Сырье производства цемента: химический состав, формула, технологии производства (+9 фото и 7 видео)
химический состав, формула, технологии производства (+9 фото и 7 видео)
Цемент – это искусственное порошкообразное вещество, которое выполняет функцию вяжущего при замешивании бетонной смеси. В сочетании с водой он образует пластичную массу, которая в дальнейшем застывает и становится камневидной. То, из чего состоит цемент, в первую очередь зависит от способа производства. В общем случае основой служит клинкер в сочетании с минеральными добавками и гипсом.
История цемента
Слово «цемент» происходит от латинского caementum, что переводится как «дробленый, битый камень». Это вещество стало результатом поиска способов справиться с низкой водостойкостью гипсовых и известняковых пород. С этой целью в их состав вводились водостойкие минеральные вещества. В самом начале ими выступали остатки кирпичей из обожженной глины и вулканические породы. Древние римляне применяли отложения пепла знаменитого вулкана Везувия – пуццоланы.
Оптимальная технология производства цемента была выработана много лет спустя, когда потребность в большом количестве недорого и прочного вяжущего не стала наиболее острой. Наибольший вклад в исследования внесли:
- Каменщик Джон Аспинд, который в 1824 г. получил патент на портландцемент.
- Русский строитель Егор Челиев, написавший в 1825 г. книгу о цементе для подводных работ.
Название портландцемент происходит от английского острова Портленд, состоящего из известковых пород. В Англии камни с этого острова считались самым престижным строительным материалом. Аспинду удалось получить искусственный камень, который по прочности и цвету был очень похож на указанный материал.
Но он изготавливался без обжига исходного сырья. Большее соответствие технологии тому, что сегодня является портландцементом, отмечается именно в процессе производства Челиева.
Из чего делают цемент: состав и основное сырье
В состав цемента входят следующие компоненты:
- Известь (оксид кальция, CaO) – 60%.
- Кремниевый диоксид (SiO2) – 20%.
- Алюминий (глинозем, Al2O3) – 4%.
- Гипс и оксиды железа (Fe2O3) – 2%.
- Магния оксид (MgO) – 1%.
Указанное процентное соотношение перечисленных компонентов характерно для наиболее популярного вида цемента – портландцемента. Оно может несколько видоизменяться. Все зависит от технологии производства и класса цементной продукции.
Важно! Существованием различных видов и марок объясняется отсутствие точной химической формулы цемента. Всю важную информацию дают показатели минералогического состава.
Основное, из чего делают цемент – это клинкер. Так называют продукт обжига исходного сырья – известняка и глины, которые берут в пропорции 3:1. Клинкер – это полуфабрикат для получения цемента. После обжига при температуре до 1500 °C клинкер измельчают, в результате чего он оказывается представлен в форме гранул диаметром до 60 мм.
При измельчении в состав клинкера вводят добавки:
- Гипс (CaSO42h3O), регулирующий сроки схватывания.
- Корректирующие добавки (до 15-20%), улучшающие определенные свойства цемента: пластификаторы, присадки и пр.).
В качестве главного исходного сырья для производства цемента используются разные горные породы:
- Ископаемые карбонатного типа. Могут иметь аморфную или кристаллическую структуру, которая определяет, насколько эффективно материал будет взаимодействовать с другими компонентами в составе при обжиге.
- Осадочного происхождения. Это глинистое сырье с минеральной основой, которое при избыточном увлажнении становится пластичным и разбухает, т. е. увеличивается в объеме. Главная особенность материала – вязкость, которой обусловлено его применение при сухом процессе производства.
Советуем изучить подробнее: «Все, что нужно знать о суперпластификаторах, или как уменьшить расход цемента».
Карбонатные породы
Среди карбонатных пород для производства цемента используются:
- Мергелистый известняк, или мергель. Содержит в себе примеси глины, поэтому считается переходным материалом между карбонатными и глинистыми породами.
- Мел – разновидность мажущего известняка, которая характеризуется легкостью в перетирании.
- Ракушечник. Для него характерна пористая структура, которая не слишком устойчива к сжимающим нагрузкам.
- Доломитовые породы. Из всех видов карбонатных пород отличаются самыми ценными физическими свойствами.
Глинистые породы
К глинистым породам, используемым при изготовлении цемента, относятся:
- Глина. Основная разновидность глинистых пород с минеральными включениями в составе.
- Суглинок. Отличается от глины увеличенной концентрацией пылеобразных частиц и песчаной фракции.
- Лёсс. Менее пластичная горная порода. Для нее больше характерны пористость, рыхлость и мелкозернистость. В составе лесса могут присутствовать включения кварца или силиката.
- Глинистый сланец. Из всех видов подобных пород имеет наиболее высокую прочность. При измельчении сланец преобразуется в пластинчатые частицы. В материале мало влаги, его характеризует стабильный гранулометрический состав.
Корректирующие добавки
С целью корректировки в состав цемента вводят специальные минеральные добавки. В первую очередь это модификаторы на базе ископаемых, содержащих:
- железо,
- кремнбелитовый
- плавиковый шпат,
- апатиты,
- глинозем.
Еще корректирующие добавки могут быть представлены промышленными отходами с других производств. В качестве них используются:
- пиритные огарки;
- пыль из доменных печей;
- белитовый шлам;
- минерализаторы.
Применение добавок позволяет улучшить характеристики цемента и бетонного раствора, который готовится на его основе. Каждый из модификаторов придает смеси особые свойства, к примеру:
- CemFrio – обладает противоморозным, пластифицирующим и ускоряющим действиями.
- CemPlast – позволяет получить высокоподвижную бетонную смесь с повышенной удобоукладываемостью, а также повысить активность вяжущего, т. е. цемента, и обеспечить полноту гидратации.
- CemAqua и CemAquaStop – гидроизолирующая дводоредуцирующаясное водоотталкивающее средство для обработки поверхностей.
- CemBase – увеличивает прочность, морозостойкость, водонепроницаемость и долговечность бетонных изделий.
- Plastix – многофункциональная водоредуцирующая и пластифицирующая добавка, повышающая марочную прочность бетонных изделий.
- CemFix – добавка-ускоритель, используемая для бетонных смесей, к которым предъявляются требования высокой ранней прочности.
Как делают цемент: 3 главных способа
Производство цемента в современных условиях осуществляется одним из трех способов:
- Мокрым. Ее главная особенность – замена извести мелом, а также процесс производства с добавлением воды. Сырьем для изготовления здесь становится шихта (смесь исходных материалов) с влажностью до 50%.
- Сухим. Эта технология с минимальными энергозатратами и себестоимостью, поскольку здесь несколько технологических операций объединены в один процесс. Поступая в шаровую мельницу, все компоненты одновременно и размалываются, и сушатся.
- Комбинированным. Этот способ производства объединяет особенности процессов сухой и мокрой технологии. Здесь по результатам обжига получается полусухой состав с влажностью 18%.
Сухой способ производства
Как делают цемент по сухой технологии:
- Исходное сырье подвергают дроблению.
- Просушивают его до определенного уровня влажности.
- Высушенную смесь измельчают до состояния муки.
- Ее обжигают внутри вращающейся печи, после чего охлаждают и отправляют на склад.
Мокрая технология производства
В отличие от сухого метода изготовления здесь после измельчения компонентов к ним дополнительно добавляют воду. В результате получается не мука, а сырьевой шлам, который и попадает в печь на обжиг, а затем – в холодильник на охлаждение. Уже охлажденные клинкер подвергают измельчению и дополнению добавками.
Комбинированная технология изготовления
Комбинированный способ производства цемента объединяет в себе этапы сухого и мокрого:
- Сначала по мокрой технологии получают сырьевой шлам.
- Шлам подвергают обезвоживанию и гранулированию.
- Гранулы проходят обжиг в печи, которая применяется для сухой технологии.
Бесклинкерный способ производства
В бесклинкерной технологии производства в качестве исходного сырья для изготовления цемента используют гидравлический или доменный шлак. Его также дополняют различными добавками и активаторами. Полученную шлако-щелочную смесь подвергают дроблению и перетиранию до порошкообразного состояния. Подобная технология производства имеет несколько преимуществ:
- Повышение чистоты окружающей среды за счет переработки отходов металлургической отрасли.
- Получение продукта с высокой устойчивостью к негативному влиянию окружающей среды.
- Возможность производить цемент с разными свойствами и в широком спектре оттенков.
- Более низкие затраты на электро- и тепловую энергию.
Виды цемента по составу и сфере применения
Видео: что такое шлакопортландцемент
Производство цемента на заводах
Изготовление цемента мокрым способом традиционно осуществляется отечественными цементными заводами. За рубежом чаще применяют сухую технологию. Ею пользуются цементные заводы в Китае, Турции и Египте. Белый цемент выпускается только одним российским предприятием – ООО «Холсим (Рус) СМ». Большая часто подобного вяжущего поставляется зарубежными компаниями, такими как:
- AalborgWhite (Дания).
- Cimsa/Adana (Турция).
- «Холсим» (Словакия).
В общем виде технология производства цемента включает несколько этапов:
- Смешивание всех компонентов для изготовления клинкера (75% известняка и 25% глины).
- Обжиг исходного сырья при высокой температуре. На этом этапе и получают клинкер, который является основой для цемента.
- Измельчение клинкера в шаровых мельницах. В результате должно получиться вещество порошкообразной консистенции. Шаровая мельница – это горизонтальные барабаны со стальными шарами внутри.
Советуем изучить подробнее: «Важная величина: как узнать время схватывания бетона».
Обратите внимание: чем меньше фракция помола клинкера, тем выше эксплуатационные характеристики и марка цементного состава.
Оборудование для производства цемента
Производства цемента на каждом этапе требует применения специального оборудования. Его делят на следующие категории:
- для добычи исходного сырья;
- для транспортировки сырья на место производства;
- печь для обжига;
- шаровые мельницы для измельчения и смешивания клинкера;
- станки для фасовки готового цемента.
Как сделать цемент в домашних условиях
Получить цемент можно в домашних условиях, но только если иметь все исходные материалы и необходимое оборудование:
- доменная печь для обжига при температуре 1500 °C;
- дробилка для измельчения клинкера в муку.
В одном из способов домашнего изготовления цемента используются смола и сера. Полученный цемент можно применять для кладки плитки и кирпича, создания цементной стяжки. Технология изготовления следующая:
- Растопить в металлической емкости 1 кг смолы, в огнеупорной емкости – 1 кг серы.
- Соединить жидкие компоненты, перемешать до однородной консистенции.
- Ввести 2 кг просеянного однородного песка и 3 кг оксида свинца (свинцового глета).
- Постоянно подогревая смесь, размешивать ее до получения однородной массы.
- Произвести обжиг в доменной печи и дать продукту отстояться.
В реальности с изготовлением цемента в домашних условиях возникают определенные трудности, поскольку для производства нужны печь для обжига и мельница для размалывания. В связи с этим в домашних условиях приходится несколько менять рецептуру цемента, используя для его изготовления воду, водную известь и каменную золу. Полученный раствор пригоден для заделки мелких трещин, причем использовать его необходимо сразу же после изготовления.
Видео: как сделать огнеупорный цемент из золы
Как делают белый цемент
Отличие белого цемента также заключается в составе. В нем содержится меньше железа, чем в сером, а еще присутствуют добавки:
- минеральные,
- гипс,
- соли,
- известняк и пр.
Исходным сырьем для изготовления белого цемента служат глинистые или карбонатные породы. Главное преимущество вяжущего – его белоснежный цвет, которая повышает декоративные свойства цементной смеси. Из-за этого белый цемент часто еще называют декоративным. В то же время ввиду более сложной технологии производства материал имеет более высокую стоимость.
Видео: стол из белого бетона в стиле Loft
Видео: как приготовить раствор на белом цементе
Видео: как и из чего делают цемент
Как правильно приготовить цементный раствор
Для замешивания цементного раствора необходимо соблюдать пропорции его составляющих. На 1 часть цемента приходится 3 части песка. Вода же добавляется в зависимости от того, насколько пластичный или вязкий нужно получить раствор. Также пропорции выбираются с учетом типа работ и марки цемента. К примеру, для приготовления раствора на стяжку пола пользуются пропорциями из таблицы:
Сначала между собой смешивают сухие фракции, т. е. цемент и песок. Только потом начинают небольшими порциями добавлять воду, постепенно доводя состав до нужной консистенции. В качестве наполнителя можно использовать не только песок, но еще и гравий или щебень.
Обратите внимание: лучше для замешивания раствора использовать осадочную воду, а не водопроводную.
Классы раствора для разных типов работ:
- М50 или М100 – для штукатурных работ;
- М50 или М100 – для возведения кирпичной кладки;
- М100 или М200 – для стяжки пола;
- М200 или М300 – для фундаментов и оснований.
Для замешивания раствора необходимо использовать специальный поддон или бетономешалку. Последняя позволяет получить смесь наиболее однородной консистенции.
Советуем изучить подробнее: «Что стоит знать при покупке цемента в мешках и как рассчитать количество».
Видео: цементный раствор, приготовления без инструмента
Видео: как правильно замешивать цементный раствор
В заключение
В современном мире цемент производится в большом количестве разных видов, что позволяет подобрать вяжущее для любых строительных работ. За счет применения различных добавок цементу можно придавать определенные свойства и использовать его в различных сложных условиях, например, для конструкций, эксплуатируемых под водой или при низких температурах. Цемент очень прост в применении, а также может быть приготовлен в домашних условиях, если знать его состав и общую технологию изготовления.
состав и производство, как добывают сырье на заводе, технология и изготовление в домашних условиях
Цемент входит в число основных строительных материалов. Он используется при создании связующих строительных растворов, цемент используют при изготовлении бетонных и железобетонных изделий. От качества данного материала зависит, насколько прочное и долговечное будет здание, или железобетонная конструкция.
История цемента началась в Англии, где в 1824 году был зарегистрирован патент на его изобретение. В то время для изготовления цемента использовалась известковая пыль, смешанная с глиной. Полученная смесь подвергалась воздействию высокой температуры, при которой она спекалась.
Обожжённый полуфабрикат цемента называется клинкер. Цементом он становится после перемалывания клинкера до порошкообразного состояния.
В строительстве используется основное свойство цемента – при смешивании с водой он постепенно твердеет, а затем превращается в прочный камень. Характерную для готового изделия прочность материал может приобрести даже в воздушной среде, если присутствует избыточная влажность.
Сырьё для производства цемента, из чего он делается, технология изготовления
Сегодня процесс изготовления цемента изменился. Изготовляют его несколькими способами, да и компоненты, входящие в его состав, тоже отличаются от использовавшихся две сотни лет назад.
Чтобы было понятно, из чего делают цемент и как происходит его производство, необходимо знать, какие виды сырья используют сегодня производители этого важного строительного материала.
Так как сырьём для производства цемента гост31108 2003, гост 30515 2013 служат естественные породы, то и предприятия, занимающиеся его изготовления, чаще всего размещают поблизости от мест добычи этих пород.
Все ископаемые, из которых делается цемент, делятся на два вида:
- Карбонатные ископаемые, отличающиеся характеристиками и особенностью структуры. Именно структура породы обеспечивает эффективное её взаимодействие с остальными ингредиентами состава продукта.
- Глинистые и горные породы, имеющие осадочное происхождение. Имея минеральную основу, при увлажнении они приобретают пластичность и увеличиваются в объёме. Так как для данного вида сырья характерна вязкость, то их можно использовать, производя цемент сухим способом.
Теперь следует назвать конкретно, какие ископаемые относятся к каждому из видов сырья, используемых при производстве цемента.
