Производство подошвы для обуви: Мегапласт — производство подошв для обуви
Производство Подошв обувных оптом на экспорт. ТОП 28 экспортеров Подошв обувных
Продукция крупнейших заводов по изготовлению Подошв обувных: сравнение цены, предпочтительных стран экспорта.
- где производят Подошвы обувные
- ⚓ Доставка в порт (CIF/FOB)
- Подошвы обувные цена 18.01.2022
- 🇬🇧 Supplier’s Shoe soles Russia
Страны куда осуществлялись поставки из России 2018, 2019, 2020, 2022
- 🇺🇦 УКРАИНА (31)
- 🇰🇿 КАЗАХСТАН (17)
- 🇦🇿 АЗЕРБАЙДЖАН (7)
- 🇧🇾 БЕЛАРУСЬ (4)
- 🇲🇳 МОНГОЛИЯ (2)
- 🇵🇱 ПОЛЬША (2)
- 🇺🇿 УЗБЕКИСТАН (2)
- 🇹🇷 ТУРЦИЯ (2)
- 🇩🇪 ГЕРМАНИЯ (1)
- 🇫🇷 ФРАНЦИЯ (1)
- 🇿🇼 ЗИМБАБВЕ (1)
- 🇮🇹 ИТАЛИЯ (1)
- 🇲🇩 МОЛДОВА, РЕСПУБЛИКА (1)
- 🇰🇬 КИРГИЗИЯ (1)
Выбрать Подошвы обувные: узнать наличие, цены и купить онлайн
Крупнейшие экспортеры из России, Казахстана, Узбекистана, Белоруссии, официальные контакты компаний. Через наш сайт, вы можете отправить запрос сразу всем представителям, если вы хотите купить
Подошвы обувные.
🔥 Внимание: на сайте находятся все крупнейшие российские производители Подошв обувных, в основном производства находятся в России. Из-за низкой себестоимости, цены ниже, чем на мировом рынке
Поставки Подошв обувных оптом напрямую от завода изготовителя (Россия)
Крупнейшие заводы по производству Подошв обувных
Заводы по изготовлению или производству Подошв обувных находятся в центральной части России. Мы подготовили для вас список заводов из России, чтобы работать напрямую и легко можно было купить Подошвы обувные оптом
Подошвы и каблуки из пластмассы
Изготовитель полиуретаны
Поставщики адгезивы на основе полимеров товарных позиций — или каучука
Крупнейшие производители формы для литья резины или пластмасс
Экспортеры пигменты и препараты
Компании производители Машины инжекционно- литьевые
Производство Гвозди и кнопки
Изготовитель Прочее оборудование
Поставщики части для оборудования для обработки резины или пластмасс или для производства продукции из этих материалов
Крупнейшие производители Формы для литья резины или пластмасс
Экспортеры невулканизированные резиновые смеси
Компании производители материалы смазочные не содержащие нефть или нефтепродукты
Производство органические красящие вещества синтетические и препараты
Сополимеры этилена с винилацетатом
поливинилхлорид пластифицированный
Пигменты и препараты
пластины
Используемые материалы и технологии ГК «Спецобъединение»
Подошва – это самое главное в обуви. Между тем, когда мы выбираем обувь, мы гораздо больше внимания уделяем деталям верха, подкладке, но редко задумываемся, из чего же сделана подошва, которая, собственно и призвана дать обуви почти все те защитные свойства, которые ей необходимы. Ниже даны самые популярные на сегодняшний день материалы, из которых изготавливаются подошвы для спецобуви и их сравнительные характеристики.
Достоинства | Недостатки |
Полиуретан | |
| |
ПВХ | |
| |
Нитрил | |
|
|
Термоэластопласт (ТЭП) | |
Термополиуретан (ТПУ) | |
|
Работа на производстве часто связана с риском падения тяжелых предметов. Носочная часть рабочей обуви укрепляется металлическим или пластиковым элементом, который называется подноском. Подноски могут быть изготовлены из самых разных материалов, но наиболее распространенными являются металл и композит.
Вид подошвы | Вес | Сопротив-
ление скольже- нию | Сопротив-
ление истираемо- сти | Прочность | Прочность крепления к верху кожаной обуви | Стойкость к много-
кратному изгибу | Морозо- стойкость | Термо- пластич-
ность | Крупные грунто-
зацепы | МБС | КЩС |
ПВХ | большой | среднее | низкое | низкая | низкая | низкая | средняя | высокая | нет | редко | редко |
ТЭП | большой | высокое | низкое | низкая | средняя | средняя | средняя | высокая | да | редко | редко |
ЭВА | малый | низкое | среднее | низкая | высокая | низкая | нет | нет | нет | да | да |
ПУ | малый | среднее | высокое | высокая | высокая | средняя | нет | нет | нет | да | да |
ПУ/ПУ | средний | низкое | высокое | высокая | высокая | средняя | нет | нет | нет | да | да |
ТПУ | большой | высокое | высокое | высокая | средняя | высокая | да | высокая | да | да | да |
ПУ/ТПУ | средний | высокое | высокое | высокая | высокая | высокая | да | высокая | да | да | да |
Резина (нитрил) | большой | высокое | высокое | высокая | высокая | высокая | да | нет | да | да | да |
Резина (нитрил)/ПУ | средний | высокое | высокое | высокая | высокая | высокая | да | нет | да | да | да |
Возврат к списку
Производственные направления
Производство «Обуви России» базируется в Новосибирске и Новосибирской области. В настоящее время «Обувь России» производит обувь со всеми основными типами крепления подошвы — клеевым, литьевым, комбинированным. А фабрика «Обуви России» является одной из самых передовых с точки зрения технологий и используемого оборудования в нашей стране. «Обувь России» производит ассортимент для собственной розницы, а также изготавливает обувь по заказам других торговых сетей.
Фабрика «Обуви России» характеризуется высокой степенью автоматизации производства и использованием современного высокотехнологичного оборудования:
Автоматизированных системам раскроя и пошива обуви, таких как Orisol.
Роботов АББ.
Высокопроизводительных литьевых машин, таких как DESMA.
Систем компьютерного моделирования и 3D-принтеров.
Производство «Обуви России» включает следующие направления:
Линия по производству обуви с клеевым методом подошвы из натуральной кожи
На предприятии осуществляется производство, начиная с подготовки верха обуви и заканчивая закреплением подошвы и финишной обработкой продукции.
Включает в себя участки по изготовлению подошв, каблуков, основных стелек и колодок. Завод комплектующих обеспечивает не только потребности компании, но и осуществляет поставки внешним потребителям.
Автоматизированный производственный комплекс для производства обуви из ЭВА
Новая производственная линия была запущена весной 2014 года. Инвестиции в закупку нового оборудования составили 1,7 млн евро. Поставщиком оборудования выступила немецкая компания Bohmer Technik GmbH. Производственный комплекс позволяет осуществлять полный цикл производства обуви, включая отлив в пресс-форму, усадку на колодку и т. п. Мощность производственного комплекса составляет 500 тыс. пар обуви в год.
Фабрика по производству обуви литьевым методом
В ноябре 2015 года «Обувь России» приобрела 100% обувной компании S-TEP, в состав которой входит обувная фабрика в городе Бердске Новосибирской области и подразделение по оптовой продаже обуви. Фабрика S-TEP осуществляет полный цикл производства обуви с литьевым методом крепления подошвы, производство полностью автоматизировано. Работает на рынке уже 15 лет, оснащена современным высокотехнологичным оборудованием от лидеров в своих отраслях — литьевые агрегаты DESMA , автоматизированные раскройные комплексы Newlast, швейные системы Orisol, роботы АББ, ЧПУ-станки; на предприятии можно осуществлять 3D-моделирование обуви.
Линия по производству специальной обуви
Начала работать в мае 2016 года на производственной площадке в городе Бердске. Линия оснащена оборудованием известной компании Svit. Для запуска линии «Обувь России» освоила новую технологию — метод горячей вулканизации резины на заготовку.
Изготовление подошвы обуви в Санкт-Петербурге по привлекательной стоимости \ Обувная мастерская Алеганна
Изготовление подошвы обуви в мастерской «Алеганна»: качественно, недорого
Ненадежная подошва – проблема обуви многих изготовителей, и обидно порой выкидывать красивые на вид и очень удобные туфли или ботинки только потому, что она пришла в негодность. К счастью, сегодня можно починить подошву обуви или заменить ее полностью в ремонтной мастерской, доверив такую работу профессионалам. Воспользоваться данной услугой стоит в таких случаях, как частичный или полный износ подошвы, ее чрезмерная тонкость, значительные повреждения, полученные в результате механического воздействия, полное отхождение от верха обуви и т. д. Если туфли или сапожки являются эксклюзивными, целесообразно обращаться к услуге индивидуального изготовления подошвы.
Если вы задались целью продлить эксплуатационный срок своей обуви, приносите ее в ремонтную мастерскую «Алеганна». Мы работаем не первый год и успели завоевать доверие многочисленных клиентов. Помимо опыта, наша мастерская может похвастать и другими достоинствами, благодаря которым нам доверяют даже самые взыскательные заказчики:
- Высококвалифицированный персонал. Мастера «Алеганны» способны изготовить подошву для обуви любой сложности и восстановить ее в случае частичного разрушения.
- Использование высокотехнологичного оборудования. С помощью станков мастера выполняют сложный ремонт обуви, за который берется не каждая мастерская в Санкт-Петербурге.
- Оперативное выполнение заказов. Мы ценим время своих посетителей, поэтому стараемся укладываться в минимальные сроки, если нужно отреставрировать или заменить подошву полностью.
