Линия по переработке бутылок пластиковых: Комплекс оборудования для переработки ПЭТ
№ | Наименование | Характеристики |
1 | Ленточный загрузной конвейер GPD-8065 | Подача ПЭТ-бутылки в дробилку |
Длина | 6500 мм | |
Ширина ленты | 800 мм | |
Жесткая стальная конструкция. Траспортерная лента из резины. Система натяжения ремня | ||
Мощность двигателя | 1,5 кВт | |
2 | Дробилка GXC-4280 | Измельчение бутылки(специально разработанные ножи для ПЭТ) |
Диаметр ротора | 420 мм | |
Длина ротора | 800 мм | |
Скорость вращения | 520 об/мин | |
Устройство подачи | 4 кВт | |
Мощность двигателя | 37 кВт | |
3 | Шнековый конвейер GSC-2550 | Подача хлопьев из дробилки в ванну горячей мойки |
Длина | 5000 мм | |
Диаметр конвейера | 250 мм | |
Мощность двигателя | 2,2 кВт | |
4 | Ванна горячей мойки GTC-250 | |
Ёмкость | Нержавеющая сталь | |
Жесткая стальная конструкция.![]() |
||
Шнек | Нержавеющая сталь | |
Мощность нагревателей | 30 кВт | |
5 | Центрифуга (дегидратор) GSW-650 | Отбивание грязи и ненужных примесей от ПЭТ-хлопьев |
Диаметр цетрифуги | 650 мм | |
Ротор с лопастями. Самоочищающиеся поворотные устройства для сетки | ||
Сетка | Нержавеющая сталь | |
Система закачки и сброса воды | ||
Мощность двигателя | 37 кВт | |
6 | Ванна флотационной мойки GSF-1430 | Отмывание хлопьев и отделение частей от этикетки и крышки с кольцом |
Длина | 3000 мм | |
Ширина | 1400 мм | |
Корпус ванны, лопасти, части соприкосающиеся с водой | Нержавеющая сталь | |
Шнек для подачи очищенных хлопьев | 2 комплекта | |
Мощность двигателя | 15 кВт | |
7 | Центрифуга (дегидратор) GSW-650 | Отбивание грязи и ненужных примесей от ПЭТ-хлопьев |
Диаметр цетрифуги | 650 мм | |
Ротор с лопастями.![]() |
||
Сетка | Нержавеющая сталь | |
Система закачки и сброса воды | ||
Мощность двигателя | 37 кВт | |
8 | Сепаратор(классификатор) GRX-8012 | Окончательное отделение этикетки |
Длина | 1200 мм | |
Ширина | 800 мм | |
Регулировка объема воздуха. Циклон | ||
Поворотный клапан | 1,1 кВт | |
11 кВт | ||
9 | Ленточный выгрузной конвейер GPD-8060 | Сортировка материалов |
Длина | 6000 мм | |
Ширина | 800 мм | |
Мощность двигателя | 1,5 кВт | |
10 | Система выгрузки (силос) | Выгрузка готовой фракции хлопья (флексы) |
11 | Контрольная панель | Siemens, Schneider |
Источник высокого качества Пэт Бутылка Переработки Линии производителя и Пэт Бутылка Переработки Линии на Alibaba.
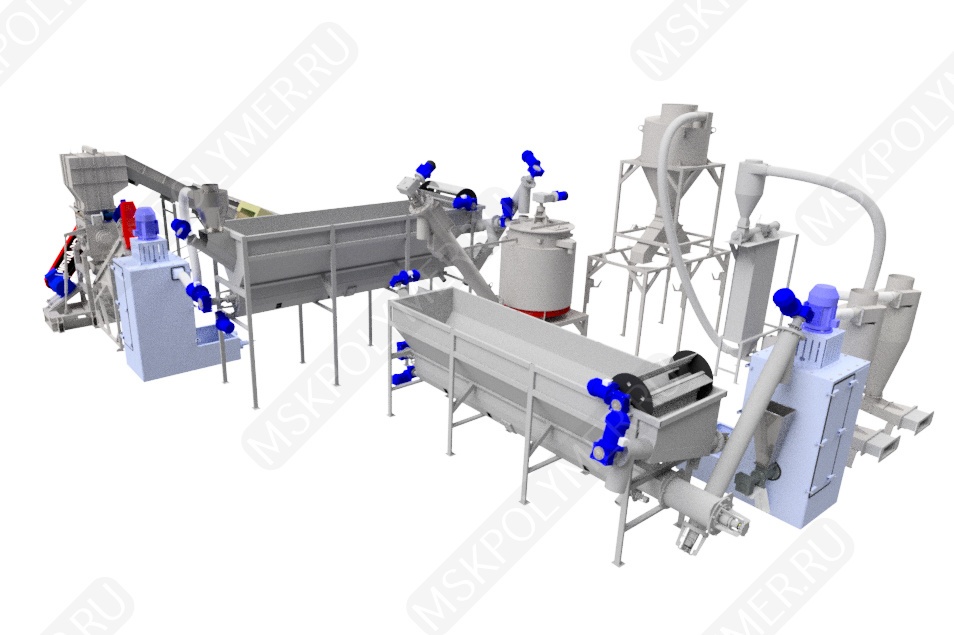
Получите эксклюзив. пэт бутылка переработки линии для ваших нужд по утилизации на Alibaba.com. С ростом производственных затрат и насущными проблемами окружающей среды спрос на. {ключевое слово} STRONG> неоспоримо. Эти. пэт бутылка переработки линии - правильный выбор для превращения грязных куч отходов в хлопья или гранулы многократного использования.The. пэт бутылка переработки линии на Alibaba.com можно использовать для разделения алюминиевой стружки, мешков из-под цемента, пластиковых бутылок, их мытья и переработки. пэт бутылка переработки линии хорошо подходят для различных типов пластиков, таких как ПЭ / ПП / ПЭТ / АБС и т. д. Они различают тип по плотности материала. Мощность обработки. пэт бутылка переработки линии колеблется от 300 до 800 кг / час. Все необходимое, связанное с рабочей силой, размером мастерской, водоснабжением, предоставлено для вас, чтобы вы могли принять обоснованное решение.