К карбонатным породам относят следующие виды природного сырья:
- мел, представляющий разновидность известняка. Обладает способностью легко измельчаться;


Мел
- мергелистый известняк, в природе встречается как в рыхлом, так и в твёрдом состоянии. В породе могут содержаться примеси глины, поэтому данный вид известняка считается сырьём переходным, обладающим свойствами, характерными и для известняков, и для глины;
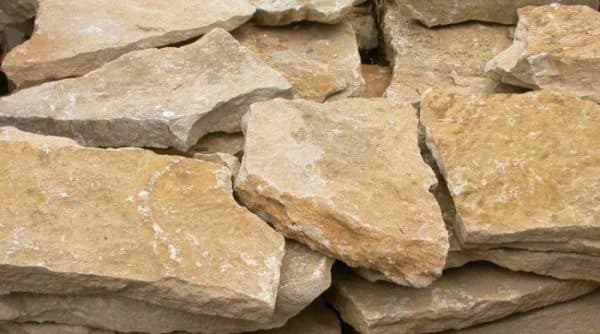
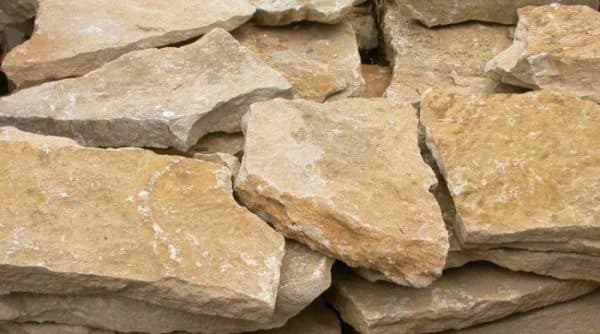
Мергелистый известняк
- известняки – ракушечники, не имеющие включений кремния. Порода имеет пористую, легко разрушающуюся при сжатии структуру;
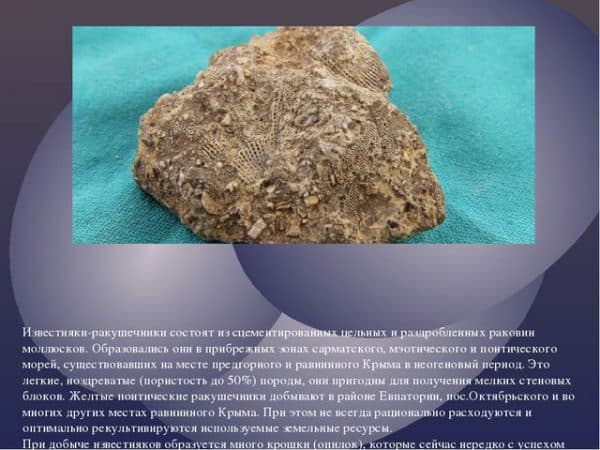
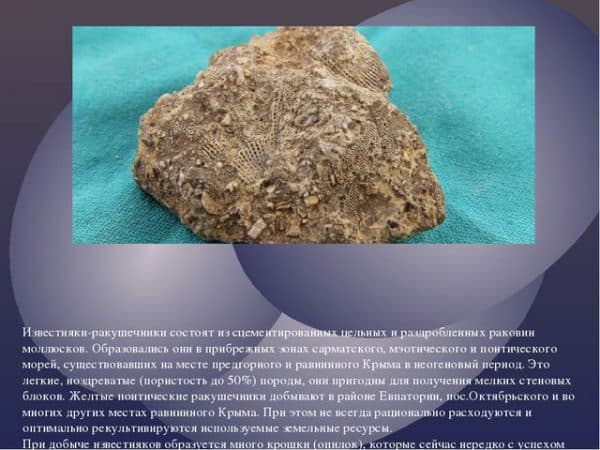
Известняки – ракушечники
- доломитовые породы и другие ископаемые осадочного происхождения. Они содержат карбонаты, придающие породе ценные свойства.
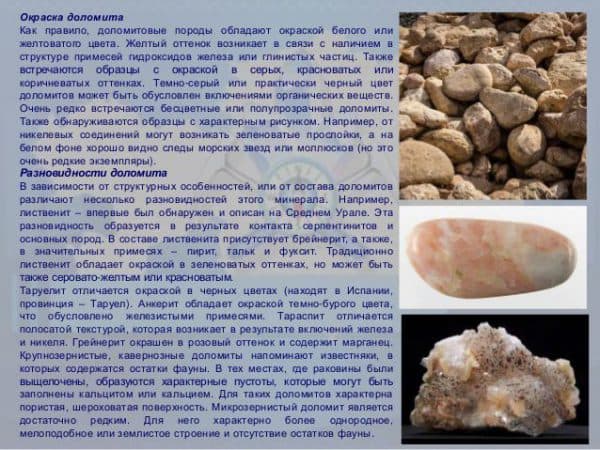
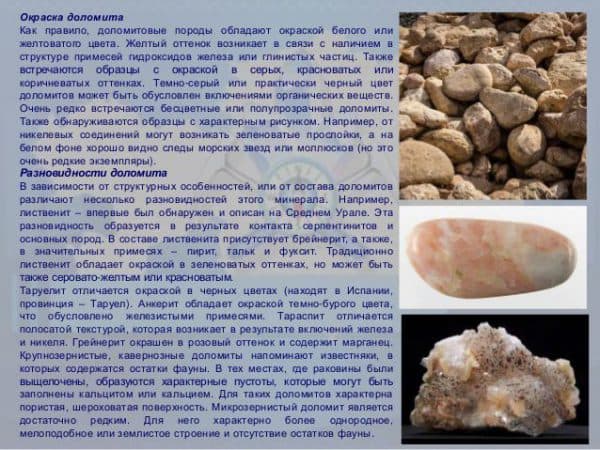
Доломит
Глинистые породы включают следующие виды ископаемых:
- глина с минеральными включениями, набухающими при контакте с водой;
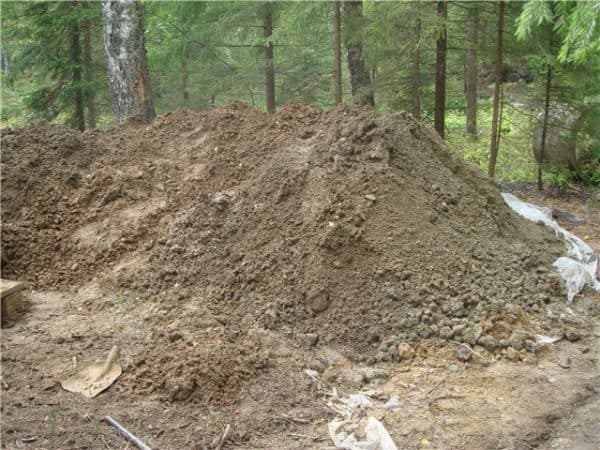
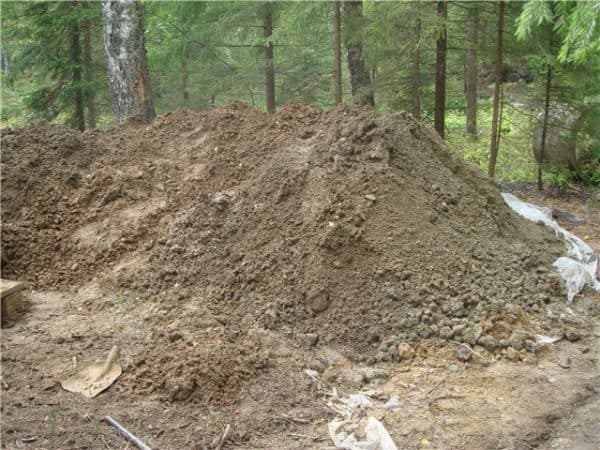
Глина
- суглинки, содержащие повышенную концентрацию частиц песка;
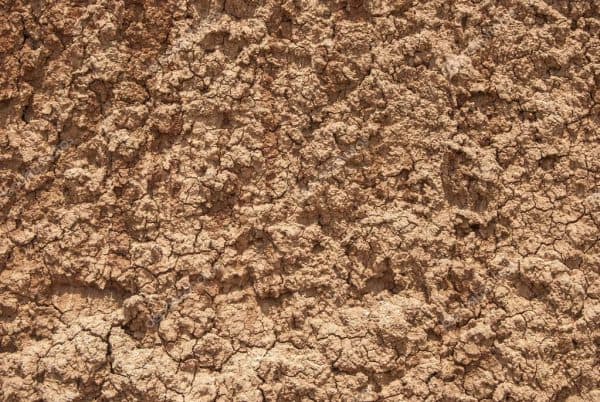
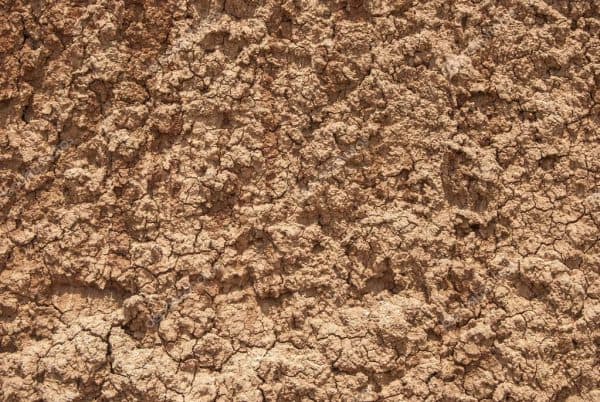
Суглинки
- сланцы, имеющие глинистую основу. Данное сырьё относят к горным породам, повышенной прочности. При механическом воздействии разделяется на пластинчатые пластины. Характеризуется стабильным составом и низким содержанием влаги;
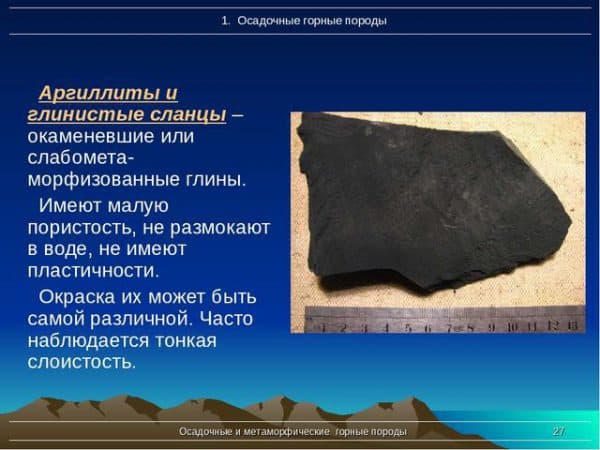
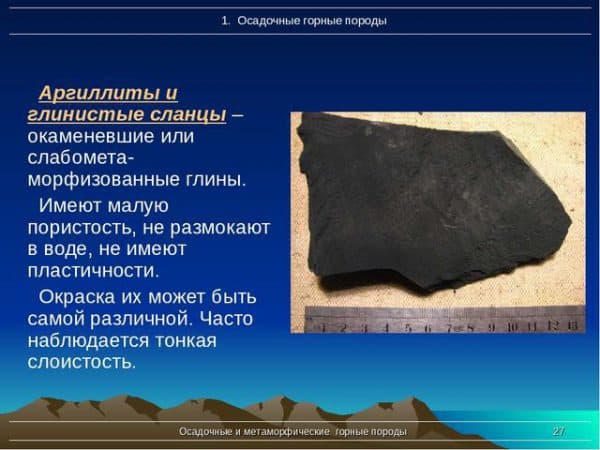
Сланцы
- лесс, пористая порода, с включениями частиц кварца и силиката.
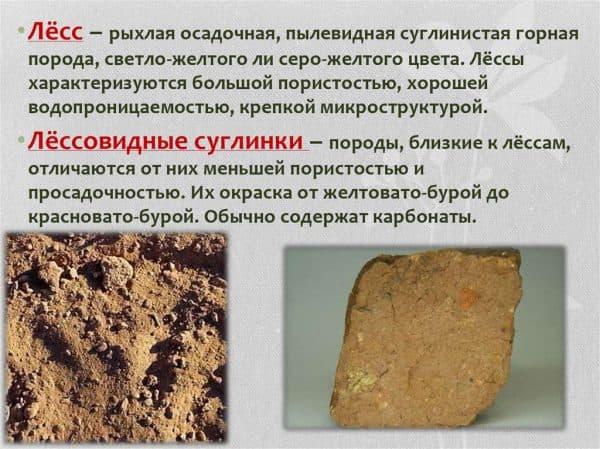
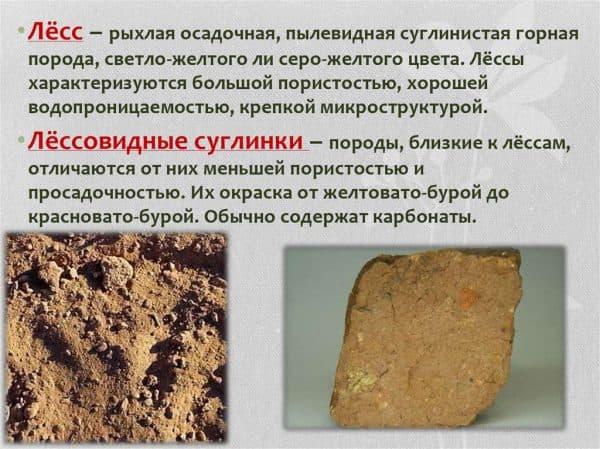
Лесс
Кроме данных видов сырья, что изготавливать цементную смесь на заводе используют некоторые виды производственных отходов. Для улучшения качества в его состав добавляют добавки, предусмотренные технологическим процессом: глинозём и кремнезём, плавиковый шпат и апатиты.
Применение песка просто необходимо при проведении самых разных ремонтных и строительных работ. Тут все о применении карьерного песка.
При проведении отделочных работ на кухне, в ванной или в любом другом помещении необходимо знать время высыхания плиточного клея. Здесь можно узнать, сколько сохнет плиточный клей.
В настоящее время декоративная штукатурка по праву является самым популярным и прогрессивным методом отделки. Перейдя по ссылке ознакомитесь с самостоятельным ее приготовлением.
Все добавки, называемые пластификаторами, также природного происхождения. Они влияют в лучшую сторону на следующие качества цемента:
- увеличивают стойкость к изменениям температуры;
- усиливают прочность;
- подвижность и эластичность продукта;
- уменьшает проникновение воды в готовое изделие.
В зависимости от свойств, добавленных в состав цемента пластификаторов, его раствор будет застывать быстрее, или же медленнее.
Состав, из которого производят цемент
Часть людей работающих в сфере строительства не знают, из чего делается цемент.
Состав цемента может быть различным в зависимости от марки и предназначения.
Однако вне зависимости от вида цемента, то есть рецепта, использованного при его производстве, основой для него служат два компонента – известняк с добавлением глины.
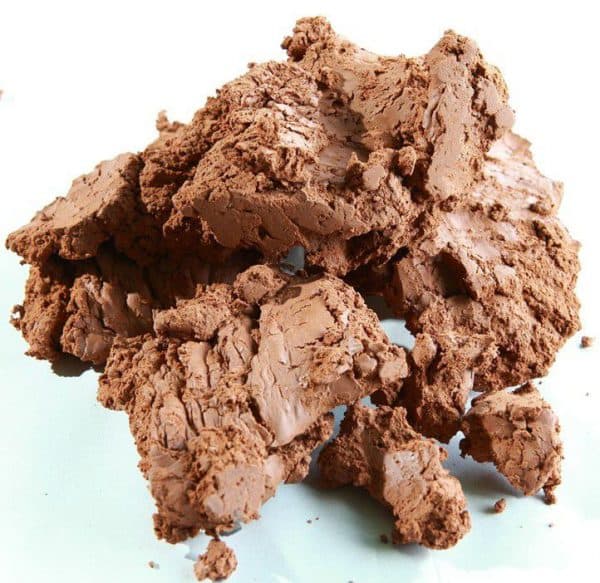
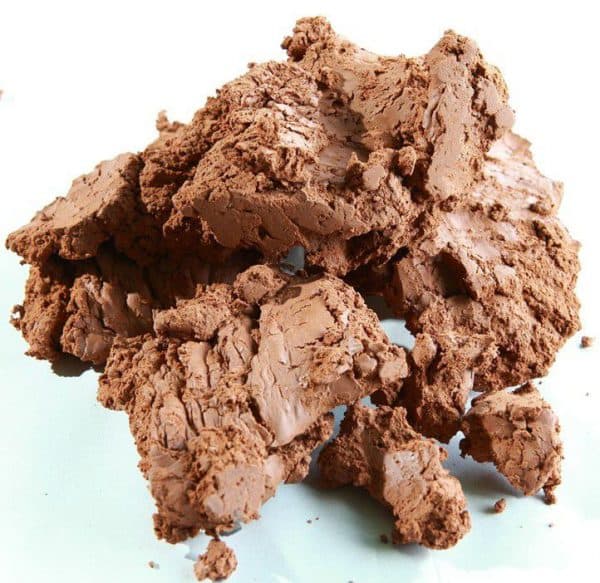
Глина
Количество известняка в три раза превышает количество глины. Такие пропорции необходимы для получения качественного клинкера, являющегося полуфабрикатом для производства цемента.
