Чем ламинируют дсп: Как ламинируют ДСП
Как ламинируют ДСП
Ламинирование ДСП представляет собой процесс обработки лицевой части древесностружечной плиты, результатом которого является нанесение на её поверхность декорированной пленки. Цвет, фактура и дизайн готовой продукции изменяется в зависимости от использования конкретной технологии.
Горячее ламинирование ДСП – основные положения
Плиты перед началом обработки выравниваются. Для горячего ламинирования подходят материалы с плотностью от 0,6 до 0, 65 г/ см3. Использование плит меньшей толщины создает риск чрезмерной прессовки ДСП, что выражается в нарушении клеевых связей между стружками материала. Это сказывается на прочности готовой продукции, а также на качестве конечного результата.
Процесс горячего ламинирования предусматривает использование конвейерных и короткотактных ленточных прессов, способных обрабатывать материал при повышении его температуры до 250 градусов. Рассматриваемая технология обеспечивает воздействие давления в 25 МПа, благодаря которому смола равномерно распределяется по рабочей поверхности, создавая единое полотно.
Холодное ламинирование ДСП – альтернативный способ декорирования
Для этой цели используются полимерные пленки, а также плнеки на основе полистирола, акриловых химических полимеров. Данный метод применим в случаях, когда отсутствует возможность в температурном воздействии на лист ДСП. В связи с большими затратами и минимальным экономическим эффектом данный метод на практике имеет ряд нюансов: применяется технология частичного нагревания поверхности (до 70 градусов), результатом которого является нанесение рисунка, неотделимого от плиты. Для процедуры холодного ламинирования в качестве ламинатора используется промышленный пресс, который создает нагрузку на рабочую поверхность и совмещает клеевую основу с текстурной пленкой.
Итог
Процедура ламинирования представляет собой способ обработки рабочей поверхности листа ДСП. Данная технология используется для создания уникальных цветовых и факторных рисунков. При горячем ламинировании пленка, а также клеевая основа плиты разогревается до 250 градусов. Такой подход способствует наложению рабочего материала на основание ДСП, что создает эффект цельной плиты, не подвергавшейся обработке. При холодном ламинировании температурное воздействие не оказывается, однако ПВХ пленка накладывается на лист посредством воздействия конвейерного пресса на её структуру.
Как заламинировать дсп своими руками
Ламинированием называют операцию по оклейке поверхности ДСП специальной пленкой или бумагой. После этого материал приобретает декоративные качества, хотя основные характеристики его остаются прежними.
Для чего нужно ламинирование?
Дешевая и достаточно прочная ДСП – это самый востребованный материал для изготовления недорогой мебели. В натуральном виде прессованные плиты из стружек и опилок выглядят не слишком декоративно, поэтому производители отделывают их поверхность и кромки пленками из пластика или бумаги, пропитанной синтетическими смолами.
Покрытие не только делает материал декоративнее. Для ламинированной ДСП характерна более высокая влагоустойчивость по сравнению с исходным материалом. Это дает возможность использовать ЛДСП для изготовления кухонных гарнитуров и другой корпусной мебели, которой приходится контактировать с влажной средой.
Какую пленку выбрать для ламинирования?
В заводских условиях ламинирование ДСП проводят при помощи:
- бумажно-слоистого пластика, пропитанного смолами;
- бумаги с пропиткой из подобных материалов.
При использовании смоляной пропитки бумаге удается придать влагоотталкивающие свойства, а толстый слой материала позволяет выполнить тиснение, имитирующее фактуру ценных пород дерева или камня.
В качестве покрытия применяют и натуральный шпон, и термопластичные пленки из синтетики. В каждом случае технология обработки ДСП немного отличается, но все материалы с влагостойким покрытием в быту называют ламинированными.
При выборе готовых плит для изготовления мебели стоит поинтересоваться способом оклейки:
- кашированная ДСП внешне не отличается от ламината, но имеет меньшую прочность покрытия;
- шпонированные изделия всегда имеют рисунок натурального дерева, можно рассмотреть отдельные пластины покрытия;
- покрытые синтетическим шпоном (пленкой) отличаются от натуральных низкой ценой и отсутствием в рисунке границ полосок деревянной облицовки.
Часто при самостоятельном изготовлении мебели мастера для экономии пытаются ламинировать ДСП в домашних условиях самостоятельно. Из-за сложности промышленного процесса воспроизвести его не удается, и облицовка ДСП проводится разными видами пленки из синтетики.
Существует несколько разновидностей покрытия, подходящего для монтажа в домашних условиях:
- Меламиновая пленка. В состав материала входят фенолоформальдегидные смолы, небезопасные для здоровья при нагревании. Ламинирование мебели дома нужно производить при хорошем проветривании.
После остывания материал становится безопасным, образует на фанере или ДСП толстый и прочный слой с влагоотталкивающими свойствами. Меламин чаще всего используют для отделки кромок.
- ПВХ. Мембраны из ПВХ могут иметь клеевой слой, но иногда выпускаются без него. В последнем случае наклеить ламинат на ДСП можно при помощи универсальных клеев. Выбрать их лучше сразу при покупке материала. Обработка стружечных плит самоклейкой – самый простой способ нанесения водонепроницаемого и декоративного покрытия.
- Фенольная пленка. Не отличается высокой влагостойкостью, но хорошо предохраняет поверхности от механического воздействия.
Выбрав нужный материал, ламинировать ДСП своими руками можно без специального оборудования.
Особенности ламинирования ДСП
В промышленных условиях для склеивания основы и покрытия используются ленточные или конвейерные прессы. Они не только плотно прижимают ламинат к основе, но и сильно нагревают его.
Провести ламинирование столешницы или дверец кухонного гарнитура в домашних условиях несложно:
- Подготовка плиты начинается с шлифовки. При большом объеме работ удобнее использовать шлифмашины с насадками для дерева. Маленькое изделие (полку, дверцу и т. п.) можно зачистить и вручную, применяя наждачную бумагу, натянутую на деревянный брусок или специальный держатель. Шлифовку продолжают до тех пор, пока поверхность не станет гладкой, без выступающих элементов стружки.
- После первичной обработки поверхность рекомендуется зашпатлевать, просушить, и снова обработать мелким наждаком. Такая тщательность обработки продиктована свойствами мембран для оклейки: тонкая пленка не ляжет ровно, если на поверхности доски останутся даже минимальные дефекты.
- Выровненную заготовку обрабатывают любым грунтовочным составом по дереву. Пропитка повысит способность пленки или клея образовывать прочное соединение облицовки с основой. Грунт наносят по инструкции и просушивают.
- Оклеивание начинают с раскроя пленки по размеру деталей. Если на самоклейке с изнанки нанесена сетка, то для раскроя можно использовать ее, не прибегая к дополнительным измерительным инструментам. Но чаще всего разметку проводят при помощи линеек и угольников. Резать пленку любого типа следует острым ножом (макетным, канцелярским резаком). Кромка получится прямой и ровной, если рез проводить по линейке (лучше взять металлическую).
- Выкройку частично освобождают от защитного слоя, клеевой стороной прижимают к краю детали и постепенно продвигаются вдоль поверхности, стараясь приклеивать мембрану ровно и без пузырей. Если под пленкой все-таки остался воздух, выгнать его можно резиновым шпателем в сторону ближайшей кромки.
Как клеить пленки без клеевого слоя?
Если выбранный для ламинирования материал не имеет клеевого слоя, используют разные технологии:
- При выборе ПВХ или другой облицовки покупают и клей для нее.
Этот состав нужно нанести на подготовленную плиту согласно инструкции. Чаще всего клеем нужно смазать поверхность в 1 слой и слегка подсушить его (10-20 минут). Раскроенную пленку накладывают и разравнивают твердым валиком или шпателем. Если есть возможность проводить работы с помощником, то рекомендуется при наклеивании слегка прогревать пленку бытовым феном. Ее будет легче выровнять и уложить без складок. Разглаживание производят от центра к кромке, стараясь удалить пузыри воздуха.
- Меламиновые материалы требуют нагрева в процессе приклеивания. В домашних условиях самый доступный нагревательный прибор – утюг. Его нужно включить заранее и прогреть на режиме для глажения хлопка или льна. Из меламина чаще всего делают кромки. Нужно отрезать ленту нужной длины, приложить ее к срезу плиты и прогладить утюгом. После остывания меламин образует на поверхности ровный слой. Ленту для кромок берут шире, чем кромка, и после приклеивания излишки срезают макетным ножом, передвигая его параллельно грани.
Затем край материала обрабатывают наждачной бумагой.
Используемые технологии позволяют получить не слишком долговечное, но надежно защищающее от воды покрытие ДСП.
Читайте также:
Автор: tat.trofimova
Ламинирование ДСП
Ламинирование ДСП — это вид отделки плитных и листовых материалов (древесностружечных и древесноволокнистых плит, фанеры) напрессовкой на них бумаги, пропитанной смолами. Облицованная этим способом поверхность не требует дальнейшей отделки. Технология получения облицованных методом ламинирования ДСП состоит из следующих этапов: подготовки основы, подготовки бумаги, формирования пакетов, напрессовки бумаги на основу.
Подготовка основы. Эта операция заключается в выравнивании поверхности основы. Для облицовывания методом ламинирования дсп могут быть использованы плиты плотностью 0,65 — 0,7 г/см3. При меньшей плотности в процессе прессования может произойти сильная упрессовка плиты (более 10%), приводящая к разрушению клеевых связей между стружками и, как следствие, снижению ее прочности. Влажность плит должна быть 7-8%, допуск по толщине плиты — в пределах 0,2 мм. Шероховатость поверхности плиты должна находиться в пределах 63-16 мкм. Для получения заданной шероховатости плиты шлифуют на шлифовальных станках ДКШ-1. Уменьшить шероховатость плит можно при их изготовлении добавлением мелких частиц и пыли в наружные слои. Выравнивают поверхность плиты нанесением шпаклевочных составов.
Подготовка бумаги. Для облицовывания плит методом ламинирования ДСП применяют три вида бумаги: бумагу-основу (сульфатную) массой 80-150 г/м2 для внутренних слоев и облицовки оборотной стороны; кроющую бумагу — декоративную, одноцветную или с рисунком текстуры древесины (сульфитную) для верхнего слоя, массой 126-170 г/м2; отделочную бумагу — прозрачную, прочную во влажном состоянии, массой 20-40 г/м2. Отделочная бумага, являясь защитной пленкой, повышает прочность покрытия к истиранию и улучшает его внешний вид.
Бумага пропитывается карбамидоформальдегидными, карбамидомеламиноформальдегидными и меламиноформальдегидными смолами. Пропитывают бумагу на специальных пропиточно-сушильных установках. На декоративную бумагу наносят рисунок текстуры способом глубокой трехцветной печати.
При пропитке бумаги весь воздух, имеющийся в ней, необходимо вытеснить и заменить смолой. Смола должна заполнить не только промежутки между волокнами, но и пропитать их. В противном случае получаются покрытия низкого качества. Поэтому для пропитки применяют пропиточные устройства, в которых бумага не сразу погружается в смолу, а сначала смачивается сеточная сторона полотна бумаги. При этом смола, впитываясь, вытесняет воздух, который выходит с другой, не смоченной стороны полотна. После этого повторно погружают все полотно.
Для предварительного одностороннего нанесения смолы используют различные методы: нанесение смолы валиком, смачивание одной стороны путем удерживания бумаги на поверхности смолы и др. Температура смолы в пропиточной ванне 30-40 °С, вязкость 11-13 с по ВЗ-4. Пропитанная бумага подается в сушильную конвекционную камеру, где испаряется летучая часть и происходит частичная поликонденсация смолы.
Сушильные камеры делают двух типов: горизонтальные и вертикальные. В вертикальных камерах бумажная лента после пропитки перемещается вверх; движение воздуха в ней преимущественно сверху вниз. В горизонтальных камерах лента движется горизонтально. Для ее поддержания применяют реечные конвейеры или, в наиболее совершенных конструкциях, струи горячего воздуха. Температура воздуха в зависимости от вида сушилки, смолы и скорости подачи находится в пределах 60-160 °С. На выходе из сушилки бумагу охлаждают и сворачивают в рулон или раскраивают на форматные листы.
Для упрощения процесса ламинирования ДСП и экономии бумаги применяют комбинированный способ пропитки кроющей бумаги: 1 — пропитка дешевой смолой (карбамидоформальдегидной), сушка; 2 — пропитка меламиноформальдегидной смолой, сушка. При этом отпадает необходимость в применении защитной бумаги.
Готовую бумагу для выравнивания влажности выдерживают в камерах климатизации. Содержание воздушно-сухой смолы в бумаге от массы непропитанной бумаги следующее: для бумаги-основы 75-90%; декоративной 120-140%, отделочной 200-250%.
Ламинировать дсп в домашних условиях. Что такое лдсп в мебели? Плюсы и минусы ДСП
Ламинированная ДСП
Ламинированная древесно-стружечная плита (ЛДСП) является одним из самых популярных материалов для изготовления мебели и стеновых панелей. Технология производства и себестоимость материала невысоки, а разнообразие расцветок и фактуры велико. Это и обусловило её популярность и широту применения.