- Индивидуальный подход к клиентам. Мастера «Алеганны» с каждым заказчиком обсуждают нюансы ремонта и предоставляют широкий выбор материала.
Изготовление подошв обуви: разновидности и особенности
Изношенная подошва требует обязательного ремонта или замены, поскольку ее дальнейшая эксплуатация может привести в негодность и остальные детали обуви. Однако исправление даже незначительных дефектов – сложная задача, решить которую способен лишь квалифицированный специалист по ремонту обуви.
В мастерской «Алеганна» это понимают, поэтому всю работу по изготовлению подошвы для обуви выполняют профессионалы. Они используют исключительно легкие износостойкие материалы проверенных поставщиков. Прежде чем изготовить подошву на заказ или частично ее заменить, мастера тщательно изучают модель и форму обуви, чтобы новая деталь подошла к ней идеально.
Если же подошва стандартная, мастера используют для ее замены готовые шаблоны после согласования с клиентом. Вы можете отдать предпочтение деталям с протектором, с бортиком или без него, опираясь на свой вкус и бюджет. Представленные в ассортименте материалы производятся на фабриках России, Китая, Германии, Италии и Испании, поэтому каждый сможет найти вариант, отвечающий всем его запросам.
Изготовление подошвы в мастерской «Алеганна – выбор практичных людей
Почему изготовить подошву сапог или ботинок многочисленные клиенты доверяют мастерам «Алеганны»? Чтобы ответить на этот вопрос, перечислим ряд плюсов, обеспечивающих выгоду обращения именно к нам:
- Адекватная стоимость услуги по ремонту подошвы обуви. Наши расценки устраивают людей с разным достатком.
- Мы стараемся чаще радовать своих клиентов, предлагая услуги со скидкой или проводя различные акции.
- Высокое качество выполненной работы. Чтобы сделать подошву обуви на должном уровне, мастера «Алеганны» используют свой опыт и навыки, которые и являются гарантией превосходного результата.
Изготовление подошвы и её установка
Изготовление подошвы и её установка
Замена подошвы на новую изготовленную в мастерской подошву под определенный тип обуви с учетом желаний клиента к форме и материалам.
Как это делается. Репортаж с производства специальной обуви
Обувь специального назначения — неотъемлемая часть средств индивидуальной защиты, без упоминания которой наш цикл статей о спецодежде не был бы полным. Само производство обуви связано с рядом технических нюансов, напрямую влияющих на ее качество. Поэтому мы решили посвятить этому направлению отдельную статью — репортаж с производственной линии СООО «Стецкевич-спецодежда», раскрывающий все секреты создания современной обуви с нуля.
Спецобувь предназначается для работников, которым требуется дополнительная защита ног от производственных рисков и неблагоприятных факторов окружающей среды. Диапазон характеристик такой обуви очень широк и напрямую зависит от области ее применения. Спецобувь может обладать устойчивостью к кислотам и щелочам, масло- и бензостойкостью, влагонепроницаемостью. Отдельные модели способны выдерживать сверхвысокие и сверхнизкие температуры (например, ботинки пожарного используются при температурах от –60 до +300 градусов). Нередко обувь специального назначения оснащается усиленным подноском (из металла или поликарбоната), фиксатором пятки или антипрокольной стелькой — все для защиты стопы от повреждений. Выпускают ботинки и с улучшенной фиксацией голеностопа, что снижает вероятность вывихов. Словом, специальная обувь может быть как комфортной ежедневной «одеждой» для ног, так и настоящей броней, значительно повышающей безопасность труда. Причем одно другого не исключает. Но из каких материалов ее делают?
Материал верха обуви — преимущественно, натуральная кожа. Ее качество и уровень обработки влияют на комфортность носки и защитные свойства изделия. Однако не менее важный показатель качества обуви — материал, из которого изготовлена подошва. Наиболее распространены подошвы из ПУ (полиуретана), комбинированные из ПУ и ТПУ (термополиуретана), нитрила. Эти материалы обладают высокой износостойкостью и гибкостью, устойчивостью к маслам, нефтепродуктам, щелочам. Термополиуретан практически по всем характеристикам превосходит полиуретан. Но и вес его выше, поэтому большая часть производимой в РБ и РФ обуви содержит комбинированную подошву ПУ/ТПУ. Такая подошва обладает и большей гибкостью по сравнению с ТПУ-монолитной. Последний, относительно новый для нашего рынка материал — нитрил. Подошва из него характеризуется еще более высокой износо-, термо- и химической стойкостью, для большинства видов работ этот материал наиболее оптимален.
Второй важный показатель качества — способ крепления подошвы к верху обуви. Наиболее распространенными являются: литьевой, метод прессовой вулканизации и клеепрошивной. Литьевой способ — наиболее современный. Он исключает вероятность возникновения зазора между верхом обуви и подошвой, попадание влаги внутрь, что иногда случается с обувью, скрепленной другими способами. Литье подошв применяется сегодня на производствах большинства экономически развитых стран мира.
Рассмотрим процесс изготовления обуви специального назначения подробнее. На производство поступает сырье — в большинстве своем это натуральные материалы. Из них кроят детали различными способами: либо рубят прессом со специальными режущими формами (резаками), либо нарезают на автораскройном комплексе.
Автоматический раскройный комплекс «Atom» предназначен для раскроя деталей верха и низа будущей обуви. Натуральные материалы кроятся на нем в один слой, искусственные — в несколько, в зависимости от их толщины. Голенище, ремень, подносок, задник, стелька, вкладная стелька — комплекс позволяет кроить любые обувные детали.
На начальном этапе модельер создает карты раскроя на компьютере. Затем карта проецируется откалиброванными проекторами прямо на материал, где автоматически раскладывает проекции деталей таким образом, чтобы они занимали максимальную площадь материала, и отходов было как можно меньше. Проекторы еще и помогают оператору визуально контролировать весь процесс. Если он увидит, что можно добавить в раскладку еще несколько мелких деталей — он это сделает «вручную», при помощи компьютерной мыши.
Затем раскроенные детали поступают на швейное производство, где сшиваются в единое целое — верх обуви. На пошивочном участке происходит затяжка обуви на колодку, крепится стелька, вставляется подносок и задник (их наличие зависит от модели). И уже затянутые заготовки пакуются в коробки, отправляются на участок для прилива подошвы.
Для наглядности рассмотрим процесс литья на примере комбинировонной подошвы из полиуретана и термополиуретана. Поступившие со швейной ленты заготовки обуви одевают на алюминиевую колодку в форме стопы (ее габариты соотносятся с распространенными размерами обуви). Колодка вставляется в свое посадочное место на автоматической линии Desma. Сама линия представляет собой «карусель» из 18 посадочных позиций, что позволяет одновременно изготавливать 9 пар обуви. Каждое посадочное место оснащено поворотным механизмом, позволяющим менять положение заготовки (верхнее/нижнее) на определенной стадии работы. На первой стадии колодки с надетыми на них заготовками устанавливаются в положение «сверху».
«Карусель» прокручивается и приносит закрепленную заготовку к роботу — координатно программируемой «руке». Робот производит «взъерошивание»: абразивным кругом подпиливает верхнюю часть кожи по контуру прилегания будущей подошвы. Это делается для того, чтобы сцепление бортика подошвы с кожей было наилучшим.
После обработки роботом «карусель» снова приходит в движение и заготовка перемещается к оператору, где он переворачивает ее сверху вниз. Заготовку помещают в пресс-форму, где происходит впрыск полиуретана.
Вкладыши поступают на производство в готовом виде, их отливает отдельная организация. Но оборудование Desma позволяет производить обувь и с цельной ПУ-подошвой. В таком случае полиуретан заполняет весь объем пресс-формы, низ которой выполнен в форме протектора.
Далее заготовку прокручивают к месту впрыска полиуретана. Впрыск в пресс-форму производится через узкое отверстие, чтобы избежать миграции материала. Пресс-форма четко задает размеры между заготовкой (верхом обуви) и нижней частью, поэтому весь объем заполняется полностью и равномерно.
Полиуретан в пресс-форме должен провести определенное время (время выдержки) при заданной температуре. Это нужно для того, чтобы заготовка хорошо «схватилась» с полиуретаном после его впрыска.
После выдержки заготовка с подошвой проходит по кругу до следующего оператора, который снимает ее и кладет в специальную холодильную установку, где подошва за считанные секунды остывает до комнатной температуры, а полиуретан окончательно принимает заданную структурную прочность.
По завершении литья на подошве остаются «бортики» (облой), могут встречаться и наплывы ПУ. Все это убирается вручную с каждой единицы обуви на машине для обрезки облоя. После чего обувь поступает на участок отделки.
На отделке изделию придают окончательный лоск: убирают все мелкие дефекты и окрашивают специальным составом — аппретурой. В ее состав входят пропитки, которые проникают глубоко внутрь кожи, закрепляют ее водоотталкивающие свойства и придают обуви «товарный» вид. После завершения этой операции внутрь вкладывают стельку и передают изделие на контроль качества.
Контролер сверяет каждый экземпляр с эталонным образцом, находящимся у него перед глазами. Поступившие к нему изделия должны строго соответствовать ГОСТу, в котором прописаны правила приемки и допуски по всем основным параметрам. В случае возникновений каких-либо подозрений (например — на неправильный размер обуви) производится обмер измерительными инструментами. Прошедшая контроль обувь поступает на шнуровку и пакуется в коробки, отправляясь на склад готовой продукции, откуда отгружается клиентам.