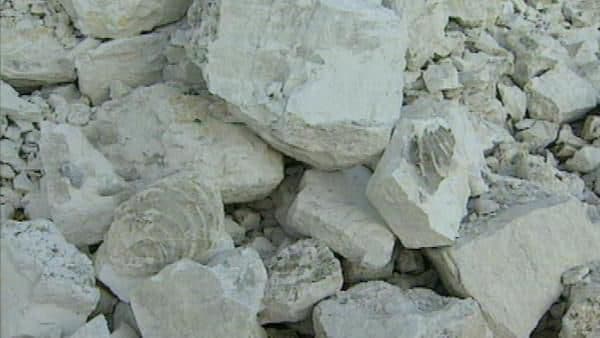
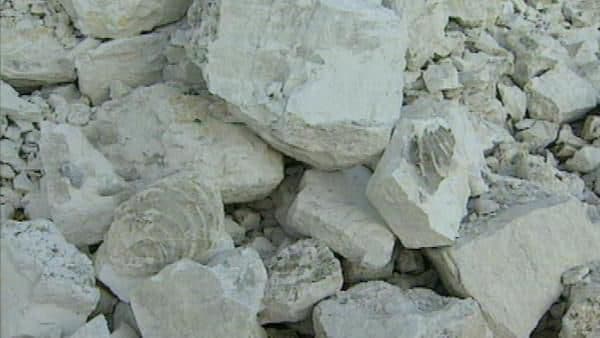
Известняк
Теперь можно назвать основные компоненты состава, чтобы каждому было ясно, из чего делают цемент:
- клинкер, основа конечной продукции, определяющая её характеристики прочности. Используется в виде гранул диаметром до 60 мм. Его термообработка выполняется при температуре, доходящей до 1500°. При плавлении клинкера образуется масса, для которой характерно высокое содержание кремнезёма и кальциевого диоксида;
- данные компоненты влияют на эксплуатационные характеристики конечного продукта. Перед обжигом гранулы клинкера измельчаются до пылеобразного состояния;
- гипс, определяющий скорость затвердевания цемента. В базовых рецептах предусмотрено добавление в состав чистого гипса до 6 % от общего количества компонентов;
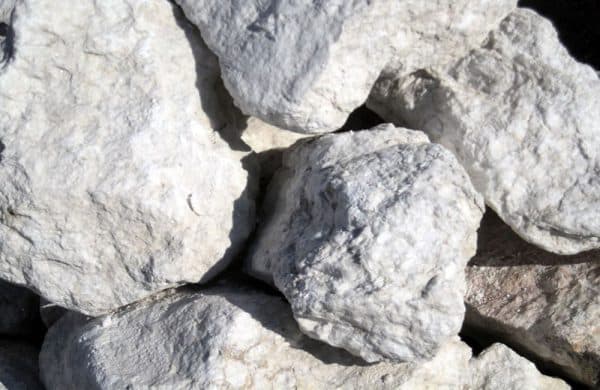
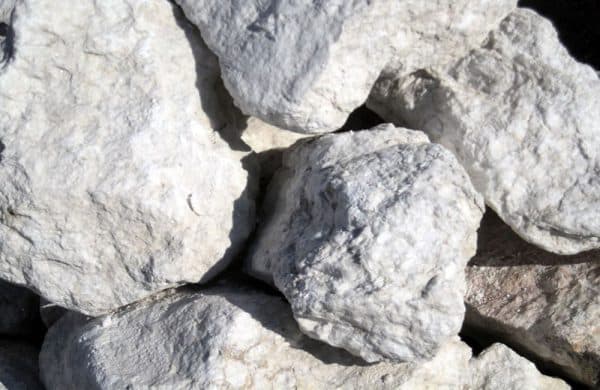
Гипс
- специальные добавки (пластификаторы, морозостойкие присадки, жидкое мыло и т.д.), усиливающие свойства, уже имеющиеся у продукции, или же придающие ей специальные характеристики, способные расширить область применения цемента.
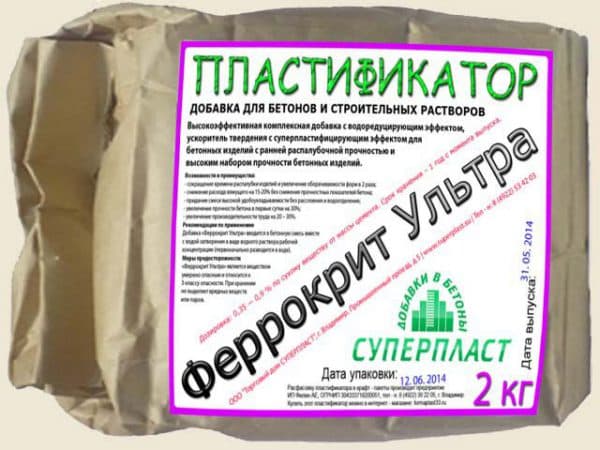
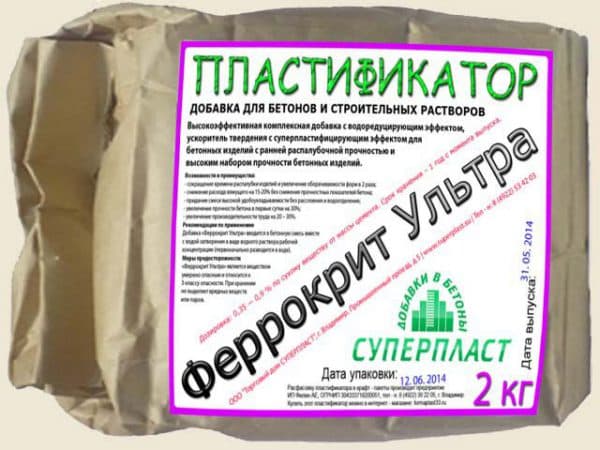
Пластификатор
Производство – как изготавливают цемент, процесс получения на заводе
Изготовление материала выполняется в определённом порядке, поэтапно. В технологии его производства предусмотрены следующие операции:
- Ингредиенты, предназначенные для изготовления клинкера, предварительно смешиваются. Обязательно необходимо точное соблюдение пропорций состава – 25 % глины и 75% известняка.
- Полученный состав обжигается при высокой температуре. При высокотемпературном обжиге глина и известь соединяются, образуя клинкер.
- Готовый продукт измельчается шаровыми мельницами, состоящими из барабанов, расположенных в горизонтальном положении, внутри которых размещены стальные шары. Помещённый в них клинкер размельчается до состояния порошка.
- Чем мельче полученные фракции цемента, тем лучшие эксплуатационные характеристики он будет иметь.
Существует несколько методов изготовления данного строительного материала. Их выбор обусловлен многими факторами, основными из которых является специфика имеющегося на предприятии оборудования и спрос на определённые марки цемента.
Разработанные технологии имеют отличие в способах подготовки сырья, используемого при производстве состава. Порядок его изготовления остаётся прежним.
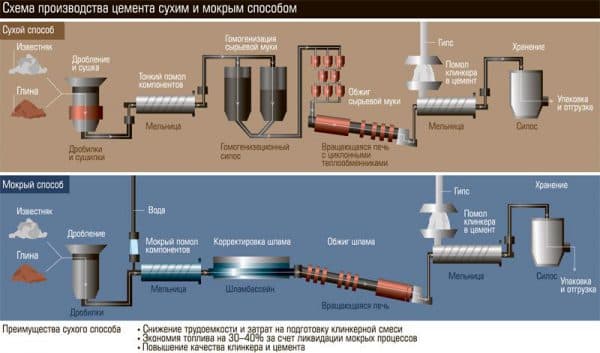
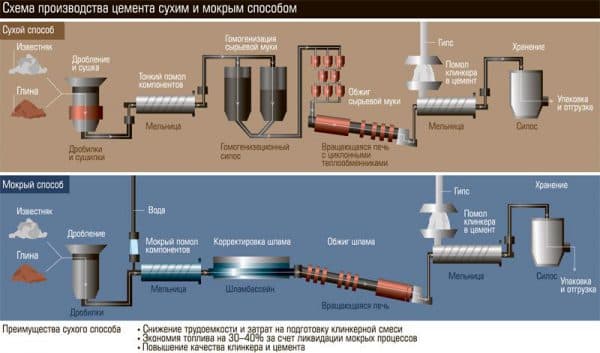
Производство
Разработаны следующие методы:
- Мокрая технология, предусматривающая замену извести мелом. В процессе смешивания компонентов состава происходит измельчение их в шаровой мельнице. Это процесс выполняется с добавлением воды. В результате образуется шихта, имеющая концентрацию влаги до 50%.
- Полученный материал затем обжигается в печи. После обжига он уже становится клинкером. Затем его измельчают.
- Сухая технология значительно уменьшает себестоимость производства, так как она объединяет несколько технологических операций в единый процесс. При использовании данной технологии компоненты, поступающие в шаровую мельницу, одновременно размалываются и сушатся.
- Для сушки используется воздействие горячих газов. Готовая шихтная масса имеет консистенцию порошка.
- Комбинированная технология объединяет особенности вышеописанных способов производства. В зависимости от оборудования, используемого на предприятии, может быть получен полусухой состав, имеющий влажность до 18%.
- Во втором варианте первоначально подготавливается сухая смесь, затем увлажнённая до 14 %. В обоих вариантах подготовленный состав затем отжигается и перемалывается.
Подробнее о производстве цемента смотрите на видео:
Классификация цементных смесей
Существует много разновидностей и различных марок данного строительного материала. Различают их по основному составу и добавкам, придающим каждому виду особые свойства.
Среди основных типов выделяют:
- портландцемент, с которого начиналось производство популярного в строительстве продукта. Для изготовления связующих растворов его не используют. Он применяется для создания бетонных изделий высокой прочности, штукатурке и отделочных работах;
- часто используют при возведении фундаментов. Для этого необходимо знать, как разводить цемент с песком;
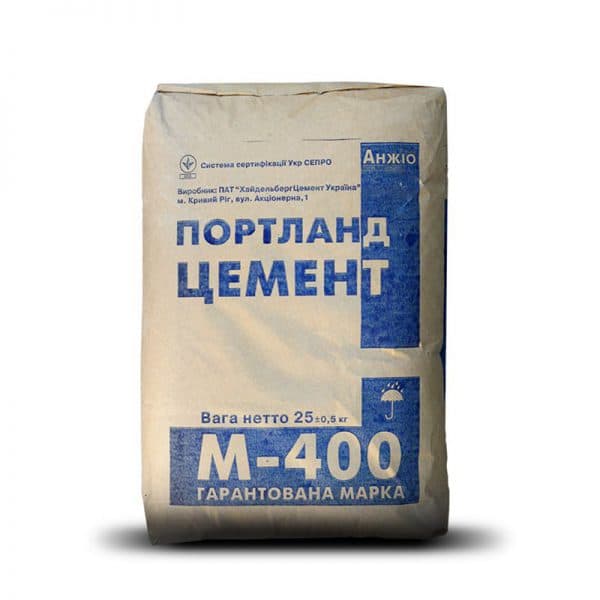
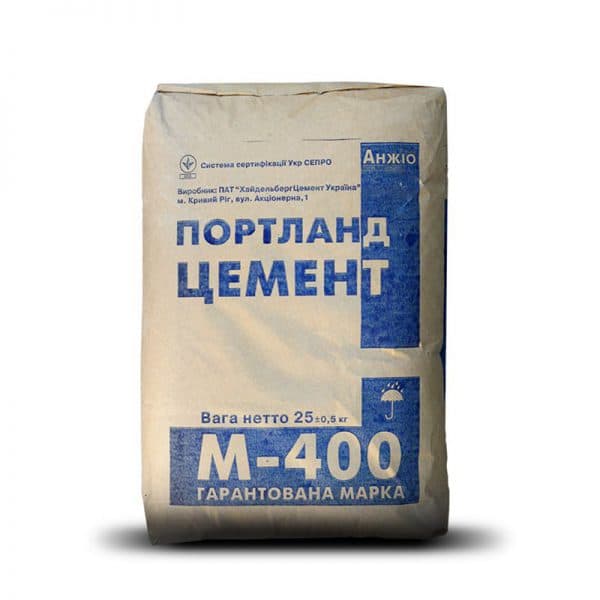
Портландцемент
- шлаковый цемент, при изготовлении которого используется доменный шлак и активные присадки. Используется для изготовления бетона и строительных растворов;
- глинозёмистый цемент, отличается устойчивостью к воздействию влаги, быстрым затвердеванием;
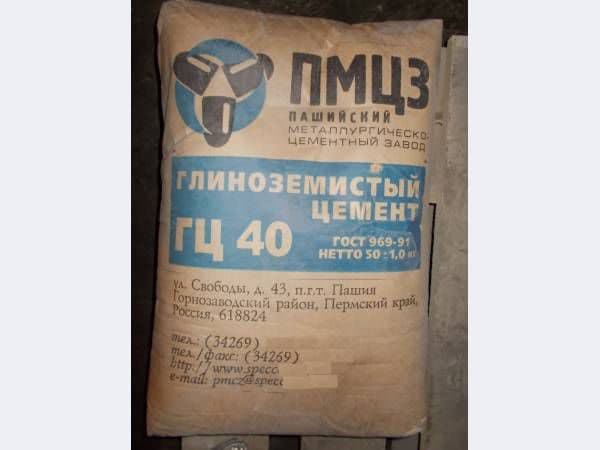
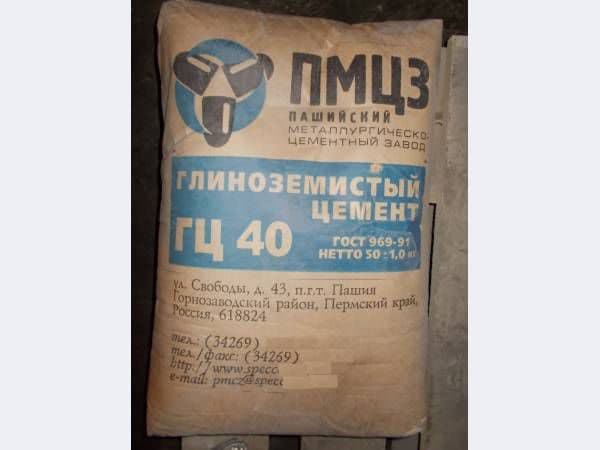
Глиноземистый
- кислотоупорный цемент, в котором используется кварцевый песок и кремнефтористый натрий. Материал устойчив к воздействию кислот, но недолговечен.
Приобретая любой из видов цемента, следует знать, что его состав активно взаимодействует с окружающей средой, при долгом хранении теряя свою прочность.
Даже если он хранится в сухом помещении, то спустя несколько месяцев его марка изменится в меньшую сторону. Поэтому, при его приобретении, следует обращать внимание на дату изготовления. Так же можете ознакомиться с нашей статьёй о технических характеристиках цемента м400.
Технология производства цемента: сырье, способы, оборудование
Для проведения строительных или ремонтных работ используют различные материалы, в том числе цемент разных видов и марок. Его используют для подготовки бетонных, кладочных, штукатурных растворов, для производства железобетонных изделий. Но при этом редко кто знаком с технологией производства цемента.

Состав цемента
Цементная смесь получается в результате смешивания ряда компонентов:- Клинкера. Вещество основано на глине и известняке, используется для определения прочности материала. Производится путем обжига глины и известняка. Под воздействием высоких температур плавится, преображаясь в гранулированную фракцию с высоким содержанием кремнезема. Затем обжигается повторно.
- Гипса. Используется для регулирования процесса твердения цемента. Вводится в состав в количестве не более 5%.
- Активных минеральных добавок. Они способствуют улучшению свойств цементного состава и расширению области его использования.
При изготовлении продукции могут быть использованы другие добавки, например, окислы кальция, магния, фосфора, соли. Но они используются в небольших количествах. Их вносят для того, чтобы получить установленные характеристики — жаропрочность, кислотоустойчивость и пр.

Если технологический процесс позволяет, то в состав могут быть введены пластификаторы.
Их использование помогает получить следующие эксплуатационные характеристики:- Препятствовать проникновению влаги в конструкцию.
- Уменьшение времени затвердевания.
- Увеличение прочности.
- Стойкость к колебаниям температур, влиянию агрессивных сред.

- Портландцемент. Самая распространенная модификация, в составе которой около 80% силиката кальция. Используется при различных строительных работах. Добавление красящих веществ улучшает декоративные свойства цемента, позволяя использовать его для отделочных работ.
- Глиноземистый. Отличается ускоренным твердением. Благодаря этому свойству его используют на объектах, которым необходима срочная реставрация, например, устранение разрушений после аварий, пожаров.
- Магнезиальный. Основной компонент — оксид магния, добавляет составу прочности, повышает адгезию к древесине. Однако из-за повышенной склонности к коррозии используется редко.
- Кислотоупорный. В процессе изготовления в состав вносится наполнитель — гидроксиликат натрия, затворяющийся жидким стеклом. Используется в кислотостойких бетонах и растворах.