Также показаны статистические данные о качестве конечного продукта с учетом возможности настройки. Характеристики, связанные с размером частиц, плотностью, допустимым уровнем примесей, производительностью обработки и т. Д., Разрабатываются индивидуально.
The. пэт бутылка переработки линии разработаны с учетом высокой степени автоматизации и высокой производительности. Оба из них гарантируют, что вы не только сократите накладные расходы на рабочую силу, но и максимизируете свой доход. Файл. Системы пэт бутылка переработки линии также имеют опцию аварийной паузы, чтобы избежать случайной ошибки. Кроме того, у них есть ЖК-экран для простоты использования и управления. Файл. пэт бутылка переработки линии настроены в соответствии с типом загрязнителя, с которым вы имеете дело. На сборочной линии используется разнообразное оборудование, такое как обезвоживающие машины и фрикционные шайбы, каждая из которых доступна по удивительным предложениям.
![]()
Откройте для себя то, что нельзя пропустить. пэт бутылка переработки линии работает только на Alibaba.com. Если ты. пэт бутылка переработки линии поставщик и оптовый торговец, ваши потребности будут удовлетворены. Купите сейчас и внесите свой вклад в сохранение планеты.
Переработка пластиковых бутылок — спасение экологии и экономически выгодное предприятие
Большинство напитков, которые приобретают люди, продаются в пластиковых бутылках. На каждого жителя города приходится примерно 100 килограммов выкинутых ПЭТ-бутылок в год. Если учитывать, что разлагаются они в течение 300 лет, то можно представить, какой непоправимый ущерб можно нанести экологии планеты, если все эти бутылки будут свозиться на свалки. Гораздо выгоднее для экономики и безопаснее для природы перерабатывать пластиковую тару и использовать как вторсырье.
Содержание:Показать
Именно ПЭТ-бутылка является основным сырьем при производстве флекса (вторсырья для получения химического волокна).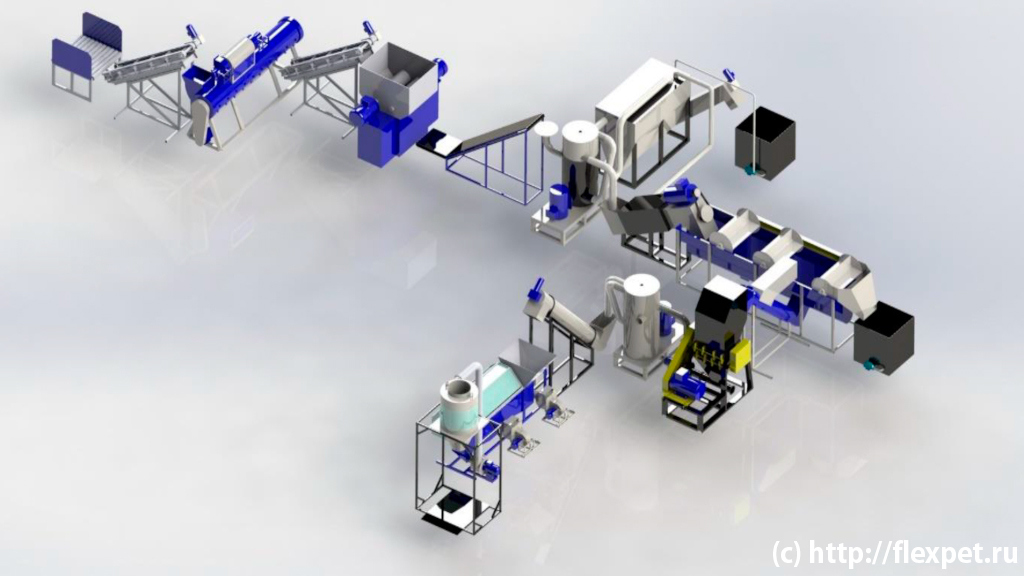
Получается циклический процесс бесконечной переработки пластиковых бутылок, что экономит средства и защищает окружающую среду. В России данный вид деятельности еще не вышел на массовый рынок, а потому подобный бизнес является особенно конкурентоспособным и привлекательным.
Оборудование для переработки пластика
Пройдя ряд этапов обработки, последним из которых станет предварительное прессование, бутылки попадают на специальную линию, перерабатывающую тару. При выходе и получается флекс, который имеет вид хлопьев. Линия представляет собой несколько агрегатов, соединенных ленточными траснспортерами. Она состоит из следующих элементов:
- роторная машина;
- дробилка;
- шнековый транспортер, оснащенный архимедовым винтом;
- паровой котел;
- моющая полировочная машина;
- аппарат полоскания;
- сушилка-водоотделитель;
- воздушная сушка;
- бункер.