История изобретения
Ламинированная ДСП была изобретена во второй половине девятнадцатого века, в далёком 1887 году. Автором новинки считается американский предприниматель Эрнст Хаббард. Он первым догадался смешать отходы деревообрабатывающего производства – стружки и опилки – с казеиновым клеем и отформовать полученную смесь в геометрически безупречные плиты. Первые ДСП были ламинированы шпоном дерева дорогих поделочных пород, и оказались доступными далеко не каждому потребителю. Первыми покупателями изделий из ламинированной ДСП были весьма состоятельные люди.
Но постепенно технология её производства становилась совершенней и дешевле. В 1926 году немец Фройденберг рассчитал оптимальное соотношение между составными частями ДСП – связующим материалом с одной стороны и стружками и опилками – с другой. Согласно этим расчетам, связующего материала должно быть от 3 до 10 процентов – в зависимости от класса ДСП. Позже эти расчеты были откорректированы и уточнены. По современной технологии связующим материалам отводится 6-8 процентов объёма ДСП.
Технология производства: изготовление ДСП
Главный материал для наполнения древесно-стружечных плит – стружка и опилки – берётся не только из отходов деревообрабатывающего производства, но и производится из низкосортной древесины на специальных рубильных станках, измельчающих крупные куски дерева на стружку толщиной 0,2 – 0,5 мм и длиной не более 40 мм. Причём в наружные слои плит укладывается стружка наименьших размеров. Частицы, предназначенные для наружного слоя, подвергаются дополнительному размельчению в дробилках (уменьшение ширины) и мельницах (уменьшение толщины). Эта операция особенно важна при производстве ламинированной ДСП, так как при её производстве к качеству поверхности предъявляются повышенные требования.
Заготовленная сырая стружка по системе механических или пневматических транспортёров поступает в бункера-хранилища. Оттуда по мере необходимости подаётся в сушилки. Просушивание стружки для разных слоёв ДСП осуществляется в разных сушилках: для внешнего слоя на выходе достаточно содержание влаги в 4-6 процентов, а вот для внутреннего требования более жёсткие – 2-4 процента. Сушилки для стружки обычно бывают конвективными барабанного типа. После просушивания стружка просеивается на сите для отделения более мелких фракций, предназначенных для наружного слоя.
Затем стружка поступает в смеситель – агрегат для обволакивания частиц сырья связующим составом. Процент связующего для внутреннего и внешнего слоя неодинаков. Для внутреннего он составляет около 60 процентов, для внешнего – 53-55. Это одна из наиболее сложных операций при изготовлении ДСП, так как при недостатке связующего стружка плохо склеивается, а при избытке происходит перерасход материала и, как следствие, плиты получается более низкого качества.
В последнее время всё большее распространение получают смесители так называемого «факельного» типа, которые производят более качественный продукт. В таких смесителях связующий состав распыляется с помощью форсунок и направляется на взвешенные с помощью пневматики в воздухе стружку и опилки. При перемешивании связующее вещество равномерно оседает на поверхности древесных частиц. Такие смесители – техника довольно тонкая и нуждается в точной настройке, чтобы соотношение между связующим составом, стружкой и отвердителем было оптимальным. Затем полученная смесь с помощью механических приспособлений удаляется в формующие машины.
В современном производстве ДСП существует два способа формовки: на ленточном конвейере и на металлических поддонах. Смесь из стружки и связующего равномерным слоем наносится на поддон или транспортёр, в зависимости от типа агрегат. Причём в наружные слои формующая машина насыпает более мелкую стружку. У каждого способа производства свои нюансы. Плита, полученная при поддонном способе формовки, получается с несколько большими допусками по толщине, но такой способ более прост и надёжен. Ленточный способ обеспечивает более точную геометрию конечного продукта и некоторую экономию энергии. Но он нуждается в скрупулёзной настройке оборудования.
Прессование ДСП осуществляется в два этапа. На первом (подпрессовка) происходит уменьшение толщины пакета из древесно-клеевой смеси: при поддонном формовании – в 2,5-4 раза, при ленточном – ещё больше. Давление при поддонном формовании составляет до 1,5 мПа, при бесподдонном – 3-4мПа. После подпрессовки плита поступает в гидравлический пресс, где при высокой температуре (180 градусов) ДСП подвергается прессованию усилием в 2,5-3,5 мПа. Продолжительность приложения усилия – 20-22 секунды на один миллиметр толщины плиты. После выхода из гидравлического пресса горячая плита обрезается по размеру и отправляется в камеру для охлаждения, где выдерживается примерно в течение пяти дней. Затем поступает на склад, откуда отгружается потребителю.
Ламинирование и каширование ДСП
Покрытие ДСП плёнкой для придания им фактуры, имитирующей шпон дерева поделочных пород, осуществляется двумя способами: ламинированием и кашированием. При ламинировании декоративная плёнка воздействием высокой температуры (до 210 градусов) и давления до 28 мПа буквально врастает, впрессовывается в плиту. При кашировании же условия более щадящие. На ДСП наносится слой клея, и затем при температуре в 150 градусов и давлении до 7 мПа происходит прочное приклеивание плёнки к основе. В зависимости от качества покрытия ЛДСП подразделяется на плиты 1 сорта (без дефектов или с незначительными дефектами, не влияющими на внешний вид изделия), 2 сорта – плиты имеют видимые дефекты, но могут использоваться по назначению, и бессортица (плиты имеют значительные дефекты, но могут использоваться в строительстве).
Для облицовки древесно-стружечной плиты используются специальные меламиновые плёнки на бумажной основе, пропитанные синтетическими смолами. Разнообразие расцветок и фактур таких пленок необычайно высоки, и имеют высокий дизайнерский потенциал. Это и обусловило широкое применение ламинированного ДСП в мебельной и строительной промышленности.
Использование ЛДСП
Производство мебели – это область, в которой применяется львиная доля ламинированных ДСП. Это и понятно: фиксированные размеры с определённой толщиной, высокий дизайнерский потенциал поверхности, лёгкость обработки, демократичная цена – данные факторы и определили популярность материала.
Стандартный размер плиты – 2500 на 1830 мм. Отечественная промышленность выпускает ЛДСП толщиной 10, 16, 18, 22 и 25 мм. Большая часть фабрик по выпуску плит сосредоточена вблизи крупных городов, где есть мебельное производство. Наша фирма занимается поставкой потребителю качественной ЛДСП по невысоким ценам. У нас вы можете дешево приобрести ЛДСП со склада в Москве и ближнем Подмосковье. Кроме этого, Вы можете купить ЛДСП в Москве как для производства мебели, так и для выпуска отделочных панелей. Большое разнообразие декора и разные типы тиснения ДСП позволят даже самому требовательному потребителю выбрать себе изделие по душе.
Продажа нашей фирмой ЛДСП в Москве производится для изготовления мебели: офисной, кухонной и даже детской. Вопреки распространённому заблуждению, современные виды ЛДСП практически не выделяют формальдегидов и разрешены для производства детской мебели. Кроме этого, наш представитель окажет помощь в выборе ЛДСП и для иных целей: для оформления интерьеров супермаркетов, магазинов, кинотеатров, выставочных павильонов и других публичных помещений. Купить ламинировано ДСП со скидкой можно купить у нас со склада в Москве.
ЛДСП нашла широкое применение и в производстве межкомнатных дверей, перегородок и стеновых панелей. Этот материал снижает уровень шума в помещении, и отвечает нормам противопожарной безопасности, так как горит значительно хуже, чем обычное дерево. Столешницы из водостойких сортов ЛДСП прекрасно заменяют столешницы из других более дорогих материалов – дерева, декоративного пластика или природного камня.
Ламинированое ДСП купить просто.
Продажа ламинированного ДСП .
Цены предоставлены в разделе .
Дефицит натуральной древесины для производства недорогой мебели стал причиной появления в середине прошлого века древесно-стружечных плит. Этот относительно дешевый вид пиломатериалов сегодня известен каждому домовладельцу.
Европейские страны в 40 годах прошлого столетия использовали для изготовления мебели фанеру и дерево, но столкнулись с подорожанием и недостаточными поставками этих материалов на свои фабрики. Немецкий инженер Макс Химмельхебер несколько лет работал над созданием прочного и доступного по цене композитного материала. По разработанной им технологии, для создания ДСП использовали древесные опилки и фенольные смолы.
ГОСТ 10632 89 регламентирует содержание свободного формальдегида в 100 гр. плиты ДСП класса Е1 – до 10 мг, класса Е2 – до 30 мг.
Производство состоит из нескольких этапов:
- производство опилок ;
- сортировка и просушка сырья;
- соединение стружки с клеем ;
- формирование ковра;
- горячее прессование плит;
- охлаждение;
- шлифовка и раскрой;
- упаковка.
- Получение стружки
Для опилок используют любые отходы пиломатериалов. Неделовая древесина освобождается от коры, режется на метровые отрезки и помещается в бассейн для гидрообработки. Стружка в станках нарезается параллельно древесным волокнам из полуметровых отрезков. Более половины в составе ДСП составляет крупная стружка, из нее формируют средний из трех слоев. Наружные слои состоят из более мелкой стружки высокого качества. Нарезанная стружка поступает в специальные мельницы, где молотками расщепляется по ширине и становится более гладкой.
- Сушка
В специальные бункеры для сбора стружки поступают опилки и с деревообрабатывающих предприятий. Для просушивания стружка поступает по транспортеру в установку, где перемешивается и продувается горячим воздухом. Крупные частицы отделяются от нормальных и возвращаются в измельчитель.
- Формирование ковра из стружки и клея
Сухая стружка дозировано поступает в смеситель, туда же подается клей – синтетическая смола. Чтобы клей равномерно покрывал стружку, его распыляют с помощью сжатого воздуха. Стружка, покрытая клеем располагается на вибрирующий транспортер.
- Прессование и охлаждение
Формирование ковра происходит на четырех холодных прессах:
- нижний слой ковра формируется в первом;
- второй и третий пресс формируют второй слой из крупной стружки;
- в четвертом прессе образуется третий, наружный слой ковра.
Далее ковер из трех слоев попадает на уплотняющий пресс, толщина композита уменьшается втрое. Разогретый и увлажненный ковер поступает под горячий пресс. Температура в камере составляет 150 градусов Цельсия, а давление – 20 кг на каждый квадратный сантиметр ковра.
Влага, быстро испаряясь под давлением, образует паровой удар. Пар проникает в каждый слой ковра, сокращая его пребывание под прессом.
Когда процесс прессования заканчивается, горячая плита охлаждается потоком холодного воздуха. Готовая плита подвергается шлифовке.
Ламинированная ДСП (ЛДСП)
Благодаря ламинированию плита получает облицовку и не нуждается в дальнейшей отделке. Процесс ламинирования непрост и состоит из нескольких этапов:
- подготовка поверхности и бумаги;
- создание пакетов;
- ламинирование под прессом.
Подготовка
Отшлифованная поверхность плиты шпаклюется и подвергается шлифовке вновь. Для ламинирования используется сульфатная, сульфитная и отделочная бумага. Она может быть однотонной или имитирующей поверхность дерева. Метод глубокой печати позволяет получить трехцветный рисунок. Перед ламинированием бумагу пропитывают смолами на специальных станках. Смолы впитываются в бумагу, полностью удаляя воздух с ее поверхности. Начала вязкая жидкость покрывает одну сторону бумаги, воздух выходит с другой стороны, потом бумага погружается в смолистое вещество полностью. Пропитанную смолой бумагу сушат в конвекционной камере.
Создание пакетов
Перед загрузкой в пресс формируется пакет из следующих слоев:
- лист ДСП;
- бумажная основа в виде больших листов с обеих сторон листа;
- декоративный и отделочный слои укладываются только на лицевую сторону листа;
- листы металла.
В установку для ламинирования загружают несколько пакетов, между ними прокладывают асбестовые прокладки.
Ламинирование плит ДСП под прессом
Плиты в пакетах укладывают под гидравлический пресс, где в течение 15 минут они подвергаются воздействию температуры 135-210 градусов Цельсия, а давление в установке – 25-28 мПа.
Ламинирование на разных предприятиях производят по двум технологиям:
- с применением водяного пара;
- без пара.
Завершает процесс охлаждение, упаковка, складирование.
Другие способы облицовки
Каширование – то же ламинирование, но происходит проще и быстрее. Поверхность плиты покрывается клеем, на нее укладывается бумага, пропитанная смолами, разравнивается вальцами. После этого плита отправляется под холодный или горячий пресс.
Поверхность ДСП покрывают пленками из ПВХ, но такая облицовка больше подвержена механическим повреждениям. Еще один вид облицовки – покрытие натуральным шпоном, процесс аналогичен кашированию.
Все плиты ДСП кажутся одинаковыми, но они подразделяются на виды и сорта , могут быть огне- и водостойкими. Плиты относительно недороги, имеют гладкую поверхность, прочны: не усыхают и не скручиваются, поэтому являются универсальным материалом для производства мебели.
Видеоматериал «Производство мебельного ДСП»:
Обычные первые плиты ДСП появились еще в 1918 году. Благодаря прогрессу за многие годы материалы стали качественнее, надежнее, в наши дни уже доступны влагостойкие ламинированные доски для производства различной продукции. Существует много видов плит, изготовленных из дерева. К ним относятся МДФ и ЛДСП с разными характеристиками и своими особенностями.
Для того чтобы выбор материала для собственного шкафа или комода был осмысленным, необходимо знать достоинства и недостатки мебельных материалов.