Производство цемента на заводах
Выпуском цементной смеси занимаются специализированные предприятия. Чтобы получить качественный продукт требуется специальное оборудование и знание технологии. От мощности предприятия и качества сырья зависит выбор способа производства цемента.
Технологический процесс предполагает выполнение ряда производственных этапов:- Добыча сырья, в состав которого входит гипс, глина, известняк.
- Дробление известняка с приданием полученному продукту необходимой влажности.
- Измельчение известняка. Смешивание его с глиной. Концентрация компонентов может меняться. Все зависит от характеристик используемого сырья. В основном соотношение составляет 3:1. В результате получается комбинированный, сухой или мокрый шлам.
- Обжиг. Сырьевая масса отправляется в печь, разогретую до 1500 градусов, где спекается и превращается в гранулированную фракцию — клинкер.
- Измельчение. Клинкер в специальных мельницах измельчается до порошкообразного состояния.
- Подготовленные ингредиенты смешиваются в соответствии с рецептурой марки будущего цемента. В процессе смешивания добавляется гипс и специальные минеральные добавки.
Цементные составы изготавливаются по проверенным технологиям. В зависимости от состава и качества используемого сырья применяются разные методы подготовки исходных материалов.

Сухой способ
При производстве не используется вода. Основные материалы — глина и известняк, дробятся на специальном оборудовании. Сушатся, перемалываются в муку. Смешиваются при помощи пневматического инструмента и подаются на обжиг.
Клинкер, что образовался после обжига, измельчается до установленной фракции, фасуется в подготовленную тару и перевозится на склад. Производство цемента сухим способом позволяет снижать производственные затраты. Но требует повышенной однородности основных материалов. К тому же является опасным, с точки зрения экологии.
Мокрый способ
Преимуществом данного метода изготовления цемента является возможность точно подобрать необходимый состав шлама, несмотря на неоднородность исходного сырья. Шлам при таком способе приобретает жидкую консистенцию. В нем содержится около 40% жидкости.

Прежде чем сделать конечный продукт, шлам помещается в специальные технологические бассейны для корректировки состава. Затем отправляется во вращающиеся печи для обжига.
Температура обжига превышает 1000 градусов, поэтому изготовление цемента мокрым способом требует больших энергозатрат. Но дает возможность получать продукт высокого качества.
Комбинированные способы
Технология предполагает объединение сухого и мокрого способов производства цемента. Один из них может быть взят за основу, а второй — выступать в качестве дополнения. На разных предприятиях эти способы имеют различия. Все зависит от особенностей имеющегося оборудования для производства цемента, близости к месту добычи сырья, а также от потребностей на установленные марки продукта.

Если за основу взят мокрый метод, то сырье вначале смешивается, а затем обезвоживается в специальных сушилках с фильтрами почти до сухого состояния. Только после этой процедуры отправляется в печь. Такая технология позволяет уменьшать теплозатраты, поскольку в процессе обжига почти нет испарений.
Когда в основе лежит сухой способ, в процессе гранулирования готовой смеси используется вода. В обоих случаях влажность клинкера, отправляющегося в печь, около 10-18%.
Как делают белый цемент
Белый цемент, производство которого несколько отличается от технологии выпуска серого продукта, может выпускаться как мокрым, так и сухим способом. Отличается технология тем, что исходное сырье обжигается при высокой температуре и затем быстро охлаждается водой.
Клинкер этого вида продукции складывается из минеральных добавок, известняка, гипса, соли и других компонентов. Исходное сырье готовится из карбонатной и глинистой породы: известняка, каолиновой глины, отходов обогащения, кварцевого песка.
Основным достоинством и отличительной чертой белого цемента является его белоснежность. Но его производство обходится намного дороже по сравнению с серым продуктом.
состав, технология и этапы изготовления
Дата: 10 января 2019
Просмотров: 41407
Коментариев: 3
Цемент – широко распространенный материал, который применяют при любых видах работ, связанных с ремонтом, реставрацией, строительством. Цементная основа – вяжущие компоненты неорганического происхождения. Из цемента производятся бетонные, кладочные, штукатурные растворы, железобетонные изделия, используемые при строительстве промышленных объектов и частных построек.
Особенностью порошкообразной цементной массы, смешанной с водой, является способность постепенно твердеть, превращаясь в каменный массив. Процесс приобретения эксплуатационной прочности происходит как в воздушной среде, так и в воде. Главное условие твердения – избыточная влажность.
Все сталкивались с цементом, однако мало кто знает, из чего делают этот универсальный строительный материал, как его производят. Его основа – клинкер, специальные минеральные добавки и гипс. Рассмотрим подробно, как делают цемент, какое сырье для этого используется.
По-прежнему клинкер – это основной компонент, входящий в состав цемента
Сырьевые материалы
Производство цемента осуществляется на специальных заводах, расположенных близко к местам добычи исходного сырья для его изготовления. Главным исходным сырьем для цементного производства являются следующие естественные породы:
- ископаемые карбонатного типа. Это ценное природное сырье, отличающееся особенностями кристаллической структуры, физическими характеристиками. Материал может иметь кристаллическую или аморфную структуру, определяющую эффективность его взаимодействия при обжиге с другими компонентами;
- глинистые материалы, горные породы осадочного характера. Они имеют минеральную основу, становятся пластичными, объемно увеличиваются при избыточном увлажнении. Сырье характеризуется вязкостью, применяется при сухом методе производства.
[testimonial_view id=”3″]
Карбонатные породы
Остановимся на карбонатных породах, характерными представителями которых являются:
- Мел, являющийся горной породой осадочного характера, которая легко перетирается, относится к разновидностям мажущего известняка. Он популярен при изготовлении цемента.
- Мергель или мергелистый известняк – ископаемые осадочного типа, которые добываются в рыхлом или твердом состоянии, отличаются удельным весом, концентрацией влаги. Содержат примеси глины, что позволяет относить их к переходному сырью, имеющему много общего с известняковыми породами и ископаемыми на основе глины.
В состав входят активные минеральные добавки (15%) в соответствии со стандартами производства
- Известняковое сырье, ракушечники, отличающиеся отсутствием включений кремния. Порода обладает пористой структурой, легко разрушается под воздействием сжимающих усилий.
- Породы доломитового типа, а также горные ископаемые осадочного происхождения, содержащие карбонаты. Они характеризуются ценными физическими свойствами.
Глинистое сырье
К глинистым породам относятся:
- глина, содержащая минеральные включения, разбухающие при добавлении воды;
- суглинки, являющиеся разновидностью глины, с повышенной концентрацией песчаной фракции и пылеобразных частиц;
- сланцы на глинистой основе, относящиеся к горным породам с повышенной прочностью, которые при измельчении расслаиваются на пластинчатые частицы. Сырье характеризуется стабильным гранулометрическим составом, низкой концентрацией влаги.
- лесс, представляющий рыхлую горную, непластичную породу, отличающуюся пористостью, мелкозернистостью. Содержит включения силиката, кварца.
Возможно применение отходов промышленного производства, других видов природных материалов и шлаков.
Корректирующие добавки
Цементный состав делают из минерального сырья с применением специальных пластификаторов, добавляемых при производстве.
Если увеличить количество добавок до 20%, то свойства цемента будут несколько изменены
Технология предусматривает использование добавок на базе ископаемых, содержащих:
- Глинозем.
- Кремнезем.
- Глину.
- Плавиковый шпат.
- Апатиты.
Введение корректирующих добавок, с помощью которых делают цемент и улучшают его характеристики, предусмотрено технологией. Пластификаторы позволяют улучшить следующие свойства цементного состава:
- стойкость к воздействию коррозионных процессов;
- устойчивость к воздействию перепадов температуры, глубоким циклам замораживания;
- прочностные характеристики;
- продолжительность твердения;
- подвижность цементного раствора, его эластичность;
- степень проницаемости водой.
Состав
Задумывались ли вы, из чего сделан цемент? Его состав обусловлен особенностями сырья и конкретной маркой продукции. Так, пользующийся широкой популярностью портландцемент имеет следующий состав:
- Кремниевый диоксид (кремниевая кислота или кварц) – 25 %.
- Известь – 60 %.
- Алюминий (глинозем) – 5 %.
- Оксиды железа и гипс – 10 %.
Сегодня производится множество видов цемента
Процентное соотношение ингредиентов может изменяться, согласно особенностям технологии и марки цементной продукции. Отдельные виды цементов, в частности шлакопортландцемент, включают в свой состав шлак, представляющий уголь, полученный в результате обжига клинкера.
Независимо от рецептуры, основные ингредиенты при изготовлении цементного состава – глина и известняк. Концентрация известняка трехкратно превышает содержание глины, что обеспечивает необходимое качество клинкера для производства цементной продукции.
Основными компонентами, из которых производят цемент, являются:
- клинкер, определяющий прочностные характеристики, получаемый при обжиге исходного сырья (известняка, глины). Клинкер является основой конечной продукции, используется в гранулированном виде диаметром 10-60 мм. Клинкер термообрабатывается при температуре порядка полторы тысячи градусов Цельсия. Он плавится с образованием массы с высоким содержанием кальциевого диоксида и кремнезема, которые определяют эксплуатационные характеристики цементных составов. Гранулы дробятся до пылеобразного состояния с последующим обжигом;
- гипс, процентное содержание которого определяет период твердения. Базовая рецептура предусматривает использование до 6% чистого порошкообразного гипса или гипсового камня, содержащего примеси;
- специальные добавки, вводимые для усиления имеющихся свойств или придания составу специальных характеристик, расширяющих сферу применения.
Очень часто цемент применяют в строительстве для создания бетона и армированных конструкций
Процесс изготовления
Производство цемента осуществляется поэтапно, предусматривает следующее технологические операции:
- Предварительное смешивание ингредиентов для изготовления клинкера, который делают из известняка, вводимого в количестве 75%, и из глины, доля которой составляет 25%.
- Высокотемпературный обжиг, после которого образуется клинкер. Он – результат процесса соединения глины и извести под воздействием повышенной до 1450 градусов Цельсия температуры.
- Измельчение, осуществляемое с помощью шаровых мельниц. Они представляют горизонтально расположенные барабаны с находящимися внутри стальными шарами, обеспечивающими измельчение клинкера до порошкообразного состояния. С уменьшением фракции помола возрастают эксплуатационные характеристики и марка цементного состава.
Этапы производства
Особенности производства предусматривают изготовление цемента различными методами, что сказывается на особенностях применяемого сырья. Это обусловлено расположением цементного производства, спецификой применяемого оборудования, спросом на определённые марки продукции.
Все варианты технологий отличаются только особенностями подготовки исходного сырья, которые осуществляются:
- мокрым путем. Мокрая технология предусматривает использование вместо извести мела, смешивание которого с необходимыми ингредиентами происходит одновременно с измельчением в горизонтальном барабане с обязательным добавлением воды. При этом образуется шихта с концентрацией влаги 30-50%. Шихтовый материал обжигается в печи, превращаясь в шарообразный клинкер, который затем измельчается;
- сухим методом. Сухая технология характеризуется уменьшенной себестоимостью производства цемента, сокращением технологического цикла. Это связано с объединением технологических операций, позволяющих одновременно осуществлять помол и сушку компонентов в шаровой мельнице под воздействием поступающих горячих газов. Полученная шихта имеет порошкообразную консистенцию;
- комбинированным способом. Комбинированный вариант объединяет особенности мокрого и сухого способа производства, но на разных предприятиях имеет определенные отличия. Один из вариантов обеспечивает возможность получение полусухого состава с влажностью до 18%, произведенного путем высушивания шихты, полученной по мокрой технологии. Второй метод предусматривает подготовку сухой смеси с последующим ею увлажнением до 14%, гранулированием, заключительным отжигом.
Заключение
Материал статьи предоставляет информацию о том, как делают цемент, какое сырье применяют, какие технологические особенности используют в процессе производства. Имеется множество технологических нюансов, которыми в совершенстве владеют специалисты, занимающиеся изготовление цемента.
На сайте: Автор и редактор статей на сайте pobetony.ru
Образование и опыт работы: Высшее техническое образование. Опыт работы на различных производствах и стройках – 12 лет, из них 8 лет – за рубежом.
Другие умения и навыки: Имеет 4-ю группу допуска по электробезопасности. Выполнение расчетов с использованием больших массивов данных.
Текущая занятость: Последние 4 года выступает в роли независимого консультанта в ряде строительных компаний.
Сырье для производства цемента, из чего делают цемент
Сырьевыми материалами в производстве цемента служат в основном глинистые и карбонатные породы, а также иное природное сырье и некоторые типы промышленных отходов, шлаков и т.п.
Карбонатные породы — это известняк, известняк-ракушечник, мел, мергелистый известняк, мергель, метаморфические либо осадочные горные породы доломитового, карбонатно-глинистого и известнякового состава. Качество и ценность таких пород в качестве сырья для создания цемента определяется их структурой и физическими свойствами. Породы с кристаллической структурой хуже, по сравнению с породами аморфной структуры, взаимодействуют с другими элементами смеси при обжиге.
- Мел – легко растирающаяся мягкая осадочная горная порода, вид мажущего известняка. Он легко измельчается и является популярным сырьем для создания цемента.
- Мергель — осадочная порода, переходная от известняковых к глинистым. Может иметь твердую или рыхлую структуру, различную плотность и влажность в зависимости от процентной доли глинистых примесей. Строительные растворы на основе мергеля активно применяются при устройстве печей, каминов и т.п.
- Из известняков для производства цемента предпочтительны пористые и мергелистые виды с небольшим порогом прочности на сжатие и без содержания кремниевых включений.
- Из глинистых пород в производстве цемента применяют: суглинок, глину, лесс, глинистый сланец, а также лессовидные суглинки.
Глины, горные осадочные породы, состоят из разного рода минералов, при увлажнении приобретают пластичность и разбухают. В сухом способе производства цемента связующая способность и пластичность глины дает возможность гранулирования муки и брикетирования. Суглинком называется глина, в которой содержится высокое количество пылеватых и песчаных частиц.
Глинистые сланцы представляют собой плотные и твердые горные породы, способные легко расслаиваться на пластинки небольшой толщины. Относительно глины глинистые сланцы имеют более постоянный состав и меньшую влажность.
Лессом называется тонкозернистая горная порода, рыхлая и пористая, состоящая из тончайших частиц глинистых материалов, полевого шпата, кварца и иных силикатов. Лесс не отличается высокой пластичностью. Лессовидный суглинок – материал, по своим свойствам являющийся переходным между суглинком и лессом.
Кроме основного сырья в процессе производства активно используются различные виды корректирующих добавок в цемент, позволяющих изменить некоторые свойства конечного продукта. Это могут быть глиноземистые, кремнеземистые, глиносодержащие добавки, а также плавиковый шпат в качестве минерализаторов (кремнефтористый натрий, гипс, апатит, фосфогипс, флюорит)
Хотелось бы отметить, что сырьевой состав, как при сухом, так и при мокром способе производства цемента, может меняться в зависимости от местоположения цементного завода, от доступности того или иного вида сырья, от возможностей оборудования, спроса на те или иные виды продукции в этом регионе и многого-многого другого
Состав цемента: характеристики и свойства цемента
Цемент – распространенный строительный материал, используемый чаще всего в качестве вяжущего в строительных смесях и растворах. Представляет собой мелкодисперсный порошок серого цвета с зеленоватым или другим оттенком. После взаимодействия с водой цемент и продукты на его основе образуют пластичную массу, которая при твердении трансформируется в искусственный камень.
Сырье для изготовления цемента
Сырьем для производства цемента являются горные породы, добываемые открытым способом:
- Карбонатные – мел, известняки, известняки-ракушечники, доломит, мергель, туф. В промышленном производстве используются в основном известняки. Точное количество компонента зависит от его свойств и минерального состава. Чем больше в составе породы веществ с кристаллической структурой, тем выше температура плавления.
- Глинистые – глина, глинистые сланцы, лесс, суглинки, монтмориллонит. Этот компонент осадочного происхождения разбухает при контакте с водой. Цель применения глинистых веществ – повышение пластичности смесей и растворов на базе цементного вяжущего.
- Добавки. Их перечень определяется в зависимости от свойств, которые необходимо получить. Обычно добавки содержать глинозем, железо, кремний. Для их изготовления используют различные производственные отходы – доменную пыль и другие.
Единой формулы химического состава цемента не существует, так как производители предлагают большое количество разновидностей этого строительного материала с различными эксплуатационными характеристиками.
Наиболее распространен в строительстве портландцемент – без минеральных добавок и с минеральными добавками.
