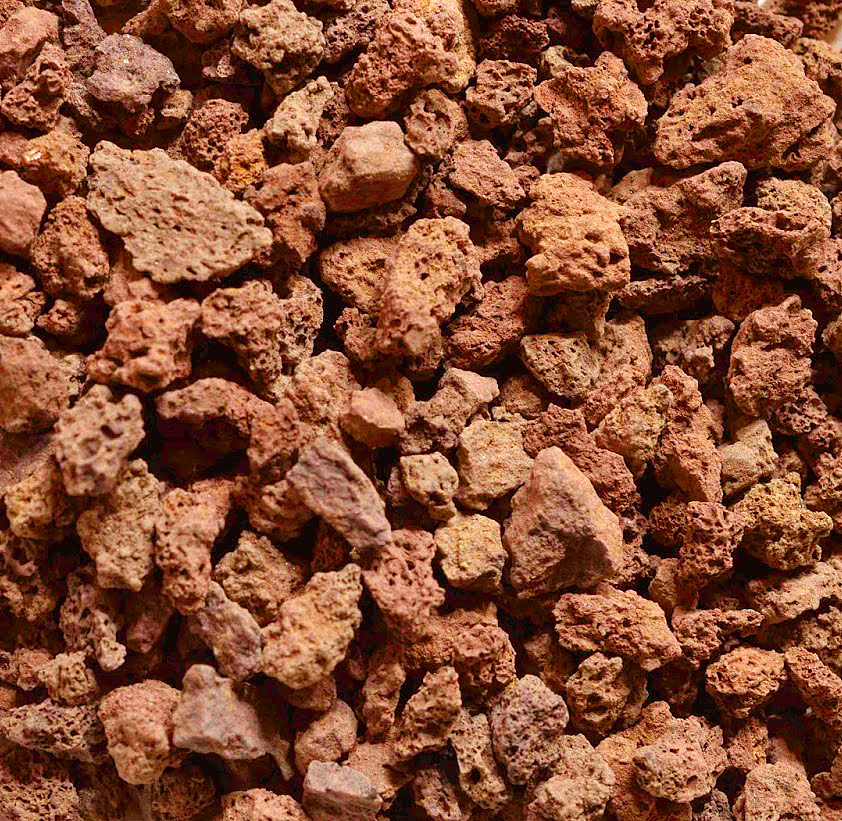
Анадырь (Чукотский АО)
Россия, Чукотский АО, Анадырь (Чукотский АО)Советский (Тюменская обл.)
Россия, Тюменская обл. и Ханты-Мансийский АО, Советский (Тюменская обл.)Ярославль
Россия, Ярославская обл., Ярославль Подать объявлениеПроизводство керамзита — свойства керамзита
Керамзит прочно занял свою нишу среди других строительных материалов, и лишь набирает популярность. Небольшая стоимость и универсальность дают возможность для постоянного расширения сфер применения керамзита. Это и строительство – в виде наполнителя для легких марок бетонов и бетонных блоков, в качестве тепло- и звукоизоляции как в строительстве различных зданий и сооружений, так и для утепления теплотрасс, как дренаж в садоводстве, как декоративный материал для садовых дорожек и украшение в ландшафтном дизайне, даже в аквариумистике.
Это обусловлено свойствами, которыми обладает керамзит:
- доступная стоимость;
- низкая теплопроводность;
- малый вес, не создающий нагрузок на несущие части зданий;
- пожаробезопасность;
- устойчивость к гниению, микроорганизмам;
- морозоустойчивость;
- низкая впитываемость влаги.
При таком широком спектре положительных свойств спрос на керамзит постоянно растет, а учитывая то, что производство его не такое уж и сложное, то цена остается постоянно доступной.
Исходным материалом для керамзита являются глинистые породы, включающие в себя как глинистую основу, так и различные натуральные органические и минеральные примеси, например, кварц, полевой шпат.
Свою форму и свойства керамзита исходное сырье получает в процессе обжига в медленно вращающейся наклонной печи, где происходит вспучивание подготовленного материала, получение пористой внутренней структуры и крепкого внешнего слоя.
Готовый полуфабрикат обязательно охлаждается (температура в печах для обжига 800 – 900 градусов), при помощи цилиндрических грохотов сортируется на фракции (песок, щебень, гравий) и отправляется на склад готовой продукции или прямо к потребителю. Следует заметить, что цикл производства одной партии (ее объемы зависят от размеров печи) сравнительно мал по времени, и в большинстве своем занимает до 45 минут. Благодаря этому производство керамзита – бизнес прибыльный и быстро окупающийся.
Похожие материалы:
Кемеровский завод «Керамзит». Глина и «попкорн»
А что это мы всё про уголь да про уголь? Земля наша богата и обильна… В общем, сегодня мы решили обратиться к теме работы с нерудными материалами, в частности, с глиной. Для этого мы отправились на производственную площадку кемеровского завода «Керамзит», где увидели знакомое оборудование и несколько подробно описанных нами ранее технологий, однако в новом амплуа.
Нам помогал
Денис Вертилецкий,
главный механик завода «Керамзит»
Больше полувека назад в разных городах Страны Советов появлялись заводы, где производили лёгкий, нетоксичный и негорючий теплоизоляционный материал — керамзит. Тогда учёные обошли земли в поисках главного компонента — специфической глины и глинистого сланца.
Рядом с месторождениями и возникали заводы.
Правда, сегодня далеко не все предприятия этого профиля остались на рынке, но кемеровский «Керамзит» — один из успешных долгожителей: он работает с 1963 года. Кузбасский керамзит сегодня производят только здесь.
Особый карьер
«Керамзит» не только производит теплоизоляционный материал, но и самостоятельно добывает сырьё для него. Так что первым делом мы привычно отправляемся на карьер. От завода до места добычи — всего несколько минут на машине, и такое небольшое транспортное плечо — одна из составляющих продуктивной работы предприятия.
Глинистые почвы сразу выдаёт разросшаяся здесь дикая облепиха.
Признаться, таких карьеров нам видеть ещё не доводилось: он по-настоящему миниатюрный — несколько метров по длине и ширине и чуть более человеческого роста в глубину. Такие особенности объясняются технологией работы и спецификой залегания глины.
«Глина залегает на небольшой глубине. Сейчас мы работаем с карьерами глубиной 2,5–3 м. Конечно, экскавационных работ немного, и это плюс.
Но на такой глубине карьер промерзает, поэтому добыча в зимнее время становится невозможной. Даже при глубине залегания в 5 м можно продолжать работы, а тут приходится останавливаться. Поэтому мы активно производим керамзит в тёплое время года, а зимой консервируем оборудование, проводим текущие ремонты», — рассказывает главный механик завода «Керамзит» Денис Вертилецкий.
Ну а небольшой периметр карьера объясняется деликатной технологией добычи, которая здесь практикуется.
«Сначала мы срезаем плодородную почву — получаются гурты, которые вы здесь можете видеть. Почву мы осторожно сохраняем, потому что при рекультивации нам нужно будет восстановить земли таким образом, чтобы они были пригодны для сельского хозяйства.
Так что верхнюю часть суглинка мы сдвигаем и забираем только ту глину, которая нужна нам в производстве. Бывает, встречается запесоченная глина — она нам не подходит, мы её оставляем в карьере.
Мы стараемся делать небольшие карьеры, чтобы можно было оперативно проводить рекультивацию.
То есть мы добыли глину и сразу же восстановили этот участок — чтобы земли не простаивали и на них могли работать фермеры», — объясняет наш провожатый.
С такими работами справляется небольшой гусеничный экскаватор Volvo и самосвал КАМАЗ. Добытую глину сразу же отправляют на предприятие, однако на производство она пойдёт не скоро. Сырьё обязательно должно вылежаться — от месяца до трёх. За это время глина обогащается кислородом, становится более рыхлой и однородной.