Ламинированные древесностружечные плиты на основе термореактивных полимеров – это основной и часто применяемый материал для производства массовых элементов обстановки в промышленности, также он широко используется в строительстве. Такие плиты достаточно устойчивы к механическим и химическим воздействиям (бензин, ацетон, вода, растворители, спирт, кислота, кофе и другие вещества). Из этого можно сделать вывод, что ЛДСП – отличное сырье для производства медицинской, лабораторной, учебной, бытовой и офисной мебели.
Благодаря своей невысокой стоимости и великолепным строительным свойствам ДСП — самый широко используемый материал для изготовления мебели эконом-класса.
ЛДСП – материал, который изготовлен на основе натуральной древесины. Это тот же ДСП, но белее отшлифован, на поверхности которой стойкая меламиновая пленка. То есть главное их отличие – покрытие. Когда она запрессовывается в саму структуру доски – делает ее более влагостойкой и намного прочнее. Это «рыхлое» сырье, его стоимость бюджетная, по дизайну за счет пленки и покрытия можно достичь различных цветовых решений, в том числе и с рисунком натуральной древесины. Он широко используется в производстве корпусных изделий для кухни, офиса, дома, других предметов интерьера дома как основной материал. Из него изготавливают стенды для выставок, мебель для интерьера магазинов, аптек и супермаркетов. С МДФ происходит так же, но при этом такие доски более дорогие.
Большая часть офисной мебели производится именно из ДСП.
Ламинирование плиты ДСП производится различными цветами и разных текстур:
фантазийные векторные декоры;
- геометрия;
- орнаменты;
- однотонные бумаги;
- рисунки и имитация древесины.
Однако есть у этого материала и свои минусы — это вредные формальдегидные выделения.
Декоративная пленка для облицовки пропитывается смолой, она изготовлена из специальной декоративной бумаги, плотностью 60-90 г/м2.
Ламинирование — процесс нанесения декоративного покрытия под действием давления и воздействия температуры.
Ламинирование происходит в прессе. В процессе прессования бумага становится плотнее, по свойствам она наравне с пластиком. Сверху образовывается плотная глянцевая пленка, снизу такая же, но другой структуры — клеевая. Покрытие ламинированных досок достаточно прочное, образуется за счет растекания смолы по всей поверхности ДСП при давлении 25-28 Мпа и температуре 140-210°С. Для производства их ширина не может быть меньше 10 мм, но и не больше 22 мм. При ламинировании из плиты ДСП не выделяются пары альдегида, которые вредны для окружающей среды.
Ламинирование считается более надежным и дорогим способом изготовления ЛДСП.
Она впрессовывается в структуру плиты, делая её более прочной и влагостойкой.
Производители по-разному маркируют структуру ЛДСП, но обычно так:
- BS – это офисная;
- SE – дерево с поверхностными порами;
- SM — гладкая поверхность;
- МАТ — матовая гладкая поверхность;
- PR – пористая структура;
- PE – «апельсиновая корка».
Вне зависимости от способа нанесения такое ДСП называется ДСП с меламиновым покрытием.
Для производства чаще всего используются первые две: BS и SE. PR – также популярна, но используется реже, SM используется в производстве внутренних перегородок. Могут встречаться другие маркировки.
Широко используется для изготовления мебели, заполнения двери типа купе и прочих эдементов декора интерьера.
Преимущества и недостатки ЛДСП в мебели
Чтобы выбрать хорошее сырье для конкретной мебели необходимо знать его особенности в том числе плюсы и минусы. Любой материал из ДСП изготавливают из опилок и древесной стружки, пропитанных формальдегидной смолой как связующее вещество. ДСП выделяет формальдегид, который плохо сказывается на окружающей среде и здоровье человека, но в ЛДСП есть защитная пленка – ламинированный слой, который не позволяет веществу испаряться из досок.
Многообразие цветов и фактур, имитация фактуры натурального дерева.
Это не пластик, не железо, а все та же всем знакомая древесина.
Чтобы изготовить ламинированную пленку используется бумага определенной фактуры и орнамента. Ее пропитывают меламиновой смолой, вследствие чего та становится определенного уровня жесткости и более рыхлой. Потом под прессом поверхность доски соединяют с пленкой – так образовывается ламинированный лист стандартной толщины.
Устойчивость механическим повреждениям.
ЛДСП достаточно устойчивый материал к механическим и термическим воздействиям с большим ассортиментом фактур и расцветок. Его можно разработать в форме ценной породы дерева. Благодаря устойчивости к высоким температурам на столешницы из этого сырья можно ставить горячую посуду.
Устойчивость к термическому воздействию (к горячим кофейникам и сковородкам).
ЛДСП – это материалы, изготовленные на основе натурального дерева.
К минусам стоит отнести отсутствие возможности тонкой обработки и наличие формальдегидных смол в составе ДСП, а плюсы в высокой механической и химической устойчивости.
ЛДСП – это представитель старых всем известных древесно-стружечных плит (ДСП) в более шлифованном виде.
Мебель из МДФ — что это такое?
МДФ – улучшенная технология производства ДСП материалов. Доска состоит из мелких спрессованных фракций опилок. Благодаря такому способу скрепления материал получается высокопрочным, однородным и безвредным для здоровья. Благодаря этим показателям он может использоваться для производства любой мебели, в том числе и для детской комнаты. Стоимость его немного выше.
Основное отличие ЛДСП от ДСП – это покрытие Она впрессовывается в структуру плиты, делая её более прочной и влагостойкой.
Основными плюсами является высокая прочность плит, однородность, легкость обработки, влагостойкость, антидеформационные способности, широкий ассортимент и красивый дизайн.
МДФ довольно плотный материал — это делает его незаменимым в производстве мебели требующей вытачивания изящных линий, округлостей и пр.
Минусы: высокая цена, доски боятся механических повреждений и ударов, легко воспламеняются.
МДФ является экологичным материалом и не имеет ограничений по применению.
Как правильно выбрать ЛДСП?
На сегодняшний день существует немалое количество ДСП разного назначения. Их отличия заключаются в толщине, составе, износоустойчивости, плотности. Такие особенности связаны с использованием в разных областях производства плит. Существует стереотип о плотности плиты. Считается, чем она плотнее, тем лучше. Но это не совсем так. Плюс этих досок — в бюджетном сырье (низкосортной древесине). К ней относятся «тонкомеры», горбыль, рейки. Главное, чтобы эти материалы отвечали следующим стандартам.
- Фракции стружки не должны быть мелкими.
- Сечение стружки должно быть квадратным, а форма лепестковая. Если нарушить эти требования физико-химические свойства готовой плиты ухудшатся (пострадают изгиб и сопротивление).
ЛДСП имеет широкую цветовую гамму, что широко используется при производстве корпусной мебели.
Часто потребители задаются вопросами: что это за материал такой для кровати — МДФ? Чем отличается МДФ от ЛДСП для мебели? Рассмотрим эти нюансы подробнее.
Пленка представляет собой бумагу, пропитанную меламиновыми смолами, поэтому часто можно встретить и такой термин, как «меламиновая плита».
Преимущества ДСП:
- низкая цена;
- не рассыхается, не расслаивается, не плесневеет;
- благодаря химическим добавкам в плите не живут жучки;
- срок эксплуатации более 10 лет.
Плюсы МДФ:
- приемлемая цена для потребителей со средними доходами;
- прочность;
- влагостойкость;
- включает все вышеперечисленные плюсы ДСП.
ЛДСП можно мыть и чистить — он влагоустойчив.
Выбор материала зависит от того, что планируется изготовить. ЛДСП можно использовать в изготовлении мебели, предназначенной для офиса, дома, магазина, супермаркета. МДФ лучше выбрать для детской мебели.
Высокие температуры ему также не страшны.
Производство древесноволокнистых плит позволяет изготавливать продукцию по доступным ценам для различных интерьеров. Благодаря мебели МДФ и ЛДСП каждый дом будет наполнен уютом, теплом и комфортом.
Его достоинством, помимо всего вышеперечисленного, считается его великолепная возможность имитировать различные текстуры, чаще всего — имитация фактуры дерева.
Обращайте внимание на нормы содержания формальдегида в корпусной мебели.
ВИДЕО: Мебель из дерева или мебель из ЛДСП.
Производство мебельной продукции – это весьма прибыльный бизнес, который занимает второе место после строительной отрасли. Однако этот сегмент на данный момент очень занят, поэтому новичку потребуется много сил, чтобы эффективно войти на рынок.
Если встает вопрос о том, как начинают бизнес, стоит сказать, что многие предприниматели отказываются верить, что намного выгоднее оказывается производить сырье для мебельной промышленности, чем готовую продукцию. На данный момент ламинированное ДСП (ЛДСП) представляет собой весьма популярный материал, который активно применяется не только для изготовления мебели, но и для различных внутренних работ по отделке.
Конечно, ЛДСП по ряду параметров уступает древесине, но легкость в обработке и дешевизна – это основные его преимущества, поэтому данный материал с каждым годом пользуется все большим спросом.
Если вы решили организовать производство ЛДСП, то должны знать еще об одном преимуществе такого решения: на данный момент у вас будет незначительное количество конкурентов на рынке. Результатом этого можно назвать прорисовывание крупного рынка сбыта, так как почти все мебельные фабрики готовы закупать материалы для производства своих изделий.
Производство ЛДСП – грамотная организация бизнеса
Даже ребенок понимает, что для изготовления чего-либо требуется специализированное оборудование. В данном случае оно тоже нужно. Производство ЛДСП невозможно организовать без следующих инструментов:
- Специальная сушильная машина. С ее помощью изготавливается ламинированная бумага.
- Пресс. С его помощью осуществляется запрессовывание ДСП с такой бумагой.
- Калибровально-шлифовальный станок (он оказывает влияние на качество поверхности, получаемой в результате).
Итак, необходимо не только основное оборудование для ламинирования ДСП, но и сопровождающее. В первую очередь можно говорить о приборе, предназначенном для приготовления клеевой основы, которая далее разливается по формам и прессуется в плиты.
Основа ЛДСП
ДСП, или древесно-стружечная плита, представляет собой достаточно востребованный строительный материал, а также основу ЛДСП, используемого для производства мебели. ДСП активно применяется в таких сферах:
- при сооружении напольных покрытий;
- в процессе конструирования разнообразных стеновых панелей;
- для производства мебели, как уже было указано;
- в качестве материала обшивки крыш.
Такое производство вполне можно назвать перерабатывающим, так как в качестве основного сырья для изготовления таких плит служат отходы от древесных предприятий.
Способы производства
Древесно-стружечные плиты могут изготавливаться одним из двух способов – периодическим и непрерывным. Периодический способ предполагает использование этажных процессов периодического давления, а непрерывный – экструкционные процессы.
Особенности изготовления ДСП
Производственный процесс в данном случае моно разделить на ряд основных этапов:
- Подготовительный. На этом этапе осуществляется подготовка сырья посредством дробления древесины для получения стружки требуемых размеров. Если приобретать сразу готовое сырье, то данный шаг вполне можно пропустить.
- Второй этап предполагает смешивание стружки со связующим веществом, в качестве которого традиционно используется клей. Очень важно придерживаться строгих пропорций, так как при излишке клея можно получить изделие, имеющее ухудшенные технические свойства, в связи с чем такие плиты будут считаться бракованными.
- Далее заготовленная смесь помещается в специальные формы, которые потом запрессовывают. Влияние таких факторов, как давление и достаточно высокая температура, позволяют материалу схватиться, чтобы получилось единое целое.
- Далее полученные заготовки помещают в специальную камеру для просушки.
- После этого наступает этап обрезки краев плит.
- Заключительным шагом является шлифование плиты.
Организовать производство можно в складском помещении, где вы сможете установить не только линию по изготовлению ДСП, а в последующем и ЛДСП, но и стенды, на которых будет храниться готовая продукция.
Необходимое оборудование
Если рассматривать вариант производства, когда на вашем предприятии осуществляются все операции, начиная с заготовки самого сырья, то потребуется целый ряд приборов и станков.
Подготовка сырья подразумевает наличие таких приспособлений:
- оборудование, перерабатывающее бревна в щепки;
- сушильные камеры для щепок;
- строгальный станок;
- вибросито.
Процесс производства материала подразумевает вовлечение такого оборудования:
- аппарата, предназначенного для смешивания стружки и связующего вещества;
- формы, где будут заготавливаться плиты;
- термопресса;
- сушки или охладителя для продукции, готовой к дальнейшей обработке.
Для реализации завершающего этапа вам понадобятся:
- распилочный станок, с помощью которого вы будете придавать листу какие-то определенные размеры;
- станок, который производит шлифование торцов;
- устройства, посредством которых производится грубая и тонкая шлифовка.
Изготовление ЛДСП потребует вовлечение в процесс пресса, который наносит двустороннюю ламинацию. Возможно, вам потребуются аппараты для транспортировки, к примеру, ленточные или роликовые.
О ламинировании
Изначально производство и ламинирование плит ДСП представляло собой весьма трудоемкий процесс, который требовал колоссальных энергозатрат. Почти 30 лет назад были освоены совершенно новые типы смол, с помощью которых удалось начать применение новых процессов для ламинирования плит.
В ходе производства очень важно максимально равномерно распределять нагрузку, что позволяет существенно повышать качество плиты. Изделие, изготовленное таким способом, может выдерживать большое количество деформаций и нагрузок, что очень важно.