Существуют определенные ограничения по минимально допустимым ических соединений, из которых состоит портландцемент:
- CaO – 62%;
- SiO2 – 20%;
- Al2O3– 4%;
- Fe2O3 – 2%;
- MgO – 1%.
Химические составы в процентах некоторых типов цементов
Химический состав, % | Характеристика | ||||
CaO | SiO2 | Al2O3 | Fe2O3 | Другие оксиды | |
Портландцемент | |||||
63…66 | 21…24 | 4…8 | 2…4 | 3…5 | Нормально твердеющий |
Глиноземистый цемент | |||||
35…43 | 5…10 | 39…47 | 2…15 | 1,5…2,5 | Быстро твердеющий |
Что такое цементный клинкер?
Основной компонент производства цемента – клинкер. Это промежуточный полуфабрикат, получаемый обжигом смеси известняка (мела, мергеля или других пород) в количестве 75% и 25% глины. Сырьевые компоненты плавятся с образованием гранул. Клинкер перемалывают и соединяют с молотыми добавками.
Весь процесс изготовления цементного вяжущего можно условно разделить на 3 этапа:
- изготовление клинкера обжигом – основной процесс, наиболее затратный и трудоемкий;
- помол клинкера до образования тонкодисперсного порошка;
- смешивание клинкерного порошка с порошкообразными добавками.
Изготовление клинкера делится на следующие этапы:
- доставка сырья для клинкера на цементный завод;
- измельчение сырьевых компонентов;
- смешивание компонентов в пропорциях, указанных в техдокументации, для последующего обжига.
Технологии производства цемента
Существует несколько технологий производства цемента.
Конкретный вид производства определяется тем, из чего делают цемент:
- Мокрый. Клинкер изготавливается из мела, глины и воды. К измельченным компонентам добавляют воду. Влажную смесь (шлам) отправляют на обжиг. Полученный после обжига продукт транспортируют в холодильник. После охлаждения его измельчают, смешивают с добавками для получения необходимых свойств вяжущего. Эта технология требует финансовых затрат, поэтому производители в основном применяют другие. Но при необходимости получения цемента с прекрасными эксплуатационными свойствами применяют именно этот способ, позволяющий тонко корректировать состав сырья. Корректировка состава осуществляется в специальных бассейнах при температуре 1000°C.
- Сухой. Все компоненты – известняк, глина, добавки дробятся в сухом виде. Готовые порошки смешиваются в закрытых боксах с помощью подачи воздуха. Эта методика часто используется производителями, благодаря простоте реализации и относительно невысоким затратам. При производстве нет водяных испарений. Такой способ требует небольших затрат энергоносителей. Он оптимален для однородных сырьевых компонентов.
- Комбинированный. Эта технология сочетает элементы сухого и мокрого способов. Одна из этих технологий является основной, а вторая дополнительной. Если основной является мокрая методика, то сначала изготавливают сырьевой шлам, корректируют его состав, затем его обезвоживают и обжигают в печи, предназначенной для сухой технологии.
Цемент, независимо от того, из чего он состоит и каким способом приготовлен, складируется в специальных башнях – силосах, в которых, благодаря проветриванию, материал не слеживается, сохраняя рабочие характеристики.
К потребителю цемент поступает навалом или расфасованным в бумажные мешки.
Производство бесклинкерного цемента
Сырьем для бесклинкерного цемента являются доменный или гидравлические шлаки, активаторы и другие дополнительные компоненты. Смесь из подготовленных и взятых в нужных пропорциях компонентов, дробят и перемалывают до мелкодисперсного со стояния. Для бесклинкерного цемента характерны:
- устойчивость к различным воздействиям окружающей среды;
- экономичность производства, благодаря невысоким энергозатратам;
- утилизация отходов металлургических и других производств, что положительно влияет на состояние окружающей среды;
- различные цвета и свойства конечного продукта, которые можно получать без изменения основных этапов технологического процесса и привлечения дополнительного оборудования.
Основное оборудование для изготовления цемента
При производстве вяжущего используются следующие основные виды оборудования:
- техника для добычи сырья и его транспортировки к месту изготовления;
- линия дробления сырья;
- печи для высокотемпературной обработки;
- линия дробления полученного клинкера, дозирования и смешивания молотого клинкера с добавками;
- оборудование для фасовки готового продукта в бумажные мешки.
Типы цемента и сферы их использования
Выпускается множество разновидностей вяжущего с разными эксплуатационными и декоративными характеристиками. Основные виды:
- Портландцемент. Этот тонкодисперсный порошок серого цвета с зеленоватым оттенком является наиболее распространенным строительным материалом, широко используемым в индивидуальном, масштабном жилищном и промышленном строительстве. Отдельно не применяется. Выступает компонентом строительных смесей и растворов. В сочетании с песком и щебнем используется при производстве бетонных смесей. Из цемента и песка изготавливают сухие строительные смеси, поступающие в продажу фасованными в мешки, или пластичные цементно-песчаные растворы, доставляемые на строительную площадку в виде, готовом к применению. Пластифицирующие добавки регулируют время схватывания раствора и другие характеристики конечного продукта.
- Сульфатостойкий. Устойчив к химически активным средам. Применяется для бетонирования подземных и подводных конструкций.
- Глиноземный. В состав добавляют гипс и глиноземистый шлак, благодаря котором вяжущее быстро схватывается и приобретает марочную прочность. Глиноземный цемент используется при строительстве конструкций, работающих в условиях высокой влажности.
- Кислотоупорный. При его производстве используются кварцевый песок и кремнефтористый натрий. В качестве жидкости для затворения используется не вода, а жидкое стекло.
- Шлакопортландцемент. В состав этого вяжущего добавляют гранулы шлака (примерно 25%). Материал применяется в крупномасштабном строительстве.
Как делают цемент: технология производства цемента
Любое строительство или ремонтные работы невозможны без использования универсального строительного материала – цемента разных видов и марок. Мы настолько привыкли к этому продукту, что даже не задумываемся над проблемой, а как делают цемент. Можно ли его можно изготовить в домашних условиях и не переплачивать?
СодержаниеСвернуть
Сразу ответим на вопрос – можно ли сделать цемент своими руками? Имея необходимое оборудование и исходные материалы – получить цемент в домашних условиях можно. На данный момент времени в Российской Федерации большим спросом пользуются мини-заводы по производству цемента, мощностью порядка 120 000 тонн цемента в год. Производить же цемент для единичной стройки экономически невыгодно. Проще и дешевле купить этот необходимый строительный материал на заводе или в магазине.
Состав цемента
Цемент получается при длительном дроблении клинкера и гипса. Клинкер — продукт равномерного обжига до спекания однородной сырьевой смеси, состоящей из известняка и глины определённого состава, обеспечивающего преобладание силикатов кальция.
При измельчении клинкера вводят добавки: гипс СaSO4·2H2O для регулирования сроков схватывания, до 15 % активных минеральных добавок (пиритные огарки, колошниковую пыль, бокситы, пески) для улучшения некоторых свойств и снижения стоимости цемента.
Производство цемента на заводах
На данный момент времени производителями цемента используются три технологии производства связующего:
- Мокрый способ.
- Сухой способ.
- Комбинированный метод.
Стоит заметить что «сухую» технологию используют зарубежные производители цемента: Египет, Турция и Китай. «Мокрая» же технология традиционно используется отечественными цементными заводами.

Сухой способ
Здесь нет необходимости использовать воду. Исходный материал (глину и известняк) дробят на специальном оборудовании. Сушат и перемалывают в мелкодисперсную муку, смешивают пневматическим способом и подают на обжиг.
Образовавшийся в результате обжига цементный клинкер измельчается до соответствующей степени фракции, фасуется в упаковку и отправляется на склад готовой продукции. Данный способ позволяет снизить затраты на производство, однако отличается «капризностью» к однородности исходных материалов и является экологически опасным вариантом.
Мокрый способ
Неоспоримые достоинства данного метода заключается в возможности точного подбора состава исходного сырья при высокой неоднородности исходных компонентов: порода, вид породы и пр. Исходный материал (шлам) представляет собой жидкую субстанцию, содержащую до сорока процентов влаги.
Перед тем как сделать цемент, состав шлама корректируется в специальных технологических бассейнах. После выдержки сырья в бассейне, производится отжиг в специальных вращающихся печах и последующее измельчение.
Мокрый способ требует большего расхода тепловой энергии расходуемой на высушивание исходного сырья. Это существенно увеличивает себестоимость производства цемента, однако качество конечной продукции не страдает от возможной неоднородности клинкера, как при мокром варианте.
Комбинированные способы
Данная технология опирается на мокрый вид получения связующего. Промежуточную субстанцию обезвоживают по специальной технологии. Клинкер гранулируют с добавлением воды, после чего производят отжиг и последующее измельчение до той или иной марки цемента.
В числе достоинств комбинированного способа производства цемента: высокий выход «годного», возможность использования отходов металлургической промышленности.
Как делают белый цемент
Технология производства белого цемента незначительно отличается от технологии производства обычного «серого» материала. Как и обычный «серый» материал, белый цемент выпускают сухим и мокрым способом. Основное отличие технологии – обжиг исходного сырья при высокой температуре и резкое охлаждение в воде.
Клинкер белого цемента характеризуется как «маложелезистый» и содержит в своем составе: минеральные добавки, известняк, гипс, соли и другие компоненты. В качестве исходного сырья для клинкера используются карбонатная и глинистая порода (известняк, каолиновая глина, отходы обогащения, кварцевый песок).
В Российской Федерации белый цемент производится только на одном предприятии – ООО «Холсим (Рус) СМ» (до 2012 года ОАО «Щуровский цемент»). Большинство белого цемента поставляется на рынок России из-за рубежа следующими компаниями: «Холсим» (Словакия), «Cimsa иAdana» (Турция), «AalborgWhite»(Дания) и «AalborgWhite» (Египет).
Основное достоинство белого цемента его уникальная характеристика – белоснежность, а основной недостаток в разы большая стоимость по сравнению с обычным «серым» материалом.
Заключение
Теперь вы знаете, как делают цемент на заводе в общем случае. Информацию как правильно делать цемент во всех подробностях, цифрах, схемах, таблицах и других тонкостях смотрите в специальной литературе.
Моделирование и оптимизация процесса смешивания цементного сырья
В данной статье основное внимание уделяется моделированию и решению проблемы оптимизации соотношения ингредиентов в процессе смешивания цементного сырья. Общая нелинейная изменяющаяся во времени модель (G-NLTV) создана для процесса смешивания цементного сырья с учетом химического состава, колебаний потока сырья и различных ограничений ремесла и производства. Представлены различные целевые функции для получения оптимального соотношения ингредиентов при различных производственных требованиях.Задача оптимизации соотношения ингредиентов трансформируется в задачу оптимизации с одной или несколькими задачами с дискретным временем и нелинейными ограничениями. Представлена структура метода внутренних точек сетки для решения задачи оптимизации скользящих нелинейных ограничений. На основе платформы MATLAB-GUI разработано соответствующее программное обеспечение для определения соотношения ингредиентов для получения оптимального соотношения ингредиентов. Наконец, представлены несколько численных примеров для изучения и решения задач оптимизации соотношения ингредиентов.
1. Введение
Цемент — широко используемый строительный материал в мире. Производство цемента будет проходить через несколько процедур, включая процесс смешивания и обжига сырья, процесс измельчения цементного клинкера и процесс упаковки. Цементное сырье и цементный клинкер в основном содержат четыре оксида: оксид кальция или известь (CaO), кремнезем (SiO 2 ), оксид алюминия (Al 2 O 3 ) и оксид железа (Fe 2 O 3). ). Качество цементного клинкера оценивается по указанным выше четырем оксидам.Следовательно, соотношение ингредиентов цементного сырья существенно повлияет на качество и свойства цементного клинкера. Оптимальное соотношение ингредиентов улучшит и стабилизирует качество цемента и ремесло производства. Поэтому цементное сырье следует разумно перемешивать. Следовательно, получение оптимального соотношения ингредиентов является серьезной проблемой.
Во многих публикациях изучаются различные цементные процессы в производстве цемента. В [4], при различных коэффициентах заполнения шарового заряда, размерах шаров и времени пребывания, шаровая мельница непрерывного действия изучается для оптимизации процесса измельчения цементного сырья.В [5] представлена система адаптивного управления процессом смешивания сырья, а также обсуждается соответствующая оптимальная структура управления. В [6, 7] представлены стратегии управления процессом смешивания цементного сырья методами наименьших квадратов, методами нейронной сети и методами адаптивного нейронно-нечеткого вывода. В [8–10] обсуждались проблемы идентификации модели и усовершенствованного управления с учетом возмущения изменений химического состава, а для расчета оптимального соотношения подачи сырья используется контроллер с прогнозированием модели.В [11] предложен изменяющийся во времени фильтр Калмана для рекурсивной оценки оксидного состава цементного сырья с помощью рентгеновского анализа. В [12] предлагается нечеткий контроллер T-S для улучшения характеристик в реальном времени в процессе смешивания. В [13] питатель, шаровая мельница и бункер гомогенизации рассматриваются как единая система, входные и выходные данные используются для анализа процесса смешивания. В [1, 14, 15] нечеткая нейронная сеть с методами оптимизации роя частиц (FNN-PSO) и искусственная нейронная сеть (ИНС) применяются для установления и оптимизации процесса смешивания цементного сырья.В [2, 16–24] алгебраические методы, методы наименьших квадратов, методы нейронных сетей, методы линейных программ и эмпирические методы используются для расчета или получения оптимальных соотношений ингредиентов в процессе смешивания цементного сырья. В [3, 25–28] в процесс купажирования вводится новое оригинальное сырье и инструменты. В [29–33] обсуждаются проблемы производства цемента.
При этом не уделяется много внимания моделированию и получению оптимального соотношения ингредиентов в процессе смешивания. В данной статье анализируется задача оптимизации соотношения ингредиентов для процесса смешивания цементного сырья в различных условиях.Модель G-NLTV создана для процесса смешивания цементного сырья. Задачу оптимизации соотношения ингредиентов можно эквивалентно преобразовать в задачи выпуклой формы. Предложена структура метода внутренней точки сетки для решения задачи оптимизации соотношения ингредиентов. Программное обеспечение разработано для решения проблемы оптимизации соотношения ингредиентов через MATLAB-GUI. Этот документ организован следующим образом: процесс смешивания сырья и критические параметры цементного ремесла представлены в разделе 2; Модель G-NLTV процесса смешивания сырья при различных обстоятельствах установлена в Разделе 3; структура метода внутренней точки сетки и программное обеспечение для ингредиентов цемента представлены в Разделе 4; числовые примеры в процессе смешивания представлены в разделе 5; содержание статьи завершено в разделе 6.
2. Процесс смешивания сырья и критические параметры изготовления цемента
Процесс производства цемента можно условно разделить на три этапа. На первом этапе производится цементное сырье, которое включает процесс смешивания сырья и процесс измельчения. Второй этап и третий этап предназначены для сжигания сырья и измельчения цементного клинкера соответственно. Процесс смешивания цементного сырья является важным звеном, потому что процесс смешивания влияет на качество цементного клинкера и критические параметры цементного ремесла, поэтому процесс смешивания в конечном итоге влияет на качество цемента.На рисунке 1 показан процесс смешивания цементного сырья и система его контроля. Исходные материалы для цемента — это обычно известняк, стальной шлак, сланец, песчаник, глина и другие материалы. Исходные цементные материалы должны быть смешаны в разумных пропорциях, а затем исходные цементные материалы транспортируются в шаровую мельницу, которая измельчает исходные цементные материалы до определенных размеров. Классификатор выбирает подходящий размер исходного цементного материала, который транспортируется в цементную печь для сжигания.