Технология переработки происходит по определенной схеме:
- собранные бутылки сортируются по цветам, каждый цвет обрабатывается отдельно;
- вручную удаляются различные посторонние предметы – резина, бумага, прочие виды пластика;
- в роторной машине отделяются этикетки и крышки;
- в дробилке с несколькими ножами, напоминающей большой блендер, бутылки измельчаются;
- затем на шнековый транспортер помещают массу из пластиковых бутылок в паровой котел, где происходит еще один процесс очищения;
- полностью очищенный пластик отправляют в сушилку-водоотделитель, потом в воздушную сушку;
- после того как полученный флекс полностью высохнет, его переместят в специальный бункер;
- путем агломерации производится спекание крошки в маленькие комки, их уже можно использовать в качестве сырья. Для усреднения характеристик комков проводят грануляцию, что повышает плотность полученного материала и облегчает его дальнейшее использование.
Что получается из вторично переработанного сырья
Переработанные бутылки идут на изготовление множества различных изделий
Как из переработанных отходов может получится резиновая плитка для дачи.
Смотрите в статье: какие еще покрытия можно получить из резиновой крошки, приготовленной из вторсырья.
Перспективы данного направления
На сегодняшний день переработка пластиковых бутылок является одним из самых рентабельных сегментов рынка переработки. Если говорить о прибыли для конкретного предпринимателя, то вложения в данный вид деятельности при правильном подходе окупятся уже через 14–18 месяцев, а чистая месячная прибыль составит около 8 тысяч долларов.
Стоит отметить, что городские власти зачастую идут навстречу желающим заняться подобным видом деятельности. Так, если подать заявку на участие в какой-либо программе по очистке города, то вполне можно получить бесплатно помещение, подходящее под завод для переработки. Все, что останется, – это зарегистрировать предприятие и закупить необходимое оборудование (линию полного цикла).
С нахождением сырья для производства проблем не возникает: так как города завалены пластиковыми бутылками, остается либо собирать их, либо открыть пункты приема; еще один вариант – договориться со свалкой о доставке сырья. Особенность данного бизнеса в том, что, обеспечивая себе прибыль, предприниматель делает полезное дело для экологии. Ведь ПЭТ-бутылки – это настоящая проблема, особенно в больших городах, когда после массовых мероприятий либо просто в местах скопления людей остаются огромные груды мусора, большая часть которого и есть пластиковые бутылки.
Линии по переработки ПЭТ пластиковых бутылок
Для того, чтобы наладить процесс и специализированное оборудование для переработки ПЭТ, необходимо сотрудничать только с квалифицированными проверенными специалистами, зарекомендовавшими себя настоящими профессионалами.
Почему переработка ПЭТ бутылок – это важный производственный процесс? Какие преимущества имеет переработка ПЭТ?
Линия по переработке ПЭТ – эффективно и выгодно
Схематичное изображение линии по переработки ПЭТ
Основными преимуществами и особенностями производственной линии по переработке ПЭТ бутылок, являются:
- Минимальные затраты при сборе бывшего в употреблении материала для переработки;
- Простое обучение обслуживающего персонала для производственной линии;
- Постоянный рынок сбыта готовой продукции;
- Ежегодный процент дохода до 25%;
- Перспектива производства и рабочих мест на многие годы;
- Получение субсидий и других льгот от государства, на переработку товаров, наносящих вред экологии и окружающей среде.
Этапы и шаги налаживания производственного процесса
Какие именно этапы способствуют тому, чтобы оборудование для переработки ПЭТ бутылок было правильно и грамотно настроено и отлажено?
- 1) Установить тесные партнерские отношения с мусоросортировочными предприятиями, а также поставщиками б/у продукции в виде ПЭТ;
- 2) Установить связи с покупателями вторичного сырья, получаемого после переработки б/у ПЭТ;
- 3) Покупка качественного оборудования, которое даже при интенсивной и длительной эксплуатации не будет изнашиваться или выходить из строя.
Линия по переработке ПЭТ бутылок с гарантией
Настройка новой производственной линии по переработке ПЭТ бутылок, требует больших финансовых вложений, которые быстро окупаются. В нашей компании можно не только приобрести качественные агрегаты, конвейеры и другие составляющие линий по переработке ПЭТ, но и заказать специалистов, которые на месте произведут качественную настройку для эффективной работы. Все агрегаты и компоненты линии производства поставляются непосредственно от производителя, поэтому сопровождаются многолетней гарантией качества.
Принцип работы оборудования
Габаритный комплекс для переработки ПЭТ бутылок – это эффективная и производительная линия, где в результате технологического процесса, б\у материал превращается в качественное, пригодное для повторного использования сырье. При помощи данного оборудования, можно перерабатывать ПЭТ бутылки любого объема и вида, получая на выходе чистый и качественный материал, который производитель может использовать для создания новых товаров и продукции.
Комплекс состоит из двух основных участков:
- Участок дробления, где ПЭТ продукция измельчается до состояния хлопьев;
- Экструзионный участок, который выдает готовую для реализации продукцию, в виде специальных гранул.
Чтобы переработка ПЭТ бутылок купить линию для которой можно в нашей компании, была налаженным и эффективным производственным процессом, мы готовы сотрудничать и отвечать на вопросы клиентов 24 часа в сутки. Наши заказчики, среди основных преимуществ работы с нами отмечают:
- Адекватную стоимость оборудования и составляющих;
- Удобную форму оплаты производственных агрегатов;
- Оформление всех разрешительных и таможенных документов, а также осмотр и аренду склада для хранения агрегатов, за счет нашей компании.