Превращения глины
Особенная глина, используемая в производстве керамзита, обладает ключевым свойством: она вспучивается при обжиге — на манер попкорна. Именно поэтому специалисты кемеровского завода упомянули, что оставляют в карьере запесоченную глину: кварц при обжиге плавится. Важнейший элемент керамзитовых глин — оксид железа. Специалисты предприятия рассказали, что на предприятиях в других городах они видели и чёрную глину — своим цветом она обязана углероду и железу в составе. И вспучиваемость этой глины была очень высокой.
Два других принципиальных свойства глины тесно связаны с первым. Это легкоплавкость — иначе образующиеся при обжиге газы свободно выйдут, не вспучив материал, а также необходимый интервал вспучивания.
«Для контроля сырья и готовой продукции мы работаем с лабораторией. Глину проверяем на пригодность для производства, а также она проходит гамма-спектрометры. Это обязательное условие при создании любых строительных материалов, поскольку сырьё, добытое из земли, может содержать в себе радионуклиды. У нашей продукции — наименьшие показатели по России, и керамзит соответствует классу А. Также в лаборатории мы контролируем свойства готовой продукции — прочностные характеристики и гранулометрический состав», — комментирует Денис Вертилецкий.
Поехали!
Прибыв с карьера, глина через несколько недель начинает своё превращение в керамзит. В этом теплоизоляционном материале только два компонента — глина и опилки. Причём последние необходимы для более активного вспучивания, а в процессе производства они выгорают.
Для начала необходимо смешать ингредиенты.
Чем тщательнее организован этот процесс, тем лучше продукт на выходе.
Напоминает он замешивание теста — только масштабы побольше. Может быть, поэтому это женская работа.
Правда, аппарат у специалиста совсем недевичий и не кухонный — грейферный кран.
Ковш захватывает смесь глины с опилками, поднимает на небольшую высоту и высыпает обратно. Таким образом, сырьё становится однородным и уже в таком виде отправляется в бункер, который находится ниже уровня земли. В барабане крупные куски разламываются, после чего глина попадает на ленточный конвейер.
Спустившись, мы наблюдаем, как кусочки глины с опилками поднимаются по ленте. Выше стоит контролёр, который проверяет, чтобы на ленту не попали крупные камни, а также следит за корректностью работы оборудования. В случае чего именно он первым сигнализирует о неисправности.
«Все элементы конвейерной системы у нас работают подолгу. Даже те части, которые считаются расходниками, ходят по нескольку лет.
Если транспортёрную ленту эксплуатируют правильно и она ни за что не цепляется и не рвётся, то этот элемент работает по 5–8 лет. Та, которая у нас установлена сейчас, в ходу уже 8 лет.
Ленты мы заказываем у местного кемеровского производителя. Срок службы роликов — обычно 3–4 года. Их меняем по мере поломки: если конкретный ролик заклинил, убираем только его. Ролики тоже заказываем в Кузбассе — в Ленинске-Кузнецком производят оборудование для шахт», — говорит наш провожатый.
На заводе вообще всё или почти всё оборудование — отечественное. Часть элементов системы, как уже упоминалось, изначально ориентировано на работу в шахтах, а что касается специализированных систем, то здесь наши производители имеют отличную базу. В Самаре работает единственный в мире научно-исследовательский институт по керамзиту ЗАО «НИИКерамзит», и все заводы России и даже стран СНГ спроектированы здесь.
Печь — главное оборудование керамзитового завода — произведена на заводе «Строммашина», а обслуживают её специалисты из Топков: город известен «Топкинским цементом», и керамзитовая печь чем-то похожа на вращающиеся печи цементных заводов. Пройдя формовочные вальцы и сушильный барабан, сформированные из глины шарики поступают именно сюда. При высокой температуре (порядка 1100–1300 градусов) глина вспучивается и превращается в керамзит.
Теперь его осталось только выгрузить и остудить. Если материал будет постепенно остывать в естественных условиях, он потеряет прочность. Поэтому керамзит отправляется в специальный холодильник.
Это, между прочим, уникальное и в каком-то смысле экспериментальное оборудование: кемеровский завод очень компактный, поэтому холодильник ему понадобился необычно маленький.
Такой агрегат создали на Кемеровском опытно-ремонтном механическом заводе, а собрали его специалисты завода «Керамзит» самостоятельно.
Четыре фракции
Керамзит создан, однако к отправке потребителю ещё не готов. Предварительно его необходимо разделить на фракции, поскольку каждая из них находит собственное применение. Для разделения используют хорошо известное нам оборудование — грохот.
Процесс начинается на высоте: керамзит поднимается наверх с помощью ковшей, мы же отправляемся по лестнице — к месту старта ведёт 101 ступенька.
По дороге Денис Вертилецкий рассказывает нам о применении четырёх фракций керамзита, на которые разделяется покинувший холодильник материал.
«Самая маленькая фракция — 0–5 мм. Такой керамзит используют для создания сухой стяжки тёплого пола. Эту фракцию ещё называют «тёплый песок».
Фракция 5–10 мм идёт на производство товарного бетона, железобетона, керамзитоблоков. Стяжку из него тоже делают, потому как керамзит может сохранять температуру до трёх суток.
Фракцию 10–20 мм в основном используют строители для утепления чердачных перекрытий и плоских кровель.
Самая крупная фракция — 20–40 мм — идёт на утепление погребов, а также подземных складов, в частности складов нефтепродуктов», — комментирует наш собеседник.
Раньше, рассказывает специалист, на керамзитовых заводах использовали ещё и дробилки: самая крупная фракция 20–40 не была востребована, поэтому материал измельчали.
Делать это нежелательно: при дроблении происходит потеря объёма, керамзит становится менее прочным, поскольку разрушается его «скорлупа».
Сегодня от дробления ушли, но фракции 5–20 по-прежнему самые востребованные.
Поднявшись наверх, мы видим самое первое сито грохота — сетку из толстой стальной проволоки. Чем ниже, тем тоньше становится эта самая проволока и тем меньше ячейки сита.
Как и многие другие материалы, проходящие через грохот, керамзит, обладающий абразивными свойствами, истирает сита, поэтому верхнее и сделано максимально прочным.
Рядом с грохотом мы видим старые сита иной конструкции — с круглыми перфорированными отверстиями. Их использовали раньше, однако плетёные решения показатели себя как более эффективные.
«Прежде мы использовали другое оборудование для рассева. Это была труба с вот такими перфорированными ситами. Но для керамзита лучшее сито — это сетка, потому как материал представляет собой шарики неидеальной формы. По ГОСТу фракция менее 5 мм должна занимать не более 10%, а при работе с перфорированными ситами отходов получалось намного больше», — объясняет Денис Вертилецкий.
И грохот, и сита к нему «Керамзит» приобретает у челябинского производителя.
На выходе с грохота керамзит распределяется по четырём банкам, соответствующим четырём фракциям. Осталось только расфасовать продукт в тару разного объёма, и он готов к отправке на стройплощадки. Ну или в питомники, или сельскохозяйственные предприятия, ведь керамзит активно используется ещё и как дренажный материал.
На производстве побывали: Анна Кучумова (текст),
Евгений Ошкин (фото)
| |||||
| |||||
| |||||
Вращающиеся печи для производства керамзитового агрегата
Керамзитовый заполнитель, также называемый экслай, или легкий заполнитель керамзита (LECA), является полезным материалом во все большем числе отраслей промышленности, в первую очередь в строительстве и садоводстве. Следующими на очереди, вероятно, будут приложения для очистки воды и фильтрации.
Уникальная структура и физические свойства керамзита, которые можно использовать в различных областях, производятся в результате тщательно контролируемой термической обработки (обычно называемой прокаливанием или спеканием), проводимой во вращающейся печи.
Термическая обработка керамзитового заполнителя (прокаливание или спекание)
Свойства керамзита, которые делают его идеальным для использования в определенных областях, достигаются благодаря высокотехнологичному производственному процессу.
Глины обычно измельчают, агломерируют и / или сушат в качестве средства подготовки сырья, хотя этот процесс может варьироваться. Экструзия кажется предпочтительным методом агломерации в этих условиях, но можно также изучить другие методы.