В соседнем цеху функционирует вторая линия Desma. Она предназначена для литья нитрила — более современного, но и более дорогостоящего материала для подошвы. Линия включает 12 посадочных позиций и позволяет лить подошвы для 6 пар обуви одновременно.
Сырьем для литья служит резиновая лента, поступающая от стороннего производителя. Лента заправляется внутрь шнека, где разогревается до температуры 170–175 градусов, при которой происходит вулканизация резины. Размягченная резина впрыскивается в пресс-форму тем же методом, что и на линии ПУ-литья.
После чего заготовка выдерживается заданное время, извлекается из пресс-формы и остывает естественным способом. Далее все происходит по вышеописанному техпроцессу: обрезка облоя, отделка, контроль и упаковка.
Результатом всех вышеперечисленных операций становится широкий ассортимент обуви, способный удовлетворить потребности любого производства, строительной компании или отдельно взятого человека. На этом мы прощаемся с производством обуви, но не прощаемся с нашими читателями — впереди вас ждет подробный репортаж о крупнейшем производстве спецодежды в Республике Беларусь. Следите за обновлениями на сайте!
Обувь ручной работы: этапы производства
Туфли и ботинки, сделанные полностью вручную, встречаются сегодня очень редко и стоят дорого — примерно от 400 евро, если мы говорим о Венгрии, и примерно от 600 евро, если речь идёт о Западной Европе и более или менее известных мануфактурах. На производство такой обуви затрачивается много времени, но оно того стоит: у туфель полностью ручной работы, например, можно большее число раз заменять подошву; они немного по-другому выглядят, а зачастую ещё и более комфортны. В этой статье мы опишем ключевые этапы создания туфель ручной работы на ранту.
Оглавление:
Раскрой кожи
Естественно, кожа для обуви ручной работы кроится только вручную. Если речь идёт о пошиве обуви на заказ, то используются индивидуальные, специально созданные лекала для вырезания кусков кожи. Для готовой обуви используются стандартные лекала, обычно изготовленные из плексиглаза или другого современного материала.
Для раскраивания шкур обувщики используют нож-кликер, а сама эта процедура называется кликингом (clicking).
Раскрой кожи для обуви
Перед выполняющим её работником стоит непростая задача: нужно использовать шкуру максимально рационально, отбраковав при этом все участки с дефектами. В случае с очень дорогой обувью, сшитой на заказ, используются лишь самые лучшие участки шкуры, причём многие шкуры отбраковываются ещё на этапе закупки.
Сшивание частей верха
На следующем этапе, который называется клоузингом (closing), вырезанные части кожи сшиваются друг с другом — и получается верх обуви.
Сшивание частей верха обувиПомимо этого, верх сшивается с подкладкой, а также осуществляется декорирование отдельных частей верха — например, брогирование. На обуви полностью ручной работы брогирование делается вручную, без использования машин — и это занимает довольно много времени по сравнению с брогированием на фабричной обуви, где одна машина может делать дырочки одновременно на десяти кусках кожи.
Натягивание верха на колодку
Готовый верх обуви нужно натянуть на колодку, и эту операцию — ластинг (lasting) — делает ластер (laster). В случае с фабричной обувью ластинг обычно осуществляется полностью или частично с помощью специальных машин, что заметно сокращает издержки.
Натягивание верха обуви на колодкуЛастер — это ремесленник, натягивающий кожу на деревянную колодку и временно прибивающий её гвоздиками. Позже, когда верх накрепко пришивается к ранту, гвозди снова вынимаются. Молоток часто намагничивается для облегчения манипуляций с множеством мелких гвоздей.
Бернхард Ретцель, автор книги «Джентльмен»
Стоит добавить, что раньше колодки изготавливались исключительно из дерева, но сегодня в ряде случаев даже для обуви на заказ (bespoke) используются колодки из пластика. У производителей готовой обуви имеются готовые колодки, а мастера, которые шьют заказную обувь, либо вытачивают колодки под клиента, либо используют готовые колодки разных размеров и форм, к которым по мере надобности прикрепляют в необходимые места куски кожи, чтобы добиться соответствия формы колодки форме стопы клиента.
Подготовка внутренней подмётки и пришивание ранта
Обувь полностью ручной работы часто шьётся с использованием ранта, причём этот рант пришивается вручную. Во внутренней подмётке (insole) вручную вырезается гребень, и после этого к нему и к верху вручную пришивается рант; сама подмётка тоже вырезается вручную. Это довольно трудоёмкая операция, и в случае с фабричной обувью сам процесс упрощают: гребень не вырезают в самой подмётке, а приклеивают к ней, используя заметно более тонкие подмётки (а сам гребень при этом сделан из текстиля). Рант к подмётке и верху на фабричной обуви пристрачивает машина, и делает это очень быстро.
Вырезание гребня на внутренней подметке
Сшивание ранта, гребня и верха обуви
В чем же заключается преимущество ручной работы на данном этапе? Знатоки говорят, что ручное крепление ранта (hand-welting) позволяет большее число раз заменять подошву; кроме того, hand-welted обувь при прочих равных оказывается более комфортной.
Пришивание подошвы и крепление каблука
После того, как рант соединен с внутренней подмёткой и верхом, на подмётку помещают пробковый наполнитель (cork filling) — это могут быть пробковые брикеты или же вязкая смесь на основе пробковой крошки.
На следующем этапе — soling — рант сшивается с внешней подошвой (outsole).
Сшивание ранта с внешней подошвой обувиНа обуви полностью ручной работы это делается вручную, иглой и нитью — такая операция трудоёмкая и длительная, и поэтому даже на hand-lasted и hand-welted обуви шов, соединяющий рант и внешнюю подошву, довольно часто выполняется с помощью машины. После крепления к верху «талия» (средняя часть) подошвы на туфлях ручной работы обычно изящно закругляется.
Далее осуществляется сборка каблука. На классических туфлях каблуки наборные — они сделаны из нескольких слоев кожи и резины, которые крепятся друг к другу и к подошве при помощи клея и маленьких гвоздиков. На сравнительно недорогих фабричных туфлях часто используются слои не из кожи, а из кожкартона — это обходится дешевле.
Сборка составного каблукаФинишинговые процедуры
После крепления подошвы и каблука туфли проходят ещё несколько процедур. В частности, ребро подошвы и каблука, и сами каблук и подошва шлифуются, вручную окрашиваются и полируются. Верх туфель вручную полируется, на него может наноситься уникальная патина с помощью красок и кремов.
Окрашивание каблука
Окрашивание верха обуви
Внешняя сторона подошвы и её верхний край иногда обрабатываются вручную зубчатыми колесиками. Затем в туфли вставляются стельки, обувь проверяют на отсутствие дефектов, после чего зашнуровывают и упаковывают.
Оборудование для производства обуви
Используя современное технологичное оборудование для производства обуви, изготовители существенно повышают качество готовой продукции, в разы увеличивают масштабы выпускаемых партий, сокращают себестоимость работ. Все эти факторы являются залогом рентабельности предприятия в условиях жесткой конкуренции.
Что нужно для оснащения обувного цеха
Процесс изготовления обуви делится на четыре базовых этапа, на каждом из которых используется специализированное оборудование для пошива обуви:
- раскрой — раскройные комплексы, оборотные и траверсные вырубные прессы;
- заготовка — специальные прессы, машины для двоения кожи, швейные машины и т.
д.;
- пошив — устройства для затяжки и формования, фиксации подошвы, стелек, прибивки каблуков и пр.;
- финишная обработка — автоматы для устранения дефектов, обжига нити, покраски и т. п.
Где купить оборудование
Вы сможете купить оборудование для производства обуви в Москве, обратившись в компанию «Грамос». Предприятие реализует качественные специализированные машины и устройства от ведущих мировых производителей. Преимущества для клиентов:
- Большой опыт работы. Компания была основана в 1999 году.
- Широкий ассортимент. Всегда в наличии любые модели.
- Экономия. Цены на оборудование для изготовления обуви остаются доступными, несмотря на внешние обстоятельства.
- Удобные условия. Оперативная доставка станков во все регионы России.
Специалисты компании «Грамос» оказывают профессиональную помощь в выборе машин и станков, ориентируясь на специфику предприятия заказчика, его требования к мощности, производительности и экономичности.
Мы предлагаем купить оборудование для производства обуви и получить бесплатный гарантийный сервис на протяжении одного года. Опция включает в себя пусконаладочные работы, регулярные плановые проверки (раз в три месяца) и устранение неисправностей (замену деталей).
Чтобы получить консультацию и заказать оборудование для обуви с доставкой по России, оставьте заявку на сайте или свяжитесь с представителем фирмы любым удобным способом.
Как делают подошву для обуви
Мы считаем само собой разумеющимся резину на подошве нашей обуви — материал, который сцепляет и удерживает нас в обуви для тенниса, кроссовках, повседневной обуви и даже в классических туфлях. Но как резиновая подошва обуви стала настолько привычной? И как современные производители массово производят миллионы резиновых подошв, которые необходимо выпускать каждый год, чтобы обеспечить безопасность и комфорт ног во всем мире?
Процесс производства обуви восходит к 1844 году, когда Чарльз Гудьир совершил прорыв после многих лет экспериментов. Он использовал процесс, который назвал «вулканизацией», чтобы нагреть натуральный каучук, чтобы смешать его с серой — смесью, которая помогла создать тип резины, используемой сегодня в подошвах обуви.
Мы по-прежнему используем тот же метод вулканизации для создания резины для подошвы обуви. Сочетание отверждения, смешивания и нагрева в Goodyear привело к созданию прочных подошв обуви, которые мы знаем сегодня.