Варианты того, как правильно ламинировать бумагу, разрабатывались долги годы, но теперь решение найдено, и оно весьма эффективное. Бумага изготавливается в пропиточных машинах, где проводится ее обработка смолой, что позволяет получить из нее декоративную пленку, под прессом становящуюся пластикоподобной.
Ламинированная древесностружечная плита (ЛДСП) – это основной компонент для производства корпусной мебели, который достоверно имитирует натуральную древесину , но обходится во много раз дешевле .
Дешевизна обусловлена использованием отходов деревообработки — стружки.
Производство ЛДСП имеет несколько основных технологий.
- что такое ЛДСП;
- чем производство ЛДСП отличается от производства ДСП;
- какие документы регламентируют качество ЛДСП в России;
- какое оборудование применяют для ламинирования;
- как изготавливают кромочную ленту;
- как ламинируют ДСП самостоятельно.
ЛДСП – это обычная древесностружечная плита , о которой мы рассказывали , облицованная декоративным покрытием .
Покрытие может быть, как одноцветным и гладким, так и разноцветным или имитирующим текстуру древесины.
Основные характеристики, такие как:
- прочность на изгиб;
- способность удерживать шуруп;
- плотность;
- классы влагостойкости;
- класс эмиссии формальдегида;
- горючесть
полностью соответствуют этим же характеристикам исходного материала.
Толщина ламинированного материала зависит от его назначения. Для изготовления корпусной мебели чаще всего берут ЛДСП толщиной 16 мм , однако крышки столов часто делают из плиты толщиной 25–38 мм .
ЛДСП для облицовки стен, пола и потолка изготавливают из ДСП толщиной 8–12 мм .
Ламинирующий слой с объемным рисунком увеличивает толщину древесно-стружечной плиты, ведь такой рисунок создают с помощью прессования основного слоя , продавливая на нем контуры рисунка.
Наружная пленка лишь повторяет контуры этого рисунка.
Как делают ЛДСП?
Для изготовления ЛДСП используют обычные шлифованные древесностружечные плиты, поэтому их выпускают на заводе по производству ДСП, подключив участок ламинирования .
Причем для покрытия исходного материала ламинирующей пленкой применяют 3 технологии:
- ламинирование;
- каширование;
- гладкое ламинирование.
Ламинирование
При ламинировании на основу наклеивают 1–2 слоя специально подготовленной бумаги , причем первый слой — основу — делают максимально толстым, чтобы в нем можно было продавить рисунок.
Толщина основы, в зависимости от глубины рисунка, может достигать 0,5–1 мм, толщина второго слоя составляет десятые, а то и сотые доли мм.
Поверх этих слоев укладывают еще один, изготовленный из прозрачной бумаги и смеси различных смол, которые при нагреве превращаются в прочную пленку , надежно защищающую декоративную поверхность.
На подготовленную поверхность ДСП укладывают основной слой и придавливают его горячим штампом с подходящим рисунком.
Температура поверхности штампа составляет 150–220 градусов, благодаря чему пропитывающая основной слой смола смешивается со смолой, склеивающей стружку в ДСП и, бумага становится неотделимой частью плиты .
Затем таким же образом наклеивают декоративный слой с подходящим рисунком и наружный слой, обеспечивающий защиту плиты от повреждений.
На некоторых предприятиях все слои покрытия сначала соединяют друг с другом, затем сушат и, только после этого крепят к ДСП.
При такой технологии покрытие делают в виде ленты. Рисунок на нем формируют с помощью цилиндра с установленной матрицей, аналогично формированию рисунка при кашировани.
Разница с кашированием в том, что ленту крепят без клея, прогревая пропитывающие бумагу смолы до расплавления и смешивания со смолой в ДСП.
Каширование
При кашировании сначала подготавливают облицовочный материал, для чего все слои укладывают по порядку и пропечатывают на них рисунок с помощью холодного пресса .
При этом незастывшая смола различных слоев смешивается, благодаря чему покрытие превращается в широкую и длинную ленту.
Если для печати рисунка применяют цилиндрический штамп , то возникает возможность делать ленты любой длины .
Многие небольшие предприятия, производящие ламинат с объемной текстурой, предпочитают не тратиться на дорогостоящее оборудование , необходимое для изготовления ленты, а покупать уже готовый материал.
Готовую ленту отправляют в сушилку, затем сматывают в рулоны, которые поставляют на участок каширования. Там облицовочный материал обрезают по размеру и укладывают на смазанную специальным клеем плиту, затем придавливают прессом и прогревают до тех пор, пока клей полностью не полимеризуется.
Благодаря этой технологии облицовка проходит быстрее , ведь не приходится прогревать каждый слой покрытия отдельно , поэтому предприятие может производить больше продукции.
Минус этой технологии в том, что приклеенная облицовка держится гораздо слабей , чем настоящее ламинирование.
Гладкое ламинирование
Эта технология сходна с кашированием , однако является полноценным ламинированием, ведь при нагреве смола покрытия и плиты смешиваются, образуя единый материал. Кроме того, на участке подготовки ленты нет пресса для создания рисунка .
Для создания гладкой поверхности достаточно уложить 2 слоя, нижний из которых будет сделан из бумаги , а верхний — из специальной пленки, которая при нагреве образует прочное и прозрачное покрытие .
Благодаря тому, что крупные производители ЛДСП постоянно ищут способы увеличения технологичности производства и снижения затрат, в этот процесс постоянно вносят различные изменения, суть которых производители держат втайне. Ведь любое улучшение качества ламинирующего покрытия, равно как и снижение затрат, делает их продукцию более конкурентоспособной.
Документы, регламентирующие качество
Основной документ, регламентирующий качество и характеристики ЛДСП в России – это ГОСТ Р 52078-2003 , который вы сможете найти по этой ссылке .
Существует и международный стандарт EN 14322:2004 , который во многом сходен с российским. Его вы можете найти .
Эти стандарты отличаются от принятых в отношении ДСП только требованиями к ламинирующему покрытию. Во всем остальном они полностью идентичны .
Кроме того, существуют различные ТУ (технические условия), которые разрабатывают как производители ламинированных древесностружечных плит, так и производители мебели. В ТУ прописывают те требования, которые не вошли в общепринятые стандарты или по каким-то причинам выбиваются из них.
К примеру, в ТУ могут быть прописаны нестандартные размеры продукции , а также указан подробный состав клея , отличающийся от того, что предприятие использует при производстве обычного ДСП.
Оборудование: завод и его составляющие
В большинстве случаев для ламинирования ДСП используется многофункциональное устройство, которое называют ламинатор . Его основа – мощный пресс с паровым или масляным нагревом плиты, а также с возможностью установки матриц с необходимым рисунком.
Ламинатор может быть большим, способным обрабатывать листы максимального размера, а также средним или маленьким. Если установлен большой пресс, то после охлаждения ламинированный лист поступает на раскроечный станок, полностью аналогичный тому, что применяют при производстве ДСП.
Кроме того, ламинатор бывает одно- или двухсторонним , то есть наклеивать пленку только с лицевой стороны или одновременно обрабатывать лицевую и заднюю плоскости.
Прессы среднего размера предназначены для ламинирования уже нарезанных плит, размер которых соответствует требованиям ГОСТ Р 52078-2003 и EN 14322:2004.
Малый пресс предназначен для ламинирования готовых деталей, например, входных и межкомнатных дверей или мебельных элементов. Поэтому предприятию следует выбирать ламинатор исходя из ассортимента продукции.
Кроме того, вместе с большим или средним ламинатором нередко используют линию по укладке ленты, которая также выполняет несколько функций:
- определяет качество подготовки поверхности ДСП к дальнейшей обработке;
- укладывает ленту на плиту и правильно ориентирует ее;
- обрезает излишки ленты.
На предприятиях, где установлены малые ламинаторы, эту операцию обычно выполняет специально подготовленный работник высокой квалификации , укладывающий и обрезающий ленту вручную. Чаще всего так поступают на мебельных фабриках, когда приходится изготавливать детали, которые по каким-то причинам нельзя вырезать из целого листа.
Похожим образом поступают и на крупных деревообрабатывающих цехах или производствах, изготавливающих не только мебель, но и различную столярную продукцию .
Ламинатор можно использовать не только для ламинирования, но и для обычного приклеивания, поэтому нет смысла тратиться на специальную линию .
Нередко среднюю и малую плиту после охлаждения подают на раскроечный станок, который отрезает 1–2 мм плиты, формируя ровную кромку. Такой станок оснащают дисковыми пилами большого диаметра с напайками из твердых сплавов или с алмазным напылением.
Перемещают плиты по всей линии с помощью ленточных транспортеров и вакуумных подъемников, причем все операции происходят в автоматическом режиме .
Стоимость оборудования зависит от многих факторов, поэтому большинство предприятий, выпускающих такие линии и отдельные станки, озвучивают цену только после предоставления заказчиком конкретных требований по конфигурации и производительности.
На Алиэкспресс и других площадках можно встретить отдельные устройства и целые линии с указанием примерной стоимости без учета доставки и монтажа.
Средний односторонний ламинатор для плит размером 1220*2440 мм можно приобрести за 100–200 тысяч долларов США , а линия подачи ламинирующей ленты шириной 60–120 см обойдется в 18–25 тысяч долларов США .
Кромочная лента
При изготовлении ЛДСП ламинируют только лицевую и обратную поверхности, а кромки остаются без покрытия . Поэтому предприятия, выпускающие ЛДСП, вместе с ней поставляют и кромочную ленту , которую используют для самостоятельного ламинирования торцов.
Цвет ленты полностью соответствует цвету плиты, поэтому после наклейки ленты вся плита становится одноцветной.
Ленту для кромления, то есть оклейки кромок, делают заметно тоньше, чем ту, что применяют при облицовке древесностружечных плит на производстве. Ведь в условиях мебельной мастерской невозможно создать настолько высокое давление и большинство мастеров обходится обычным утюгом , прогревая им уложенную на кромку ленту.
Как ламинировать ДСП самостоятельно?
Не всегда ЛДСП, которую можно приобрести в магазинах, подходит по цвету или рисунку , поэтому можно облицевать плиту самостоятельно.
Для этого хорошо подойдут различные виды декоративных пленок, которые продают в строительных магазинах.
Пленки бывают самоклеящимися и обычными .
Для нанесения самоклеящейся пленки с нее снимают тонкое защитное покрытие и укладывают на очищенный от грязи и пыли лист ДСП, затем прокатывают валиком, удаляя пузырьки воздуха.
Для нанесения обычной пленки применяют специальный клей, рекомендованный производителем пленки, затем выжидают 2–5 минут и аккуратно накладывают пленку, не допуская появления складок .
Такие способы позволяют наклеивать на ДСП лишь те рисунки, которые есть в магазине, поэтому можно использовать метод, который применяли во времена СССР , когда ЛДСП была в огромном дефиците.
На очищенную от пыли и грязи поверхность ДСП наносили тонкий слой грунтовки (ПВА, разбавленный водой в соотношении 5:1). Затем на листах альбомной бумаги делали желаемый рисунок и с обратной стороны грунтовали ПВА.
Через 2–4 дня, когда клей полностью застыл, листы с рисунком раскладывали на поверхности ДСП так, чтобы собрать рисунок воедино. Затем каждый лист прогревали с помощью утюга.
Если все листы были правильно уложены и прогреты, то после охлаждения они образовывали сплошной рисунок, полностью покрывавший всю поверхность плиты.
Однако сдвиг любого из листов приводил к нарушению рисунка и портил всю картину, поэтому для большей надежности старались достать не альбомную, а типографскую бумагу, которая превосходила плиту по размерам.
Готовый рисунок покрывали мебельным или паркетным лаком в 2–3 слоя и получали самодельный ламинат с невысокой прочностью покрытия , зато с необходимым рисунком.
Видео по теме
На этом видео можно увидеть работу завода по производству ЛДСП:
Вывод
Производство ЛДСП – это сложный процесс, включающий в себя много операций, поэтому для превращения обычных древесностружечных плит в ламинированные необходим участок с хорошим оборудованием .
Прочитав статью, вы узнали, как происходит процесс ламинирования и можно ли его сделать самостоятельно.
Вконтакте
Технология ламинирования и каширования ДСП. Производство ламинированного ДСП. Декоративное покрытие мебельных плит. Для использования ДСП в мебельном производстве шлифованное ДСП
подвергают декоративной обработке — наносят декоративное покрытие из бумажно-слоистых (меломиновых) пленок. На этом участке производства шлифованное ДСП превращают в ламинированное, в ЛДСП. Производство ЛДСП предсставляет собой процесс облицовки шлифованных плит ДСП пленками на бумажной основе (бумажно-слоистыми плёнками). Существует два способа декоративной обработки плит ДСП бумажно-слоистыми пленками:
Основное различие между ламинированием и кашированием плит ДСП в том, что при ламинировании декоративное покрытие создается при прессовании химическим путем и является составляющим плиты, а при кашировании к плите приклеивается уже готовая твердая бумажная-смоляная пленка. Ламинирование ДСП.Ламинирование ДСП — это процесс покрытия поверхностей плиты бумажно-смоляными плёнками, пропитанными смолами. Комплексное воздействие
давления (25-28 МПа) и высокой температуры(140-210 ̊ С) способствует тому, что
пленка практически «врастает» в поверхность ДСП. Само слово «ламинирование»
(lamination) имеет английское происхождение и переводится как «расслоение, раскатка, напластование». Линия ламинирования ДСП, производство Китай. (фото с сайта: china1.ru) Линия быстрого ламинирования. (фото: elo.ru ) Составляющие линии: Каширование ДСП.Каширование ДСП — припрессовывание отвержденной пленки к древесностружечной плите. По всей поверхности плиты наносят слой клея и к этому слою припрессовывают твердую декоративную пленку. Процедура каширования плит ДСП проходит при более «мягких» условиях, чем при ламинировании: под давлением в 5-7 МПа и при температуре 120 -150 ̊С. Термин «каширование» имеет немецкие корни и произошло от немецкого Kaschieren, которое означает «оклеивать бумагой». (фото с сайта: izoplit.ru)Видио процесса каширования какого-то плитного материала на одной из китайских фабрик. Кашированные панели ДСП толщиной 10 мм.