Качество цементного сырья и цементного клинкера оценивается по коэффициенту насыщения цементной извести (LSF), силикатному соотношению (SR) и соотношению оксидов алюминия (AOR). LSF, SR и AOR напрямую определяются известью, кремнеземом, глиноземом и оксидом железа, которые содержатся в цементном сырье. LSF, SR и AOR являются критическими параметрами цементных судов, поэтому соотношение ингредиентов определяет критические параметры цементных судов. Аналогичным образом, критические параметры цементного ремесла также используются для оценки процесса смешения.При производстве цемента LSF, SR и AOR должны контролироваться или стабилизироваться в разумных пределах. Критические параметры цементного корабля не стабилизированы, поэтому он не может производить цемент высокого качества. Рентгеновский анализатор на рисунке 1 используется для анализа химического состава исходного цементного материала или сырья, затем рентгеновский анализатор может получать обратную связь по LSF, SR и AOR за фиксированное время выборки. На LSF, SR и AOR могут влиять многие неопределенные факторы, такие как колебания состава и поток подачи материала.В таблице 1 приведен химический состав исходных цементных материалов. Химический состав — это функция, изменяющаяся во времени. Символы,, и представляют химический состав исходного цементного материала-. В таблице 1 R 2 O представляет собой общий химический состав оксида натрия (Na 2 O) и калия (K 2 O).
|
Почему химический состав является изменяющейся во времени функцией? Исходные цементные материалы добываются в природной шахте, поэтому химический состав зависит от времени.Колебания состава неизбежны и могут содержать случайность. По мере экономического развития потребление ресурсов увеличивается, и ресурсы потребляются. Поэтому найти оригинальные цементные материалы со стабильным химическим составом становится все труднее. С точки зрения защиты окружающей среды при производстве цемента необходимо использовать части отходов и шлама, поэтому колебания исходного состава цементных материалов в долгосрочной перспективе увеличатся.
В некоторой степени моделирование и оптимизация процесса смешивания цементного сырья становится более важной и сложной задачей.Из-за различного исходного типа цементного материала, различного химического состава и различных требований к критическим параметрам цементного корабля соотношение ингредиентов должно быть более научным и разумным в процессе смешивания. Следовательно, соотношение ингредиентов должно адаптироваться к колебаниям химического состава и гарантировать критические параметры цементных судов в допустимых пределах.
3. Общая динамическая модель процесса смешивания
Процесс смешивания предназначен для производства качественного цементного сырья.В процессе смешивания цементного сырья ключевой задачей является стабилизация критических параметров цементных судов LSF, SR и AOR в допустимых пределах. На практике формулы из [26, 34] используются для расчета LSF, SR и AOR следующим образом: где LSF, SR и AOR. Не теряя общности, предполагается, что в процессе смешивания используются исходные цементные материалы. Массу CaO, SiO 2 , Al 2 O 3 и Fe 2 O 3 в цементном сырье можно получить как
.Сырье для производства SrAC
1. Сырье и обработка сырья
Для синтеза алюминатного цемента стронция необходимо найти надлежащий источник стронция (SrO) и оксида алюминия (Al 2 O 3 ).
Два основных минерала стронция — это его карбонат, стронцианит (SrCO 3 ) и более распространенный сульфатный минерал целестит (SrSO 4 ). Уильям Круикшанк в 1787 году и Адэр Кроуфорд в 1790 году независимо обнаружили стронций в минерале стронцианите, небольшие количества которого связаны с минералами кальция и бария.Они определили, что стронцианит был совершенно новым минералом и отличался от барита и других минералов бария, известных в то время. В 1808 году сэр Хамфри Дэви выделил стронций электролизом смеси влажного гидроксида или хлорида стронция с оксидом ртути с использованием ртутного катода. Элемент был назван в честь города Стронтиан в Шотландии, где был обнаружен минерал стронтианит [91].
Оксид стронция (SrO) является первым существенным компонентом клинкера из алюмината стронция.Следовательно, карбонат стронция (SrCO 3 ) является наиболее подходящим исходным материалом для синтеза клинкера из алюмината стронция. В природе SrCO 3 встречается как редкий орторомбический минерал стронцианит [1] — (пространственная группа Pcmn ) и вместе с изоструктурными минералами арагонитом (CaCO 3 ), витеритом (BaCO 3 ) и церусситом (PbCO ). 3 ) относится к безводным карбонатам из группы арагонита [1] — [92,93].
Структура стронцианита (рис.1 (а)) основан на изолированных треугольниках [CO 3 ] 2-, которые размещены слоями, перпендикулярными оси c . Слой имеет две структурные плоскости, в которых ионы [CO 3 ] 2- ориентированы в противоположном направлении. Между этими слоями размещены катионы с координационным числом 9.
Рисунок 1.
Структура стронцианита состоит из изолированных [CO3] 2-треугольников, расположенных в слои с ионами Sr2 + в пространстве между слоями.
Природные и искусственно синтезированные бинарные ( арагонитов до 14 мол.% Sr [94], стронтианитов от до 27% Ca [94], витеритов [94], баритокальцитов [95]) или тройных твердых растворов ( альстонитов [94]) этих карбонатов интенсивно изучены с целью выяснения механизма их образования, их структуры, термодинамической устойчивости и люминесцентных свойств.
Минералы карбоната кальция включают значительное количество стронция из морской воды, когда они осаждаются. Естественно, что наиболее изучены твердые растворы стронцианита с кальцитом и арагонитом (Ca x Sr 1-x CO 3 ).Существует разрыв несмесимости в диапазоне 0,12 (арагониты) < x <0,87 (стронтианиты) в условиях окружающей среды, который исчезает при температуре ~ 107 ° C [92,94,96,97-100].
Таким образом, природные источники SrCO 3 являются редкими и не имеют промышленного значения, карбонат стронция, а также другие соединения, такие как нитрат стронция, оксид и хлорид стронция, получают из орторомбического минерала целестита [1] — (SrSO 4 , пространственная группа Pnma с параметрами ячейки a = 8.359 Å, b = 5,352 Å, c = 6,686 Å и Z = 4), используя методы, описанные в главе 2.1.1. Структура целестита состоит из изолированных тетраэдров [SO 4 ] 2- и ионов Sr 2+ (рис.2).
Рисунок 2.
Структура целестита (а) и распределение крупных месторождений целестита в мире (б).
Целестит вместе с изоструктурным баритом (BaSO 4 ) и англезитом (PbSO 4 ) относятся к безводным сульфатам из группы барита [1] -.Подобно твердым растворам карбонатов, упомянутым выше, в морской среде сосуществуют также целестит и барит (BaSO 4 ) со значительной долей Sr и Ba в твердых растворах. Поэтому лучше идентифицировать барит, взвешенный в морской воде, как стронциевый барит (Sr x Ba 1-x SO 4 ) [101].
Вторым важным компонентом алюминатного цемента стронция является оксид алюминия (Al 2 O 3 ).Наиболее стабильной кристаллической формой Al 2 O 3 является полиморфная модификация гексагонального корунда ( α -Al 2 O 3 ) из пространственной группы R 3¯C [1] -. Кристаллическая структура корундового типа типична для других оксидов, таких как гематит (Fe 2 O 3 ), эсколаит (Cr 2 O 3 ), карелианит (V 2 ). O 3 ) и тистарит (Ti 2 O 3 ).Следовательно, природные минералы часто окрашиваются примесью этих элементов, например. Рубин окрашен в красный цвет Cr и синий сапфир на Fe и Ti. Это означает, что эти элементы также интересны с точки зрения модификации свойств (процесса спекания, гидратации и схватывания) алюминатного цемента стронция. Этой теме посвящены главы 4 и 5 [424].
Чистый оксид алюминия встречается относительно редко, но монокристаллы драгоценных камней, таких как сапфир (бесцветный) или рубин (красный из-за содержания хрома), можно найти в природе [424].Промышленное производство Al 2 O 3 основано на процессе Байера бокситов. Основная часть производимого глинозема используется в металлургической промышленности для производства алюминия по процессу Холла-Эру [102-105].
Применение Al 2 O 3 в керамике включает производство глиноземного фарфора и керамики из оксида алюминия, керамики ZTA (закаленный оксид алюминия), а также такие области применения, как электрокерамика, строительная керамика, фасонные и неформованные огнеупорные изделия, абразивные материалы. материалы и др. [106-112].С точки зрения объемов производства поликристаллический оксид алюминия является наиболее часто используемым материалом в качестве керамики для структурных применений. Однако по сравнению, например, с нитридом кремния (глава 6), где влияние различных добавок на микроструктуру и свойства хорошо изучено и изучено, оксид алюминия остается материалом со многими неизвестными факторами, которые еще предстоит выявить. Материалы на основе оксида алюминия можно условно разделить на три группы [424]:
Твердотельные спеченные оксиды алюминия: позволяют получать нанокристаллические материалы с превосходными механическими свойствами и хорошо спеченную керамику, прозрачную для видимого света [113,114].
Жидкофазный спеченный оксид алюминия (LPS): является существенной частью промышленных материалов на основе оксида алюминия. В качестве спекающих добавок используются кремнезем, оксиды щелочных металлов и оксиды щелочноземельных металлов [115-117].
Композиты на основе оксида алюминия: Нанокомпозиты на основе ZTA и оксида алюминия с неоксидными фазами, такими как SiC или TiC [118-123].
Получение монокристаллов Al 2 O 3 основано на процессе Вернейля , заключающемся в плавлении в пламени в области высоких температур от 1500 до 2500 ° C [124-127].Боксит (рис. 3) также используется для производства алюминатного цемента [128] или кальцинируется и используется как открывающий материал для огнеупорных изделий [129–131].
Рис. 3.
СЭМ-изображение обожженного зерна боксита.
Для получения абразивных, огнеупорных и керамических изделий хорошего качества необходимо снизить содержание примесей. Химические процессы включают пирохимические методы, методы кислотного выщелачивания или альтернативы восстановительному растворению. Пирохимические методы включают обработку бокситов при высокой температуре такими газами, как H 2 , Cl 2 или безводным HCl [132, 133].Методы кислотного выщелачивания основаны на применении сильных неорганических кислот, таких как HCl или H 2 SO 4 [134-137].
Серьезная проблема этих методов заключается в том, что выщелачивание железа часто сопровождается существенным совместным растворением гидроксидов алюминия, особенно при обработке гибситовых и бемитовых руд. Селективное растворение железа может быть достигнуто в мягких восстановительных условиях. В этом случае растворение оксидов Fe (III) происходит за счет восстановления трехвалентного железа до двухвалентного состояния.Широко признано, что биологические механизмы часто участвуют в мобилизации железа в природных системах. В частном случае бокситов биологическая активность железоредуцирующих микроорганизмов наиболее вероятно вовлечена в образование бокситов, обедненных железом серого цвета [138, 139].
Поскольку при производстве глинозема из бокситовых руд требуется большое количество каустической соды и образуется большое количество жидких отходов « красный шлам », были исследованы альтернативные процессы производства алюминия и алюминиевых сплавов путем карботермического восстановления бокситовых руд.Последовательность восстановления оксидов металлов в бокситовых рудах — это оксиды железа, затем диоксид кремния и диоксид титана, а затем оксид алюминия (рис. 4). Металлическое железо образуется при температурах ниже 1100 ° C. При температуре 1200 ° C или выше образуется фаза ферросплава с кремнием и алюминием. Карбиды титана, кремния и алюминия образовывались карботермическим восстановлением. Металлы образовывались и растворялись в фазе ферросплава, которая после насыщения выделялась в виде карбидов металлов, распределенных внутри фазы сплава в виде включений или вокруг частиц сплава [140, 141].
Рис. 4.
Процесс, предлагаемый для одновременного извлечения железа, алюминия и титана из красного шлама [146].
Также изучается возможность использования технологических остатков Bayer в производстве цемента. В предыдущих работах был предложен способ обработки красного шлама насыщенным раствором Ca (OH) 2 с последующим добавлением 3% H 2 SO 4 для удаления Na. После нагрева обработанный материал предлагается для использования в производстве цемента. Основная часть красного шлама представлена гематитом и глиноземистыми фазами (рис.7), участвующие в производстве гидравлических кристаллических фаз C 3 A и C 4 AF. Затем богатые железом отходы могут быть использованы для производства сульфатостойких цементов [142]. Другой вариант включает такие области применения, как катализаторы и адсорбенты, керамика, покрытия и пигменты, очистка сточных вод и газов, восстановление основных и второстепенных металлов [143-146].
Байер предположил, что [143]: «Красный железосодержащий остаток, который образуется после переваривания, хорошо оседает и при достаточной практике может быть отфильтрован и промыт.Благодаря высокому содержанию железа и низкому содержанию оксида алюминия его можно соответствующим образом обработать или переплавить с другими железными рудами до железа ». Концепция остатков боксита как ресурса железа была проверена рядом рабочих за прошедшие 120 лет, однако «соответствующий способ» обработки остается неясным [144].
Гели алюминия, соли (сульфаты, нитраты или хлориды) или алкоксиды, а также передовые технологии производства керамики могут применяться для получения продуктов высокой чистоты (см. Главу 9).Боксит представляет собой смесь гидроксидов и оксигидроксидов алюминия, таких как бемит, диаспор и гиббсит, с различным содержанием примесных минералов. Основными из них являются гетит, лепидокрокит, гематит, магнетит, каолинит, хлориты, кальцит, анатаз, фосфаты и др. [148].
Бокситы, как первичный источник алюминия, представляют собой типичное скопление выветрившейся континентальной коры [147,148]. Бокситы обычно относятся к трем основным генетическим типам [149–152]:
Латерические бокситы (иногда называемые экваториальными) образуются из выветрившихся первичных алюмосиликатных пород в экваториальном климате, составляющем около 90% мировых эксплуатируемых запасов бокситов. .Латеритный боксит обычно образуется в результате латеритизации на месте, поэтому наиболее важными факторами, определяющими степень и степень его содержания, считаются состав материнской породы, климат, топография, дренаж, химический состав и движение подземных вод, расположение уровня грунтовых вод, микробная активность и продолжительность процессов выветривания.
Осадочные бокситы в основном образуются в результате накопления латеритных бокситовых отложений во время механического переноса поверхностных потоков.Кроме того, последующее выветривание и перенос Al и Fe играют существенную роль в бокситизации, которая не только поддерживает образование бокситов из каолиновых глин, но также способствует обогащению первичных обломочных руд.
Карстовые бокситы названы в честь их приуроченности к карстовым зонам с карстифицированными или карстифицирующими карбонатными породами. Отложения карстового типа происходят из самых разных материалов в зависимости от области источника.
Рисунок 5.
Распространение сверхкрупных месторождений бокситов по всему миру [152].
Каждая генетическая группа бокситов испытала разделение алюминия (Al) и кремния (Si) в результате накопления Al, а также удаление Si, щелочных металлов и редкоземельных элементов из материнской породы (осадка) во время ее выветривания [148 ].
Месторождения бокситов (Рис.5) формируются в основном при атмосферном давлении и температуре на (под) поверхности континентов. Обилие биодоступного железа, питательных элементов, серы и органического углерода делают бокситы пригодными для обитания микроорганизмов, поэтому они становятся редкими геологическими объектами, которые могут сохранять записи о микробиологической активности на поверхности континентов при сильных погодных условиях.В результате деятельности микроорганизмов может образовываться семейство минералов с особой морфологией и составом стабильных изотопов. Месторождения бокситов были детально изучены из-за их экономической ценности. Они играют важную роль в изучении палеоклимата и палеогеографии континентов, поскольку содержат немногочисленные записи о выветривании и эволюции континентальных поверхностей [148].
1.1. Промышленное и лабораторное производство SrCO 3
Химическая промышленность потребляет более 95% добытого целестита для преобразования в другие соединения стронция.Основные примеси в целеститовых рудах — кальцит (CaCO 3 ), гипс (CaSO 4 2H 2 O), кварц (SiO 2 ) и глинистые минералы. Методы гравитационного разделения и флотация [1] — в основном используются для отделения этих примесей из-за высокой эффективности и низких эксплуатационных затрат. Кроме того, процесс не требует использования других химикатов для очистки и оказывает незначительное воздействие на окружающую среду. С другой стороны, эффективность этих методов приготовления целеститового концентрата зависит от текстуры руды, а также от типа и количества связанных примесей [153-155].Другой наиболее важный фактор — это размер частиц. Чрезвычайно мелкий размер частиц должен быть достигнут путем измельчения для выделения целестита и кальцита [156]. Разница в измельчаемости позволяет отделить целестит от гипса дифференциальным измельчением [157].
Сдвиговая флокуляция [1] мелкодисперсной суспензии целестита с додецилсульфатом натрия (SDS, C 12 H 25 SO 4 Na) или с анионным алкилсукцинатным поверхностно-активным веществом может проводиться в широком диапазоне pH (3 — 11), но максимальная эффективность достигается при pH 7.Повышение концентрации поверхностно-активного вещества положительно влияет на ход процесса. Наиболее распространенными неорганическими диспергаторами являются силикат натрия, фосфат натрия и полифосфат натрия. Исследование взаимного влияния добавок показывает, что силикат натрия сильно предотвращает флоккуляцию целестита с додецилсульфатом натрия, но диспергирующий эффект SDS невелик при использовании анионного алкилсукцинатного поверхностно-активного вещества. В присутствии полифосфата натрия сдвиговая флокуляция суспензии целестита медленно увеличивается для обоих поверхностно-активных веществ.Подобное увеличение можно также наблюдать для фосфата натрия в присутствии SDS. Однако фосфат натрия диспергировал суспензию целестита в присутствии анионного алкилсукцинатного ПАВ [158]. Натрийолеат (натриевая соль цис-9-октадеценовой кислоты) и ацетат амина твердого жира (ТАА) были более эффективными для суспензий целестита в диапазонах pH 7–11 и 6–10 соответственно [159].