Процесс изготовления обувной подошвы
Мы являемся специализированной химической компанией, специализирующейся на выпуске пресс-форм для полиуретановой интегральной обшивки для подошв обуви.Мы являемся небольшой, но важной частью процесса, который помогает обуви завершиться и найти свое место на ваших ногах. Процесс включает в себя:
- Резиновая подошва Прессование: Обувные формы используются для изготовления двух деталей — стельки и подошвы. Во-первых, подошва подготавливается цветом для логотипа, а также фоновым цветом.
Средняя пластина закрывается с добавлением красителей, а затем сырая резина помещается в форму, где она вскоре зальется и сформирует подошву.Закройте полную форму и нагрейте в течение короткого времени, чтобы создать подошву. После извлечения из духовки излишки резины отрезаются, оставляя идеально сформированную подошву.
- Резиновая стелька Штамповка: Вместо логотипа и цвета фона для стельки требуется цвет каблука. Добавьте сырой каучук, который сформирует передний край, и поместите форму обратно в тепло, чтобы сформировать стельку.
- Плавка: Теперь пришло время сплавить стельку и подошву, чтобы получилась готовая резиновая подошва.После сплавления просто отрежьте лишнюю резину и наслаждайтесь красивой (и удобной) резиновой подошвой, которая сделана не так уж и иначе, чем Чарльз Гудьир делал свою резину более 150 лет назад.
Этот процесс может различаться в зависимости от типа подошвы, которую вы создаете, и типа обуви, для которой вы ее создаете. Но основные элементы процесса одинаковы, и вы можете найти этот базовый процесс на заводах по всему миру. Операции по смешиванию и прессованию каучука грязные, с большим количеством движущихся частей и большим количеством излишков, поэтому этот процесс так часто передается на аутсорсинг.Но поскольку эти фабрики специализируются на производстве резиновых подошв, они могут выполнять большие объемы работ и выпускать невероятное количество подошв каждый день — эффективно и точно.
Индивидуальные решения для высвобождения пресс-форм
В WN Shaw мы специализируемся на формовании полиуретана, резины и композитных материалов, включая разделительные составы для подошв как одинарной, так и двойной плотности. С 1985 года мы обслуживаем производителей специальными разделительными составами для моделей, повышая ценность благодаря нашим экономичным решениям и передовым технологиям.
Мы можем создавать индивидуальные решения для выпуска пресс-форм для производителей, работающих в различных отраслях, обувном производстве и не только. Мы также можем адаптироваться по мере появления новых технологий и инноваций. Мы разделяем вашу потребность в создании максимально эффективных и доступных процессов.
У нас есть практический опыт, полученный в нашем собственном цехе, где эти специальные разделительные составы тестируются и разрабатываются. По мере того, как мы совершенствуем эти разделительные составы, мы делаем их доступными для производителей в США и Канаде, а также через дистрибьюторов в Мексике, Китае, Японии, Азии, Южной Америке и Европе.Наш глобальный охват дает нам опыт и знания в режиме реального времени о том, что работает, а что нет, а также об агентах, продуктах и возможностях, которые производители больше всего ценят.
Высококачественная продукция
Мы гордимся тем, что продолжаем традицию производства высококачественной обувной подошвы, отдавая дань уважения наследию Чарльза Гудиера. В процессе производства обувной подошвы мы уделяем особое внимание деталям и добиваемся результатов, отражающих максимальную заботу. Если вам нужны нестандартные разделительные составы для изготовления обувных подошв, обращайтесь в компанию W.N. Shaw — компания, которая предлагает опыт, знания и ресурсы для выполнения работы.
Свяжитесь с нами
Свяжитесь с нами сегодня, чтобы получить информацию о разделительных составах для однослойных подошв одинарной и двойной плотности.
(PDF) Передовые технологии производства обувной подошвы
с индивидуальной односторонней боковой клиновидной стелькой, напечатанной на 3D-принтере, и продемонстрированная реабилитация при ходьбе
[2]. Несмотря на форму, различные материалы, используемые для изготовления стелек, играют важную роль, влияя на тыльное и подошвенное сгибание голеностопного сустава и максимальное сгибание колена
при ходьбе [3].Исследования, проведенные несколькими авторами, пришли к выводу, что производство
анатомических стелек с помощью 3D-печати экономически выгодно и осуществимо на промышленном уровне [4],
с уменьшением давления [5] и с использованием 3D-сканирования, что делает его доступным вариантом для
обувь [6]. С инструментами САПР, разработанными группой авторов, можно сократить время, повысить качество и функциональность. Более того, технология 3D-печати предлагает новые возможности для изготовления изделий сложной геометрии [7].Подошва обычно изготавливается из кожи
, вулканизированной резины, TPR (термопластичной резины), полиуретанов, TPU (термопластичных
полиуретанов) или EVA (этиленвинилацетата) [8]. Твердость подошвы играет важную роль в комфорте обуви
. Тесты, проведенные на взаимосвязь между распределением давления стопы
и твердостью подошвы, показали большое влияние на комфорт обуви [9]. Из-за неправильной геометрии
и сложных свойств материала подошв, компьютерное моделирование, как
методы МКЭ помогают изучить взаимодействие обуви и обуви, где персонализация
стелек более важна для снижения пикового подошвенного давления, чем жесткость материала
используется для изготовления стелек [10].С помощью реверс-инжиниринга изготовленная обувь может быть использована для изучения и предложения улучшений распределения материала внутри промежуточной подошвы
[11]. Результаты, полученные в результате моделирования методом конечных элементов стельки и промежуточного слоя подошвы, изготовленных из
различных вспененных материалов, как в случае со спортивной обувью, оптимизируют распределение модуля упругости
в промежуточной подошве для улучшения работоспособности [12] с целью снижения силы реакции на грунт
[13].Кроме того, эти приложения помогают контролировать свойства подошвы за счет использования решетчатых структур
[14] и за счет сочетания механических структур метаматериалов с
создавать персонализированные подошвы [15] и обувь с помощью 3D-печати [16]. Решетчатые структуры
генерируются некоторыми программами САПР, но они могут создавать трудности при
операционализации процесса проектирования. Чтобы избежать этого, исследователи разработали интерфейс
на языке программирования Visual Basic, который основан на функциях API
SolidWorks.Это может помочь в автоматическом создании сложных моделей решетчатых структур
[17] и использовании метода конечных элементов для исследования механических свойств
каждой конфигурации решетчатой структуры [18] и производстве с помощью 3D-печати и инвестиционного литья
[18]. 19]. Другой инновационный метод, такой как деформация ограниченной свободной формы и 3D-сканирование
, продемонстрировал большое влияние, ускорив процесс разработки и производства обуви
[20].Поскольку обувь является интерфейсом между стопой и полом
, что важно для каждого человека, исследование, понимание и управление биомеханикой стопы посредством измерения давления являются обязательными для проектирования обуви
. Подошвенное давление стопы — это поле давления, которое действует между стопой и
опорной поверхностью во время повседневной двигательной активности. Одной только оценки подошвенного давления
недостаточно для тщательного изучения биомеханики стопы.Подошвенное давление, однако, имеет большой потенциал в области исследований и настройки обуви [21].
2 Практический пример – Модернизация обуви с топологической оптимизацией
На основе биомеханических данных
Чтобы продемонстрировать потенциал сочетания биомеханики с несколькими цифровыми и физическими
технологиями, представлен пример дизайна обуви. Основное внимание уделяется модели подошвы, которая была
, ранее разработанная в программе Shoemaker, как показано на рисунке 1.В предыдущей работе было реализовано
численное моделирование подошвенных моделей. При этом без учета
соображений карты давления на стопы [22]. Но принимая во внимание биомеханический фактор, заключающийся в том, что
каждый человек демонстрирует асимметричное поведение между обеими сторонами, биомеханическое исследование
началось с определения подошвенного давления стопы, чтобы понять
различия между левой и правой стопой.
MATEC Web of Conferences 318, 01012 (2020) https://doi.org/10.1051/matecconf/202031801012
Патенты и заявки на крепление резиновой подошвы (класс 12/142RS)
Номер патента: 5843268
Abstract: Раскрыто изделие обуви, состоящее из относительно эластичных и относительно неэластичных материалов, химически связанных друг с другом. В одном варианте осуществления относительно эластичный и относительно неэластичный материалы расположены таким образом, чтобы придать изделию обуви гибкость. В частности, пластик и резина соединяются вместе для повышения гибкости подошвы обувного изделия. Изобретение также направлено на изготовление новых или усовершенствованных устройств и элементов для использования в обувных изделиях и связанных с ними способов изготовления, таких как запорные механизмы, содержащие относительно эластичные ремни, прикрепленные к относительно неэластичным анкерным частям, и наоборот, шарнирно-сочлененные неэластичные и эластичные экзоскелеты. конструкции, используемые в коньках и лыжных ботинках, а также эластичные или неэластичные проушины, окруженные неэластичными или эластичными материалами.
Тип: Грант
Подано: 15 мая 1995 г.
Дата патента: 1 декабря 1998 г.
Правопреемники: Найк, Инк., Найк Интернэшнл Лтд.
изобретателей: Роберт М. Лайден, Росс А. Маклафлин, Генри Т. Крисс, Кэлвин М. Бак, IV, Дэниел Р.Поттер, Стивен М. Винсент
Материалы для подошв обуви: определения и типы
Подошва – это основная часть обуви, которую многие покупатели игнорируют при покупке. Итак, в этой статье поговорим о материалах подошвы обуви!