В то время как подготовка сырья имеет важное значение при производстве заполнителей керамзита, ключевым процессом, лежащим в основе заполнителей керамзита, является термическая обработка.От этой термической обработки произошло название керамзитового заполнителя, поскольку он используется для физического расширения частиц глины.
Для описания таких методов термической обработки используются различные термины. В этом случае обработка обычно называется прокаливанием или спеканием. Хотя эти два термина часто используются как синонимы, важно отметить, что технически они относятся к разным методам. Поскольку спекание технически происходит при гораздо более высоких температурах, для целей этой статьи мы будем называть его прокаливанием, хотя в некоторых случаях расширенные агрегаты могут быть действительно спеченными.
В случае керамзита прокаливание играет важную роль в создании продукта, который может служить заполнителем керамзита. Температура, обычно от 1050 ° C до 1250 ° C, вызывает выделение газов в результате различных изменений в материале, включая разложение и восстановление оксидов трехвалентного железа, горение органических веществ, продувку захваченной воды и разложение карбонаты . ³
Это выделение газов вызывает физическое расширение или вздутие глины, в результате чего она имеет более низкую плотность, более высокую пористость и гораздо большую площадь поверхности внутри материала, а также более твердую поверхность — все характеристики, которые делают ее идеальной для использования. как легкий заполнитель.
Факторы, влияющие на расширение глины при прокаливании
Как и в случае с большинством материалов, для достижения наилучших результатов в производственном процессе необходимо оптимизировать различные факторы. Обширное исследование, проведенное на трех различных источниках глины, показало, что, хотя ряд факторов важен, параметры процесса расширения, которые, возможно, являются наиболее важными, включают: 4
Температура обработки
Температура обработки является наиболее важным фактором в процессе расширения.Было обнаружено, что расширение увеличивается вместе с температурой, чуть ниже температуры плавления конкретной глины (температура плавления варьируется в зависимости от типа глины).
Размер зерна глины
Исследование показало, что размер зерна глины также является определяющим фактором, причем расширение увеличивается по мере уменьшения размера зерна.
Размер пеллет
Размер гранул или агломератов также оказывает влияние на расширение, причем расширение увеличивается вместе с размером гранул.Следовательно, уменьшение размера гранул коррелирует с меньшим расширением.
Время удерживания
Было обнаружено, что оптимальное время удерживания зависит от типа обрабатываемой глины. Оптимальное время удерживания было важным, поскольку наблюдались последствия как несоответствующего, так и чрезмерного времени.
Вращающаяся печь
Предпочтительным оборудованием для проведения процесса расширения глины является вращающаяся печь.
Вращающиеся печи доступны в конфигурации с прямым или косвенным нагревом и часто называются декарбонизаторами. Производство керамзита обычно осуществляется в печи с прямым нагревом, в которой глина и продукты сгорания находятся в прямом контакте друг с другом.
с прямым нагревом можно настроить для прямоточного или противоточного воздушного потока, но противоток, как правило, является более эффективной настройкой процесса при этой настройке.
3D Модель вращающейся печи с прямым обогревом
Почему глина как легкий заполнитель
Как и многие легкие заполнители (LWA), использование вспученных глин может обеспечить широкий спектр как экономических, так и экологических преимуществ:
Экономическая выгода
Использование легких заполнителей предлагает множество экономических стимулов, в том числе:
- Снижение затрат на конструкции в строительстве
- Снижение транспортных расходов
- Снижение затрат и уменьшение зависимости от импорта, где это применимо
Экологические преимущества
По данным Европейской ассоциации керамзитовой глины (EXCA), керамзит является экологически чистым материалом с рядом экологических преимуществ:
- Снижение выбросов CO 2 при использовании в качестве замены ископаемого топлива
- Снижение выбросов CO 2 в строительстве и на транспорте
- Повышение энергоэффективности зданий
- Возможность 100% вторичной переработки
- Химически инертен (без вредных компонентов и, следовательно, без возможности выделения ЛОС или вымывания загрязняющих веществ
- Преимущества фильтрации воды и воздуха
- Высокое соотношение продукта к сырью (из одного кубометра глины можно получить пять кубометров керамзита)
Кроме того, возможность заключается в использовании восстановленных или переработанных глиняных материалов, что еще больше повышает экологичность этого материала.
Использование LECA
В то время как области применения легкого керамзитового заполнителя (LECA) продолжают расти, в настоящее время существует два основных направления для продуктов LECA:
Строительство
Строительство — это наиболее распространенное приложение для LECA. Керамзит можно найти во всех видах бетона, наполнителя и конструкционных элементов в строительстве и промышленности строительных материалов. Преимущества, которые он может предложить в этой настройке, включают: ²
- Высокая износостойкость при минимальных затратах на обслуживание и долгий срок службы
- Прочность и устойчивость
- Полностью негорючие (огнестойкие)
- Возможность 100% вторичной переработки снижает проблемы утилизации
- Легкий вес без ущерба для прочности
- Служит теплоизолятором
- Обеспечивает снижение шума
- Обеспечивает отвод воды
- Нетоксичный
Садоводство
Использование LECA в садоводстве — сравнительно новое применение, но все еще развивающаяся область.Керамзитовые наполнители могут принести множество преимуществ при различных условиях выращивания. Сюда входят:
¹- Улучшенная аэрация (особенно при использовании в качестве субстрата при выращивании в коммерческих контейнерах) и пониженное уплотнение
- Способность к увеличению содержания воды и питательных веществ
- Повышенная катионообменная емкость
- Устойчивость к разрушению со временем
- Возможно использование в качестве барьера от сорняков
Помимо строительства и садоводства, LECA также изучается на предмет использования в системах очистки и фильтрации воды.
Испытания: залог успеха с керамзитом
Как и во многих случаях термической обработки, испытания являются критическим элементом успешной операции расширения глины. Исследования показали, что идеальные параметры процесса уникальны для типа обрабатываемой глины.
Тестирование образцов глины в серийном масштабе для сбора исходных данных процесса является первым шагом в успешной программе тестирования. Данные, собранные во время пакетного тестирования, затем можно использовать для масштабирования тестирования до непрерывных пилотных запусков. Испытания также могут быть использованы для поиска баланса между идеальными параметрами процесса и тем, что является экономически целесообразным.
Инновационный центр FEECO предлагает различные испытательные печи для проведения как периодических, так и пилотных испытаний. Печи могут быть оснащены различным вспомогательным оборудованием для моделирования различных условий коммерческой эксплуатации.
Испытания различных методов агломерации также могут быть объединены для получения идеальных характеристик гранул для рассматриваемого уникального источника глины.
Печь периодического действия, использованная для испытаний в инновационном центре FEECO
Система автоматизации инновационного центра собирает широкий спектр данных, которые можно отслеживать и анализировать в режиме реального времени для непревзойденной прозрачности процесса. Сюда входят точки данных, такие как скорость подачи и продукта, соответствующие показания температуры, давления в системе, отбор проб и анализ газа и многое другое.
Заключение
Керамзитовый керамзит — полезный материал в строительной индустрии, находит применение в садоводстве и водоочистке.Вращающиеся печи — это предпочтительное устройство для переработки глиняных агломератов в керамзит.
Способность оптимизировать параметры процесса для производства керамзита высшего качества имеет решающее значение для успеха операции. FEECO предлагает обширные возможности тестирования для тех, кто находится на этапах процесса и разработки продукта. Затем мы используем данные, собранные в ходе испытаний, для проектирования и производства на заказ коммерческих вращающихся печей высочайшего качества. Для получения дополнительной информации о наших возможностях в отношении керамзитовых заполнителей свяжитесь с нами сегодня!
Линия по производству легкого вспененного глиняного агрегата (LECA)
Что такое легкий керамзитовый заполнитель (LECA)?
Определение : свет
заполнитель керамзита или заполнитель керамзита (LECA или ECA), также называемый керамическим
окатыши — один из самых популярных легких заполнителей, получаемых путем спекания глины. во вращающейся печи примерно до 1200 ° C.
Вращающаяся печь для спекания глины
Сырье и применение : существуют различные типы легкого керамзитового заполнителя, и основными материалами являются глина, сланец, сланец, угольный порошок, хвосты и т. д.