Упаковка плит ДСП на паллеты. В соответствии с требованиями стандарта плиты сортируются, а затем или раскраиваются на заготовки для мебельных щитов, или отправляются потребителям полноформатными. В зависимости от критериев внешнего вида плиты (трещины, сколы, окрашивание, пятна, выступы и углубления) плиты ЛДСП делятся на следующие сорта:
Меламиновая плёнка для облицовки ДСП.Меламиновые плёнки – современный облицовочный материал на основе декоративных бумаг различной плотности (однотонных или с печатным рисунком), пропитанных аминоформальдегидными смолами с неполной степенью поликонденсации. (фото с сайта: bimma.ru) Чтобы получить меламиновую пленку необходимо пропитать специальную декоративную
бумагу смолой. Пропитка происходит в несколько приёмов. На пропиточной машине происходит сначала нанесение смолы валиком на нижнюю сторону полотна, а потом
бумага полностью погружается в смолу, находящуюся в ванне. Между первой и второй ступенями пропитки бумага проходит зону «пенетрации». После первой пропиточной машины бумага сушится, в результате чего происходит удаление летучих веществ. Затем полотно поступает во вторую пропиточную машину. Там слой меламиноформальдегидной смолы наносится на обе стороны бумажного листа. Целью нанесения второго слоя смолы, является придание верхнему слою повышенных свойств текучести при прессовании, а также придание облицовочной поверхности гладкости и повышенной прочности. Затем бумага поступает в другую сушилку, имеющую три зоны обогрева и одну зону охлаждения. Попадая в зону охлаждения, полотно пленки поступает на
роликовый транспортёр (рольганг), валы которого охлаждаются водой. Так бумага превращается в плёнку. После этого пленка режется на листы заданного размера.
Эти листы пленки укладываются на листоукладчике в стопы и упаковывается. |
Мебель из МДФ или ДСП. Что лучше?
49764 Просмотра ,
БОльшая часть современной мебели производится из МДФ и ЛДСП. Тем не менее, многие даже не знают, что они из себя представляют и чем отличаются. Мы расскажем вам об основных отличиях древесных плит коротко и просто.Как отличить МДФ от ДСП?
Во-первых, разберемся, как эти названия расшифровываются.

Производство ДСП? Как определить качество?
Для производства ДСП опилки и стружку спрессовывают и для склейки пропитывают формальдегидными смолами, а получившуюся плиту обычно ламинируют меламиновой пленкой. Буква «Л» в начале аббревиатуры указывает на то, что ДСП ламинированное. Пленка не только защищает плиту от влаги и других внешних воздействий, но и препятствует выделению формальдегида во внешнюю среду .
Существует классификация безопасности ЛДСП, основанная на концентрации формальдегида:
- Е1 – класс эмиссии формальдегида, считающийся безопасным для производства мебели (такая плита изготовлена по Европейским стандартам;)
- Класс Е2 — категорически запрещен для использования в производстве детской мебели;
- Класс Е 0,5 – также соответствует Европейским стандартам качества.
Однако в его использовании не всегда есть необходимость, поскольку пленка препятствует испарению вредного соединения;
- E 3 – категорически запрещен для использования в производстве.
Как производят МДФ? Как определить качество?
Для производства МДФ дерево измельчают, высушивают и спрессовывают. Лигнит — натуральное вещество, содержащееся в древесине – связывает частички дерева между собой вместо смол. Формальдегидов в МДФ практически нет, и по химической безопасности материал максимально приближен к натуральной древесине. Для защиты на него наносят пленку ПВХ, шпон или эмаль.На фото ниже — ДСП фирмы EGGER, используемое нами на производстве:
Что прочнее – МДФ или ДСП?
МДФ плотнее не только ДСП, но и цельного массива. Этот материал «не боится» высокой влажности, поэтому подходит для использования в ванной или кухне.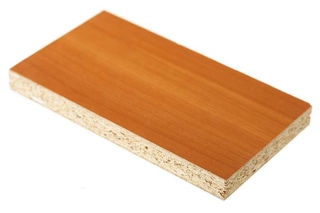
ДСП менее прочен, чем массив и МДФ. В ванных комнатах и на кухне его использовать не рекомендуют, поскольку через порезы и отслойки на пленке влага может просачиваться внутрь. Это вызывает набухание, изменение формы и еще больше снижает прочность.
Что дешевле МДФ или ДСП и почему?
МДФ в полтора-два раза дороже, чем ДСП, и применяется для сегментов «премиум» и «люкс». Продукция эконом-сегмента производится всегда из ЛДСП. На конечную стоимость продукции может влиять отделочный материал. Самые бюджетные — пленка ПВХ и листовые пластики, несколько дороже выходит эмаль. Самая же дорогая отделка – натуральный шпон.
Какой материал для какой комнаты подходит?
Преимущества МДФ очевидны, однако это дорогой материал, поэтому мебель полностью из МДФ почти не изготавливают.
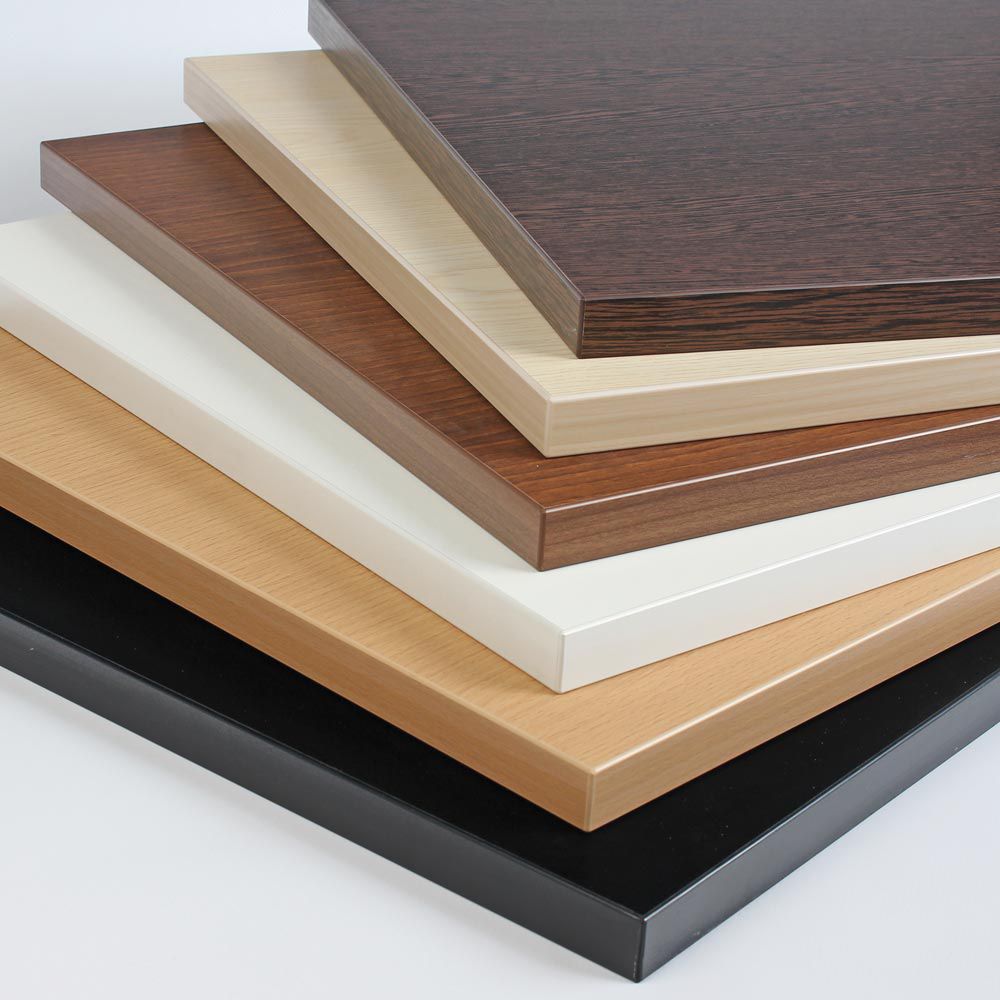
Это позволяет сохранить качество за разумные деньги. Вы не переплачиваете за дорогой МДФ там, где он не нужен.
Так как выбрать материал для своей мебели?
Вот вам наша памятка в виде простых тезисов:
- ЛДСП отлично подойдет для гостиной и прихожей. Только позаботьтесь о том, чтобы плита была качественной. Запросите сертификат, подтверждающий класс плиты.
- Сочетание ДСП и МДФ подойдет для детских и спален, но правило то же: материал должен быть обязательно высокого класса, а изделие – хорошо проклеено, включая кромки и стыки.
- Для кухни и ванной правильнее выбрать МДФ: в этих комнатах наиболее часто подвергается перепадам температуры и влажности.
В чем отличие фасадов ЛДСП и МДФ
Клиенты часто спрашивают в чем отличие таких материалов как мдф и лдсп, давайте разбираться.
Что такое ЛДСП И МДФ?
ДСП И МДФ — прессованные плиты из древесных стружек с примесями смол. Не будем цитировать википедию, точное определение сможете найти в словарях и справочниках.
Как получают ДСП:: берут прессованные опилки и ламинируют различными декорами (под дерево или однотонные).
Как получают МДФ:: берут более экологичную и плотную плиту из прессованных опилок и ламинируют или красят или шпонируют (тонкий натуральный слой древесины разных пород).
В чем отличие? Сравнение по характеристикам МДФ И ДСП
1.Содержание вредных веществ в МДФ ниже, а плотность самой плиты выше, чем у ЛДСП.
2. ДСП более рыхлый материал и менее экологичный, но и более дешевый.
3. Мдф более устойчив к воздействию влаги в силу конструктивный особенностей при прочих равных условиях. То есть ЛДСП — плита с ламинацией сверху и снизу плиты, а по бокам проклеивается кромкой. В эти соединения м/д кромкой и ламинацией может легко проникнуть влага.
4. Декоры МДФ более разнообразны, с учетом того, что МДФ можно красить, то до бесконечности разнообразны. Плюс МДФ можно деформировать и фрезеровать (фрезерованные кухонные фасады).
Фасады из ЛДСП или из МДФ?
Невооруженным и неопытным взглядом сразу не отличить. Давайте научимся! Фасады МДФ цельные с округлыми краями. Фасады ЛДСП с кромкой, можно заметить переход м/д ламинацией и кромкой. Кромка может быть разной толщины, может быть не в цвет самого листа.
Фасады для кухни из ЛДСП
Выбирая, какие фасады установить на вашу кухню, помните, что из ЛДСП дешевле, но вариантов декора меньше. Можно выбрать любой цвет из представленных производителем, скомбинировать их м/д собой или реализовать фасады с алюминиевой рамке (профиле). На этом разнообразие заканчивается.
Фасады для кухни из МДФ
Дороже, экологичнее и больше вариантов дизайна: крашенные, гнутые, с пленкой ПВХ, с фрезеровкой, матовые и глянцевые, с эффектом патины, шпонированные, в рамке МДФ.
Мы можем изготовить любые кухни с фасадами МДФ или ЛДСП. Заказывайте мебель напрямую у производителя без переплат посредникам и перекупам. Свяжитесь с нами и получите полную консультацию по материалам и ценам.
ДСПили МДФ Что лучше для изготовления мебели для хряков с меламиновым покрытием? — Знание
ДСП против МДФ
что такое ДСП
что такое ДСП ламинат? ДСП изделие из древесной щепы облицованное меламином. или другой древесный целлюлозный материал, искусственный картон. после нанесения под действием технологического процесса термического прессования. Листы ДСП также известны как ДСП. цена на древесностружечные плиты, используемые в производстве мебельных плит и строительстве.древесные отходы древесно-стружечные плиты белые, а также производство кузовов поездов и вагонов.
По плотности ДСП: низкая плотность (0,25-0,45 г / см 3), средняя плотность (0,55-0,70 г / см 3). произведена бритвенная доска высокой плотности (от 0,75 до 1,3 г / см 3), от 0,65 до 0,75 г / см 3. В структуре ДСП определение пластинчатого типа делится на однослойное, трехслойное (в том числе многослойное). и структура различных сортов. Водонепроницаемость разделена на водонепроницаемость в помещении.и наружная водостойкая древесно-стружечная плита.
По расположению стружки на плите. его можно разделить на два вида стружки из ДСП и случайной стружки. Также недревесный материал, такой как стебель хлопка, стебель конопли, жмых, рисовая шелуха и т.п. и цементная древесная плита из неорганического связующего материала — цементно-стружечная плита. и т.п. также предоставляются. Толщина ДСП имеет большую спецификацию, толщина от 1.От 6 мм до 75 мм. стандартная толщина 19 мм. и общая толщина составляет 13,16,19 мм.