Сегодня мы хотим обсудить материалы подошвы обуви. В статье ниже представлены восемь самых популярных материалов. Что касается руководства по покупке, мы рекомендуем сначала обратить внимание на материалы, а затем на различные системы крепления.
Последние можно объединить в следующие группы:
- Термопластичные материалы: PVC – TR – TPU
- Двухкомпонентные полиуретановые материалы: PU на основе полиэфира – PU на основе полиэстера
- Сополимеры : такие как каучук и EVA посмотрите на все, кроме материалов подошвы обуви: Однако тип используемого материала, система крепления между подошвой и верхом, рисунок протектора и общая толщина могут многое сказать о типе обуви, которую вы покупаете.
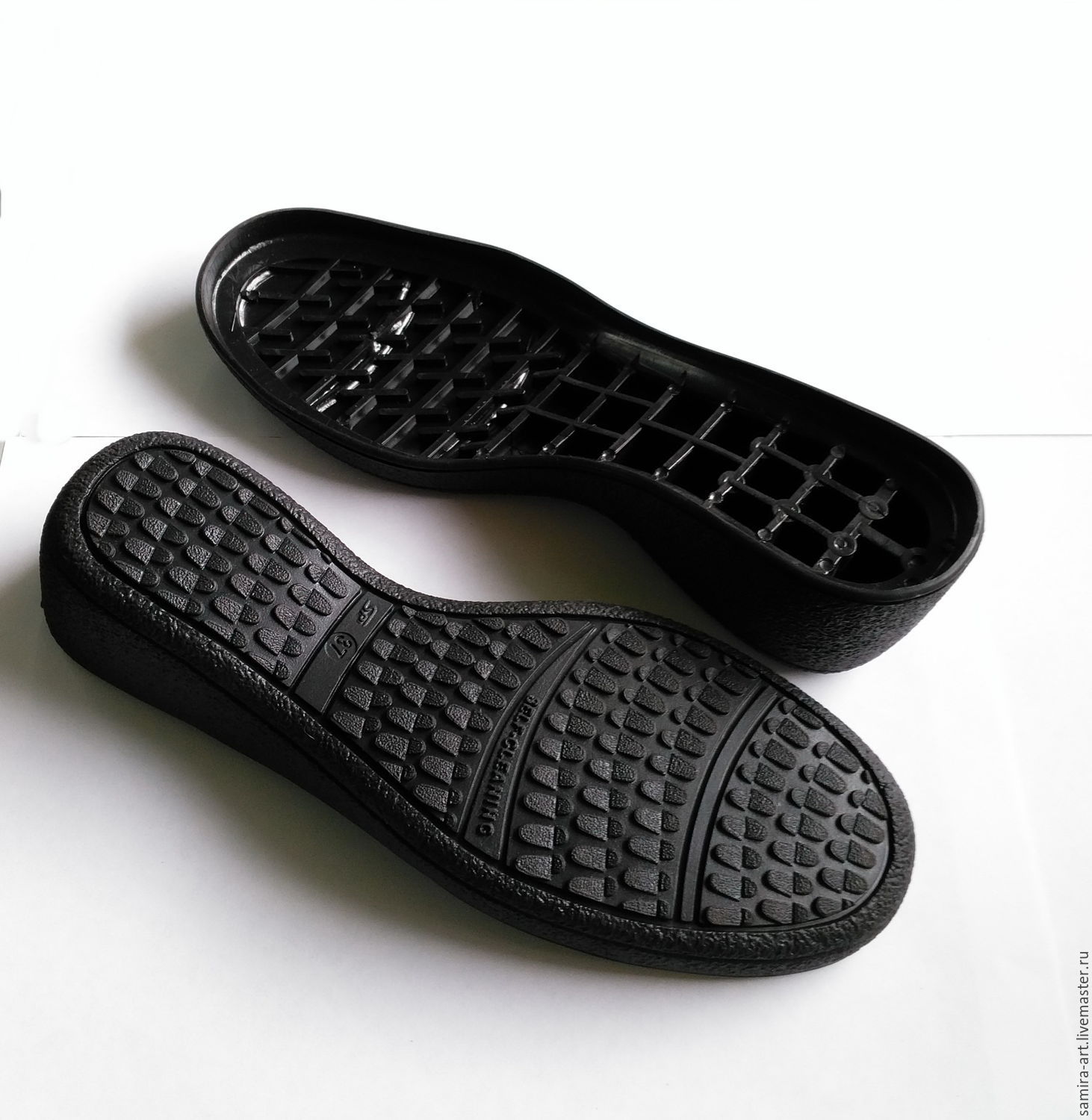
Тип материала подошвы обуви
Ассортимент материалов, доступных обувным предприятиям для изготовления подошвы, широк. Это позволяет им давать наиболее подходящие ответы на различные потребности в качестве, стоимости и функциональности. Они варьируются от натуральных материалов, таких как кожа, веревка, пробка, дерево и пара, до синтетических материалов. Закончить комбинированными материалами, составляющими подошву. Вот основные материалы подошвы обуви:
Полиуретановая подошва
Полиуретандоступен в двух формах для изготовления подошв для обуви.Термопластичный полиуретан популярен для изготовления спортивной, защитной рабочей обуви и обуви для отдыха. В противном случае двухкомпонентный полиуретан, как следует из названия, доступен в жидкой форме, состоящей из изоцианата и полиола.
Определение подошвы TPR
Думая о материале подошвы обуви, многие сразу думают о термопластичной резине (TPR)? Их наиболее важным ингредиентом является знаменитый стирол-бутадиен-стирол (SBS), который может улучшить производительность.
Есть и другие вещества, например минеральные наполнители.Антиоксиданты доступны время от времени, в зависимости от использования и производителя. Подошвы из термопластичной резины идеально подходят для зимней обуви, гарантируя отличные характеристики даже при низких температурах.
Идеально подходит для изготовления подошв, как накладных, так и для прямого впрыска на верх. Подошвы TPR представляют собой соединения, основным компонентом которых является стирол-бутадиен-стирол (SBS) с добавлением масел, полистирола, минеральных наполнителей, пигментов и антиоксидантов. Термопластичные каучуки при правильном планировании не имеют проблем с морозостойкостью и могут сохранять отличную гибкость при температурах намного ниже 0 градусов.
Материал резиновой подошвы
Термопластичный полиуретан (ТПУ) состоит из полиуретановых эластомеров, обработанных по технологии термопластичных материалов. Люди производят их с помощью процесса добавления изоцианата и имеют эластичные характеристики каучука в диапазоне температур.
Термопластичные полиуретаны идеально подходят для различных подошв, предназначенных для обуви для спорта, работы и отдыха. Из-за своей специфики они требуют особого типа рецептуры в соответствии с механическими характеристиками конечного продукта.
Полиуретан Материал подошвы
Двухкомпонентный полиуретан доступен в жидкой форме и содержит полиол и изоцианат. Эти продукты принадлежат к двум различным классам: простые полиэфиры и сложные полиэфиры. Разница между этими двумя классами членства определяется структурой пены. Полиэфир образует компактную поверхностную кожу, а внутри подошвы он представлен открытыми ячейками. Полиэстер имеет закрытые ячейки.
Материал кожаной подошвы
Кожаные подошвы идеально подходят к элегантной кожаной обуви.Среди их преимуществ — высокая воздухопроницаемость в сочетании с отличной стойкостью. Он предлагает эти характеристики, чтобы иметь эффективную подошву.
Нет необходимости прибегать к значительной толщине, чтобы всегда иметь легкую обувь. Благодаря своеобразному расположению волокон кожа устойчива к проколам. Наконец, несмотря на подчеркнутую воздухопроницаемость, кожа гарантирует хорошую теплоизоляцию.
Кожа состоит из крошечных нитевидных волокон, сгруппированных в более крупные волокна и переплетенных друг с другом по трехмерному рисунку.Он образует систему каналов и проходов для воздуха. Его физических характеристик много, но наиболее важными для его использования являются:
- Воздухопроницаемость благодаря высокому коэффициенту пористости
- Низкий удельный вес относительно толщины и поверхности, что на практике означает легкость
- Значительная термостатическая способность с последующей термозащитой стопы
- Высокая устойчивость к перфорации благодаря особому асимметричному расположению волокна, переплетенные трехмерным образом
- Превосходная структура для обеспечения электрического баланса организма после плохой изолирующей способности для электричества
Материал подошвы ПВХ
Винилхлорид (ПВХ) — один из самых распространенных пластиков в мире. Производитель находит свое применение в обуви как для сапог, так и для изготовления подошв, сандалий и аксессуаров. Благодаря постоянному технологическому развитию, он достиг хорошего уровня экологической эффективности и эффективности применения, что позволяет гарантировать максимальную безопасность на всех этапах его жизненного цикла.
Материал подошвы из ЭВА
EVA представляет собой полимер, состоящий в основном из этилена и винилацетата. Соотношение между двумя компонентами и процентное содержание сшивающих агентов, наполнителей и расширяющих агентов.Мы добавляем их в компаунд, чтобы определить его эксплуатационные характеристики. EVA в основном идеально подходит для производства подошв и промежуточных подошв. Микропористые подошвы, характеризующиеся легкостью, гибкостью и эластичностью, обладают способностью сохранять первоначальную форму.
Комбинированные материалы
Среди феноменов эволюции подошвы — сочетание материалов, отвечающих стилистическим, техническим и стоимостным требованиям. Все это сочетается с сдерживанием затрат и выходом визуально привлекательного изделия.Комбинации различаются по типу материалов, цветам и простоте обработки. В большинстве случаев идеально подходят материалы из полиуретана, резины и EVA.