LECA в основном применяется в строительстве, внутренняя отделка, сельское хозяйство, садоводство, садоводство, детская площадка, гидропоника, и Т. Д.
Оценка (мм) | Плотность (кг / м 3 ) | Приложения |
0-4 | ≤710 | Легкий бетон, легкий кирпич, сборная плита, легкая плитка, система очистки воды, сельское хозяйство |
4-10 | ≤480 | Легкий бетон, легкая плитка, сборные конструкции плита, аквакультура, шумозащитный барьер |
10-20 | ≤380 | Легкий бетон, канализация, садоводство, дренажная система |
0-25 | ≤430 | Отделка пола, светлая набивка, дорога строительство, аквакультура |
Перспектива разработки керамзита легкого керамзита
Современный легкий керамзитовый заполнитель рыночные данные показывают, что рынок LECA изменил свое направление с традиционная строительная техника для изготовления изделий и садоводства поддержание.
Перспектива развития LECA
Материалы для производства из традиционных материалов такие как глина и сланец были заменены остатками промышленных отходов и илом и тенденция развития машин превратилась в крупномасштабные и автоматизация.
В связи с тенденцией глобализации защиты окружающей среды,
ресурсосберегающая экономика и устойчивая промышленность будут активно
продвигаются в разных странах и регионах.
В будущем, сосредоточив внимание на экономического развития, поставщики LECA должны обратить внимание на сокращение загрязнение и растрата ресурсов для обеспечения быстрого и стабильного развития производственные линии.
Технологии производства LECA
Обычно существует два типа LECA. Технология изготовления: спекание и спекание-вспучивание. Разница между ними находится в процессе спекания-расширяется, агрегат расширяется на больший объем.
Производительность LECA при спекании
Агломерационная машина для процесса спекания LECA
- Прочность на сжатие : на сжатие прочность агломерата относительно высокая, достигая 3,0-7,0 МПа, а прочность на сжатие высокоспеченных агрегатов может достигать 25-40 МПа.
- Density : плотность спеченного заполнитель крупнее, обычно больше 600 кг / м3, даже некоторые из которых более 900 кг / м3.
- Водопоглощение : водопоглощение обычного спеченного заполнителя немного выше, чем у спеченного вспененного материала. продукт, а высокопрочные изделия аналогичны спеченному вспененному продукту.
- Устойчивость к карбонизации : спеченный заполнитель обладает высокой устойчивостью к карбонизации, поэтому его прочность на сжатие не уменьшится даже под действием углекислого газа.
Характеристики LECA при спекании-расширении
Вращающаяся печь для агломерационного процесса LECA
- Прочность на сжатие : на сжатие прочность агломерированного вспененного заполнителя обычно ниже 2,0 МПа, поэтому он в основном используется для внутренней отделки, такой как шумоизоляция и садоводство.
- Теплоизоляционные характеристики : спеченный-вспененный
продукт имеет закрытую микропористую структуру с очень высокой пористостью, что обычно
составляет 48% -70% от общего объема агрегата, что дает только 0.
08-0,15 Вт /(m.k) теплопроводности.
- Низкая плотность : в слое много пор спеченно-вспененный материал, поэтому плотность преимущественно 300-500 кг / м 3 , что составляет лишь половину от спеченного заполнителя. Однако у него есть значительное преимущество в легкой производительности, поэтому его также можно использовать для различных декоративная промышленность и строительство с более низкими требованиями к плотности в строительстве материалы.
- Превосходное звукопоглощение и изоляция : среди всех видов агрегатов звукопоглощающие и изоляционные характеристики из спеченно-вспененного заполнителя является наиболее выдающимся.
Когда звук проходит через материал, большое количество звуковых волн поглощается его порами, что уменьшает распространение звука.
Для разных процессов требуется разное оборудование. Агломерационная машина обычно используется в процессе спекания, в то время как роторная Печь используется в процессе спекания с расширением.
По сравнению с агломашиной роторный печь более эффективна и экологична, поэтому предпочтительное оборудование для поставщиков LECA.
Производственная линия LECA и основные машины
Производство LECA в целом требует семи шагов: дробление, смешивание, измельчение, гранулирование, спекание, охлаждение и просеивание.
Производственная линия LECA
Основное оборудование на производстве LECA Линия включает в себя щековую дробильную машину, смесительную машину, шаровую мельницу, гранулятор, роторная сушилка, троммельный экран, вращающаяся печь, охлаждающая машина.
Щековая дробилка — первичное дробление
Щековая дробилка — это основная машина, которая применяется для крупного, среднего и тонкого измельчения различных руд и горных пород с комплексная прочность от 147 до 245 МПа и превращает их в небольшие куски 10-350 мм.
Зубодробилка, мордоворот
Преимущества : В последние годы FTM
специально разработанная мощная щековая дробилка для нужд дробления
высокопрочный и высокотвердый микроуглеродистый феррохром в металлургии,
горнодобывающая, строительная и другие отрасли промышленности.
Шаровая мельница — дальнейшее измельчение
Шаровая мельница — ключевое оборудование для измельчения материал после измельчения. Шаровая мельница широко используется в производстве цемента, силикатные изделия, новые строительные материалы, огнеупорные материалы, удобрения, шлифовка черных и цветных металлов и стеклокерамика, сухое или мокрое шлифование различных руд и других измельчаемых материалов.
Шаровая мельница
Преимущества : Энергосбережение, гибкий дизайн разгрузочной части, большой порт подачи, высокая эффективность измельчения, хорошая качество футеровки и закрытая система для уменьшения запыленности.
Дисковая грануляционная машина — контроль размера частиц
Диск — это ключевая машина, определяющая частицы керамзитового заполнителя.
Диск гранулирования имеет общую круглую форму. структура дуги, а степень грануляции может достигать 93% и более. Гранулирование лоток имеет три выпускных отверстия, которые облегчают прерывистое производство операций, значительно снижая трудоемкость и повышая эффективность труда.
Дисковая грануляционная машина
Преимущества : Высокая скорость образования шариков, большие округлая прочность частиц, интуитивное управление и простота обслуживания.
Сушилка — удаление воды из LECA
Сушилка в основном используется для сушки определенных влажность или крупность материалов переработки минерального сырья, строительных материалов, металлургия и химическая промышленность, а работа оборудования проста и надежный.
Сушилка
Adv anta ges : длительный срок службы деталей, износостойкость,
высокая прочность на сушку, высокая эффективность, простота в эксплуатации, экологичность
защита и энергосбережение, усовершенствованная структура и сильная сушильная способность.
Барабанный грохот — разделение неквалифицированных LECA
Барабанный сетчатый фильтр часто используется для измельчения порошкообразных материалов, который имеет хороший просеивающий эффект и стабильную работу и он производит низкий уровень шума во время рабочего процесса.
Барабанный экран
Преимущества : Оборудование имеет диапазон применения, а также его можно настроить. Имеет низкий уровень шума, высокий эффективность и защита окружающей среды, усовершенствованная система смазки, долгая срок службы, малый угол наклона установки и хороший экранирующий эффект.
Вращающаяся печь — спекание LECA
Вращающаяся печь — самая необходимая машина и играет важную роль в процессе спекания, что определяет производительность LECA.
Вращающаяся печь
Преимущества : Осевое перемещение цилиндр регулируемый, скорость гибкая, установка и обслуживание удобное, а герметичность хорошая.
Кулер — быстрое охлаждение LECA
Одноцилиндровый охладитель является одним из важное оборудование в системе вращающейся печи. Клинкер из вращающейся печи (1000-1200 ° C) полностью обменивается с воздухом через вращающийся цилиндр. лента для охлаждения материала до температуры ниже 200 ° C, в то же время улучшения клинкера качество и шлифуемость.
Кулер
Преимущества : Высокая тепловая эффективность, высокая качество клинкера, быстрое охлаждение и повышенная производительность.