Линия по переработке пластиковых пэт бутылок: оборудование и процесс
Изготовление вторичного пластика – не только рациональная утилизация экологически неудобного сырья, но и доходный малозатратный бизнес. Технологически процесс механической переработки пэт бутылок состоит из:
- сортировки сырья (по виду пластмассы и цвету) и отделения мусора;
- дробления;
- агломерации;
- гранулирования.
Хотите зарабатывать на акциях? Подпишитесь на Телеграм-бот @birzevikbot — он рассылает биржевые новости, тренды, лекции — рекомендую и новичкам и профи.
Сортируют и очищают пластиковое сырье, зачастую, вручную (или используют вибросито). Последующим процессам требуется специализированное оборудование, составляющие линию по переработке пластиковых пэт бутылок.
Оборудование и процесс переработки пластиковых бутылок
- Конвейерная лента загружает отсортированное сырье в дробильную установку (через ее приемный бункер). Само дробление предусматривает тщательное измельчение пластика в гомогенизированные хлопья не более 20 мм (это и есть флекс) и его последующую гидроочистку в бункере отмывки при помощи раствора каустика.
- Специализированные сушилки удаляют влагу при строго определенной температуре. От соблюдения температурного режима (+130°) напрямую зависит качество конечного сырья.
- Агломерация флекса представляет собой процесс его спекания. Ножи, вращаясь при температуре в ёмкости +100°, измельчают ранее заготовленные хлопья в еще меньшие фракции. Именно они, имея размер от 2 до 15 мм, и отправляются на завершающую грануляцию.
- Грануляция предполагает разогрев измельченной массы (до +280°) и вытягивание ее в волокна (с последующим нарезанием определенной длины и охлаждением). Для гранулирования можно также использовать экструдер — специальную формовочную машину для пластичного сырья.
Химический способ получения флекса (ввиду высокой стоимости процесса) применяется реже, чем механический вид этого рециклинга.
Помимо обязательных составляющих оборудования для флекса, линия по переработке пластиковых пэт бутылок может включать и дополнительные агрегаты. К их числу относятся: емкости для замачивания и ополаскивания флекса, динамическая центрифуга, дозаторы, термическая ванна, фрикционный шнек.
После завершения всех производственных циклов вторичный гранулированный пластик снова становится полноценным сырьем для широкого спектра продукции.
Автор поста: Богдан ОстапченкоСпециалист по поставкам строительной и складской техники. Снабженец.
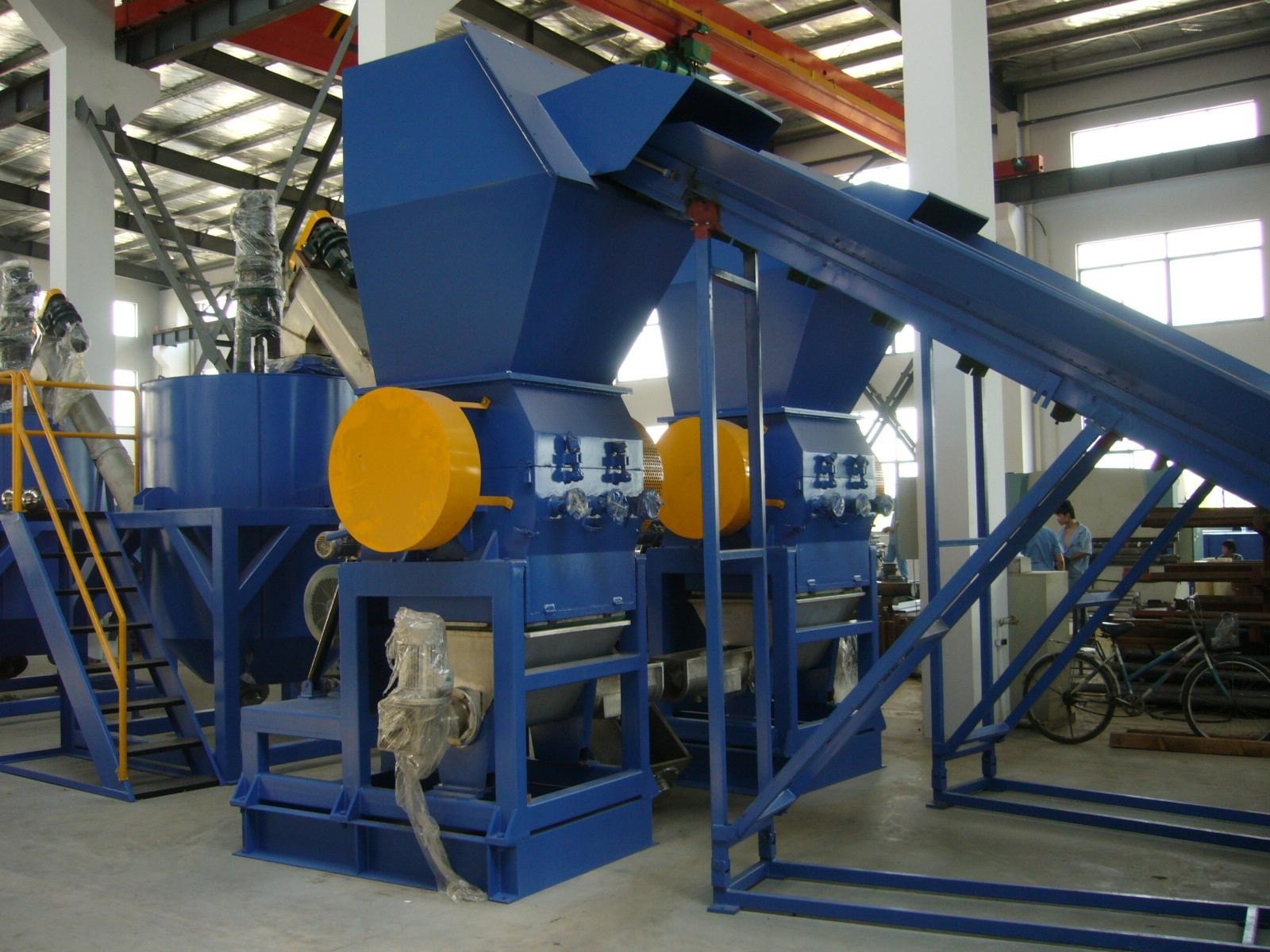
Не нашли нужного оборудования? Напишите нам через форму обратной связи или напрямую обратитесь к менеджеру по адресу china@fareasttrans.![]()
____________________________ * Информацию о процедуре приобретения оборудования Вы найдёте, перейдя сюда — Порядок работы * Ознакомиться с образцами документов для приобретения и прочей полезной информацией вы можете здесь — Информация для клиента * Просмотреть отзывы наших партнёров и оставить свой, Вы можете, перейдя в раздел — Отзывы * Наши дилерские сертификаты, а также фотоотчёт нашей деятельности, представлены здесь — Фотогалерея * По другим возникшим у Вас вопросам, пожалуйста, обращайтесь в наш офис — Контакты |
Новости 13.12.2018 06.12.2018 27.11.2018 06.04.2015 13.11.2014 |
Линии по переработке ПЭТ бутылок