Базовые знания о подошвах обуви
Обувной сектор предлагает рынку бесконечное количество моделей различных типов: тапочки, сандалии, тапочки; кроссовки, спортивная обувь и обувь для отдыха. У нас также есть классическая обувь для мужчин и женщин, женская обувь на каблуке, обувь для работы и спорта, ортопедическая обувь, защитная обувь, детская обувь и кроссовки.
Подразумевают разные технологии обработки и имеют наиболее существенное отличие в системе крепления подошвы к верху.
Тип подошвы напрямую связан с типом обработки обуви. Можно выделить две большие группы обработки подошвы. К первой группе относятся подошвы, которые будут накладываться непосредственно на собранную колодку и впоследствии дорабатываться. Второй — готовые и моноблочные подошвы. Фабрики подошв готовят их и готовы к сборке верха.
К категории готовых моноблоков относятся многие подошвы из резины или аналогичных материалов. Мы можем печатать их в пресс-формах, подготовленных по шаблонам последнего и не требующих дополнительной отделочной обработки.
Единый регламент
Среди различных действующих на международном уровне стандартов, касающихся подошвы, напомним UNI CEN ISO/TR 20880 от мая 2007 года. У нас есть требования к характеристикам компонентов обуви.
Технический отчет CEN показывает требования к характеристикам подошв для обуви, которые должны быть обязательными для качественной подошвы.Эти требования применяются ко многим подошвам (за исключением готовой обуви) независимо от материала, чтобы проверить их пригодность для последнего использования. Стандарт устанавливает методы испытаний, используемые для оценки соответствия этим требованиям.
Дополнительная информация на этикетке
Рынок обуви, в том числе благодаря онлайн-продажам и глобализации торговли, все больше наводняется обувью со всего мира. Счета-фактуры и качество сильно меняются, но даже продукты с самой скромной стоимостью все чаще делаются с обманчивым внешним видом.Важно уметь хорошо читать этикетки, чтобы различать тип используемого материала, отталкиваясь от того, что разрешено законодательством, и что запрещено.
Можно добровольно интегрировать обязательную информацию с другими дополнительными указаниями, если они соответствуют надлежащему коммерческому использованию, например, указания на качество используемых материалов и отделки.
Необязательная информация, которая должна быть представлена на официальном языке Европейского Союза, не может заменить обязательную информацию о составе продукта.Факультативные указания, если они применяются, должны быть четкими, разборчивыми и правдивыми и не должны вводить потребителя в заблуждение.
- Торговая марка Vero Cuoio сигнализирует потребителю о том, что материал. Материал, который они штамповали, — кожа. Это добровольная торговая марка.
- Торговая марка Vero Cuoio Italiano относится к коже высшего качества, выдубленной с использованием экстрактов растительного происхождения и произведенной в Италии только на кожевенных заводах, принадлежащих консорциуму Vero Cuoio.
- Для присвоения готовой продукции надписи «сделано в Китае» единственным параметром является европейское таможенное законодательство (Таможенный кодекс Сообщества РЕГ.2913/92/ЕЕС и положения о применении РЕГ. 2454/93/ЕЕС).
Производитель подошвы может указать происхождение товара, нанеся надпись только на внутреннюю часть самой подошвы. Текст должен быть на итальянском или другом официальном языке Сообщества (Постановление Министра от 30 января 2001 г.).
Обязанности производителя
Они требовали от производителя или его представителя в Европейском союзе предоставить этикетку и обеспечить точность содержащейся информации.На нем также должны быть указаны идентификационные и контактные данные производителя, а также информация для отслеживания происхождения продуктов (например, код продукта).
Если ни производитель, ни представитель не следуют за территорией Европейского Союза, указанные выше обязательства несет первый коммерческий оператор сообщества. Продавец должен позаботиться о проверке этикетки на обуви, которую он продает. Мы должны обеспечить выставление в местах продажи конечному потребителю и вывески, иллюстрирующей установленную законодательством символику.
Минэкономразвития осуществляет функции органа по надзору за рынком. Он осуществляет их с помощью Торговых палат и, возможно, в сотрудничестве со своими территориальными отделениями, а также в сотрудничестве с Guardia di Finanza. Выявлением нарушений занимаются территориально уполномоченные Торгово-промышленные палаты, а также Агентство по делам таможни и монополий и сотрудники и агенты судебной полиции.
Территориально компетентные торговые палаты налагают административные санкции.Наблюдение осуществляется путем визуально-формальной проверки или анализа образцов и может осуществляться на обуви, имеющейся на производственных и торговых площадках.
Как подошвы крепятся к обуви?
Иногда мы слышим о прошитых, вулканизированных или инжектированных подошвах. Но о чем мы говорим? Это способ крепления подошвы к верху обуви. Иногда, например, их просто приклеивают, используя мастику, совместимую с используемым для их изготовления материалом.
В другое время шьем вручную или на машине, а в другое время подошвы вулканизируем. Мы также использовали этот термин в рекламных сообщениях. Это свидетельствует о том, что мы привариваем подошву непосредственно к верху обуви, используя подогретые формы.
При покупке новых видов обуви всегда стоит ориентироваться на их подошву. Трекинговая или туристическая обувь должна соответствовать определенным требованиям. Важно иметь достаточно базовых знаний, чтобы понять, что у вас в руках!
Как делают обувь: шаг за шагом
Еще в золотой век обуви ручной работы сапожник нес ответственность за процесс изготовления обуви от начала до конца.Теперь может показаться, что быстрая мода царит безраздельно, но в создание обуви ручной работы по-прежнему вкладывается много любви. Теперь, в отличие от оригинальных сапожников, качественная обувь изготавливается с использованием процесса производства раскроя. Итак, если ваш вопрос: «Как фабрика производит обувь?», мы рассмотрим это подробнее. При производстве раскроя различные отделы фабрики выполняют разные этапы производственного процесса. Когда отдел заканчивает свою роль, обувь отправляется в следующий отдел в очереди.
И, в отличие от одноразовой модной обуви, сделанная на заказ обувь проходит удивительно большое количество различных этапов, прежде чем ее можно будет носить. Не все производители одинаковы, и количество этапов зависит от используемых ими методов производства. Ищете приблизительную фигуру? Скажем так, обувь можно создать за 70 шагов, а можно за 390!
Как фабрика производит обувь?Если у вас кружится голова от этого числа, вы, вероятно, хотели бы точно знать, как делают обувь.Не волнуйтесь, потому что мы не пройдем эти 390 или даже 70 шагов! Мы просто дадим вам всесторонний взгляд за кулисы процесса изготовления обуви.
Шаг 1: Команда разработчиков
Различные отделы отвечают за различные аспекты процесса производства обуви. Если вы запускаете собственную торговую марку, вам понадобится помощь от прототипа до готового продукта. И в первую очередь это отдел дизайна. Это ребята с творческим видением.Люди, которые знают, что заставляет обувь хорошо выглядеть и хорошо работать. Клиент предоставляет первоначальные эскизы, а штатные дизайнеры дорабатывают их, чтобы обеспечить их техническое соответствие процессу изготовления обуви. Некоторые дизайнеры обуви предпочитают рисовать от руки, другие используют компьютер. Но каждый законченный дизайн будет изображать обувь с разных сторон.
Этап 2: Последний отдел обуви
Прежде чем обувь пойдет в производство, ей нужна колодка.Это физическая основа того, как сделана ваша обувь. Обувная колодка — это форма, которая имитирует стопу, чтобы придать обуви ее форму. Традиционно они вырезались из дерева, но теперь также используются пластик и металл. Каждой левой и правой туфле нужна колодка, чтобы можно было определить ее форму и размер. Но колодка — это не кусок дерева в форме ступни, и при ее создании необходимо учитывать ряд моментов. Это включает в себя то, как стопа перекатывается при ходьбе, и как это повлияет на такие факторы, как высота каблука.Позже в процессе изготовления обуви колодка помещается внутрь обуви, чтобы ее можно было смоделировать вокруг нее. Он используется снова, как только обувь почти готова, чтобы убедиться, что посадка конца соответствует оригинальному дизайну.
Шаг 3: Штамповка и шитье
Отчасти из-за огромного количества деталей, используемых для изготовления одного ботинка, конструирование обуви является настоящим ремеслом. Детали, необходимые для изготовления обуви, вырезаются из высококачественной кожи, а затем в процессе производства обуви идет штамповка.Теперь обувь называется голенищем, а куски кожи, из которых она сделана, штампуются или маркируются. Это делается для того, чтобы избежать путаницы, когда они сшиты вместе. После того, как детали проштампованы, они помечаются, чтобы указать, где нужно пробить проушины. Если на обуви должны быть акценты с перфорацией, например, броги, они также помечаются. Как и точки кожи, которые будут сшиты вместе, чтобы получился шов. Затем сшиваемые части кожи истончаются перед отправкой голенища в швейный цех.
Обувь прошивается и отправляется в отдел сборки штампов. Никаких призов за догадки, что это означает сборку обуви — это сама основа того, как создается ваша обувь. Если обувь представляет собой классические дерби или оксфорды, можно использовать технику, называемую обшивкой Goodyear.