Спецификация производственной линии LECA (для только для справки)
- 01 тип : 0,45-0,9 мм (20-40 меш) Высокая прочность при средней плотности
- 02 тип : 0,9-1,25 мм (16-20 меш) Высокая прочность при средней плотности
- 03 тип : 1.0-1,70 мм (12-18 меш) Высокая прочность при средней плотности
- 04 тип : 0,224-0,65 мм (40-60 меш) Высокая прочность при средней плотности
Производитель оборудования LECA рекомендовано — FTM
Fote Mining Machinery (FTM), расположенная в
Хэнань — один из самых известных поставщиков горнодобывающего оборудования, который стремится
для производства горнодобывающих машин из экологически чистых строительных материалов и обеспечивает
интеллектуальные продукты для горнодобывающей промышленности и передовые решения.
Обладая более чем 30-летним опытом, FTM добился замечательных результатов в производственной линии LECA за счет непрерывного разведка и исследования.
FTM — профессиональный поставщик машины и оборудование для легкого керамзитового заполнителя, а также все оборудование имеет высокое качество и весомые преимущества, а также очень разумные цены.
Одним словом, Fote Mining Machinery — хороший выбор поставщиков LECA при выборе легкого керамзитового заполнителя производители оборудования.Добро пожаловать, чтобы проконсультироваться с нами, если у вас есть какие-либо требования о производственной линии LECA.
Превращение глины в строительный материал — это тяжелая работа.
Каждый день конвейерная лента перемещает около 1000 тонн необработанной глины из глиняного карьера Leca в Дании на завод компании в Хинге. Здесь влажное сырье подвергается жесткой обработке, которая в конечном итоге превратит глину в широко известные коричневые шары Leca ® и другие продукты Leca ® .
«Конвейерная лента транспортирует сырую глину в большие вращающиеся печи. Попутно глина проходит несколько процедур формования, так что в конечном итоге сгустки оказываются между размером руки и большим валуном. Это чрезвычайно тяжелая отрасль, в которой, помимо прочего, используются электродвигатели, редукторы и муфты », — объясняет менеджер по техническому обслуживанию Тонни Хедеванг.
Обжиговые печи выключают только два раза в год
Температура во вращающихся печах составляет около 1200 градусов Цельсия.Тепло высвобождает тысячи маленьких пузырьков газа, которые задерживаются в глине и придают материалу характерную легкость, когда глина превращается в шарики за счет кругового движения печи. Остановка и запуск печей — чрезвычайно дорогостоящая операция, поэтому Leca Denmark уделяет особое внимание предотвращению сбоев в производственном процессе.
«Мы закрываем печи только на Рождество и на летние каникулы, чтобы провести регулярное техническое обслуживание. В остальное время их нужно постоянно кормить.Механизмы и двигатели очень тяжело работают, поэтому нам нужно иметь надежное оборудование. Продукты и оборудование низкого качества и с коротким сроком службы просто не подходят », — объясняет Тонни.
Тесный контакт с Хойером
Из-за того, что компания уделяет особое внимание эксплуатационной надежности и быстрому обслуживанию, Leca Дания поддерживает тесные контакты со своими поставщиками, включая Hoyer, которые поставляют электродвигатели, шестерни и другие детали трансмиссии.
«Мы не можем быть экспертами во всем, поэтому очень приятно знать, что Хойер знает фабрику и наше оборудование и может быстро отреагировать в случае возникновения проблем.Например, несколько месяцев назад у нас возникли проблемы с некоторыми муфтами. Что ж, вышло наше постоянное контактное лицо из Хойера, которое осмотрело детали и быстро нашло решение », — вспоминает Тонни.
Факты о Leca Дания
Leca Дания является частью международного концерна Saint-Gobain
Завод в городе Хинге отвечает за производство всей продукции Leca ® в Дании.
Первые продукты Leca ® были разработаны в Дании в 1939 году.
Leca ® используется в качестве изоляционного строительного материала и легкого строительного наполнителя, используемого в зданиях, на дорогах, мостовых пандусах, велосипедных дорожках и портовых сооружениях.
Производство— Сталит
Сырье, добываемое на STALITE , представляет собой аргиллитовый сланец, расположенный в геологической зоне, известной как формация Тиллери. Представляет собой тонкослоистый алевролит серого мелкозернистого цвета, сложенный обломками (выносом) горных пород.Формация Tillery — сложная система, которую необходимо выборочно добывать, чтобы отделить желаемый продукт от нежелательного для производства высококачественного заполнителя из вспученного сланца.
Геологическая история формации Тиллери началась 550 миллионов лет назад в кембрийский период, примерно за 330 миллионов лет до появления динозавров. Обломки горных пород вулканического происхождения были отложены в водной среде (седиментация), а затем затвердели в твердую породу (литификация).Последующее захоронение и тектоническое давление затем изменили (метаморфизовали) породу в аргиллитовый сланец. Наряду с отложением вулканического пепла в тот же бассейн отложений время от времени происходил поток пепла (обломков) или гравитационный поток грязевого типа. Внутри системы образовались дополнительные слои, состоящие из вулканического туфа с высоким содержанием кальцита. Последующие миллионы лет геологических сил заставили чередующиеся слои материала складываться и разламываться, вызывая беспорядок в некогда упорядоченной слоистой системе.Наряду с этим беспорядком возникли интрузии пород диабазовых даек триасово-юрского возраста (около 180–220 миллионов лет назад), которые привели к появлению дополнительных вертикальных структур горных пород, которые еще больше усложнили систему.
Известковый туф препятствует процессу вздутия при производстве легких заполнителей. При температуре 2000 градусов по Фаренгейту (1000 градусов Цельсия) кальцит просто кальцинируется. При высоких температурах, превышающих 2200 градусов по Фаренгейту (1200 градусов Цельсия), диабазовая порода (удельный вес 3,0) плавится до стекловидного типа без изменения удельного веса.Поскольку такой высокий удельный вес создает хаос на желаемом легком материале с удельным весом, его следует полностью избегать. Единственный способ избежать этого материала — это выборочная добыча. Обширное колонковое бурение должно выполняться вместе с микроскопическими, химическими и лабораторными испытаниями вздутия керна, чтобы «нанести на карту» подземный материал и идентифицировать желательный и нежелательный агрегаты. Затем необходимо использовать компьютерное программное обеспечение для определения высококачественных разрезов желательных и нежелательных зон горных пород.Затем можно использовать программное обеспечение для горных работ для разработки последовательности выборочных горных работ. Современная установка фракционирования с управляемыми радиальными штабелеукладчиками и системами подачи затем измельчает высококачественный вспучивающийся материал до оптимального размера для обработки и разделяет его для транспортировки в бункер для хранения сырого корма.
Pacific Clay О нас — Pacific Clay Products
Более вековые традиции
В конце 1800-х годов открытие месторождений высококачественной глины и угля недалеко от Альберхилла, Калифорния, привело промышленников в этот район в поисках сырья для многочисленных обожженных керамических изделий.Эта глина геологически уникальна тем, что присутствуют как осадочные (озера, ручьи или океанические отложения), так и метаморфические (измененные по месту) глины. Это позволяет производить необходимое смешивание для изготовления множества различных керамических изделий. Нет другого такого месторождения глины в мире … этим глинам более 200 миллионов лет! Район Альберхилл поставляет глину для изготовления тонкой керамики, глиняные канализационные трубы, облицовочный кирпич, брусчатку, кровельную черепицу, глиняные горшки, огнеупорный кирпич, бурый уголь и пластилин. Одна известная гончарная компания, которая работала на острове Каталина до 1940-х годов, использовала глину из наших рудников Альберхилла для производства керамики, которая сегодня является чрезвычайно коллекционной.