Линия по переработке ПЭТ бутылок позволяет вторично использовать данное востребованное и одновременно специфичное полимерное сырье. Переработка загрязнённых ПЭТ бутылок в хлопья, с промежуточной отмывкой в линии мойки ПЭТ, даёт на выходе очищенную флексу.
Переработка ПЭТ бутылок
ГК «Апрель предлагает линии переработки ПЭТ производительностью 300, 500 и 1000 кг/ч. Стандартная комплектация линии переработки ПЭТ:
1. Ленточный транспортер
2. Роторная дробилка
3. Шнековая подача (фрикционная мойка)
4. Ванна горячей мойки
5. Ванна
6. Центрифуга
7. Панель управления
8. Дополнительное оборудование: нагреватель, насос, коллекторы этикеток и крышек, вентилятор, бункер досушки.
Технологический процесс переработки ПЭТ бутылок таков. Ленточный транспортер используется для непрерывной подачи отходов в дробильную установку.
Дробильная установка роторного типа измельчает сырье до мелкой фракции.
После этого ПЭТ сырье проходит через устройство отделения этикеток (необходимо отметить, что отделение этикеток может происходить на нескольких этапах: до дробления, после дробления, во время мойки во флотационной ванне, после сушки в циклонном сепараторе).
Фрикционная мойка осуществляет первичную мойку ПЭТ материала и перемещает его в моечную камеру.
В моечной камере происходит отделение основных загрязнений ПЭТ бутылки, оставшихся этикеток и посторонних включений. При необходимости сырье повторно пропускается через шнековые транспортеры и подвергается обработке паром.
После процесса промывки и очистки сырье поступает в центрифугу, чтобы убрать из него излишки воды. На выходе получаются мелкодисперсные куски ПЭТ («флекса» или хлопья), готовые к экструзии или грануляции.
Представленная комплектация является одним из вариантов линии переработки ПЭТ, и может быть изменена в соответствии с Вашими потребностями и ресурсами.
Процесс изготовления пластиковых бутылок | Sciencing
Производители производят широкий спектр бутылок из пластика, включая бутылки для воды, бутылки из-под газировки и контейнеры для пищевых продуктов, например, для горчицы или кетчупа. Полиэтилентерефталат (ПЭТ) является особенно популярным при производстве бутылок любого типа, соприкасающихся с продуктами питания или питьевой водой. Из этого материала получаются легкие, но при этом прочные и долговечные бутылки. Хотя производители могут немного изменить процесс в зависимости от собственных методов, основной метод производства бутылок универсален.
TL; DR (слишком долго; не читал)
TL; DR: пластиковые гранулы нагреваются до 500 градусов по Фаренгейту перед впрыском в формы в форме бутылок.
Сырье
ПЭТ — пластичная смола, полученная из нефтяных углеводородов. Производитель создает длинные цепочки пластиковых молекул с помощью процесса, называемого полимеризацией, а затем смешивает материал с несколькими химическими соединениями. Они разрезают смолу на мелкие гранулы и отправляют ее производителю бутылок.Завод по производству бутылок смешивает гранулы полиэтилентерефталата с «измельченным» — переработанным пластиком, превращенным в хлопья. Пластик теряет некоторые из своих физических свойств при многократном нагревании, поэтому производители должны ограничивать количество используемого измельченного материала, обычно ограничивая этот ингредиент 10% от общей смеси. Если не производятся прозрачные бутылки, в смесь также добавляются красители.