Типы конструкции обуви Сварка Goodyear — это сложный процесс изготовления обуви, восходящий к 1872 году. Первым шагом с помощью трех гвоздей является временное прикрепление стельки под колодкой.Затем к стельке прикрепляется резиновый выступ – это облегчает пришивание голенища к ранту Goodyear в дальнейшем. Вал шнуруется и надевается поверх последнего. Затем он прикрепляется к стельке с помощью горячего клея и гвоздей. Следующий шаг может занять от 30 минут до двух недель. Это когда голенище и колодка отложены в сторону, чтобы кожа безупречно приняла форму колодки.
Обувь в идеальном состоянии! Пришло время пришить кусок кожи шириной примерно 3 мм — рант — к стельке и подкладке.Рант пришивается на швейной машине Goodyear. Это требует точности, чтобы гарантировать, что рант находится как можно ближе к стержню и резиновому выступу.
Прелесть стежка Goodyear в том, что он полностью невидим, поскольку находится на внутренней стороне обуви. Обувь, использующая эту технику, обычно не имеет ранта, охватывающего всю стельку, за исключением пяточной части. Вместо этого голенище и стелька скреплены гвоздями, а кусок кожи в форме каблука, называемый окантовкой, соединяет их.Когда трубка будет прибита к стельке маленькими латунными штифтами, убедитесь, что она остается на одном уровне с валом. Теперь пришло время убрать последнее, что было с нами на каждом этапе пути. Между пяткой и передней частью обуви вставляется голенище, обеспечивающее поддержку перед продолжением процесса изготовления обуви.
Следует отметить, что не во всех мужских туфлях используется рант Goodyear. Еще одним популярным выбором для производителей обуви на заказ является метод Блейка.Как правило, рант Goodyear чаще используется в обуви британского производства. Особенно те, которые производятся в Нортгемптоне, городе традиционного сапожного дела в Великобритании. Тем временем метод Блейка популярен в континентальной Европе, особенно в Италии. Но каковы различия между ними?
Конструкция Blake немного старше, чем рант Goodyear, датируется 1856 годом. Сшивание вручную невозможно и выполняется с помощью швейной машины Langhorn. Сапожник прошивает каждый слой обуви — голенище, стельку и подошву — без рантов.Те, кто предпочитает Blake, скажут вам, что их обувь менее жесткая и более удобная в носке. Однако Goodyear выносливее и лучше работает в сырую погоду. (Важное соображение в Великобритании!)
Обувь Blake не имеет внешних швов и обычно имеет более плотный покрой, чем обувь Goodyear. Верх и подошва образуют более плотное соединение, снова создавая ощущение гибкости. Это подчеркивается тем фактом, что в процессе производства обуви Blake используется меньше слоев. Обувь Goodyear с рантом имеет больше слоев, что обеспечивает более прочную конструкцию, которая лучше служит мужчинам, заботящимся о стиле, во влажном климате! Однако, если влажная погода не является проблемой, то, как сделана ваша обувь, будет иметь меньшее значение.При условии, что они стильные, хорошо сделаны и помогут вам или вашим клиентам выделиться из толпы!
Шаг 5: Стельки для ступеней и украшения
Если вы запускаете собственную линию обуви, вам будет приятно узнать, что ваша обувь приобретает довольно хорошую форму. Но он по-прежнему не выглядит особенно стильно, и его внутренняя часть все еще находится на грубой и готовой стороне. Для решения этой проблемы добавляется слой наполнителя. Для обеспечения комфорта и движения наполнитель должен быть гибким, поэтому обычно используется пробка. Это выровняет основу для стельки, которая будет приклеена, а затем надежно пришита к ранту.
Как вы, наверное, уже догадались, изготовление обуви — немалый подвиг мастерства! Но наш процесс изготовления обуви еще не закончен. Теперь штифты, которые были вставлены в пятку, будут удалены, а отверстия, которые они оставили в коже, заделаны. На этом этапе позаботятся о любой декоративной перфорации. Или, если поверхность обуви гладкая, отверстия в швах тщательно скрываются с помощью процедуры глажки, окрашивания и полировки.Далее обтачивают край каблука и его подошву и декорируют видимую часть ранта. Затем уплотняют двойной шов и окрашивают пятку и кончики подошвы. В последнюю очередь вставляется полустелька с логотипом бренда и тщательно чистится обувь.
Этап 6: обувная
Вы знаете почти все, что касается обучения изготовлению обуви. И мы приближаемся к концу нашего пути. Последняя остановка: обувная комната.Это может показаться сбывшейся мечтой для любителей обуви. Но вместо того, чтобы быть гардеробной, полной брогов и ботинок, это место, где обувь отправляется на последнюю любовную ласку. Это отдел отделки, где сшитая на заказ обувь получает последние штрихи, которые отличают ее от своих более дешевых кузенов. Туфли начищены до блеска и, если того требует стиль, зашнурованы.
После этого каждая обувь проходит тщательную окончательную проверку качества. Затем они упаковываются и отправляются розничному продавцу, готовые для взыскательного покупателя — вас!? – покупать и носить с гордостью.
Возвращение производства обуви в Соединенные Штаты сопряжено с трудностями: NPR
Рабочие шьют обувь на фабрике в Цзиньцзяне, провинция Фуцзянь на юго-востоке Китая. Почти вся обувь, продаваемая в США, произведена за границей. Доля Китая снизилась, но он по-прежнему остается крупным источником. AFP/Getty Images скрыть заголовок
переключить заголовок AFP/Getty Images Рабочие шьют обувь на фабрике в Цзиньцзяне, провинция Фуцзянь на юго-востоке Китая. Почти вся обувь, продаваемая в США, произведена за границей. Доля Китая снизилась, но он по-прежнему остается крупным источником.
Обновлено в 11:04 по восточноевропейскому времени
Для Дугласа Кларка самой мрачной частью работы в Nike в 1980-х годах было наблюдение за тем, как американское производство обуви «испарялось» на северо-востоке в результате массового исхода в Азию в погоне за более дешевой рабочей силой.
«Как истинный янки — а мой отец был колониальным историком — знаете, это было душераздирающе», — сказал он.
Кларк сделал долгую карьеру в обувном бизнесе Converse, Reebok, Timberland, а затем создал собственную линию обуви в New England Footwear. И там он посвятил восемь лет одной миссии: созданию модели, которая снова сделает производство обуви в Америке прибыльным.
Это была трудная задача. В то время, когда президент Трамп говорит о восстановлении американского производства, обувь является ярким примером того, как трудно повернуть время вспять.
В наши дни 99% обуви продается в США.С. завозятся, многие из них из Китая, Вьетнама и Индонезии. Доля Китая в последние годы снизилась, но он остается ключевым источником обуви и запчастей для обуви в Америке. Вот почему некоторые обувные компании США были ярыми противниками угрозы Трампа о повышении тарифов почти на все, что импортируется из Китая.
«Мы хотели бы производить обувь в Соединенных Штатах», — сказал NPR генеральный директор Steve Madden Эд Розенфельд. Но «очень сложно представить себе сценарий, в котором мы будем производить продукты, которые мы производим, по ценам, которые мы их производим, в Соединенных Штатах.»
Для работы на обувной фабрике с оплатой 12 долларов в час фактическая стоимость изготовления обуви — с добавлением льгот — вырастает до 16 долларов в час по сравнению с примерно 3 долларами в час в Китае, сказал Майк Джеппесен, глава глобальных операций Wolverine Worldwide, которая владеет такими брендами, как Merrell, Sperry и Keds. По его словам, эта стоимость увеличивается в четыре раза после оптовых и розничных наценок, что приводит к разнице в цене в 50 долларов между парой, произведенной в США, и парой, произведенной в Китае.
«На самом деле очень мало коммерческих причин для того, чтобы делать обувь в США.S. сегодня», — сказал Джеппесен. Он признает одно исключение из этого: фабрики, которые работают, чтобы удовлетворить постоянный спрос на обувь американского производства со стороны вооруженных сил США. — сказал Том Кэппс, чья компания Capps Shoe Co. в Вирджинии в основном производит форменную обувь для правительства. 10 человек, по данным Обувных дистрибьюторов и розничных продавцов Америки.
Владельцы американских фабрик, производящих невоенную обувь в Америке, заявили, что нашли собственные причины остаться. Многие ссылались на свою любовь к ремеслу и традициям. Кэппс сказал, что он также нашел свою нишу, предложив большой выбор размеров. Оливье Маршаль из Sense of Motion Footwear в Колорадо обеспокоен воздействием на окружающую среду доставки обуви и материалов со всего мира в Азию.
Но У.Владельцы фабрик S. также назвали две основные проблемы отечественного производства обуви: поиск квалифицированных рабочих и доступные детали и материалы.
New Balance известен тем, что все еще производит или, по крайней мере, собирает некоторые кроссовки в США. Но компания получает «некоторые компоненты для нашего внутреннего производства из Китая, а также из других стран из-за ограниченной цепочки поставок в США», — сказала исполнительный директор Моника Горман. Торговые представители США в понедельник.
С исчезновением рабочих мест в обувном производстве исчезла и сеть поддержки отрасли.Поставщики таких вещей, как маленькие металлические люверсы и красочная кожа, следовали за отраслью за границей. Многие обувные фабрики превратились в склады и офисы.
San Antonio Shoemakers производит обувь в Техасе с 1970-х годов. Недавно SAS получила крупный контракт на производство кроссовок для армии США. Карсон Фрейм / Американский проект тыла скрыть заголовок
San Antonio Shoemakers производит обувь в Техасе с 1970-х годов.Недавно SAS получила крупный контракт на производство кроссовок для армии США.
Карсон Фрейм / Американский проект тылаДэн Хезелтон выпускает мокасины Maine Mountain Moccasin на одной из таких фабрик, которая освободилась во время исхода.