Компания Alberhill Coal and Clay Company добывала низкосортный бурый уголь и огнеупорную глину на этих объектах с 1890 по 1940 год. Добыча в подземных шахтах, эти туннели вырывали вручную с помощью лопат и тач. Задолго до OSHA это было опасное место для работы из-за многочисленных обрушений и связанных с ними смертей. Компания Los Angeles Brick Company, основанная в 1895 году здесь, в Альберхилле, производила облицовочный кирпич, брусчатку, канализационные трубы и кровельную черепицу. Многие из оригинальных зданий в Лос-Анджелесе были построены с использованием этих продуктов.Ройс-холл и библиотека Пауэлла Калифорнийского университета в Лос-Анджелесе, построенные в 1920-х годах, использовали кирпич этой компании. В то время Альберхилл представлял собой автономное сообщество с почтовым отделением, католической церковью и начальной школой, расположенными прямо на территории. Трехкомнатная школа Alberhill Schoolhouse оставалась открытой до 1960-х годов, а сегодня это место проведения многих встреч в классе. Los Angeles Brick Company была куплена Pacific Clay Products в 1963 году. Дэвид Х. Мердок, нынешний владелец, выкупил все акции Pacific Clay в 1973 году и сделал компанию частной.
Pacific Clay Сегодня
Pacific Clay Products постоянно расширяется для удовлетворения потребностей своих клиентов, и в 1996 году было завершено строительство современного завода по производству кирпича. Наш нынешний объект является крупнейшим на западе. Новый завод может сжигать кирпич за 14 часов, по сравнению с 35 часами на традиционном заводе, и может производить 40 000 000 кирпичей в год. Наряду со многими историческими «керамическими новинками», такими как двойной выпуклый носик, мини-кирпич, текстура с рюшами и другие, Pacific Clay продолжает удовлетворять потребности своих клиентов, создавая инновационные кирпичные конструкции и цвета.Pacific Clay Products остается доминирующим поставщиком глиняных изделий в Южной Калифорнии и выполняет прекрасные архитектурные работы по всей стране.
Наряду с богатой историей производства кирпича, название Pacific Clay также известно как канализационные трубы. У Pacific Sewer Pipe Company было несколько предприятий в Калифорнии, где они производили канализационные трубы для использования по всей стране. Hoist Pit, расположенный всего в двух милях к югу от Альберхилла, поставлял на завод Terra Cotta глину для производства канализационных труб с 1890 по 1915 год.Завод Terra Cotta был закрыт в том же году, и производство было перенесено в Санта-Фе-Спрингс, Калифорния, где компания стала публичной и стала Pacific Clay Products. Завод в Санта-Фе-Спрингс вырос до переработки 200 000 тонн в год, что в середине 1960-х годов было крупнейшим производством канализационных труб в мире. Этот завод был закрыт в 1980 году, и подразделение по производству труб переехало в Корона, ближе к Альберхиллу и его обширным месторождениям глины. Pacific Clay продолжала производить канализационные трубы в Короне до 1997 года.
Стивен Дж. Хайд: отец индустрии легкого бетона
Из документа Concrete International , август 2009 г., страницы 35-38. Воспроизведено с разрешения Американского института бетона (www.concrete.org).
Стивен Дж. Хайд: отец индустрии легкого бетона
Из остатков кирпичной сваи был разработан легкий заполнитель
T.W. Бремнер и Джон Райс
Строители давно осознали важность снижения плотности бетона при сохранении его долговечности и прочности.Римляне использовали природные отложения везикулярных агрегатов, таких как пемза и шлак, в качестве предпочтительных агрегатов для своих структур — даже когда песок нормальной плотности и речной гравий были легко доступны. Примеры, которые все еще существуют сегодня, включают пирсы в порту Коза, построенные на западном побережье Италии вскоре после 273 г. до н.э., –1 гг. И купол Пантеона диаметром 50 м (164 фута), построенный в 128 г. н.э. Адрианом. В Пантеоне внутреннюю изменчивость естественных везикулярных агрегатов удалось обойти путем сортировки их вручную по плотности, что позволило уменьшить плотность бетона по мере увеличения высоты купола и уменьшения напряжений. 2
Изменчивость природных отложений вулканических агрегатов, однако, оставалась проблемой в течение почти 2000 лет, пока ее не решил Стивен Дж. Хайд (рис. 1), родившийся в Америке сын ирландских иммигрантов из Типпарари. Его родители, Патрик Джозеф Хайд и его жена Бриджит, приехали в Нью-Йорк со своей молодой семьей, имея письмо из Ирландии, в котором говорилось, что у Патрика «верительные грамоты», что, несомненно, способствовало его делу, поскольку он с готовностью нашел работу с правительством в качестве подрядчика Инженер-строитель ремонтирует здания и мосты на Западе. 3 Стивен Хайд родился в 1861 году в Кеокеке, штат Айова, и с детства работал со своим отцом в Канзас-Сити, штат Миссури. После нескольких лет, проведенных в Сан-Франциско, штат Калифорния, Хайд вернулся домой, где стал хорошо известен как производитель кирпича и строительный подрядчик, построив такие впечатляющие кирпичные здания, как здание Миссури на выставке в Чикаго и Академия Лоретты. 4
Рис.1: Изобретатель
Производство кирпича
Изготовление кирпича с использованием ульевиков того времени было довольно неэффективным процессом, так как температура внутри печи сильно варьировалась.После того, как определенная загрузка была «сожжена», продукт пришлось отсортировать вручную. «Обожженные» кирпичи подходили для наружного применения из-за их устойчивости к проникновению дождя, а также к эффектам замерзания и оттаивания. «Лососевые» кирпичи (так называемые из-за розового цвета) не обжигались полностью, но подходили для внутреннего использования.
Третья категория, «вздутия живота», была выбракована и представляла собой значительные финансовые потери для производителя. Это были кирпичи, расположенные рядом с источником тепла в печи, которые нагревались слишком быстро, чтобы выделяющиеся в глине газы могли рассеяться, и, таким образом, расширились более чем на треть от своего первоначального размера.Кирпичи, изготовленные из определенных отложений глины, сохраняли эту растянутую форму при охлаждении, что приводило к образованию пузырьковой внутренней структуры с по существу несвязанными пустотами, окруженными твердой, непроницаемой керамической матрицей.
Стивен Хайд обладал изобретательным и находчивым умом. Он видел ценность в измельчении отбракованной сваи до нужного размера и включении ее в бетонную смесь. Он считал, что это может обеспечить последовательный способ производства легкого бетона, обладающего значительной прочностью и долговечностью. В письме своему племяннику Джорджу от 7 октября 1914 года он рассказал, как «сжег» некоторые материалы на заводе Ocean Shore Iron Works в Сан-Франциско. Он особо отметил, что «некоторые материалы настолько легкие, что плавают в воде». Он также упомянул, что в его конечном продукте не было слабых мест. Вместе с письмом он прислал образцы подготовленного им материала.
Производящий агрегат
Хайд был настолько уверен в достоинствах своего нового материала, что нанял патентного поверенного 29 января 1914 года. Патент США № 1,255,878 был впоследствии выдан на имя Хейда 18 февраля 1918 года. 5 Патент охватывал глинистый материал и специально упоминается «специальная глина, сланец и сланцевая порода», подразумевая, что не весь глинистый материал подходит, и что продукт необходимо нагреть до температуры 1220 ° C (2228 ° F) в течение примерно 2 часов.В тексте патента Хайд заявил: «Мое изобретение относится к производству кирпича, плитки, терракоты и подобных формованных изделий». 6 После возвращения из Сан-Франциско в Канзас-Сити, Хайд возглавил компанию Flannigan-Zeller Brick Company, где у него был доступ к обжиговым печам для кирпича, а также доступ к отходам процесса производства кирпича (вздутие) для измельчения до подходящего размера. для исследования бетона низкой плотности.