Поверхность целестита становится гидрофобной за счет адсорбции додецилсульфата на поверхности. Додецилсульфат натрия также эффективен для флотации целестита в растворе, не содержащем карбонатных частиц, в широком диапазоне pH от 3 до 11.Поверхностное преобразование целестита в карбонат стронция, которое происходит при pH ≥ 7,8, приводит к тому, что дзета-потенциал целестита становится более отрицательным и впоследствии становится похожим на таковой у карбоната стронция. Сульфат-ионы обмениваются на карбонат-ионы в кристаллической решетке целестита, поэтому частицы CO 3 2- и HCO 3 —, вероятно, ответственны за отрицательное увеличение дзета-потенциала. Поверхностное превращение целестита в карбонат стронция не влияет на флотируемость до pH 10.Как только pH выше 10, концентрация видов CO 3 2- и HCO 3 — в водном растворе становится очень естественной, и снижение плавучести, вероятно, вызвано абсорбцией этих частиц на газированных поверхность целестита [155].
Характеристики коагуляции и флокуляции целестита неорганическими солями, такими как CaCl 2 , MgCl 2 и AlCl 3 , показывают, что ион магния более эффективен в суспензии целестита, чем ионы кальция и алюминия при высоких уровнях pH. .Эффект значительно варьировался в зависимости от концентрации. В то время как ионы кальция и магния не были эффективны для суспензии при pH ниже нейтрального, ион алюминия вызывал стабилизацию суспензии целестита при этих уровнях pH [160].
В общем, агрегация мелких частиц может быть достигнута путем нейтрализации электрического заряда взаимодействующих частиц путем коагуляции, или флокуляция может быть проведена путем сшивания частиц полимолекулами [161]. Значение pH изоэлектрической точки целестита, определенное методом затрудненного осаждения, составляет 2.6 [160].
Существует два основных процесса производства SrCO 3 из SrSO 4 [162]:
Пирогидрометаллургический процесс или метод черной золы;
Гидрометаллургический процесс.
Первый из них — « пирогидрометаллургический процесс или черная зола метод ». Целестит карботермически восстанавливается до водорастворимого сульфида (SrS), который затем растворяется в горячей воде [1] — Первая твердотельная реакция во время карботермического восстановления происходит при температуре до 400 ° C [163]:
SrSO4 (s) +4 C (s) → SrS (s) +4 CO (г) E1После образования поверхностного слоя продукта дальнейшее развитие реакции 1 тормозится.Образовавшийся диоксид углерода диффундирует через слой и вступает в реакцию с целеститом в соответствии со следующей реакцией:
SrSO4 (т) +4 CO (г) → SrS (т) +4 CO2 (г) E2Диоксид углерода диффундирует дальше из зоны реакции и генерирует больше CO в соответствии с реакцией Будуара, если температура ≥ 720 ° C:
CO2 (г) + C (с) ↔2 CO (г) E3Это означает, что прямая реакция целестита с углеродом (уравнение 1) имеет мало важно, и SrSO 4 может быть преобразован в SrS при температуре выше, чем равновесная реакция Будуара .Важным фактором процесса 2 является потенциал восстановления газовой фазы, определяемый отношением парциальных давлений p CO / p CO2 . Было также замечено, что скорость карботермического восстановления значительно увеличивается, если целеститовый концентрат и углерод измельчают вместе. Для получения водорастворимого сульфида стронция необходимы температуры в диапазоне от 1100 до 1300 ° C с избытком металлургического кокса.
Растворение сульфида стронция в горячей воде можно выразить следующей гетерогенной реакцией [164]:
SrS (s) + h3O (l) → Sr2 + (водн.) + HS- (водн.) + OH- (водн.) E4Ур.4 показывает, что pH выщелачивающего раствора увеличивается от почти нейтрального до значения 11,5 — 12,5 по мере увеличения концентрации ионов OH — . Следует избегать чрезвычайно высоких значений pH (pH> 14), чтобы предотвратить осаждение в системе гидроксида стронция [1] -:
Sr2 + (водн.) +2 HO2 (l) → Sr (OH) 2 (s) + 2H + (водн.) E5Значение константы равновесия K при 25 ° C составляет 3,55 10 -29 , т.е. log K = -28,45. Следовательно, концентрация Sr (OH) 2 в выщелачивающем растворе (рис.6) может быть выражено как:
log10 [Sr2 +] = 28,45−2 pHE6Это означает, что выщелачивание SrS необходимо проводить в относительно слабощелочной среде, чтобы обеспечить высокую концентрацию стронция в растворе. Растворимость гидроксида стронция увеличивается при повышении температуры. Таким образом, выщелачивание и осаждение SrCO 3 при более высоких температурах означает, что образование осадков Sr (OH) 2 уменьшается.
С другой стороны, при выщелачивании при pH <7 образуется газообразный сероводород:
HS- (aq) + H + (aq) h3S (g) E7Образование газообразного сероводорода происходит на ранних стадиях выщелачивания, когда pH суспензии относительно низкий.
Введение газообразного диоксида углерода или карбонизирующего агента, такого как кальцинированная сода, приводит к осаждению карбоната стронция из перенасыщенного раствора (уравнение 13). Последовательность стадий реакции включает растворение диоксида углерода в растворе и in situ образование угольной кислоты (H 2 CO 3 , уравнение 8), диссоциацию H 2 CO 3 (уравнение .9 с константой равновесия ( K ´), заданной уравнением 10), диссоциация бикарбонатных разновидностей (уравнение.11 с константой равновесия ( K ´´), заданной уравнением 12) и осаждением карбоната стронция (уравнение 13 с ионным продуктом ( P ), заданным уравнением 14) [163-165].
h3CO3↔H + (водн.) + HCO3- (водн.) E9K ′ = [H +] [HCO3 -] [h3CO3] E10K ″ = [H +] [CO32 -] [HCO3-] E12Sr2 + (водн.) + CO32- (водн.) → SrCO3 (s) E13Растворимость карбоната стронция составляет 5,6 10 -10 при температуре 25 ° C и снижается до 1,32 10 -10 при температуре 100 ° C. Реакция гидролиза приводит к щелочности водного раствора SrCO 3 .
Рис. 6.
Влияние pH на равновесную концентрацию ионов Sr2 + и SrOH + в растворе.
Уравнения 8-14 показывают, что для осаждения каждого моля SrCO 3 требуется один моль газообразного CO 2 . Концентрация ионов CO 3 2- в выщелачивающем растворе для данного pH выражается следующим законом:
log10 [CO32 -] = log10K ″ + pH + log10 [HCO3-] E15Если pH выщелачивающего раствора выше 7, ионы H + , образованные реакцией 11, нейтрализующей анионы OH — , высвобождаются во время выщелачивания SrS (ур.4).
В целом, метод черной золы считается более экономичным, чем другие альтернативы [165].
Второй способ получения карбоната стронция — это метод прямого преобразования или гидрометаллургический метод . Карбонат стронция получают путем введения порошка SrSO 4 в горячий раствор Na 2 CO 3 , где происходит следующий процесс превращения:
SrSO4 + Na2CO3 → SrCO3 + Na2SO4E16или лучше:
SrSO4 (s) + CO32- (водный) → SrCO3 (s) + SO42- (водный) E17Влияние условий эксперимента на процесс включает влияние температуры, отношения твердой и жидкой фаз, размера частиц, скорости перемешивания, Na 2 CO 3 : мольное соотношение SrSO 4 и т. Д.Скорость превращения целестита в карбонат стронция увеличивается с увеличением температуры до 70 ° C [165-170]. Подготовленный карбонат или сульфид далее превращается в другие соли стронция [91].
Также можно использовать карбонат аммония ((NH 4 ) 2 CO 3 ) [1] — и бикарбонат (NH 4 HCO 3 ) вместо кальцинированной соды для конверсии [165,171 -174]:
SrSO4 + (Nh5) 2CO3 → SrCO3 + (Nh5) 2SO4E18(в кипящей смеси) SrSO4 + (Nh5) 2CO3 → SrCO3 + 2Nh4 + SO3 + h3O
SrSO4 (s) + 2HCO3- (водн.) ) + SO42- (водн.) + H3O (l) + CO2 (г) E19Существует также альтернатива в механохимическом синтезе, где интенсивно измельчается смесь SrSO 4 и NH 4 HCO 3 .Затем растворимый сульфат аммония удаляется выщелачиванием продукта в воде [165].
Более того, в современной литературе описано множество специальных методов получения SrCO 3 . Эти методы включают получение карбоната стронция путем твердофазного разложения из неорганического предшественника [746]. Простые методы растворения [175], сольвотермический синтез [176-178], метод кипячения с обратным холодильником [188] гидротермальный синтез [179-182], ультразвуковой метод или сонохимический синтез [183,184], синтез с помощью микроволн [185,186] и механохимический синтез [168,187] ] были описаны.В зависимости от применяемой техники приготовления могут быть получены частицы карбоната стронция различной формы, такие как сферы, стержни, усы и эллипсоиды, иглы, цветы, ленты, проволока и т. Д. [188].
Растворимость солей стронция в большинстве случаев выше или ниже, чем у соответствующих солей кальция и бария (Таблица 1).
Катионы | Ca2 + | Sr2 + | Ba2 + | |||||
Анионы | Растворимость | ОН- | 0.160 | 0,810 | 3,890 | |||
F- | 0,0017 | 0,0175 | 0,1600 | |||||
Класс | 74,5 | 53,1 | 3600 2 900 | 362 | 128,8 | 70,4 | 9,10 | |
CO 3 2- | 0,0014 (25 ° C) | 0,00155 (25 ° C) | 0,0022 (18 ° C) | |||||
0.20 | 0,0148 | 0,00023 | ||||||
C 2 O 4 2- | 0,00058 | 0,0048 | 0,0125 | |||||
0,00037 |
Таблица 1.
Растворимость солей щелочноземельных металлов при температуре 20 ° C.
Металлический стронций можно получить электролизом смешанного расплава хлорида стронция и хлорида калия в графитовом тигле с использованием железного стержня в качестве катода.Верхнее катодное пространство охлаждается, и металлический стронций собирается вокруг охлаждаемого катода и образует стержень. Металлический стронций можно также получить термическим восстановлением его оксида алюминием. Смесь оксида стронция с алюминием нагревают при высокой температуре в вакууме. Стронций собирают перегонкой в вакууме. Стронций также является восстановителем. Восстанавливает оксиды и галогениды металлов при повышенных температурах до металлической формы.
Стронций также получают восстановлением его амальгамы, гидрида и других солей.Амальгама нагревается, и ртуть отделяется перегонкой. Если используется гидрид, его нагревают до 1000 ° C в вакууме для разложения и удаления водорода. Такое термическое восстановление дает металл высокой чистоты, который на воздухе окисляется до SrO. Металл пирофорен, и SrO, и SrO 2 (пероксид стронция) образуются при воспламенении на воздухе. При нагревании газообразным хлором или парами брома стронций ярко горит, образуя галогениды (SrCl 2 или SrBr 2 ).При нагревании с серой образует сульфид (SrS) [91].
Стронций активно реагирует с водой и соляной кислотой с образованием гидроксида Sr (OH) 2 или хлорида (SrCl 2 ) с выделением водорода [91]:
Sr + 2 h3O → Sr (OH) 2 + h3E20Когда при нагревании под водородом он образует ионный гидрид (SrH 2 ), стабильную кристаллическую соль. При нагревании металлического Sr в токе азота выше 380 ° C образуется нитрид (Sr 3 N 2 ).
.Производство портландцемента — материалы и процессы
При производстве цемента используются различные сырьевые материалы и различные процессы. Каждый процесс объясняется химическими реакциями при производстве портландцемента.
Цемент представляет собой порошок зеленовато-серого цвета, изготовленный из кальцинированной смеси глины и известняка. При смешивании с водой становится твердым и прочным строительным материалом.
История цемента восходит к Римской Империи. Современный цемент. То есть портландцемент впервые был произведен британским каменщиком Джозефом Аспдином в 1824 году, который варил цемент на своей кухне.Он нагрел смесь известняка и глиняного порошка у себя на кухне и измельчил смесь в порошок, создав цемент, который затвердевает при смешивании с водой. Название Портленд было дано изобретателем, так как он напоминает камень, добытый на острове Портленд.
Впервые современный портландцемент был использован при строительстве туннеля в Темзе в 1828 году.
Процесс производства цемента
Процесс производства портландцемента описан ниже.
- Смешивание сырья
- Горение
- Шлифовальный
- Хранение и упаковка
1. Смешивание сырья
Основным сырьем, используемым при производстве цемента, являются кальций, кремний, железо и алюминий. Эти минералы используются в различных формах в зависимости от наличия минералов.
В таблице показано сырье для производства портландцемента
Процесс смешивания при производстве цемента осуществляется 2 способами,
a) Сухой процесс
Известковое и глинистое сырье сначала измельчается в гирационных дробилках, чтобы получить отдельные куски размером 2-5 см.Измельченный материал снова измельчают, чтобы получить мелкие частицы в шаровой или трубчатой мельнице.
Каждый мелко измельченный материал после просеивания хранится в бункере. Теперь эти порошкообразные минералы смешиваются в требуемой пропорции, чтобы получить сухую сырьевую смесь, которая затем хранится в силосах и готовится к отправке во вращающуюся печь. Теперь сырье смешивается в определенных пропорциях, так что средний состав конечного продукта сохраняется должным образом.
Рис. Производство цемента сухим способом
б) Мокрый процесс
Сырье сначала измельчается, превращается в порошок и хранится в силосах.Затем глину промывают в стиральных мельницах, чтобы удалить приставшие органические вещества, содержащиеся в глине.
Порошкообразный известняк и промытая водой глина направляются в каналы и поступают в мельницы, где они полностью смешиваются и образуется паста, известная как суспензия.
Процесс измельчения может осуществляться в шаровой или трубчатой мельнице, или даже в том и другом. Затем суспензия направляется в сборный резервуар, где можно регулировать состав. Суспензия содержит около 38-40% воды, которая хранится в резервуарах для хранения и хранится в готовности для вращающейся печи.
Рис. Производство цемента мокрым способом
Сравнение сухого процесса и мокрого процесса производства цемента
Критерии | Сухой процесс | Мокрый процесс |
Твердость сырья | Довольно сложно | Любое сырье |
Расход топлива | Низкая | Высокая |
Время обработки | Малый | Высшее |
Качество | Низкое качество | Превосходное качество |
Себестоимость продукции | Высокая | Низкая |
Общая стоимость | Дорогой | Дешевле |
Физическое состояние | Сырьевая смесь (твердая) | Шлам (жидкий) |
2.Сжигание сырья
Процесс обжига осуществляется во вращающейся печи, при этом сырье вращается со скоростью 1-2 об / мин на ее продольной оси. Вращающаяся печь состоит из стальных труб диаметром 2,5-3,0 метра и длиной от 90 до 120 метров. Внутренняя сторона печи облицована огнеупорным кирпичом.
Печь опирается на колонны из кирпичной кладки или бетона и опирается на роликовый подшипник в слегка наклонном положении с уклоном от 1: 25 до 1: 30.Сырьевая смесь сухого процесса или скорректированного шлама мокрого процесса вводится в печь с верхнего конца. Печь нагревается с помощью порошкообразного угля, масла или горячих газов из нижнего конца печи, так что возникает длинное горячее пламя.
Поскольку положение печи наклонено и она медленно вращается, материал, загружаемый с верхнего конца, перемещается к нижнему концу со скоростью 15 м / час. В верхней части вода или влага из материала испаряются при температуре 400 ° C, поэтому этот процесс известен как зона сушки.
Центральная часть, т.е. зона обжига, температура около 10000 ° C, где происходит разложение известняка. Оставшийся материал находится в форме небольших комков, известных как узелки после выхода CO 2 .
CaCO 3 = CaO + CO 2
Нижняя часть (зона клинкера) имеет температуру в пределах 1500-17000 ° C, где известь и глина вступают в реакцию с образованием алюминатов кальция и силикатов кальция. Эти алюминаты и силикаты кальция плавятся, собираясь в маленькие твердые камни, известные как клинкеры.Размер клинкера колеблется от 5 до 10 мм.