Создание преформы
Экструдер плавит ПЭТ и измельчает смесь при температуре около 500 градусов по Фаренгейту.Шнек внутри экструдера сжимает смесь ПЭТ и впрыскивает почти расплавленный материал в формы. Пресс-форма производит преформу бутылки, которую иногда называют заготовкой. Преформа выглядит как толстостенная пробирка, часто с характерной для бутылки завинчивающейся крышкой. Преформа охлаждается по мере того, как она попадает в машину, называемую выдувным формовщиком, и, возможно, ее придется довести до температуры, указанной производителем для этой операции. При необходимости производитель бутылок повышает температуру преформы в небольшой духовке.
Растяжение преформы
Преформы попадают в форму, состоящую из двух частей, которая закрывается вокруг нее. Внутренняя часть этой формочки имеет форму готовой бутылки. Внутри длинная игла продвигается вверх через преформу, которая подвешена концом винта вниз. Игла вытягивает преформу вверх к верху формы, которая будет дном бутылки, и одновременно вдувает в преформу достаточно сжатого воздуха, чтобы прижать ее к стенкам формы.Этот процесс формования с раздувом и вытяжкой должен происходить быстро, чтобы сохранить целостность бутылки и однородную форму. Некоторые производители приваривают отдельную деталь дна к бутылке во время выдувного формования, в то время как другие производят дно из преформы вместе с остальной частью бутылки.
Охлаждение и обрезка
Бутылку необходимо охладить почти мгновенно, иначе она потеряет форму, когда сила тяжести заставит ее сползать вниз в податливом, нагретом состоянии. Некоторые производители охлаждают бутылку, пропуская через форму холодную воду или жидкий азот, другие предпочитают наполнить ее воздухом комнатной температуры.Форма обычно дает чистую бутылку, но на швах бутылок, где встречаются две половинки формы, может произойти некоторая вспышка. В таком случае операторы обрезают лишний материал и добавляют его в измельченный материал.
Машиностроение: Производство пластиковых бутылок
Производство пластиковых бутылок (ПЭТ)
Пластиковые бутылки сегодня пользуются большим спросом, в основном из-за их долговечности. Большинство людей во всем мире используют его ежедневно.Содержащиеся в бесчисленных применениях, в частности пластиковые бутылки или пластик, должно быть одним из величайших открытий последних столетий.
Fig01: Полиэтилентерефталат, также известный как ПЭТ, является наиболее распространенным в настоящее время
Обычно используемый пластик в настоящее время
О полиэтилентерефталате, используемом для розлива в бутылки
Полиэтилентерефталат
сделано не в едином процессе.Он образуется в результате реакции двух химических веществ, известных как очищенная терефталевая кислота (PAT) и этиленгликоль (EG).
Эти два химических вещества образуют полиэтилентерефталат вместе с другими типами пластика, которые используются в различных областях, таких как машиностроение, производство нейлона и т. Д.
Ниже приведены некоторые свойства полиэтилентерефталата
- Плотность: 1,38 ~ 1,40 г / мм 3
- Температура плавления: 254-256 ° C
- Кристалличность:> = 45%
- Температура стекла: 82 ° C
Рис02: Повторяющийся блок из полиэтилентерефталата .
ПЭТ — длинноцепочечная молекула с повторяющейся единицей, показанной выше, смола, голубовато-белое вещество, полученное в результате поликонденсации терефталевой кислоты и этиленгликоля. Производители смол поставляют ПЭТ в виде небольших гранул, каждая весом около 0,05 г. Будучи прозрачным, ПЭТ может достигать предела прочности на разрыв примерно от 1/3 до 1/2 от стали.
Количество повторяющихся звеньев ПЭТ в цепи, используемых в производстве бутылок для изготовления пластиковых бутылок, составляет примерно от 100 до 155, обычно обозначается как смола IV.
Применение полиэтилентерефталата
Также известный как ПЭТ, это термопласт, который является одним из миллионов других видов пластика. Безусловно, самый полезный тип пластика, ПЭТ-бутылки, в основном используются в индустрии напитков, где бутылки наполняются конкретным напитком и поставляются по всему миру. Это может быть вода, свежевыжатый сок или любой другой напиток. Некоторые из наиболее распространенных применений — розлив минеральной воды, пищевого масла, сока, косметики, фармацевтики и т. Д.
Основные преимущества ПЭТ
- Чистый ПЭТ не вступает в реакцию с пищей или напитком, которые хранятся в контейнере. Таким образом, ПЭТ соответствует международным нормам, касающимся контакта с пищевыми продуктами.
- Легкий — в 10 раз легче стеклянной упаковки, ПЭТ-бутылки, следовательно, снижает транспортные расходы на 30%. Если сравнивать стеклянную и ПЭТ-бутылку одного размера по объему, который она может хранить, ПЭТ будет первой, так как ее стенки тоньше.
- Crystal Clear — продукт выглядит чистым, здоровым и находится в хорошей физической форме.Это привлекает внимание и увеличивает продажи содержащихся в нем продуктов.
- Нет утечки — из-за отсутствия линии сварки на дне ПЭТ-бутылки не протекают.
- Гибкость дизайна — можно создавать любые формы и размеры, дизайн и цвета.
- Пригодно для вторичной переработки — поскольку ПЭТ-бутылки представляют собой единый материал, их можно мыть, измельчать на хлопья и придавать им форму. После переработки он находит и другое применение, например, для обвязки лент, изготовления ковров и т. Д.