В разговоре с Уорреном Алленом помощник Хейда Лу Харрис объяснил, как они экспериментировали с глиняными шарами, которые помещались в различные места в печи для обжига кирпича.Их цель состояла в том, чтобы определить правильный температурно-временной режим для достижения свойств заполнителей, которые можно было бы использовать в бетонной смеси для получения оптимальных свойств в бетоне. В 1917 году его испытания показали, что вращающуюся печь можно использовать для экономичного производства керамзитового сланца, глины и сланца в больших количествах со свойствами, идентичными тем, которые производятся сегодня. 5
Суда-производители
Способность Хайда эффективно производить большие объемы бетона Concrete International / август 2009 37 легкого заполнителя, идеально подходящего для изготовления высокопрочного, долговечного и малопроницаемого бетона, была своевременной, так как в морской судоходной отрасли она была решена срочно, вызванной войной на подводных лодках. Первой мировой войны.В качестве строительного материала для лодок портландцементный бетон, вероятно, появился в 1848 году, когда Жан-Луи Ламбо построил весельную лодку для использования в пруду в своем имении в Миравале, Франция. 7 При толщине корпуса от 30 до 40 мм (от 1,2 до 1,5 дюйма), длине 3,6 м (11,8 фута) и ширине 1,35 м (4,4 фута) лодка имела успех. Помимо дыры в дне, из-за которой он затонул, он был найден в хорошем состоянии примерно 100 лет спустя, когда его выкопали из грязи и выставили на бетонной конференции в Париже.Первое океанское бетонное судно было построено в 1917 году. При водоизмещении 400 тонн (440 тонн) и длине 26 м (85 футов) норвежское судно Namsenfjord продемонстрировало морским проектировщикам возможности и ограничения использования бетона нормального веса. как материал. 8
Хотя везикулярные вулканические агрегаты были опробованы и были обнаружены способные снизить собственный вес судов до приемлемых уровней, внутренняя изменчивость отложений агрегатов была такова, что требуемая высокая прочность не могла быть достигнута на постоянной основе.Хайд был патриотом, и, осознавая, что его продукт, который вскоре будет запатентован, может помочь в военных действиях, он бесплатно предложил его правительству на время войны при условии, что Хайдит, имя данный ему легкий агрегатный продукт был изготовлен государством, а не независимым подрядчиком. 9
Его предложение было сделано в письме от 18 февраля 1918 г. директору Департамента бетонного судостроения У.S. Emergency Fleet Corporation, Вашингтон, округ Колумбия. Ответ был предоставлен 6 марта в письме, подписанном Р.Г.Дж. Парик в качестве главного инженера и подписан К.В.Б. (Карл В. Бойнтон). В письме выражался интерес к «обожженной глине в качестве заполнителя бетона в конструкции лодки» и предполагалось, что этот материал может быть развит до такой степени, что он придаст нам требуемую прочность и в то же время существенно снизит вес бетона. . » Последующие испытания подтвердили, что хайдит можно использовать для производства бетона 28 МПа (4000 фунтов на квадратный дюйм) с плотностью 1697 кг / м3 (106 фунтов / фут3).
Учитывая опыт Хейда в производстве высококачественного легкого заполнителя с использованием вращающейся печи, было удивительно, что первое судно, построенное Департаментом аварийного судостроения, было построено с использованием заполнителя из гораздо менее эффективных сушильных камер для ульев с пониженной тягой в Бирмингеме, штат Алабама. Было произведено достаточно материала для подачи бетона для 272-тонного (300-тонного) корабля Atlantis , спущенного на воду в декабре 1918 года. Вторым бетонным кораблем был Selma , длиной 132 м (434 фута) и шириной 13 м. (43 фута) и полной грузовой осадкой 8 м (26 футов).Корпус корабля имел толщину 127 мм (5 дюймов) по днищу и 100 мм (4 дюйма) по бортам. Покрытие над арматурой составляло всего около 16 мм (5/8 дюйма). Агрегаты, использованные для создания Selma , были изготовлены компанией Atlas Cement Company в Ганнибале, штат Миссури, с использованием метода вращающейся печи. В общей сложности 6670 тонн (7350 тонн) расширенных заполнителей было отправлено компании Fred T. Ley, оператору государственной верфи в г. Мобил, штат Алабама.
Хорошие характеристики легкого заполнителя, производимого вращающейся печью, при использовании для бетонного судостроения не упустили из виду государственный служащий Карл Бойнтон, который приступил к оформлению патента на то, что, по сути, было охвачено патентом Хейда.Это особенно удивительно, потому что Бойнтон сказал Аппо, одному из партнеров Хейда в компании Haydite, что «этот процесс … полностью выходил за рамки его знаний о сжигании материалов и процессах горения». 7 мая 1928 года в Апелляционном суде округа Колумбия было вынесено решение о том, что суд «убежден, что Бойнтон получил свои знания об изобретении от Хейда и что Хайд имеет право на получение приоритета». Ключевым доказательством по делу было письмо, которое Хайд написал своему племяннику Джорджу.Ходатайство о повторном слушании было отклонено 1 июня 1928 года. К сожалению, эта победа пришла примерно через 16 дней после смерти Хейда, когда он ехал по железной дороге из Монреаля в Канзас-Сити.
Реликвии
Корабль Atlantis лежит в обломках у Кристал-Бич на южной оконечности Кейп-Мей, штат Нью-Джерси. Один из авторов посетил место крушения около 1980 года и обнаружил, что бетон очень плохого качества. Модель Selma была затоплена несколько десятилетий назад у побережья Галвестона, штат Техас. Один из авторов посетил Selma в 1985 году и заметил, что бетон в целом был в отличном состоянии, и отпечаток опалубки все еще был хорошо виден — даже на уровне воды.Как и в случае с бетонными кораблями времен Второй мировой войны, на главной палубе видны бедствия в основном из-за неправильной практики бетонирования. Тем не менее, бетон был в целом в хорошем состоянии и показывает, чего можно ожидать от бетона, изготовленного с использованием легкого заполнителя, произведенного в вращающейся печи.
Производство наследства
Исследования Хейда, начатые примерно в 1897 году, позволили к 1917 году установить основные параметры производства заполнителей, которые привели к созданию современной индустрии легкого бетона. Температурный режим и степень расширения агрегатов не менялись на протяжении многих лет.Для современных дизайнеров огромным преимуществом является то, что они могут с уверенностью оглядываться назад на девять десятилетий хорошей работы с этим практически неизменным продуктом, изобретенным и введенным в коммерческое производство Стивеном Хейдом. Другими словами, Хайд сделал это правильно с первого раза, когда его продукт был зарегистрирован под названием «Хайдит».
Хотя Хайд был успешным строительным подрядчиком и финансистом, который был директором Bankers ’Trust Company, не было обнаружено никаких данных о том, что он получил большую прибыль от своих трех десятилетий исследований — даже несмотря на то, что он фактически в одиночку разрабатывал промышленность легкого бетона. Однако в записях того времени он описывается как предприимчивый и целеустремленный бизнесмен, «внесший значительный вклад в архитектурное украшение города и во время трудовых неурядиц занявший позицию, которая принесла ему непреходящую благодарность профсоюзов. ” 4
Хейда оставался в силе и после его смерти. После его смерти патент и права на производство перешли к его вдове Китти Хайд (ранее Кэтрин М. МакФаррелли). Когда Китти состарилась и стала психически немощной, права перешли к ее компаньону Уильяму Р.Стэнли, финансист. Перед своей смертью в разгар депрессии Стэнли продал патентные права другим. Хотя патент оставался в силе до 1947 года, родственники Стивена Хейда ничего от него не получили — факт, который до сих пор беспокоит большую семью. 10
Список литературы
1. Бремнер, Т.В., и Холм, Т.А., «Легкие бетоны с высокими эксплуатационными характеристиками», Материалы второго Международного симпозиума CANMET / ACI по достижениям в технологии бетона, SP-154, V.М. Малхотра, редактор, Американский институт бетона, Фармингтон-Хиллз, Мичиган, 1995, стр. 1-80.
2. Bremner, T.W .; Holm, T.A .; и Степанова В.Ф. «Легкий бетон — проверенный тысячелетиями материал», Труды о достижениях цемента и бетона, С.Л. Сакар и М.В. Груцек, редакторы, Университет Нью-Гэмпшира, Дарем, Нью-Хэмпшир, 1994, стр. 37-51.
3. Уитни К.В., Канзас-Сити, штат Миссури: его история и люди, 1800–1908 гг., Т. 3, 1908 г., стр. 134–135.