Нижняя часть, т.е. зона клинкера, имеет температуру около 1500-1700С. В этом регионе известь и глина реагируют с образованием алюминатов кальция и силикатов кальция. Эти продукты из алюминатов и силикатов кальция плавятся вместе, образуя твердые и мелкие камни, известные как клинкеры. Размер мелкого и твердого клинкера колеблется от 5 до 10 мм.
2CaO + SiO 2 = Ca2SiO 4 (силикат декламированный (C 2 S))
3CaO + SiO 2 = Ca3SiO 5 (трехкальциевый силикат (C 3 S))
3CaO + Al 2 O 3 = Ca 3 Al 2 O 6 (алюминат дикальция (C 2 A))
4CaO + Al 2 O 3 + Fe 2 O 3 = Ca 4 Al 2 Fe 2 O 10 (тетракальцийалюмоферрит (C
4 AF)) Клинкер, поступающий из зоны обжига, очень горячий.Чтобы снизить температуру клинкера, воздух пропускается противотоком в основании вращающейся печи. Остывшие клинкеры собирают в небольшие тележки.
3. Помол клинкера
Охлажденный клинкер поступает из охлаждающих ванн и отправляется в мельницы. Клинкеры тонко измельчаются в порошок в шаровой или трубчатой мельнице. Порошковый гипс добавляется около 2-3% в качестве замедлителя при окончательном измельчении. Конечным продуктом является цемент, который не быстро оседает при контакте с водой.
По истечении первоначального времени схватывания цемент становится жестким, а гипс замедляет растворение алюминатов трикальция, образуя нерастворимый трикальцийсульфоалюминат, который предотвращает слишком ранние дальнейшие реакции схватывания и твердения.
3CaO.Al 2 O 3 + xCaSO 4 .7H 2 O = 3CaO.Al 2 O 3 .xCaSO 4 .7H 2 O
4. Хранение и упаковка
Измельченный цемент хранится в силосах, откуда он продается в контейнерах или мешках по 50 кг.
. альтернативных источников сырья для производства цемента | Материалы проекта
Главная → Проекты → Альтернативные источники сырья для производства цемента- 5 глав
- 53 страницы
- 6,583 слов
- Материалы проекта
- Заявление / отчет
ИНСТРУКЦИИ: Альтернативные источники сырья для проекта «Производство цемента». Пожалуйста, расслабьтесь и внимательно изучите приведенный ниже исследовательский материал. НЕ копируйте слово в слово.Цель UniProjects предоставить этот исследовательский материал для этого проекта «Альтернативные источники сырья для производства цемента» — снизить стресс, связанный с переходом из одной школьной библиотеки в другую, и все это во имя поиска исследовательских материалов «Альтернативные источники сырья для производства цемента». Мы не поощряем плагиат в каких-либо формах. Эта услуга является законной, потому что все учебные заведения разрешают своим студентам читать предыдущие проекты, книги, статьи или статьи при разработке своих собственных работ.По словам Остина Клеона, «вся творческая работа строится на том, что было раньше».
Вы читаете материал проекта под названием: Альтернативные источники сырья для производства цемента.
Общеизвестно, что цемент получают из известняка, мрамора / глины и гипса с помощью следующих трех основных процессов: влажный полувлажный вспомогательный сухой способ.
Стоимость эксплуатации известняка: основное сырье составляет около 50% стоимости производства, что приводит к высокой стоимости цемента.Следовательно, становится крайне необходимо снизить стоимость цемента, исследуя альтернативный источник сырья для производства цемента и, следовательно, этот проект.
Согласно литературе, зола рисовой шелухи, день Укпо и день Нсу содержат основные минеральные компоненты, которые есть в известняке. Рисовую шелуху обжигали при температурах 5000 ° C, 6000 ° C, 7000 ° C и 8000 ° C. Лучшая зола была получена при температуре 7000С. Вышеупомянутые материалы также были проанализированы для определения их минеральных составляющих.Результат показал, что рисовая шелуха содержит мало алюминия (Al2O3) и не содержит извести (Ca0). Чтобы восполнить эти минеральные компоненты, Upo day, богатый алюминатом, был смешан с известью (CaO) — побочным продуктом газового завода, и три минерала были смешаны с использованием метода коэффициента насыщения известью. Использовалось соотношение смеси 70% извести, 20% ПГА и 10% глинозема (Укпо день). Смесь перемешивали сухим способом и обжигали в печи при температуре 12000 ° С. Полученная масса, известная как динкер, была измельчена с 5% гипса.Полученный цемент дал общую прочность 2 Н / м 2.
Титульная страница
Передаточное письмо
Сертификация, страница
Посвящение
Благодарность
Аннотация
Определение терминов
Таблица содержания Глава первая
Введение
1.1 Предпосылки исследования
1.2 Цель исследования
1.3 Объем проекта
1.4 Значение исследования
1.5 Ограничение исследования
Глава вторая
2.0 Обзор литературы
2.1 Известь и ее применение
2.2 Преобразование богатой шелухи в ясень
2.3 Основное цементное сырье
2.4 Типы цемента
2.5 Химия цемента
Глава третья
3.0 Дополнительные работы
3.1 Пиропереработка рисовой шелухи
3.2 Тератмент и анализ извести
3.3 Приготовление смеси Rawmix
3.4 Процесс производства
Глава четвертая
4.0 Анализ и обсуждение результата
Глава пятая
5.0 Заключение и рекомендация
5.1 Рекомендация
Каталожные номера
Глава первая «Альтернативные источники сырья для производства цемента» начинается отсюда.
Размещено UniProjects.Net в разделе «Темы и материалы проекта»
ВВЕДЕНИЕ
1.1 ПРЕДПОСЫЛКИ ИССЛЕДОВАНИЯ
Цемент — это полная смесь минеральных веществ, которые постепенно затвердевают при смешивании с водой. Это продукт реакции извести с оксидами кремнезема и железа. Он используется в строительной промышленности как смешивающий материал. Некоторые строители считают его основным инженерным материалом для строительства. многие родственные строительные материалы, такие как асбест, бетонные уплотнения водопропускных труб, бетонные опоры, цементные блоки и т. д., производятся из цемента, и они также играют очень важную роль в строительной отрасли. Для среднего нигерийца главной жизненной целью является владение цементом для жилого дома, ключевое сырье превратилось в «золото» и стало актуальной проблемой. Так же, как железо, сталь и нефтехимия, цемент в равной степени является основным трамплином для индустриализации. Это стремление к индустриализации привело к увеличению спроса с последующим увеличением стоимости цемента.
Одна из причин непомерной стоимости цемента — нехватка сырья. Эта ситуация возникает в результате его быстрого истощения, которое не заменяется.
Другой причиной непомерной стоимости цемента является высокая стоимость разведки и эксплуатации сырья. Для добычи основного сырья для производства цемента — известняка требуется много машин, установок и взрывчатых веществ. Много денег также выплачивается в качестве компенсации общинам, владеющим землей. Все эти затраты приводят к высокой стоимости цемента. Таким образом, данное исследование должно было изучить альтернативный источник сырья для производства цемента.
Это расследование было направлено на промышленные отходы и сельскохозяйственные остатки. Сельскохозяйственные остатки состоят из органических компонентов, таких как целлюлоза, лигнин, клетчатка и небольшие количества сырого протеина и жира. Кроме того, они содержат ряд минералов, в том числе кремнезем, оксид алюминия и оксид железа. Сам остаток не может использоваться в качестве замены цемента, и интерес представляет зола, полученная в результате предварительной обработки. Для составляющих золы требуются два фактора.Содержание золы важно, потому что оно указывает количество остатков, которые необходимо сжечь; это урожай. D..J COOK (1980) утверждает, что рисовая шелуха показала намного больше золы, чем другие растения, такие как сорго, кукурузные листовые пластинки, бамбуковые узлы, (внутренняя часть) бангассе, листья и стебли лантаны и рисовая солома.
На каждые 1000 кг сожженной рисовой шелухи получается 200 кг золы. Поэтому неудивительно, что рисовая шелуха стала сельскохозяйственным продуктом с наибольшим потенциалом в качестве заменителя цемента.
С другой стороны, известь является побочным продуктом газовых компаний. Это легко доступно бесплатно.
Использование этого сырья для производства цементной продукции является весьма альтернативным в развивающихся странах, таких как наша. Это связано с тем, что он не только снижает спрос на портландцемент, но также обеспечивает цемент в сельских районах страны, особенно в районах выращивания риса, где рисовая шелуха встречается в больших количествах и представляет собой вред для окружающей среды.
1.2 ЦЕЛЬ ИССЛЕДОВАНИЯ
Нынешняя высокая стоимость цемента и непомерно высокая стоимость жилых домов, вызванная высокой стоимостью эксплуатации сырья, энергии, демографическим взрывом и развитием, вызвали необходимость интенсификации поиска альтернативного сырья для производства этого продукта. Таким образом, целью этого проекта было снижение стоимости цемента за счет использования альтернативного сырья из промышленных и сельскохозяйственных отходов.
1.3 ОБЪЕМ ПРОЕКТА
Намерение было
1) Найдите и проанализируйте следующее сырье из рисовой шелухи извести (отходы газовой компании Нигера), глина Укпо, глина Нсу и пылевидная зола (ПЭА)
2) Получите наилучшие условия для предварительной обработки.
3) Приготовление сырой смеси.
4) Горящий
5) Определение физических характеристик.
1.4 ЗНАЧЕНИЕ ИССЛЕДОВАНИЯ
По завершении исследования результат будет важен для правительства и предпринимателей, которые могут захотеть заняться производством цемента.Увеличение инвестиций в эту область сократит разрыв между спросом и предложением и снизит стоимость цемента, снижение цены на цемент станет катализатором развития инфраструктуры, и большинство из них сможет владеть жилым домом.
Еще одно важное значение проекта заключается в том, что он послужит отправной точкой для производства других видов цемента, известных как смешанный цемент. Исследование также поможет обеспечить цементом сельские районы, обычно те, которые традиционно не имеют цемента.Таким образом возможен малый бизнес.
Поскольку промышленные и сельскохозяйственные отходы являются отходами, которые вызывают загрязнение окружающей среды и создают проблемы с утилизацией, их утилизация не только ограничит возможности экологической занятости для наших молодых выпускников школ.
Исследование также принесет огромную пользу будущим исследователям и студентам, которые будут заинтересованы в изучении аналогичных предметов.
1.5 ОГРАНИЧЕНИЕ ИССЛЕДОВАНИЯ
Многие факторы ограничили продвижение этого исследования, в том числе
а) Отсутствие высокотемпературной печи до 16000С.мы могли получить только один (15000) в Федеральном центре производства научного оборудования (ФЦЭИО). Он мог достигать только температуры 13000С, и у нас не было другого выхода, кроме как остановиться на нем.
б) Стоимость химического анализа PRODA очень высока — 300 евро за образец. Поэтому было проанализировано лишь несколько образцов.
c) Другим ограничением было отсутствие гипсового или графитового тигля, который выдерживал бы высокую температуру, особенно во время обжига. По этой причине у нас не было достаточного количества сгоревших образцов для физических испытаний.
Нажмите на расположенную выше кнопку 👆 «Подписаться и загрузить полную работу» , чтобы разместить заказ и загрузить полный материал проекта «Альтернативные источники сырья для производства цемента».
Автор: UniProjects.Net в разделе «Темы проекта и материалы»
Доступна вторая глава этой исследовательской работы «Альтернативные источники сырья для производства цемента». Закажите и загрузите полную версию работы. Глава вторая «Альтернативные источники сырья для производства цемента» содержит: обзор литературы, известь и ее использование, преобразование богатой шелухи в Зола, основное цементное сырье, виды цемента и химия цемента.
Третья глава этой академической работы «Альтернативные источники сырья для производства цемента» доступна, закажите и загрузите полную версию работы. Глава третья «Альтернативные источники сырья для производства цемента» содержит: экспериментальные работы, пиропереработку рисовой шелухи, обработку и анализ Известь, смесь Rawmix и производственный процесс.
Глава четвертая этого проекта «Альтернативные источники сырья для производства цемента» доступна, закажите и загрузите полную работу.. Глава четвертая «Альтернативные источники сырья для производства цемента» содержит: анализ и обсуждение результатов.
Глава пятая этого материала Альтернативные источники сырья для производства цемента доступна, закажите и загрузите полную работу. Глава пятая «Альтернативные источники сырья для производства цемента» содержит: заключение, рекомендации и ссылки.
Вы здесь: Главная → Проекты → Альтернативные источники сырья для производства цемента .
Стоимость эксплуатации известняка: основное сырье составляет около 50% стоимости производства, что приводит к высокой стоимости цемента.Следовательно, становится крайне необходимо снизить стоимость цемента, исследуя альтернативный источник сырья для производства цемента и, следовательно, этот проект.
Согласно литературе, зола рисовой шелухи, день Укпо и день Нсу содержат основные минеральные компоненты, которые есть в известняке. Рисовую шелуху обжигали при температурах 5000 ° C, 6000 ° C, 7000 ° C и 8000 ° C. Лучшая зола была получена при температуре 7000С. Вышеупомянутые материалы также были проанализированы для определения их минеральных составляющих.Результат показал, что рисовая шелуха содержит мало алюминия (Al2O3) и не содержит извести (Ca0). Чтобы восполнить эти минеральные компоненты, Upo day, богатый алюминатом, был смешан с известью (CaO) — побочным продуктом газового завода, и три минерала были смешаны с использованием метода коэффициента насыщения известью. Использовалось соотношение смеси 70% извести, 20% ПГА и 10% глинозема (Укпо день). Смесь перемешивали сухим способом и обжигали в печи при температуре 12000 ° С. Полученная масса, известная как динкер, была измельчена с 5% гипса.Полученный цемент дал общую прочность 2 Н / м 2.
Введение
1.1 Предпосылки исследования
1.2 Цель исследования
1.3 Объем проекта
1.4 Значение исследования
1.5 Ограничение исследования
2.0 Обзор литературы
2.1 Известь и ее применение
2.2 Преобразование богатой шелухи в ясень
2.3 Основное цементное сырье
2.4 Типы цемента
2.5 Химия цемента
3.0 Дополнительные работы
3.1 Пиропереработка рисовой шелухи
3.2 Тератмент и анализ извести
3.3 Приготовление смеси Rawmix
3.4 Процесс производства
4.0 Анализ и обсуждение результата
5.0 Заключение и рекомендация
5.1 Рекомендация
Каталожные номера
Размещено UniProjects.Net в разделе «Темы и материалы проекта»
1.2 ЦЕЛЬ ИССЛЕДОВАНИЯ
Нынешняя высокая стоимость цемента и непомерно высокая стоимость жилых домов, вызванная высокой стоимостью эксплуатации сырья, энергии, демографическим взрывом и развитием, вызвали необходимость интенсификации поиска альтернативного сырья для производства этого продукта. Таким образом, целью этого проекта было снижение стоимости цемента за счет использования альтернативного сырья из промышленных и сельскохозяйственных отходов.
Намерение было
1) Найдите и проанализируйте следующее сырье из рисовой шелухи извести (отходы газовой компании Нигера), глина Укпо, глина Нсу и пылевидная зола (ПЭА)
2) Получите наилучшие условия для предварительной обработки.
3) Приготовление сырой смеси.
4) Горящий
5) Определение физических характеристик.
По завершении исследования результат будет важен для правительства и предпринимателей, которые могут захотеть заняться производством цемента.Увеличение инвестиций в эту область сократит разрыв между спросом и предложением и снизит стоимость цемента, снижение цены на цемент станет катализатором развития инфраструктуры, и большинство из них сможет владеть жилым домом.
Исследование также принесет огромную пользу будущим исследователям и студентам, которые будут заинтересованы в изучении аналогичных предметов.
Многие факторы ограничили продвижение этого исследования, в том числе
а) Отсутствие высокотемпературной печи до 16000С.мы могли получить только один (15000) в Федеральном центре производства научного оборудования (ФЦЭИО). Он мог достигать только температуры 13000С, и у нас не было другого выхода, кроме как остановиться на нем.
б) Стоимость химического анализа PRODA очень высока — 300 евро за образец. Поэтому было проанализировано лишь несколько образцов.
c) Другим ограничением было отсутствие гипсового или графитового тигля, который выдерживал бы высокую температуру, особенно во время обжига. По этой причине у нас не было достаточного количества сгоревших образцов для физических испытаний.
Автор: UniProjects.Net в разделе «Темы проекта и материалы»
Комментариев нет