Обычно ПЭТ-бутылки производятся двумя разными способами.
Это: —
- Одношаговый метод «горячего выполнения».
- Двухэтапный метод «холодного выполнения».
Этап первый метод «горячего выполнения»
Этот метод представляет собой всего один этап, от гранул ПЭТ до готовых бутылок, все процессоры выполняются на одной интегрированной машине. То есть от литьевого формования преформы до извлечения преформы из впрыскивающей полости и вытягивания с раздувом преформы до бутылки — все в одной машине, при этом температура остается постоянно высокой в течение всего процесса, как литье под давлением, так и выдувное формование. , материал должен иметь эластичную форму.Этот метод экономит много энергии, так как материал необходимо нагреть только один раз, то есть когда он вводится в полость для изготовления преформы. Одношаговый метод обычно используется на малых и средних предприятиях по производству ПЭТ.
Этап-два метода «холодного выполнения»
Этот метод имеет 2 различных машины для выполнения литья под давлением и выдувного формования.Преформа впрыскивается в форму на первой машине, а затем преформа повторно нагревается, поскольку она не подается непосредственно в машину для выдувного формования и выдувается на второй машине. Этот метод не очень эффективен, так как потеря тепла рассматривается как потеря энергии. Но эти машины полностью автоматизированы. Этот метод используется на большинстве средних и крупных компаний по производству ПЭТ. Эта машина на 200% эффективнее, чем одноступенчатая.
Рис04: Двухэтапный метод «холодного выполнения», полностью автоматизированная машина.
Обычно при производстве бутылок из ПЭТ используется двухэтапный метод.
Сушка и осушение ПЭТ
ПЭТ — это тип пластика, который впитывает влагу со средним содержанием воды 0,05%. Для повышения качества преформы с точки зрения прозрачности и физических характеристик ПЭТ сушат, чтобы снизить содержание воды в смоле ПЭТ до менее или равного 0,005%. Используются следующие методы сушки.
- Сушка в печи — Сушка проводится при температуре 110 ° C в течение максимум 8 часов, после чего ПЭТ начинает разрушаться.Противни с ПЭТ, вставленные в печь, имеют толщину около 50 мм.
Духовка не подключена к литьевой машине, и высушенный ПЭТ перемещается вручную.
- Бункерная сушилка — широко используемый метод сушки ПЭТ, поскольку он очень экономичен и работает вместе с автозагрузчиком, поэтому процесс является непрерывным и автоматическим.
Рис. 5. Бункерная сушилка, используемая для сушки гранул ПЭТ. - A Dehumidifier — аналогично сушилке с бункером, это слово также обозначается как автозагрузчик, но это наиболее эффективный метод сушки.ПЭТ сохнет при температуре около -32 ° C, что увеличивает долговечность и окончательную отделку бутылки из ПЭТ.
Fig06: Осушитель, используемый для сушки гранул ПЭТ.
Оптимальная температура сушки составляет около 150 ~ 170 ° C. Оптимальная продолжительность сушки ПЭТ составляет около 4 часов. Время сушки не должно превышать 7 ~ 8, поскольку это приведет к порче ПЭТ.
Литье под давлением преформы ПЭТ
Рис. 7. Термопластавтомат с присоединенным основным оборудованием.
На приведенном выше рисунке показана термопластавтомат с автозагрузчиком и сушилкой, а также другим важным оборудованием, необходимым в процессе.
Рис. 8: Схематическое изображение процесса литья под давлением .
Процесс прост: нагретый ПЭТ, который находится в расплавленной форме, впрыскивается в камеру впрыска (2) посредством вращения цилиндра шнека (1) внутри машины, пока камера не заполнится.
После заполнения камеры винт выдвигается вперед (3), чтобы заполнить впрыскиваемую полость расплавленным пластиком через сопло в форму.
Температура внутри машины для литья под давлением различается, в задней части машины температура должна быть около 275 ° C, в середине машины около 282 ° C, у форсунки около 280 ° C. А на литнике температура должна быть около 270 ° C, чтобы сформированная бутылка имела оптимальные характеристики. (Эти температуры могут немного отличаться в зависимости от конструкции формы)
Рис.9: Форма для ПЭТ-преформ
Рис.10: Нагреваемая преформа
Затем расплав пластик внутри формы, называемый преформой, должен охлаждаться.Температура охлаждающей воды, используемой для охлаждения выступления, должна быть от 15 до 20 ° C, давление также необходимо контролировать, поэтому используется водяной охладитель. Давление должно поддерживаться на уровне 500 000 Па или 5 бар.
Преформа ПЭТ выталкивается (4) из формы. Теперь преформа снова нагревается до температуры, пока она не станет пригодной для процесса выдувания.
Рис. 11: Типовой чиллер. Преформы ПЭТ
Рис.
Следующий процесс производства ПЭТФ представляет собой тип выдувного формования, называемый формованием с раздувом и растяжением, когда воздух нагнетается в предварительно нагретую ПЭТ-преформу.
Другие типы выдувного формования: —
Экструзионное выдувное формование
Рис. 13: Процесс экструзионного выдувного формования.
2. Литье под давлением с раздувом
Рис. 14: Процесс литья под давлением с раздувом.
Выдувное формование — это процесс формования полого объекта путем выдувания в термопласт, в данном случае ПЭТ-преформа, которая нагревается и находится в максимально эластичном состоянии.Процесс выдувного формования, используемый при производстве ПЭТ-бутылок, — это формование с раздувом и вытяжкой.