4. Kansas City Architect and Builder, V. 20, No.11, ноябрь 1905 г., стр. 12.
5. Хайд против Бринтона, 26F.2d 987 (округ Колумбия, 1928 г.).
6. Патент США № 1,255,878 (выдан 12 февраля 1918 г.).
7. Фишер К.В., «Лодка Ламбо — личное открытие», Бетон, ноябрь 1967 г., стр. 380–382.
8. Bremner, T.W .; Holm, T.A .; и Морган, Р.Д., «Бетонные суда — извлеченные уроки», Труды Третьей Международной конференции CANMET / ACI по бетону в морской среде, SP-163, V.M. Малхотра, изд., Американский институт бетона, Фармингтон-Хиллз, Мичиган, 1996 г. , стр.151-170.
9. Канзас-Сити Стар, 11 июня 1928 года.
10. Разговор с Джоном Хейдом из Канзас-Сити, штат Миссури, потомком брата Стивена Дж. Хейда.
T.W. Бремнер, FACI, FCSCE, является почетным профессором и почетным профессором гражданского строительства Университета Нью-Брансуика, Нью-Брансуик, Канада. Он бывший президент Атлантического отделения ACI. Он получил премию ACI Cedric Wilson Award в 1988 году и премию ACI Construction Practice в 1989 году и бывший председатель комитетов ACI 122, Тепловые свойства и характеристики бетонных и каменных систем, и 213, Легкий заполнитель и бетон.
Член ACI Джон Райс — президент Института расширенных сланцев, глины и сланца, Солт-Лейк-Сити, Юта. В его состав входят Консультативный комитет Правления ACI по устойчивому развитию и Комитеты ACI 211 по дозированию бетонных смесей; 301, Технические условия на бетон; 302, Устройство бетонных полов; и 308, Отверждение бетона.
»В зоне печи
В зеленой сельской местности Фландрии, всего в шести милях к югу от Антверпена в Бельгии, фабрика Argex расположена на берегу реки Шельда.Цементный завод на другом берегу реки открыл это место в 1965 году для экспериментов по производству керамзитовых гранул из глины, добытой из соседнего карьера. Цементный завод сейчас закрыт, но компания Argex, основанная в 1965 году, продолжает добывать около 1100 тонн глины каждый день для производственной мощности 650 000 кубических ярдов керамзитового керамзита каждый год.
«Гранулы керамзита Argex — это легкий заполнитель и многоцелевой строительный материал, который имеет множество различных потенциальных применений», — объясняет Джонни Бултхил, управляющий заводом в Argex.«Его можно использовать в качестве наполнителя для объектов гражданского строительства, таких как дороги, легкие блоки, железные дороги и водные пути, а также он отлично подходит для спортивных площадок, садовых террас, изоляционных полов и промышленных товаров».
Бизнес Argex — это B2B, при этом 95 процентов продукции направляется на строительство и строительство. Остальные 5 процентов используются для озеленения и гидрокультуры. Около 50 процентов всей продукции экспортируется в соседние страны и несколько стран за пределами Европы.
Неочищенная глина добывается из соседнего глиняного карьера. «Мы вывозим около 1000 [метрических] тонн [1100 американских тонн] каждый день, — говорит Бултхил, — но карьера годна еще на 25 лет, поэтому мы не будем думать о том, чтобы отгружать их в течение нескольких лет. пока что.» Его смешивают с оксидом железа и иногда разбавляют водой для получения нужной консистенции перед экструдированием и измельчением, готовым к выпечке.
Гранулы выпекаются в двухсекционной вращающейся печи, огромной трубе длиной 250 футов, которая вращается днем и ночью, обрабатывая около 55 тонн гранул каждый час с производственной мощностью 2400 кубических ярдов в день.Это самая большая печь подобного типа в Европе, которая выделяется на фоне неба на плоском ландшафте. Обогреваемая с использованием бурого угля, печь работает от двух до трех месяцев за один раз, а затем останавливается на период обслуживания от двух до четырех недель.
Кусочки глины сначала перемещаются в сушильную часть печи, которая вращается со скоростью 1 об / мин. Гранулы проводят здесь около 2,5 часов при температуре от 570 до 1470 градусов по Фаренгейту. Затем они перемещаются во вторую часть, печь для обжига, которая вращается на 5.2 об / мин, где они нагреваются в течение 30 минут до температуры 2012 градусов, вызывая расширение. Затем керамзит поступает в охладитель с псевдоожиженным слоем, где он охлаждается на воздухе до температуры от 176 до 212 градусов по Фаренгейту.
В процессе сушки гранулы естественным образом разбиваются на различные размеры, от одного до 25 миллиметров (от 0,039 до 0,984 дюйма) в диаметре, причем каждый размер имеет свое конкретное целевое использование. Они сортируются, а затем отправляются на склад.
Печь поддерживается восемью опорными роликовыми узлами, каждый из которых содержит по два подшипника. Раньше они были оснащены втулками или подшипниками скольжения, но три года назад Argex решил заменить опорные ролики, начав с первого набора из двух.
«Основная причина этого — проблема безопасности, связанная с ненадежностью подшипников скольжения», — поясняет Бултхил. «Когда мы перезагружать печь после замены опорного ролика, подшипники должны быть выровнены совершенно отлично. Если это не сделать точно, смазка не будет работать должным образом; они могут нагреть смазку и воспламениться.«Действительно, за последнее время на заводе Argex произошло два возгорания катков из-за несоосности втулок. Иногда перегрев происходит сразу же, но иногда может пройти неделя, прежде чем проблема будет обнаружена. Затем производство должно быть остановлено, пока не будут произведены необходимые регулировки. Более того, навыки, необходимые для регулировки этих старых подшипников скольжения, постепенно теряются, поскольку со временем персонал обновляется.
«Другой движущей силой перехода на роликовые подшипники является потребление энергии, за которым мы всегда следим», — говорит Бултхил.«Мы искали более современное решение с улучшенной системой смазки и, следовательно, меньшим трением, которое могло бы помочь снизить затраты».
Итак, Argex обратилась в SKF. «Подшипники SKF были для нас очевидным выбором», — говорит Бултхил. «Мы уже были клиентом, и в любом случае SKF — лучшая компания; мы не чувствовали, что нам нужно искать больше никуда ».
Проект был начат в 2008 году под руководством Джорджа Кэнта из отдела технического обслуживания. Исследование заняло некоторое время, поскольку SKF попросили поставить не только подшипники, но также опорный ролик и вал, корпуса и опорные плиты с точно такими же габаритными размерами, как в предыдущем решении, чтобы упростить и минимизировать стоимость установки.Новые блоки опорных катков, каждый весом около 25 тонн, были установлены в августе 2010 года. Эти блоки также оснащены автоматической системой смазки SKF.
«С того момента, как мы договорились о сделке, все прошло идеально, и с тех пор, как мы их установили, подшипники работали отлично», — говорит Бултхил. «Мы хотели от SKF более простого и надежного решения. Кроме того, эта новая система подшипников снижает потребление энергии до 10 процентов. Учитывая значительные инвестиции, которые мы сделали, мы надеемся на максимально долгий срок службы катков.«Argex в настоящее время ищет замену второго комплекта опорных роликов на своей вращающейся печи и надеется в ближайшее время заключить сделку с SKF.
ARGEX
- Год создания 1965 84 сотрудников
- Непрерывный процесс (24 часа в сутки, 7 дней в неделю)
- Производственная мощность: 650 000 кубических ярдов / год
- Производство 2400 кубических ярдов гранул Argex / день
- Добыча 1100 тонн глины / сутки
Факты о продукте
Гранулы глины Argex:
- Экологичность: 100% глина
- Light: плотность 20-47 фунтов / куб. Фут
- Изоляция (тепловая и акустическая).Инертный, химически нейтральный. Большая грузоподъемность. Негорючие. Невосприимчив к морозам и жаре. Отличные дренажные свойства.
Argex в цифрах
Тонн гранул / час 55
Длина трубы печи в футах 250
Тонны глины / сутки 1,100
Кубических ярдов гранул / день 2,400
Максимальная температура в печи (o F) 2,192
.
Комментариев нет