Преимущества ДСП
Изготовлен из композита горячего прессования. древесных отходов, связанных формальдегидной смолой. ДСП — это плотный строительный материал, который широко используется с 1960-х годов. Подходит для многих применений, включая столешницы, шкафы, двери. полы, вагонка и мебель ДСП плотнее дерева и так прочнее. При облицовке шпоном или окрашивании улучшается ее внешний вид.По сравнению с другими древесноволокнистыми плитами или композитными строительными материалами на древесной основе он слабее.
В настоящее время он дешевле цельной древесины или фанеры. Мебель и другие изделия из дерева. сделано из массива дерева, тогда как считается роскошью. ДСП — предпочтительный материал для недорогих товаров.
Недостатки ДСП
Недостатком ДСП является то, что она может расширяться под воздействием влаги. Использование на открытом воздухе почти никогда не бывает хорошей идеей, даже если оно покрыто герметиком.В ванных комнатах и кухнях. его можно использовать в качестве основного материала, если он покрыт влагостойким винилом.
ДСП мебель
из дерева внешний вид изделия, размер. и форма частиц опилок в центре поперечного сечения. Длина обычно подходит для длины 5-10 мм. структура слишком длинная рыхлая, сопротивление деформации слишком мало. так называемая статическая прочность на изгиб не соответствует стандарту. Влагостойкость древесной плиты зависит от ее плотности.и влагоизоляционный агент. Его нельзя хорошо защитить от влаги в воде. Влагостойкость относится к влагостойким и не водонепроницаемым.
ДСП. поверхность меламина гладкая. вообщем езжу на заводе по поводу светлой наждачки, в целом хорошо. но в некоторых случаях, например, вискозная плита слишком тонкая, висящий клей. 4, от края ДСП. это хорошая кромка из ДСП. Хорошая герметизация кромок может не только снизить количество выделяемого формальдегида.но также стремимся к расширению. влагостойкость ДСП тонкого древесного волокна.
Что такое МДФ?
Что такое МДФ? Обшивка из МДФ — это пигмент из твердых, мягких или других растительных волокон. которые разбиты, отделены, высушены, покрыты карбамидоформальдегидной смолой или другим подходящим связующим. а потом нагревается. Прессованная панель на древесной основе. ДВП средней плотности обычно плотнее фанеры. Хотя состоит из отдельных волокон.из него можно изготавливать тысячи строительных материалов, например фанеру. Кроме того, его прочность и плотность больше, чем у Geneboard. Мебель из дерева МДФ, понятно?
Преимущества листа МДФ
В чем преимущества листа МДФ? Панели МДФ можно использовать разных размеров и толщины. Резка простая и гладкая, без повреждений и трещин. Его края и поверхности позволяют использовать различные случаи глубокого травления желчного пузыря. а глянцевая поверхность идеально подходит для окраски, склейки, ламинирования, фактурной печати.и окраска. Некоторые производители предлагают ряд различных по цене видов плит МДФ). в том числе стандартные, огнестойкие, влагостойкие, наружные и с высокой плотностью. На эти характеристики не влияет резка или механическая обработка.
За счет МДФ высшего качества. эта древесноволокнистая плита стала идеальным сектором производства древесных плит. для мебели, строительства, дорожных знаков, оформления магазинов и других отраслей.
Недостатки панелей мдф
Дороговизна. Чистая необработанная ДВП — 1.В 5 раз дороже ДСП. Цены на декорированную табличку МВД еще выше. особенно в отношении покрытия из высококачественного пластика или эмали. Мягкость. Склонен к образованию вмятин от ударов. Если на поверхность нанесен декор, вряд ли удастся избавиться от некрасивых углублений. Легкий розжиг от открытого пламени.
Как насчет мебели из МДФ
Из-за прочности мебели из МДФ. мягкая ударопрочность, высокая прочность, равномерная плотность после прессования.и простой в переработке, это хороший материал для изготовления зарубежной мебели. Хотя влагостойкость МДФ оставляет желать лучшего, если после раскрутки винт ослабнет, снова исправить его непросто. Но, поверхность массива МДФ гладкая, гладкая. очень хороший материал, стабильная работа, преимущество компании. легко моделируется, избегает гниения, горечи. и другие проблемы, превосходящие ДСП. прочность на изгиб и ударная вязкость поверхности пластины.
Декоративные характеристики очень хорошие, особенно внешний вид мебели из массива дерева.Плотная доска, изготовленная из подходящих отделочных изделий, деревьев. и другие ремесленные изделия путем горячего шлифования, мощения, горячего прессования и погружения в воду. Он сделан из древесного волокна или других растительных волокон. и покрытые карбамидоформальдегидной смолой или другими подходящими связующими. Конечно, жевательная резинка содержит химические вещества как бензола, так и формальдегида.
Прежде всего, он вреден для здоровья и не соответствует национальным стандартам. определенное влияние окажет и широкое использование клеев.по качеству композитных материалов щитового типа. это только увеличит стоимость. Хорошая плита из массива дерева — это плита, которая измельчается твердой древесиной. а затем образуется под действием высокой температуры и высокого давления. Обычно его используют для изготовления мебели из плит средней плотности. Из-за того, что из плиты высокой плотности нельзя делать мебель, ее плотность слишком высока, и ее легко расколоть. Обычно его используют на полу. Но разделять преимущества МДФ легче, чем у мебели из цельного дерева. МДФ практичен и полезен.
Выбор прочности меламина и мдф
В то время как древесноволокнистая плита средней плотности имеет много преимуществ перед ДСП. главный фактор — цена предмета. И это всегда определяет, какой тип платы мы используем для какого приложения. Как правило, в отношении торговых площадей мы настаиваем на том, чтобы покупатели платили немного больше, чтобы получить доменное имя. предмет, который прослужит намного дольше. Использование ДСП или МДФ всегда зависит от того, сколько клиент готов потратить.
Подробнее
Каковы преимущества и недостатки ламината ДСП?
Теги:
ДСП.средняя плотность. МДФ против плотного ДВП. инженерная древесина. производственный процесс. небольшой лес. предметы мебели. обычно используется. удерживайте винты. изделие из дерева. текстура древесины. шпон. древесный композит. Недавние Посты. электроинструменты. множество. натуральное дерево. бюджетный. ориентированная прядь. стружечная плита. доска мдф. повреждение водой. столешницы. держит винты.
Сравнение мебели из массива дерева и ДСП | Руководства по дому
Кэти Адамс Обновлено 14 декабря 2018 г.
Хотя мебель из ДСП может выглядеть как настоящая древесина, для подражания которой она предназначена, особенно если она покрыта деревянным шпоном, который маскирует внутренности, ее сильные и слабые стороны немного отличается от мебели, изготовленной исключительно из массива дерева.Мебель из ДСП во многих случаях является недорогой альтернативой аналогичной деревянной мебели. Чтобы определить лучший тип мебели для вашей комнаты, подумайте, как вы будете ее использовать и в каких условиях она будет находиться.
Superior Points из массива дерева
Мебель из качественного дерева с красивой текстурой, резными деталями или даже инкрустацией — впечатляющий декор в любой комнате, не имеющий себе равных даже с самой красивой мебелью из ДСП. Твердая древесина имеет прочность, которая выдерживает испытание временем, особенно если изделие изготовлено из твердой древесины, такой как клен.Настоящая древесина выдерживает модификации, такие как распиловка ножек или перемещение оборудования, в то время как ДСП может развалиться, если просверлить или распилить. Прочная конструкция, такая как соединения типа «ласточкин хвост», скрепляет деревянную мебель вместе, в то время как части ДСП могут быть скреплены клеем, скобами или шурупами.
Неудачи из массива дерева
Мебель из массива дерева, особенно из редких или красивых пород дерева, таких как эбеновое дерево, капиллярный клен или европейский бук, может быть довольно дорогой, потому что сама древесина дорогая.Большой кусок твердой древесины, например, столешница из одной широкой доски, со временем может деформироваться, так как многие породы дерева расширяются и сжимаются при изменении влажности.
Преимущества древесностружечных плит
Помимо того, что они обычно дешевле, чем аналогичные изделия из цельной древесины, мебель из древесно-стружечных плит имеет несколько положительных качеств. Он не будет деформироваться, расширяться или сжиматься, как натуральное дерево, до тех пор, пока исходный ламинат не поврежден. Он довольно прочен при регулярном использовании и не вмятин так же легко, как некоторые мягкие породы дерева, такие как сосна.Он также поддается покраске, поэтому, если вы не заботитесь о существующем шпоне, загрунтуйте его грунтовкой, предназначенной для ламината, а затем покрасьте мебель по своему вкусу.
Недостатки ДСП
Мебель из ДСП, если рассматривать ее бок о бок с аналогичной версией из массива дерева, при ближайшем рассмотрении может выглядеть не так хорошо. Дно и задняя часть ящиков предметов для хранения может быть изготовлена из непрочных материалов. Если какая-либо часть ламината или фанеры отслаивается, открытая ДСП начинает крошиться.Если основа куска ДСП намокнет и ламинат повредится, ДСП впитывает воду, ведя себя больше как слои влажного гофрированного картона, увеличиваясь в несколько раз по сравнению с первоначальным размером. Если вода повреждена до такой степени, сама древесно-стружечная плита не подлежит ремонту. Длинное открытое пространство из ДСП, такое как полка на книжном шкафу, достаточно хрупкое, чтобы его можно было сломать.
Что лучше чернового пола из фанеры или ДСП?
Если вы планируете улучшить черновой пол слоем фанеры или ДСП, вы можете спорить, что будет более эффективным.В этой статье мы надеемся, что сможем помочь вам принять правильное решение для вашего проекта, проведя вас через различные этапы. Вот что мы рассмотрим: ü Что такое фанера? ü Что такое ДСП? ü Что дешевле? ü Что лучше? ü Один лучше подходит для паркетного пола, чем другой? ü Один лучше подходит для полов из массивной древесины, чем другой? ü Что проще установить? ü Как вы решаете? Что такое фанера? Фанера, как следует из названия, представляет собой изделие из дерева, которое состоит из тонких слоев или слоев шпона, которые склеиваются вместе, образуя своего рода многослойный деревянный сэндвич.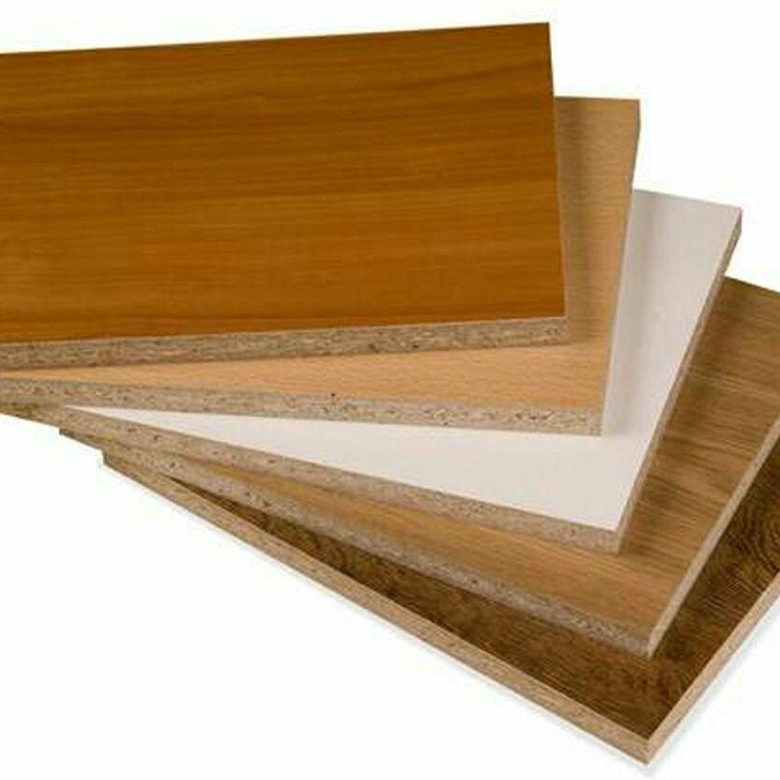



МДФ против ДСП | Популярный журнал Woodworking
Мы можем получать комиссию, когда вы используете наши партнерские ссылки. Однако это не влияет на наши рекомендации.
Как два разных дерева могут быть и благословением, и проклятием.
Карен Накамура
Дешево, однотонно и определенно не из дерева. Именно так многие плотники описывают ДСП и МДФ (древесноволокнистую плиту средней плотности), но вместо этого думают этими словами: недорогие, однородные и стабильные.
- Недорого. Панели из МДФ и ДСП стоят от 25 до 35 долларов за лист (крупногабаритный — 49 на 97 дюймов, чтобы можно было отрезать потрескавшийся край).
- Униформа. Панели МДФ и ДСП, которые вместе называются композитной древесиной, не имеют неровностей, характерных для фанеры со шпоном, таких как пустоты внутри и пятна на внешней стороне.
- Конюшня. Композитная древесина не сжимается, не набухает по волокнам и не коробится в такой же степени, как цельная древесина.