«Мы публикуем вакансии, — сказал он, — и очень редко кто-то моложе 40 лет приходит к нам, чтобы подать заявку». Среди оставшихся рабочих артрит — обычное дело.
«Многие люди неоднократно говорили, что они определенно не хотят, чтобы их сын или дочь делали это», — сказал Хезелтон.«Это тяжело слышать».
Из-за более высокой стоимости рабочей силы и материалов в США оставшиеся производители, как правило, полагаются на своих покупателей, предпочитающих платить больше за бренд «Сделано в Америке».
«Мы знаем, что не можем сделать обувь за 19 долларов для продажи в Target или Walmart. Это просто невозможно для нас», — сказала Нэнси Ричардсон, генеральный директор SAS, компании среднего размера, которая производит обувь в США. Сан-Антонио с 1970-х годов. «Поэтому мы фокусируемся на том, чтобы люди чувствовали, что они получают пару обуви за 800 долларов за 150 или 200 долларов.»
Тем временем компании массового рынка сосредоточили свои операции в США больше на дизайне и маркетинге, оставив все операции по вырезанию, склеиванию и сшиванию производителям за границей.
Кларк хотел это изменить. В своей миссии по возвращению массового производства в Америку он сосредоточился на стоимости и сложности труда, связанного с изготовлением обуви.
СШАВладельцы фабрик часто говорят, что хотели бы, чтобы люди знали, сколько деталей и процессов требуется для изготовления обуви. Есть несколько слоев для создания одной подошвы, в том числе множество тяжелых швов. Закрепление низа обуви выполняется в несколько этапов. К тому времени, когда обувь будет готова к носке, над ней могут работать десятки людей.
Кларк знал об этом и о борьбе производителей США с материалами, деталями и рабочими. Но он также знал, что история уже начинает повторяться в Китае.Зарплата там росла. Обувные компании снова переезжают в другие страны в погоне за более низкими затратами.
Это может стать началом возвращения Америки, подумал Кларк. Но чтобы это заработало, процесс нужно было упростить — может быть, десяток деталей вместо 50 — и еще больше автоматизировать. Возможно, тогда, по его словам, производство могло быть «там, где есть рынки, а не там, где рабочая сила».
Несколько лет назад он получил контракт с крупным брендом и грант для начала работы.Он начал с изготовления верхних частей или верха, «что не требовало много труда», — сказал он.
Обувное производство уже давно включает станки для резки или склеивания подошв. Но инновации более высокого уровня? По иронии судьбы, владельцы фабрик заявили, что это происходит там, где находится промышленность, — за границей.
Крупные бренды, такие как Nike и Adidas, разрабатывают новые технологии, в том числе в США, но они по-прежнему сильно зависят от фабричных рабочих за границей.Потому что, в отличие от людей, роботы не шустрые — они не могут заметить недостатки или быстро переключиться на новый стиль одежды.
«Роботы не прощают», — сказал Кларк.
Для Кларка история закончилась печально. Разработка автоматизации стала очень дорогой и продвигалась медленнее, чем ожидалось. Он истощал свои средства и согласился продать свою фабрику технологической компании, которая знала толк в роботах. Фабрика сейчас закрыта.
Кларк подписал соглашение о неконкуренции, так что теперь «по сути, я ушел в отставку не по своей воле», — сказал он.Он надеялся, что его наследие возродит американское производство обуви. Вместо этого он сейчас занимается недвижимостью.
Полимерная 3D-печать для компонентов обуви
Полимерная 3D-печать для компонентов обуви | воксельджет Мы используем файлы cookie на нашем веб-сайте.
Некоторые из них необходимы, а
другие помогают нам улучшить наш онлайн
улучшать наши онлайн-сервисы и управлять ими экономично.
Вы можете принять это или нажать
кнопка «Принимать только необходимые файлы cookie
кнопку «принять».Вы можете найти дополнительную информацию
вы найдете в нашем заявлении о защите данных. Если вам меньше 16 лет и вы хотите дать согласие на дополнительные услуги, вы должны спросить разрешения у своих законных опекунов. Мы используем файлы cookie и другие технологии на нашем веб-сайте. Некоторые из них необходимы, в то время как другие помогают нам улучшить этот веб-сайт и ваш опыт. Персональные данные (например, IP-адреса) могут обрабатываться, например, для персонализированной рекламы и контента или измерения рекламы и контента. Более подробную информацию об использовании ваших данных вы можете найти в нашей политике конфиденциальности.Вы можете отменить или изменить свой выбор в любое время в настройках.
Выбрать все
Подтвердить выбор
Принимать только необходимые файлы cookie
Индивидуальные настройки файлов cookie
Сведения о файлах cookie Политика конфиденциальности Выходные данные
Защита данных
Если вам еще не исполнилось 16 лет, и вы хотите дать согласие на дополнительные услуги, вы должны спросить разрешения у своих законных опекунов. Мы используем файлы cookie и другие технологии на нашем веб-сайте. Некоторые из них необходимы, в то время как другие помогают нам улучшить этот веб-сайт и ваш опыт. Персональные данные (например, IP-адреса) могут обрабатываться, например, для персонализированной рекламы и контента или измерения рекламы и контента. Более подробную информацию об использовании ваших данных вы можете найти в нашей политике конфиденциальности. Вы можете отменить или изменить свой выбор в любое время в настройках. Здесь вы найдете обзор всех используемых файлов cookie. Вы можете дать свое согласие на целые категории или отобразить дополнительную информацию и, таким образом, выбрать только определенные файлы cookie.
Имя | Печенье Борлабс |
---|---|
Провайдер | Eigentümer dieser Сайт, выходные данные |
Назначение | Speichert die Einstellungen der Besucher, die in der Cookie Box от Borlabs Cookie ausgewählt wurden.![]() |
Имя файла cookie | borlabs-cookie |
Время выполнения файлов cookie | 1 Яр |
Имя | Диспетчер тегов Google |
---|---|
Провайдер | Google Ireland Limited, Gordon House, Barrow Street, Dublin 4, Ирландия |
Назначение | Куки-файлы из Google для проверки подлинности скриптов и управления ими.![]() |
Политика конфиденциальности | https://policies.google.com/privacy?hl=de |
Имя файла cookie | _ga,_gat,_gid |
Время выполнения файлов cookie | 2 года |
Имя | Google reCaptcha |
---|---|
Провайдер | Гугл.![]() |
Назначение | Этот файл cookie используется для различения людей и ботов. Это полезно для веб-сайта, чтобы генерировать достоверные отчеты об использовании своего веб-сайта. |
Имя | SmartUTMjar |
---|---|
Провайдер | SmartUTMjar |
Принять | Пиксель Facebook |
---|---|
Имя | Пиксель Facebook |
Провайдер | Meta Platforms Ireland Limited, 4 Grand Canal Square, Dublin 2, Ирландия |
Назначение | Файл cookie от Facebook, используемый для аналитики веб-сайта, таргетинга рекламы и измерения рекламы.![]() |
Политика конфиденциальности | https://www.facebook.com/policies/cookies |
Имя файла cookie | _fbp,act,c_user,datr,fr,m_pixel_ration,pl,presence,sb,spin,wd,xs |
Время выполнения файлов cookie | Сицунг / 1 Яр |
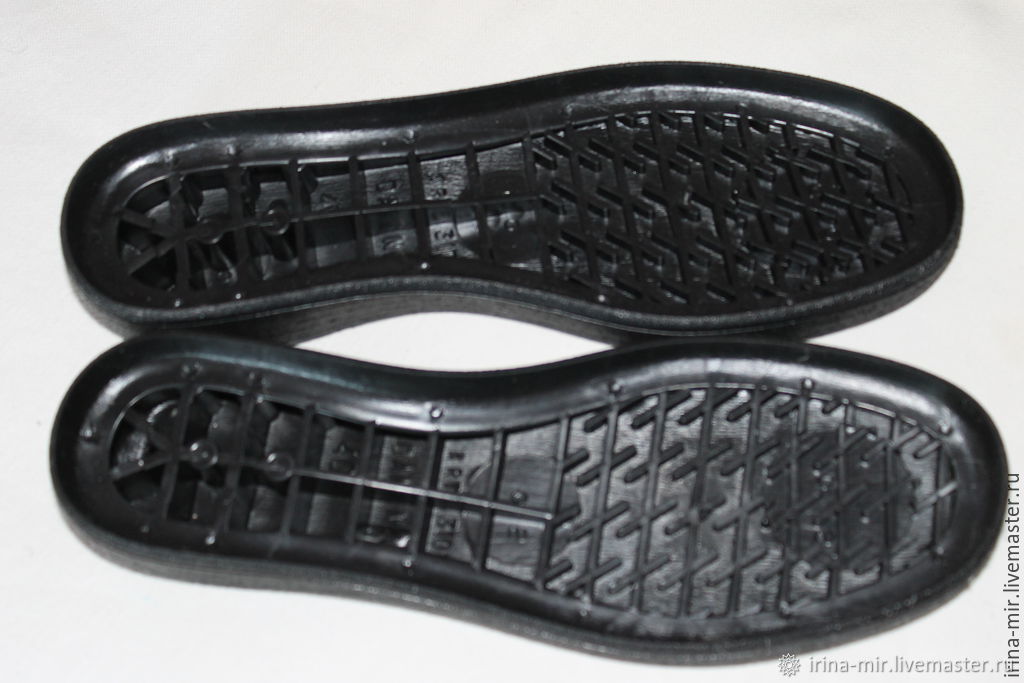
Комментариев нет