Этот процесс также называется формованием с раздувом с двухосной ориентацией, поскольку преформа сначала растягивается выдувным устройством по той причине, что молекулы предварительно нагретой преформы выстраиваются в одном направлении и все параллельны друг другу, а затем выдуваются вправо. углы к направлению выравниваемых молекул.
Теория, лежащая в основе того, как это работает, заключается в том, что когда ПЭТ нагревается, молекулы с длинными цепями могут расшатываться, а затем, в качестве альтернативы разрыву, они ориентируются при растяжении.Таким образом, это (выдувание с вытяжкой) также называется двухосной ориентацией, поскольку она касается растяжения по двум осям.
Это растяжение увеличивает прочность материала, потому что вместо того, чтобы молекулы в материале действовали по отдельности, они действуют как единое целое.
Следующие характеристики улучшаются или увеличиваются в результате такого растяжения ПЭТ-преформы перед выдуванием в нее.
- Предел прочности
- Ударная вязкость
- Барьер
- Химическая стойкость
Идеальная температура для ориентации ПЭТ — 105 ° C.
Сжатый воздух (), подаваемый в ПЭТ-преформу, сначала очищается с помощью воздухоочистителя (). Воздух необходимо очищать, так как он содержит влагу и масло, что напрямую влияет на качество бутылки. Преформа ПЭТ устанавливается на выдувную машину (). После очистки предварительно нагретую ПЭТ-преформу продувают воздухом с помощью воздуходувки на форму ().
Толщина выдувных бутылок Stetched составляет 0.25 ~ 0,38 мм. Этой толщины вполне достаточно, так как ориентация улучшает качество продукции.
Возможные дефекты при производстве бутылок из ПЭТ
Одним из основных недостатков при производстве бутылок из ПЭТ является производство ацетальдегида.
Это соединение, также называемое АА, представляет собой кислый вкус большинства цитрусовых. Этот привкус в бутылке может испортить вкус напитков, особенно если вода, как вкус чистой воды, недостаточно сильна, чтобы скрыть вкус AA, в отличие от сладких ароматов.Если присутствие АА замечено, качество продукта в буквальном смысле идет насмарку.
AA производится вместе с ПЭТ, когда температура материала выше 260 ° C, эта температура достигается внутри литьевого формования преформ, поэтому процесс не поддерживается должным образом, AA производится вместе с Преформа ПЭТ.
Понижение температуры расплава и времени пребывания помогает снизить образование АК.
Прочие виды дефектов кратко описаны ниже.
- ОН- или СООН-концевые группы не становятся инертными.
- Увеличивается количество полифункциональных макромолекул.
- Гидроксидные и пероксидные группы накапливаются на поверхности ПЭТ и т. Д.
Рис. 16: Общий процесс производства ПЭТ-бутылок
Процесс: Процесс производства ПЭТ-бутылок включает в себя два основных этапа: изготовление преформ и выдувное формование бутылок.В одноэтапном процессе ПЭТ-бутылки изготавливаются непосредственно из смолы. Как изготовление преформ, так и формование с раздувом и вытяжкой выполняется на одной линии. (см. Таблицу I)
Машинное оборудование | Номер | Индийская рупия | |||
750000 | |||||
Выдувная машина | 2 | 800000 | |||
Компрессор | 1 | 150000 | |||
Чиллер | 1 | 80000 | |||
Lather 9045, обновленный | |||||
Планка д 5. | 1 | 72000 | |||
Сверло для столба 26 дюймов с насосом | 1 | 50000 9045 Face3 | |||
Shaper | 1 | 125000 |
(Это ориентировочные оценки, поэтому предполагаемый инвестор должен сделать свои собственные расчеты на основе исследования рынка).Требуются термопластавтоматы двух разных размеров, поскольку предлагаемая производственная смесь зависит от разных размеров. Обычный срок поставки техники составляет 15-20 дней, а импорт может занять до 4 месяцев, в зависимости от наличия. Машины для формования с раздувом и вытяжкой производятся на месте. Необходимые для мастерской токарные станки, кольцевые сверлильные станки, фрезерные станки и профилировщики также производятся на месте. (см. Таблицу II)
Человеческие ресурсы | Число | Годовая зарплата | ||||||||||||||||||||||||||||||||||||||||||||||||||||||||||||||||
360000 | ||||||||||||||||||||||||||||||||||||||||||||||||||||||||||||||||||
Менеджер по производству | 1 | 1 | ||||||||||||||||||||||||||||||||||||||||||||||||||||||||||||||||
Бухгалтер Операторы литьевых машин | 2 | 168000 | ||||||||||||||||||||||||||||||||||||||||||||||||||||||||||||||||
Операторы выдувных машин | 2 | 168000 | 30,000 | |||||||||||||||||||||||||||||||||||||||||||||||||||||||||||||||
Помощники | 4 | 120,000 | ||||||||||||||||||||||||||||||||||||||||||||||||||||||||||||||||
3 |
3 | 9 Земельный участок и здание: Площадь около 5000 кв. Ключевые допущения: 288 дней в год Годовая производственная мощность 5 840 640 бутылок, загрузка производственных мощностей (1-й год) 40 процентов, темпы роста производственных мощностей (годовые) 2 процента, максимальная загрузка производственных мощностей 95 процентов, использование производственных мощностей в первый год 2 304 288 бутылок. (см. Таблицу III)
|
Комментариев нет