Композитная древесина имеет несколько существенных недостатков: она тяжелая, легко повреждается и не очень жесткая. Кроме того, он не удерживает винты так же хорошо, как массив дерева, разбухает при намокании и создает облака неприятных опилок. ДСП подходит для утилитарных работ, но для мебельных проектов предпочтительнее МДФ. МДФ более гладкий, лучше воспринимает детали, лучше держит шурупы и очень хорошо окрашивается после герметизации краев.Какую бы из них вы ни выбрали, используйте только твердосплавные фрезы, потому что связующие в древесине очень абразивные. Даже карбид изнашивается быстрее, чем обычно. Здесь мы рассмотрим только основы, но огромное количество бесплатной технической информации о различных сортах композитной древесины можно получить от Совета по композитной древесине. Вы можете загрузить целые брошюры на сайте www.pbmdf.com или по телефону (301) 670-0604.
МДФ против ДСП против настоящего дерева
У МДФ более четкие края, чем у ДСП.МДФ состоит из очень мелких древесных волокон, почти как мука, а ДСП — из более крупных и грубых волокон. ДСП имеет тенденцию к отслаиванию при фрезеровании. Если вы хотите, чтобы у ДСП были четко очерченные края, приклейте полоску из массива дерева. |
Черт, это тяжелая штука! Проекты из МДФ и ДСП могут весить до тонны.![]() |
МДФ и ДСП очень плоские. Они идеально подходят для облицовки, потому что на очень тонких листах шпона нет комков или ряби. Приклейте шпон с двух сторон, чтобы панель не деформировалась. | |
Он может быть плоским, но не жестким.Выглядит знакомо? Полки из МДФ и ДСП печально известны тем, что они свисают даже от собственного веса, если у них нет дополнительной опоры. Полки 10-дюйм. глубина должна быть не более 24 дюймов. длинная. | |
Толщина МДФ обычно невысока. В отличие от фанеры, которая обычно бывает заниженной, МДФ и ДСП часто укладываются прямо в пазы стандартного размера.![]() | |
МДФ идеально подходит для кондукторов. Он плоский, гладкий, одинаково стабильный по длине и ширине, изготовлен с точной толщиной, разрезается и формируется без сколов. Кроме того, в нем можно просверливать точно расположенные отверстия, поскольку нет волокон, отклоняющих сверло. Этот зажим используется для заточки долот с наждачной бумагой на сверлильном станке и был описан в AW № 98, январь 2003 г., стр. 62. | |
Тонкий МДФ удобен для выкройки. МДФ бывает 1/4 дюйма и 1/2 дюйма. листы, хотя вам, возможно, придется заказать их через лесной склад. МДФ легко шлифовать, особенно когда он тонкий. 1/4 дюйма МДФ — лучший материал для выкройки, чем фанера, потому что его края более гладкие, но он недостаточно прочен, чтобы образовывать длинные и тонкие узоры.![]() | |
Шаблоны для фрезерования из МДФ имеют прочные края.Лучше всего подойдет МДФ толщиной 1/2 дюйма. Он имеет большую опорную поверхность, чем 1/4 дюйма. материал, и его легче шлифовать для придания формы, чем 3/4 дюйма. материал. Вот здесь идеально ровная кромка шаблона действительно помогает создавать дубликаты деталей, требующие небольшого шлифования. | |
В композитной древесине легко появляются трещины, если вы срежете углы и не просверлите пилотное отверстие для шурупа. Это создает проблемы для несущего стыкового соединения.Из крошечных трещин приходят большие неудачи! Короткие шурупы с мелкой резьбой плохо держатся за края композитной древесины. | |
Длинные винты и закрытые соединения лучше всего подходят для полок. Обязательно наличие глубокой резьбы на винтах.![]() | |
Мокрые полы подвала или гаража наносят ущерб МДФ и ДСП.Волокна обоих видов древесины впитывают воду и расширяются, как губка. Однако, когда материал высыхает, он не садится обратно. Вместо этого появляются крошечные трещинки, ослабляющие древесину. Если этот кусок сдвинуть, нижний край рассыпется. | |
Поднимите корпус над мокрым полом с помощью ножек из массива дерева. Здесь мы использовали пропитанные под давлением пиломатериалы (чтобы ножки не гнили, даже если они оставались влажными), приклеили и прикрутили их к корпусу водостойким желтым клеем.Клеевой барьер предотвращает впитывание воды корпусом.![]() | |
Опасны ли МДФ и ДСП для вашего здоровья?Формальдегид и пыль представляют собой серьезную проблему для композитной древесины. Перечисленные здесь стратегии могут ограничить вашу подверженность обеим проблемам. Формальдегид используется в клеях и связующих для композитной древесины и медленно выделяется из всей панели в виде газа.Многие производители снизили выбросы формальдегида за последние несколько лет, но у некоторых людей возникают аллергические реакции даже на небольшие количества. Есть три вещи, которые вы можете сделать с выбросами формальдегида: • Покупайте панели с низким содержанием формальдегида (для одного такого продукта см. Источник ниже). • Проветрите композитные панели в гараже или сарае на несколько недель. • Заделайте формальдегид, покрыв все поверхности вашего проекта краской, лаком или ламинатом. Как хорошо знают плотники, композитная древесина создает гигантские облака из очень ценных пород дерева и вяжущей пыли. МДФ — худший нарушитель. Эта пыль не только раздражает, но и длительное воздействие может привести к респираторным заболеваниям. Защитите себя с помощью трех уровней защиты от пыли: • Соберите пыль у источника с помощью любого типа вакуумного шланга, который вы можете установить. • Всегда носите маску. Ищите маски NIOSH N95 с двумя ремнями и зажимом для носа для плотного прилегания. • Не позволяйте пыли оседать на вашем магазине и доме, улавливая ее в скруббере верхнего воздуха. | |
Эта история впервые появилась в журнале American Woodworker, январь 2004 г., выпуск № 105.
Исходная информация могла быть изменена с момента первоначальной даты публикации.
Источник
Dow BioProducts Ltd. , (800) 441-4DOW www.dow-bioproducts.com Древесноволокнистая плита (с низким содержанием формальдегида).
Рекомендации по продукту
Вот некоторые расходные материалы и инструменты, которые нам необходимы в повседневной работе в магазине. Мы можем получать комиссию с продаж по нашим ссылкам; однако мы тщательно отбирали эти продукты с учетом их полезности и качества.
В чем разница между ДСП и фанерой?
Иногда мы сталкиваемся с проблемой выбора между различными материалами для одной и той же задачи или мебели. Вы должны учитывать очень много вещей, таких как стоимость, долговечность, эстетика и так далее.Фанера и ДСП — аналогичные типы материалов, которые можно использовать в качестве альтернативы, а может и нет. Использование или применение любого из этих материалов зависит от множества факторов. Хотя оба материала доступны в виде одинаковых листов и разной толщины, вы можете не знать, как каждый из них можно использовать дома. Вот сравнение ДСП и фанеры.
Что такое ДСП?
Изготавливается путем прессования древесной стружки вместеДСП — это материал на основе древесины, который изготавливается путем прессования древесной стружки с помощью клея.Древесная стружка в поверхностном слое тоньше, чем в среднем слое, поэтому поверхность ДСП более плотная и компактная, чем в середине. Количество клея, используемого в ДСП, составляет 10%.
Преимущества ДСП
ДСП имеет легкий весТеперь, когда вы знаете, что такое ДСП, важно четко различать преимущества ДСП по сравнению с фанерой. ДСП имеет массу преимуществ, которые могут сделать ее идеальным выбором для многих вещей.
- Поверхность ДСП обычно более гладкая, чем у фанеры.
- ДСП изготавливаются из обрезков других пиломатериалов, что делает их экологически чистыми.
- ДСП очень легкие. Мебель из этих плит относительно легко транспортировать и перемещать.
- ДСП определенно более рентабельно, чем фанера
Недостатки ДСП
ДСП может быть не очень прочнымТеперь, когда вы знаете о преимуществах использования ДСП в интерьере, вы должны знать, что это не идеально.Использование ДСП в домашних условиях по сравнению с фанерой имеет много недостатков. Посмотрим на некоторые из них:
- По сравнению с фанерой, древесно-стружечная плита не считается очень прочной или долговечной
- Более мягкий и хрупкий состав древесностружечных плит делает их склонными к повреждениям
- ДСП теряет большую часть своей прочности под действием влаги и набухает
- ДСП может быть токсичным. В производственном процессе используется карбамидоформальдегидная смола, которая выделяет газообразный формальдегид
Где использовать ДСП?
Идеально для полов и отделки. ДСП универсальны, и их можно использовать по-разному в домашних условиях. Его можно использовать в полах, фурнитуре и арматуре, в качестве основы для паркетных полов, в качестве основного материала для облицовки планок, мебели и многого другого. Самое интересное в ДСП заключается в том, что их можно использовать во многих проектах DIY, поскольку они легко доступны и недороги. Так что, если вы любите ремонтировать свой дом самостоятельно, тогда вам следует выбрать ДСП.
Марки ДСП
ДСП доступен в различных сортах, которые зависят от их использования и применения.Вот несколько марок, в которых вы можете найти ДСП:
- Промышленный сорт (M2 и M3) — Может использоваться в шкафах, мебели и приспособлениях
- Товарный сорт (MS) — Может использоваться в шкафах и ламинированных панелях
- Сорт для столешницы (M2) — Этот сорт можно использовать в почте столешницы и ламинированные панели
- Shop Grade (M1) — Экономичная панель для неструктурных применений
Что такое фанера?
Слои древесного листа в фанере называются сваями.
Фанера — это искусственно созданный древесный листовой материал, состоящий из тонких слоев или тонких нитей шпона, соединенных вместе, соединяющих зерна древесины.Слои известны как «сваи», отсюда и название фанеры. Чем больше слоев, тем толще будет фанерный лист. В строительстве он может использоваться в стенах, полах, крышах, лестницах и т. Д. Вы можете широко использовать фанеру в мебельном производстве.
Преимущества фанеры
Фанера идеально подходит для сложных изделий из дереваКак и любой другой материал, фанера имеет ряд преимуществ при использовании в строительстве. Если вы планируете использовать фанеру дома, знайте, почему это будет хорошая идея:
- Фанера считается более прочной, чем другие листовые изделия из дерева, например МДФ
- Фанера используется бесконечно, как в помещении, так и на открытом воздухе
- Фанера разной плотности может использоваться для различных целей, что делает ее универсальной
- Фанера является универсальной.
отличный материал для сложных деревянных работ
- Из-за больших размеров панелей фанеры вы можете использовать ее для покрытия огромных площадей
- Она может хорошо удерживать бригады
Недостатки фанеры
Фанера может быть немного дорожеФанера — это здорово, но у какого материала нет недостатков? У этого также есть ряд недостатков, и вы должны знать о них, прежде чем использовать его дома.
- Это немного дороже по сравнению с другими древесными листами
- Края фанеры должны быть отделаны ламинатом или шпоном
- Фанеру немного сложно резать и формовать
- Листы ламината должны покрывать большинство коммерческих сорт фанеры
Где использовать фанеру?
Идеально подходит для шкафов, дверей и ставен Теперь перейдем к делу. Вы знаете, где можно использовать фанеру в домашних условиях? Вы знаете, что это такое и каковы плюсы и минусы использования фанеры, но когда дело доходит до выбора ее для вашей домашней мебели или интерьера, вы должны знать, как лучше всего ее использовать. В домашних условиях можно использовать фанеру для полов, гардеробы, шкафов, дверей, ставен и стен. Он может использоваться в качестве изголовья и подножек, обшивки стен и в качестве конструкции для мягкой мебели. Вы можете обрабатывать фанеру, чтобы она была устойчивой к таким опасностям, как насекомые, огонь, плесень и вода.
Сорта фанеры
Доступны различные маркиВы можете легко различать материалы по их маркам. Количество дефектов и объем работ по ремонту материала определяют его марку.На каждой марке материала есть отметка или штамп, которые можно легко идентифицировать. Имеется в наличии фанера следующих сортов:
.- Сорт S (высший) — только мелкие сучки и характеристики
- Сорт BB (средний) — сращенные овальные участки заменяют любые крупные сучки и дефекты
- Сорт WG (нижний) — открытые дефекты на более мелких сучках с некоторыми исправленными более крупными сучками
- C Grade (low) — открытые дефекты допустимы
The Verdict
С учетом всех преимуществ и недостатков, если сравнить ДСП и фанеру, то однозначно выигрывает фанера. Но это, однако, не означает, что вы отворачиваетесь от ДСП. Как мы уже упоминали, у древесно-стружечных плит тоже есть свои преимущества и преимущества. Если это работает для вас, вам обязательно стоит пойти на это. Подумайте о долгосрочной перспективе и взвесьте все «за» и «против» обоих материалов, прежде чем принимать решение.
Надеемся, это вам помогло. Если вы хотите узнать больше о МДФ и фанере, прочтите это: МДФ против фанеры: выбор правильного материала.
Ознакомьтесь с этим наглядным руководством к обоим материалам.
Хотите знать, как наши клиенты относятся к работе с Livspace? Вы можете ознакомиться с обзорами Livspace здесь!
Есть что добавить? Напишите нам по адресу: editor@livspace. com .
Различия между ДВП и ДСП
Древесноволокнистая плита средней плотности
Древесноволокнистая плита средней плотности (МДФ) — это изделие из древесины, получаемое путем разрушения мягкой древесины на древесные волокна, часто в дефибраторе, комбинирования ее с воском и связующим на основе смолы и формирования панелей путем приложения высокой температуры и давления.Он состоит из отдельных волокон (не фанеры), но может использоваться как строительный материал, аналогичный по применению фанере. Он намного плотнее обычного ДСП.
МДФ имеет много преимуществ перед дощатым деревом, ДСП или ДВП высокой плотности. Он очень гладкий, потому что древесные волокна, используемые при его производстве, однородны и тонки. Это обеспечивает низкий «отрыв», что означает, что при распиливании конец имеет гладкий срез, а не зазубренный край. Это также означает, что хорошо подходят слой грунтовки и несколько слоев краски, оставляя привлекательную законченную поверхность в отличие от других композитных деревянных изделий. МДФ также мягко реагирует на влагу, что означает, что он не деформируется и не набухает в помещениях с высокой влажностью, таких как шкаф для ванной комнаты.
Строители часто используют МДФ в мебели, стеллажах, ламинате, декоративной лепке и дверях. Они ценят МДФ за его тепло- и звукоизоляционные качества. Кроме того, его можно прибивать, склеивать, привинчивать, скреплять скобами или прикреплять дюбелями, что делает его таким же находчивым, как деревянная доска. Обычно люди, работающие с МДФ, используют твердосплавную пилу с вакуумом, чтобы уменьшить количество переносимой по воздуху пыли.Поскольку МДФ усилен смолой, содержащей формальдегид, те, кто подвергается воздействию, стараются снизить риск вдыхания или используют специальный МДФ с более низким содержанием формальдегида.
Изделия из восстановленной древесины, такие как МДФ, часто покрываются шпоном или ламинатом. Эти тонкие слои винила или натурального дерева маскируют МДФ, особенно по видимым краям. Некоторые люди предпочитают использовать МДФ по сравнению с обычными пиломатериалами, потому что они менее вредны для окружающей среды. МДФ производится исключительно из отходов, оставшихся обрезков, которые в противном случае были бы выброшены на свалку.Этот аттракцион помог ему завоевать популярность среди домовладельцев.
ДСП
ДСП (или древесно-стружечная плита в Великобритании, Австралии и некоторых других странах) представляет собой конструкционный продукт из древесины, изготовленный из древесных частиц, таких как древесная щепа, стружка лесопилок или даже опилки, и синтетической смолы или другого подходящего связующего, который является прессованные и экструдированные.
ДСП — это разновидность древесноволокнистой плиты, но она состоит из более крупных кусков древесины, чем ДВП и ДВП средней плотности.
ДСП дешевле, плотнее и однороднее, чем обычная древесина и фанера, и заменяет их, когда внешний вид и долговечность менее важны, чем стоимость. Однако ДСП можно сделать более привлекательным путем окраски или использования шпона, который наклеивается на видимые поверхности. Хотя он более плотный, чем обычная древесина, это самый легкий и самый слабый тип древесноволокнистой плиты, за исключением изоляционной плиты. ДВП и ДВП средней плотности, также называемые ДВП высокой плотности, прочнее и плотнее, чем ДСП.
Основным недостатком древесно-стружечных плит является то, что они очень склонны к расширению и обесцвечиванию из-за влаги, особенно когда они не покрыты краской или другим герметиком. Поэтому его редко используют на открытом воздухе или в местах с высоким уровнем влажности, за исключением некоторых ванных комнат, кухонь и прачечных, где он обычно используется в качестве подложки под сплошным листом винилового напольного покрытия.
Мебель Circle — МДФ против натурального дерева: необходимая информация
24 Сентябрь 2020
Когда дело доходит до покупки деревянной мебели, существует множество факторов; стоимость, цвет и качество, и это лишь некоторые из них.Но, пожалуй, самый главный вопрос — какое дерево вы получаете.
По существу, в мебели используется три типа «дерева»: массив дерева, МДФ и фанера.
И в этих категориях есть версии высокого и более низкого качества, которые повлияют на долговечность мебели и цену.
Бывают ли случаи, когда МДФ лучше, чем натуральное дерево? Или всегда стоит вкладывать деньги в качественную мебель из твердых пород дерева? Мы отвечаем на эти вопросы и выясняем разницу между МДФ и натуральным деревом.
Массив дерева — это природный ресурс, который не подвергается производственному процессу, как МДФ. Он подразделяется на твердую и мягкую древесину; Неудивительно, что древесина твердых пород является более прочной и долговечной из двух.
Твердая древесина и хвойная древесина Деревья лиственных пород растут медленно и дают более плотную древесину и, как правило, имеют более глубокий тон, чем деревья хвойных пород. Типичными породами древесины высококачественной деревянной мебели являются дуб, вишня, клен, орех, береза и ясень.
С другой стороны, древесина хвойных пород менее плотная и не такая прочная, как древесина твердых пород. Иногда их используют в качестве подложки или внутри ящиков для товаров. Типичными породами древесины хвойных пород являются сосна, тополь, акация и каучуковое дерево.
Качества и характеристики натуральной древесиныНатуральное дерево — живой материал.Его характеристики никогда не будут одинаковыми, поэтому ожидать «совершенства» не приходится. Мы думаем, что в этом красота мебели из твердых пород дерева. Каждая отметина, минеральное пятно и цветной узор рассказывают историю о том, как дерево адаптировалось к окружающей среде.
Мебель из натурального дерева, особенно из твердых пород дерева, невероятно долговечна, если за ней хорошо ухаживать. Это предметы, которые в конечном итоге становятся семейными реликвиями — обеденный стол вашей бабушки или старинная тумбочка, которую вы подарили другу.
Самое замечательное в мебели из натурального дерева то, что ее можно отполировать и отшлифовать, что еще больше продлит ее срок службы.
Подробнее: Руководство домовладельца по натуральному дереву в мебели
Итак, что насчет МДФ?
Древесноволокнистая плита средней плотности (МДФ) — это композитный древесный материал, состоящий из остатков твердой или мягкой древесины. Он может быть довольно плотным и прочным, что делает его практически невозможным для резки настольной пилой.
МДФ иногда путают с древесно-стружечной плитой (также известной как древесно-стружечная плита), которая намного менее прочна, поскольку состоит из больших деревянных щепок, скрепленных клеем и смолой. Хотя ДСП дешевле, мы рекомендуем держаться подальше. Пространство между древесной стружкой в ДСП делает его менее прочным и более подверженным повреждениям.
При этом не все древесные композиты дешевы и некачественны. МДФ хорошо использует свою прочность и плотность в некоторых областях применения. Вы можете найти его, например, в шкафах для носителей, потому что он не деформируется от тепла, исходящего от электроники.
Большинство полок для книжных шкафов изготовлены из МДФ, так как они могут выдерживать больший вес и предотвращают коробление. И, наконец, у большинства комодов есть МДФ на сайдинге, чтобы уменьшить стоимость и вес, а также обеспечить устойчивость с течением времени.
Каким бы плотным он ни был, МДФ значительно тяжелее, чем мебель из твердых пород, — о чем следует помнить, если вы покупаете более крупный предмет.
А фанера?Инженерная древесина (фанера) состоит из слоев древесины, склеенных между собой чередующимися секциями.
Фанера может быть как твердой, так и мягкой, что влияет на ее долговечность. Кроме того, фанера может иметь разное количество слоев, обычно от 3 до 9.Чем больше слоев, тем прочнее фанера и тем выше ее стоимость.
Фанера высшего качества изготавливается из просушенных в печи слоев твердой древесины, что позволяет ей сохранять форму и предотвращать коробление. Преимущество фанеры заключается в том, что ей можно придавать форму и изгибать для конкретных целей, например, для изготовления основы стула Stressless.
Что такое виниры?
Другой термин, который вы можете услышать при поиске деревянной мебели, — это «шпон».«Итак, что такое шпон?
Хотя существуют разные уровни качества фанеры, это менее дорогая альтернатива древесине твердых пород, полученная путем наложения тонкого куска высококачественной древесины на сорт искусственной древесины.
youtube.com/embed/NFwcgsoQL6E»/>
Однослойный материал выглядит как древесное зерно, но нижний слой снижает стоимость. Одним из недостатков шпона является то, что он ограничивает количество повторной полировки мебели.По этой причине мы не рекомендуем облицовывать столы фанерой.
Убедитесь, что если вы покупаете шпон, то это настоящий кусок твердой древесины. Кроме того, дешевый шпон — это самый простой способ сделать ДСП или ДСП похожими на натуральное дерево. Если у вас под фанерой используется ДСП более низкого качества, вы с большей вероятностью заметите износ.
Когда вы обсуждаете между МДФ и предметом мебели из твердых пород дерева, зачастую дело сводится к стоимости, за исключением тех областей применения, где МДФ выделяется.
Покупая мебель из твердых пород дерева, вы платите не только за высококачественный материал, но и за ручной труд, точность и внимательность, которые необходимы при ее изготовлении. И, как мы любим говорить, когда вы платите за качество, оно окупается в долгосрочной перспективе.
Прежде чем выбирать деревянную мебель, важно провести исследование, прочитать отзывы и получить информацию. Чем больше информации об этом предмете мебели, тем меньше вероятность того, что вы будете ошеломлены, когда он прибудет в ваш дом.
Наши консультанты по дизайну обладают обширными знаниями о деревянной мебели и смогут подробно рассказать о конструкции и мастерстве изготовления нашей коллекции. Зайдите в выставочный зал и поговорите с дизайнером, чтобы начать свое дизайнерское путешествие.
.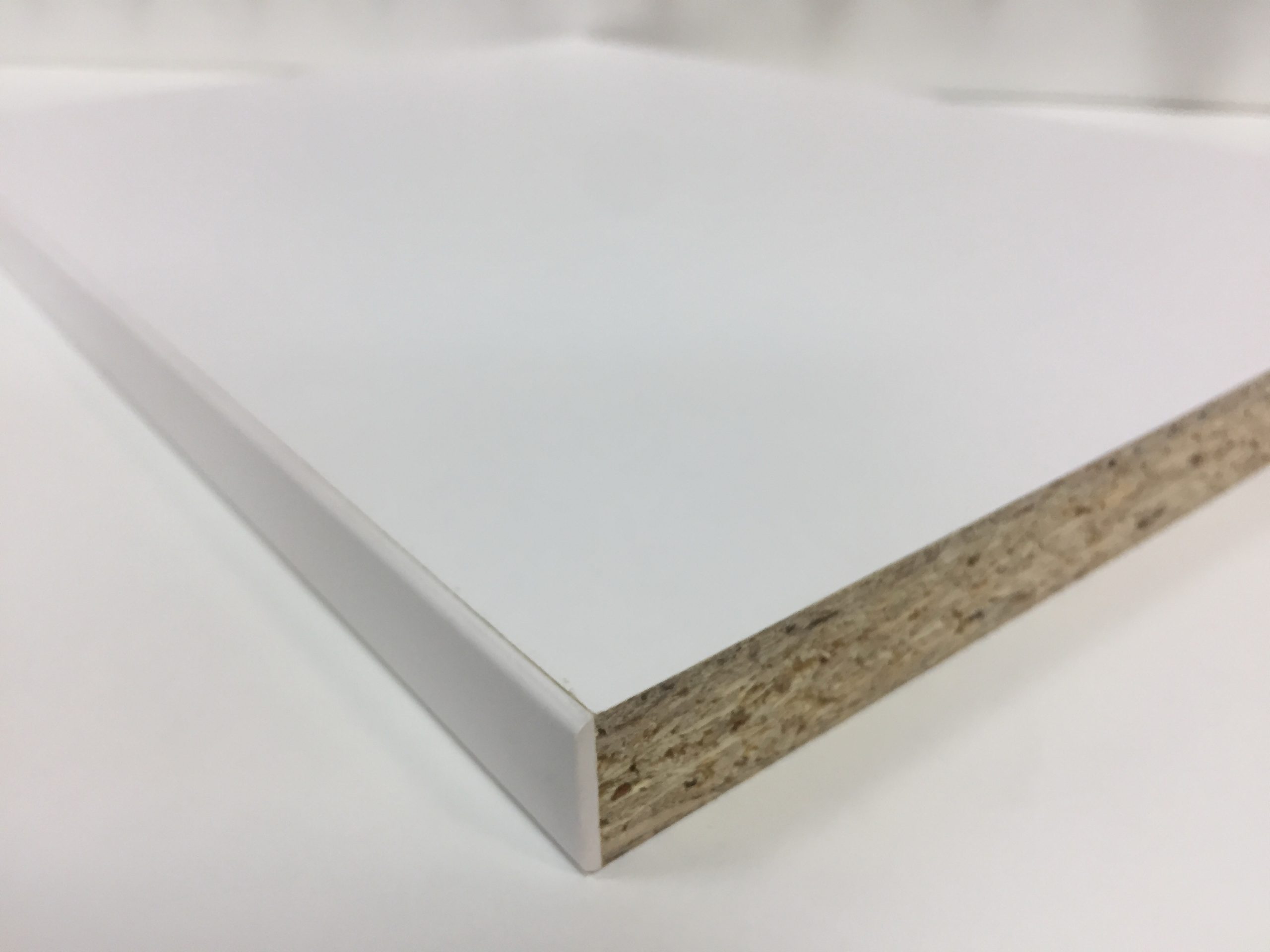
Комментариев нет